Weaving
Weaving is a method of textile production in which two distinct sets of yarns or threads are interlaced at right angles to form a fabric or cloth. Other methods are knitting, crocheting, felting, and braiding or plaiting. The longitudinal threads are called the warp and the lateral threads are the weft, woof, or filling. (Weft is an old English word m eaning "that which is woven"; compare leave and left.[lower-alpha 1]) The method in which these threads are inter-woven affects the characteristics of the cloth.[1] Cloth is usually woven on a loom, a device that holds the warp threads in place while filling threads are woven through them. A fabric band which meets this definition of cloth (warp threads with a weft thread winding between) can also be made using other methods, including tablet weaving, back strap loom, or other techniques without looms.[2]
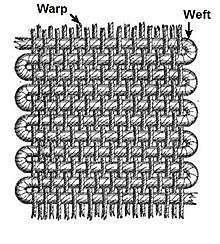
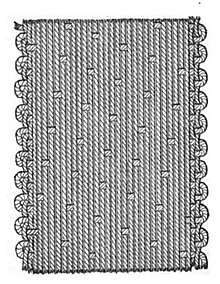
The way the warp and filling threads interlace with each other is called the weave. The majority of woven products are created with one of three basic weaves: plain weave, satin weave, or twill. Woven cloth can be plain (in one colour or a simple pattern), or can be woven in decorative or artistic design.
Process and terminology
In general, weaving involves using a loom to interlace two sets of threads at right angles to each other: the warp which runs longitudinally and the weft (older woof) that crosses it. One warp thread is called an end and one weft thread is called a pick. The warp threads are held taut and in parallel to each other, typically in a loom. There are many types of looms.[3]
Weaving can be summarized as a repetition of these three actions, also called the primary motions of the loom.
- Shedding: where the warp threads (ends) are separated by raising or lowering heald frames (heddles) to form a clear space where the pick can pass
- Picking: where the weft or pick is propelled across the loom by hand, an air-jet, a rapier or a shuttle
- Beating-up or battening: where the weft is pushed up against the fell of the cloth by the reed[4]
The warp is divided into two overlapping groups, or lines (most often adjacent threads belonging to the opposite group) that run in two planes, one above another, so the shuttle can be passed between them in a straight motion. Then, the upper group is lowered by the loom mechanism, and the lower group is raised (shedding), allowing to pass the shuttle in the opposite direction, also in a straight motion. Repeating these actions form a fabric mesh but without beating-up, the final distance between the adjacent wefts would be irregular and far too large.
The secondary motions of the loom are the:
- Let off motion: where the warp is let off the warp beam at a regulated speed to make the filling even and of the required design
- Take up motion: takes up the woven fabric in a regulated manner so that the density of filling is maintained
The tertiary motions of the loom are the stop motions: to stop the loom in the event of a thread break. The two main stop motions are the
- Warp stop motion
- Weft stop motion
The principal parts of a loom are the frame, the warp-beam or weavers beam, the cloth-roll (apron bar), the heddles, and their mounting, the reed. The warp-beam is a wooden or metal cylinder on the back of the loom on which the warp is delivered. The threads of the warp extend in parallel order from the warp-beam to the front of the loom where they are attached to the cloth-roll. Each thread or group of threads of the warp passes through an opening (eye) in a heddle. The warp threads are separated by the heddles into two or more groups, each controlled and automatically drawn up and down by the motion of the heddles. In the case of small patterns the movement of the heddles is controlled by "cams" which move up the heddles by means of a frame called a harness; in larger patterns the heddles are controlled by a dobby mechanism, where the healds are raised according to pegs inserted into a revolving drum. Where a complex design is required, the healds are raised by harness cords attached to a Jacquard machine. Every time the harness (the heddles) moves up or down, an opening (shed) is made between the threads of warp, through which the pick is inserted. Traditionally the weft thread is inserted by a shuttle.[4][5]
On a conventional loom, the weft thread is carried on a pirn, in a shuttle that passes through the shed. A handloom weaver could propel the shuttle by throwing it from side to side with the aid of a picking stick. The "picking" on a power loom is done by rapidly hitting the shuttle from each side using an overpick or underpick mechanism controlled by cams 80–250 times a minute.[4] When a pirn is depleted, it is ejected from the shuttle and replaced with the next pirn held in a battery attached to the loom. Multiple shuttle boxes allow more than one shuttle to be used. Each can carry a different colour which allows banding across the loom.

The rapier-type weaving machines do not have shuttles, they propel the weft by means of small grippers or rapiers that pick up the filling thread and carry it halfway across the loom where another rapier picks it up and pulls it the rest of the way.[6] Some carry the filling yarns across the loom at rates in excess of 2,000 metres per minute. Manufacturers such as Picanol have reduced the mechanical adjustments to a minimum, and control all the functions through a computer with a graphical user interface. Other types use compressed air to insert the pick. They are all fast, versatile and quiet.[7]
The warp is sized in a starch mixture for smoother running. The loom warped (loomed or dressed) by passing the sized warp threads through two or more heddles attached to harnesses. The power weavers loom is warped by separate workers. Most looms used for industrial purposes have a machine that ties new warps threads to the waste of previously used warps threads, while still on the loom, then an operator rolls the old and new threads back on the warp beam. The harnesses are controlled by cams, dobbies or a Jacquard head.

The raising and lowering sequence of warp threads in various sequences gives rise to many possible weave structures:
- Plain weave: plain, and hopsacks, poplin, taffeta,[8] poult-de-soie, pibiones and grosgrain
- Twill weave: these are described by weft float followed by warp float, arranged to give diagonal pattern; examples are 2/1 twill, 3/3 twill, or 1/2 twill. These are softer fabrics than plain weaves.[9]
- Satin weave: satins and sateens[10]
- Complex computer-generated interlacings, such as Jacquard fabric
- Pile fabrics: fabrics with a surface of cut threads (a pile), such as velvets and velveteens[10]
Both warp and weft can be visible in the final product. By spacing the warp more closely, it can completely cover the weft that binds it, giving a warp faced textile such as repp weave.[8] Conversely, if the warp is spread out, the weft can slide down and completely cover the warp, giving a weft faced textile, such as a tapestry or a Kilim rug. There are a variety of loom styles for hand weaving and tapestry.[8]
History
.jpg)
There are some indications that weaving was already known in the Paleolithic Era, as early as 27,000 years ago. An indistinct textile impression has been found at the Dolní Věstonice site.[11] According to the find, the weavers of the Upper Palaeolithic were manufacturing a variety of cordage types, produced plaited basketry and sophisticated twined and plain woven cloth. The artifacts include imprints in clay and burned remnants of cloth.[12]
The oldest known textiles found in the Americas are remnants of six finely woven textiles and cordage found in Guitarrero Cave, Peru. The weavings, made from plant fibres, are dated between 10100 and 9080 BCE.[13][14]
Middle East and Africa
The earliest known Neolithic textile production in the Old World is supported by a 2013 find of a piece of cloth woven from hemp, in burial F. 7121 at the Çatalhöyük site[15] suggested to be from around 7000 B.C.[16][17] Further finds come from the Neolithic civilisation preserved in the pile dwellings in Switzerland.[18] Another extant fragment from the Neolithic was found in Fayum, at a site dated to about 5000 BCE.[19] This fragment is woven at about 12 threads by 9 threads per centimetre in a plain weave. Flax was the predominant fibre in Egypt at this time (3600 BCE) and had continued popularity in the Nile Valley, though wool became the primary fibre used in other cultures around 2000 BCE.[lower-alpha 2] Weaving was known in all the great civilisations, but no clear line of causality has been established. Early looms required two people to create the shed and one person to pass through the filling. Early looms wove a fixed length of cloth, but later ones allowed warp to be wound out as the fell progressed. The weavers were often children or slaves. Weaving became simpler when the warp was sized.
The Americas

The Indigenous people of the Americas wove textiles of cotton throughout tropical and subtropical America and in the South American Andes of wool from camelids, primarily domesticated llamas and alpacas. Cotton and the camelids were both domesticated by about 4,000 BCE.[20][21] American weavers are "credited with independently inventing nearly every non-mechanized technique known today."[22]
In the Inca Empire of the Andes, women did most of the weaving, using backstrap looms to make small pieces of cloth and vertical frame and single-heddle looms for larger pieces.[23] Andean textile weavings were of practical, symbolic, religious, and ceremonial importance and used as currency, tribute, and as a determinant of social class and rank. Sixteenth-century Spanish colonists were impressed by both the quality and quantity of textiles produced by the Inca Empire.[24] Some of the techniques and designs are still in use in the 21st century.[25]
The oldest-known weavings in North America come from the Windover Archaeological Site in Florida. Dating from 4900 to 6500 B.C. and made from plant fibres, the Windover hunter-gatherers produced "finely crafted" twined and plain weave textiles.[26][27]
East Asia
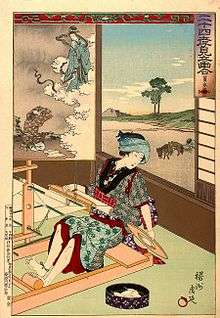
The weaving of silk from silkworm cocoons has been known in China since about 3500 BCE. Silk that was intricately woven and dyed, showing a well developed craft, has been found in a Chinese tomb dating back to 2700 BCE.
Silk weaving in China was an intricate process that was very involved. Men and women, usually from the same family, had their own roles in the weaving process. The actual work of weaving was done by both men and women.[28] Women were often weavers since it was a way they could contribute to the household income while staying at home.[29] Women would usually weave simpler designs within the household while men would be in charge of the weaving of more intricate and complex pieces of clothing.[30] The process of sericulture and weaving emphasized the idea that men and women should work together instead of women being subordinate to men. Weaving became an integral part of Chinese women's social identity. Several rituals and myths were associated with the promotion of silk weaving, especially as a symbol of female power. Weaving contributed to the balance between men and women's economic contributions and had many economic benefits.[29][31]
There were many paths into the occupation of weaver. Women usually married into the occupation, belonged to a family of weavers and or lived in a location that had ample weather conditions that allowed for the process of silk weaving. Weavers usually belonged to the peasant class.[32] Silk weaving became a specialized job requiring specific technology and equipment that was completed domestically within households.[33] Although most of the silk weaving was done within the confines of the home and family, there were some specialized workshops that hired skilled silk weavers as well. These workshops took care of the weaving process, although the raising of the silkworms and reeling of the silk remained work for peasant families. The silk that was woven in workshops rather than homes were of higher quality, since the workshop could afford to hire the best weavers.[34] These weavers were usually men who operated more complicated looms, such as the wooden draw-loom.[35] This created a competitive market of silk weavers.
The quality and ease of the weaving process depended on the silk that was produced by the silk worms. The easiest silk to work with came from breeds of silk worms that spun their cocoons so that it could be unwound in one long strand.[30] The reeling, or unwinding of silk worm cocoons is started by placing the cocoons in boiling water in order to break apart the silk filaments as well as kill the silk worm pupae. Women would then find the end of the strands of silk by sticking their hand into the boiling water. Usually this task was done by girls aged eight to twelve, while the more complex jobs were given to older women.[36] They would then create a silk thread, which could vary in thickness and strength from the unwound cocoons.[30]
After the reeling of the silk, the silk would be dyed before the weaving process began. There were many different looms and tools for weaving. For high quality and intricate designs, a wooden draw-loom or pattern loom was used.[35] This loom would require two or three weavers and was usually operated by men. There were also other smaller looms, such as the waist loom, that could be operated by a single woman and were usually used domestically.[35]
Sericulture and silk weaving spread to Korea by 200 BCE, to Khotan by 50 CE, and to Japan by about 300 CE.
The pit-treadle loom may have originated in India though most authorities establish the invention in China.[37] Pedals were added to operate heddles. By the Middle Ages such devices also appeared in Persia, Sudan, Egypt and possibly the Arabian Peninsula, where "the operator sat with his feet in a pit below a fairly low-slung loom". In 700 CE, horizontal looms and vertical looms could be found in many parts of Asia, Africa and Europe. In Africa, the rich dressed in cotton while the poorer wore wool.[38] By the 12th century it had come to Europe either from the Byzantium or Moorish Spain where the mechanism was raised higher above the ground on a more substantial frame.[38][39]
Southeast Asia
In the Philippines, numerous pre-colonial weaving traditions exist among different ethnic groups. They used various plant fibers, mainly abacá or banana, but also including tree cotton, buri palm (locally known as buntal) and other palms, various grasses (like amumuting and tikog), and barkcloth.[40][41] The oldest evidence of weaving traditions are Neolithic stone tools used for preparing barkcloth found in archeological sites in Sagung Cave of southern Palawan and Arku Cave of Peñablanca, Cagayan. The latter has been dated to around 1255–605 BCE.[42]
Medieval Europe
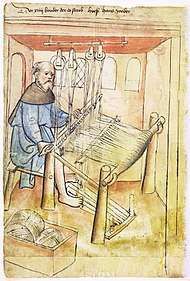
The predominant fibre was wool, followed by linen and nettlecloth for the lower classes. Cotton was introduced to Sicily and Spain in the 9th century. When Sicily was captured by the Normans, they took the technology to Northern Italy and then the rest of Europe. Silk fabric production was reintroduced towards the end of this period and the more sophisticated silk weaving techniques were applied to the other staples.[43]
The weaver worked at home and marketed his cloth at fairs.[43] Warp-weighted looms were commonplace in Europe before the introduction of horizontal looms in the 10th and 11th centuries. Weaving became an urban craft and to regulate their trade, craftsmen applied to establish a guild. These initially were merchant guilds, but developed into separate trade guilds for each skill. The cloth merchant who was a member of a city's weavers guild was allowed to sell cloth; he acted as a middleman between the tradesmen weavers and the purchaser. The trade guilds controlled quality and the training needed before an artisan could call himself a weaver.[43]
By the 13th century, an organisational change took place, and a system of putting out was introduced. The cloth merchant purchased the wool and provided it to the weaver, who sold his produce back to the merchant. The merchant controlled the rates of pay and economically dominated the cloth industry.[43] The merchants' prosperity is reflected in the wool towns of eastern England; Norwich, Bury St Edmunds and Lavenham being good examples. Wool was a political issue.[44] The supply of thread has always limited the output of a weaver. About that time, the spindle method of spinning was replaced by the great wheel and soon after the treadle-driven spinning wheel. The loom remained the same but with the increased volume of thread it could be operated continuously.[43]
The 14th century saw considerable flux in population. The 13th century had been a period of relative peace; Europe became overpopulated. Poor weather led to a series of poor harvests and starvation. There was great loss of life in the Hundred Years War. Then in 1346, Europe was struck with the Black Death and the population was reduced by up to a half. Arable land was labour-intensive and sufficient workers no longer could be found. Land prices dropped, and land was sold and put to sheep pasture. Traders from Florence and Bruges bought the wool, then sheep-owning landlords started to weave wool outside the jurisdiction of the city and trade guilds. The weavers started by working in their own homes then production was moved into purpose-built buildings. The working hours and the amount of work were regulated. The putting-out system had been replaced by a factory system.[43]
The migration of the Huguenot Weavers, Calvinists fleeing from religious persecution in mainland Europe, to Britain around the time of 1685 challenged the English weavers of cotton, woollen and worsted cloth, who subsequently learned the Huguenots' superior techniques.[45]
Industrial Revolution

Before the Industrial Revolution, weaving was a manual craft and wool was the principal staple. In the great wool districts a form of factory system had been introduced but in the uplands weavers worked from home on a putting-out system. The wooden looms of that time might be broad or narrow; broad looms were those too wide for the weaver to pass the shuttle through the shed, so that the weaver needed an expensive assistant (often an apprentice). This ceased to be necessary after John Kay invented the flying shuttle in 1733. The shuttle and the picking stick sped up the process of weaving.[46] There was thus a shortage of thread or a surplus of weaving capacity. The opening of the Bridgewater Canal in June 1761 allowed cotton to be brought into Manchester, an area rich in fast flowing streams that could be used to power machinery. Spinning was the first to be mechanised (spinning jenny, spinning mule), and this led to limitless thread for the weaver.
Edmund Cartwright first proposed building a weaving machine that would function similar to recently developed cotton-spinning mills in 1784, drawing scorn from critics who said the weaving process was too nuanced to automate.[47] He built a factory at Doncaster and obtained a series of patents between 1785 and 1792. In 1788, his brother Major John Cartwight built Revolution Mill at Retford (named for the centenary of the Glorious Revolution). In 1791, he licensed his loom to the Grimshaw brothers of Manchester, but their Knott Mill burnt down the following year (possibly a case of arson). Edmund Cartwight was granted a reward of £10,000 by Parliament for his efforts in 1809.[48][49] However, success in power-weaving also required improvements by others, including H. Horrocks of Stockport. Only during the two decades after about 1805, did power-weaving take hold. At that time there were 250,000 hand weavers in the UK.[50] Textile manufacture was one of the leading sectors in the British Industrial Revolution, but weaving was a comparatively late sector to be mechanised. The loom became semi-automatic in 1842 with Kenworthy and Bulloughs Lancashire Loom. The various innovations took weaving from a home-based artisan activity (labour-intensive and man-powered) to steam driven factories process. A large metal manufacturing industry grew to produce the looms, firms such as Howard & Bullough of Accrington, and Tweedales and Smalley and Platt Brothers. Most power weaving took place in weaving sheds, in small towns circling Greater Manchester away from the cotton spinning area. The earlier combination mills where spinning and weaving took place in adjacent buildings became rarer. Wool and worsted weaving took place in West Yorkshire and particular Bradford, here there were large factories such as Lister's or Drummond's, where all the processes took place.[51] Both men and women with weaving skills emigrated, and took the knowledge to their new homes in New England, to places like Pawtucket and Lowell.
Woven 'grey cloth' was then sent to the finishers where it was bleached, dyed and printed. Natural dyes were originally used, with synthetic dyes coming in the second half of the 19th century. The need for these chemicals was an important factor in the development of the chemical industry.
The invention in France of the Jacquard loom in about 1803, enabled complicated patterned cloths to be woven, by using punched cards to determine which threads of coloured yarn should appear on the upper side of the cloth. The jacquard allowed individual control of each warp thread, row by row without repeating, so very complex patterns were suddenly feasible. Samples exist showing calligraphy, and woven copies of engravings. Jacquards could be attached to handlooms or powerlooms.
A distinction can be made between the role and lifestyle and status of a handloom weaver, and that of the power loom weaver and craft weaver. The perceived threat of the power loom led to disquiet and industrial unrest. Well known protests movements such as the Luddites and the Chartists had handloom weavers amongst their leaders. In the early 19th-century power weaving became viable. Richard Guest in 1823 made a comparison of the productivity of power and handloom weavers:
A very good Hand Weaver, a man twenty-five or thirty years of age, will weave two pieces of nine-eighths shirting per week, each twenty-four yards long, and containing one hundred and five shoots of weft in an inch, the reed of the cloth being a forty-four, Bolton count, and the warp and weft forty hanks to the pound, A Steam Loom Weaver, fifteen years of age, will in the same time weave seven similar pieces.[52]
He then speculates about the wider economics of using power loom weavers:
...it may very safely be said, that the work is done in a Steam Factory containing two hundred Looms, would, if done by hand Weavers, find employment and support for a population of more than two thousand persons.[53]
Hand loom weavers
Handloom weaving was done by both genders but men outnumbered women partially due to the strength needed to batten.[54][55] They worked from home sometimes in a well-lit attic room. The women of the house would spin the thread they needed, and attend to finishing. Later women took to weaving, they obtained their thread from the spinning mill, and working as outworkers on a piecework contract. Over time competition from the power looms drove down the piece rate and they existed in increasing poverty.
Power loom weavers
Power loom workers were usually girls and young women. They had the security of fixed hours, and except in times of hardship, such as in the cotton famine, regular income. They were paid a wage and a piece work bonus. Even when working in a combined mill, weavers stuck together and enjoyed a tight-knit community.[56] The women usually minded the four machines and kept the looms oiled and clean. They were assisted by 'little tenters', children on a fixed wage who ran errands and did small tasks. They learnt the job of the weaver by watching.[55] Often they would be half timers, carrying a green card which teacher and overlookers would sign to say they had turned up at the mill in the morning and the afternoon at the school.[57] At fourteen or so they come full-time into the mill, and started by sharing looms with an experienced worker where it was important to learn quickly as they would both be on piece work.[58] Serious problems with the loom were left to the tackler to sort out. He would inevitably be a man, as were usually the overlookers. The mill had its health and safety issues, there was a reason why the women tied their hair back with scarves. Inhaling cotton dust caused lung problems, and the noise was causing total hearing loss. Weavers would mee-maw[59][60] as normal conversation was impossible. Weavers used to 'kiss the shuttle', that is, suck thread through the eye of the shuttle. This left a foul taste in the mouth due to the oil, which was also carcinogenic.[61]
Craft weavers

Arts and Crafts was an international design philosophy that originated in England[62] and flourished between 1860 and 1910 (especially the second half of that period), continuing its influence until the 1930s.[63] Instigated by the artist and writer William Morris (1834–1896) during the 1860s[62] and inspired by the writings of John Ruskin (1819–1900), it had its earliest and most complete development in the British Isles[63] but spread to Europe and North America.[64] It was largely a reaction against mechanisation and the philosophy advocated of traditional craftsmanship using simple forms and often medieval, romantic or folk styles of decoration. Handweaving was highly regarded and taken up as a decorative art.
Bauhaus weaving workshop
In the 1920s the weaving workshop of the Bauhaus design school in Germany aimed to raise weaving, previously seen as a craft, to a fine art, and also to investigate the industrial requirements of modern weaving and fabrics.[65] Under the direction of Gunta Stölzl, the workshop experimented with unorthodox materials, including cellophane, fibreglass, and metal.[66] From expressionist tapestries to the development of soundproofing and light-reflective fabric, the workshop's innovative approach instigated a modernist theory of weaving.[66] Former Bauhaus student and teacher Anni Albers published the seminal 20th-century text On Weaving in 1965.[67] Other notables from the Bauhaus weaving workshop include Otti Berger, Margaretha Reichardt, and Benita Koch-Otte.
Other cultures
Weaving in the American Colonies (1500–1800)
Colonial America relied heavily on Great Britain for manufactured goods of all kinds. British policy was to encourage the production of raw materials in colonies and discourage manufacturing. The Wool Act 1699 restricted the export of colonial wool.[68][69] As a result, many people wove cloth from locally produced fibres. The colonists also used wool, cotton and flax (linen) for weaving, though hemp could be made into serviceable canvas and heavy cloth. They could get one cotton crop each year; until the invention of the cotton gin it was a labour-intensive process to separate the seeds from the fibres.
A plain weave was preferred as the added skill and time required to make more complex weaves kept them from common use. Sometimes designs were woven into the fabric but most were added after weaving using wood block prints or embroidery.
American Southwest

Textile weaving, using cotton dyed with pigments, was a dominant craft among pre-contact tribes of the American southwest, including various Pueblo peoples, the Zuni, and the Ute tribes. The first Spaniards to visit the region wrote about seeing Navajo blankets. With the introduction of Navajo-Churro sheep, the resulting woolen products have become very well known. By the 18th century the Navajo had begun to import yarn with their favorite color, Bayeta red. Using an upright loom, the Navajos wove blankets worn as garments and then rugs after the 1880s for trade. Navajo traded for commercial wool, such as Germantown, imported from Pennsylvania. Under the influence of European-American settlers at trading posts, Navajos created new and distinct styles, including "Two Gray Hills" (predominantly black and white, with traditional patterns), "Teec Nos Pos" (colorful, with very extensive patterns), "Ganado" (founded by Don Lorenzo Hubbell), red dominated patterns with black and white, "Crystal" (founded by J. B. Moore), Oriental and Persian styles (almost always with natural dyes), "Wide Ruins," "Chinlee," banded geometric patterns, "Klagetoh," diamond type patterns, "Red Mesa" and bold diamond patterns. Many of these patterns exhibit a fourfold symmetry, which is thought to embody traditional ideas about harmony, or hózhó.
Amazon cultures
Among the indigenous people of the Amazon basin densely woven palm-bast mosquito netting, or tents, were utilized by the Panoans, Tupinambá, Western Tucano, Yameo, Záparoans, and perhaps by the indigenous peoples of the central Huallaga River basin (Steward 1963:520). Aguaje palm-bast (Mauritia flexuosa, Mauritia minor, or swamp palm) and the frond spears of the Chambira palm (Astrocaryum chambira, A.munbaca, A.tucuma, also known as Cumare or Tucum) have been used for centuries by the Urarina of the Peruvian Amazon to make cordage, net-bags hammocks, and to weave fabric. Among the Urarina, the production of woven palm-fiber goods is imbued with varying degrees of an aesthetic attitude, which draws its authentication from referencing the Urarina's primordial past. Urarina mythology attests to the centrality of weaving and its role in engendering Urarina society. The post-diluvial creation myth accords women's weaving knowledge a pivotal role in Urarina social reproduction. [70] Even though palm-fiber cloth is regularly removed from circulation through mortuary rites, Urarina palm-fiber wealth is neither completely inalienable, nor fungible since it is a fundamental medium for the expression of labor and exchange. The circulation of palm-fiber wealth stabilizes a host of social relationships, ranging from marriage and fictive kinship (compadrazco, spiritual compeership) to perpetuating relationships with the deceased.[71]
Computer science
The Nvidia Parallel Thread Execution ISA derives some terminology (specifically the term Warp to refer to a group of concurrent processing threads) from historical weaving traditions.[72]
See also
- Basket weaving
- Persian weave
- Petate
- Textile manufacturing terminology
- Weaving (mythology)
Notes
- deriving from an obsolete past participle of weave (Oxford English Dictionary, see "weft" and "weave".
- Easton's Bible Dictionary (1897) refers to numerous Biblical references to weaving:
Weaving was an art practised in very early times (Ex 35:35). The Egyptians were specially skilled in it (Isa 19:9; Ezek 27:7), and some have regarded them as its inventors.
In the wilderness, the Hebrews practised weaving (Ex 26:1, 26:8; 28:4, 28:39; Lev 13:47). It is referred to subsequently as specially the women's work (2 Kings 23:7; Prov 31:13, 24). No mention of the loom is found in Scripture, but we read of the "shuttle" (Job 7:6), "the pin" of the beam (Judg 16:14), "the web" (13, 14), and "the beam" (1 Sam 17:7; 2 Sam 21:19). The rendering, "with pining sickness," in Isa. 38:12 (A.V.) should be, as in the Revised Version, "from the loom," or, as in the margin, "from the thrum." We read also of the "warp" and "woof" (Lev. 13:48, 49, 51–53, 58, 59), but the Revised Version margin has, instead of "warp," "woven or knitted stuff."
References
- Collier 1974, p. 92.
- Dooley 1914.
- Collier 1974, p. 102.
- Collier 1974, p. 104.
- Dooley 1914, p. 54.
- Collier 1974, p. 110.
- "Cotton: From Field to Fabric" (PDF). Memphis, Tennessee: Cotton Counts. Retrieved 31 October 2011.
- Collier 1974, p. 114.
- Collier 1974, p. 115.
- Collier 1974, p. 116.
- "Dolni Vestonice and Pavlov sites". Donsmaps.com. Retrieved 26 April 2016.
- "BBC News - SCI/TECH - Woven cloth dates back 27,000 years". news.bbc.co.uk.
- Stacey, Kevin (13 April 2011). "Carbon dating identifies South America's oldest textiles". University of Chicago Press Journals. Retrieved 6 October 2016.
- Jolie, Edward A.; Lynch, Thomas F.; Geib, Phil R.; Adovasio, J. M. (2011). "Cordage, Textiles, and the Late Pleistocene Peopling of the Andes". Current Anthropology. 52 (2): 285–296. doi:10.1086/659336.
- Hodder, Ian (2013). "2013 Season Review" (PDF). Çatal Newsletter. pp. 1–2. Archived from the original (PDF) on 13 April 2015. Retrieved 7 February 2014.
- "Pavlov VI: an Upper Palaeolithic living unit | Miriam Nývltová Fišáková". Academia.edu. 1 January 1970. Retrieved 26 April 2016.
- "Centuries-old fabric found in Çatalhöyük". hurriyet daily news. 3 February 2014. Retrieved 7 February 2014.
- Barber, E. J. W. (1991). Prehistoric Textiles: The Development of Cloth in the Neolithic and Bronze Ages with Special Reference to the Aegean. Princeton University Press. pp. 97, 134. ISBN 9780691002248. Retrieved 30 August 2019.
- "Woven linen". University College London. 2003. Retrieved 19 March 2015.
- Rajpal, Vijay Rani; Rao, S. Rama; Raina, S. N. (2016). Gene Pool Diversity and Crop Improvement. Switzerland: Springer International Publishing. p. 117.
- Hirst, K. Kris (29 September 2014). "The History of Llamas and Alpacas in South America". ThoughtCo. Retrieved 6 October 2016.
- Stanfield-Mazzi, Maya (2012). "Textile Traditions of the Andes". Retrieved 6 October 2016.
- McEwam, Gordon F. (2006). The Incas: New Perspectives. New York: W. W. Norton & Co. p. 167; Cartwright, Mark (1 February 2015). "Inca Textiles". Ancient History Encyclopedia. Retrieved 7 October 2016.
- Morris, Craig; Von Hagen, Adriana (1993). The Inka Empire and its Andean Origins. American Museum of Natural History. New York: Abbeville Press. pp. 185-191.
- Meisch, Lynn A. "The Murúa Code". Natural History Magazine. Retrieved 7 October 2016.
- Spike, Tamara (July 2003). "Review of Doran, Glen H., ed. Windover: Multidisciplinary Investagations of an Early Archaic Florida Cemetery". H-Net Reviews. H. Florida. Retrieved 7 October 2016.
- Tyson, Peter (6 February 2006). "America's Bog People". NOVA. Retrieved 7 October 2016.
- Feng 2001, p. 385.
- Rothschild, Harry (2015). Emperor Wu Zhao and Her Pantheon of Devis, Divinities, and Dynastic Mothers. Columbia University Press. p. 72.
- Netherton, Robin; Owen-Crocker, Gale R. (2013). "Robin Netherton and Gale R. Owen-Crocker, eds., Medieval Clothing and Textiles 8. Woodbridge, Suffolk, UK: Boydell Press, 2012. Pp. 197. $60". Speculum. 88 (2): 608. doi:10.1017/s0038713413001814. ISBN 9781843837367. ISSN 0038-7134.
- Li 1981, p. 135.
- Feng 2001, pp. 407–409.
- Li 1981, p. 131.
- Bell, Lynda Schaefer (2000). "Of Silk, Women, and Capital: Peasant Women's Labor in Chinese and Other Third World Capitalisms". Journal of Women's History. 11 (4): 83. doi:10.1353/jowh.2000.0002. ISSN 1527-2036.
- Li 1981, p. 27.
- Li 1981, p. 29.
- Broudy, Eric (1979). The Book of Looms: A History of the Handloom from Ancient Times to the Present. University Press of New England. pp. 111–112. ISBN 978-0874516494.
- Pacey, Arnold (1991). Technology in world civilization: a thousand-year history. MIT Press. pp. 40–1. ISBN 0-262-66072-5.
- Jenkins, D.T., ed. (2003). The Cambridge History of Western Textiles, Volume 1. Cambridge University Press. p. 194. ISBN 978-0521341073.
- Sorilla, Franz, IV. "Weaving the Threads of Filipino Heritage". Philippine Tatler. Retrieved 12 December 2018.
- Perez, Tina (16 February 2017). "Puerto Princesa: City in a Forest". Mrs. Wise. Retrieved 13 December 2018.
- "Bark-Cloth Beater". National Museum Collections. National Museum of the Philippines. Retrieved 12 December 2018.
- Backer 2005.
- Unwin, George, ed. (1918). "The estate of merchants, 1336–1365: IV – 1355–65". Finance and trade under Edward III: The London lay subsidy of 1332. Institute of Historical Research. Retrieved 18 November 2011.
- Page, William, ed. (1911). "Industries: Silk-weaving". A History of the County of Middlesex: Volume 2: General; Ashford, East Bedfont with Hatton, Feltham, Hampton with Hampton Wick, Hanworth, Laleham, Littleton. Institute of Historical Research. Retrieved 18 November 2011.
- Guest 1823, p. 8.
- "Historic Figures: Edmund Cartwright". BBC.
- English, W. (1969). The Textile Industry. pp. 89–97.
- Chaloner, William Henry (1963). People and Industries. pp. 45–54.
- Timmins 1993.
- Bellerby 2005, p. 17.
- Guest 1823, p. 47.
- Guest 1823, p. 48.
- Burnette, Joyce (26 March 2008). "Women Workers in the British Industrial Revolution". EH.net. Retrieved 15 April 2019.
- Freethy 2005, p. 62.
- Bellerby 2005, p. 24.
- Freethy 2005, p. 86.
- Freethy 2005, p. 70.
- Freethy 2005, p. 123.
- Bellerby 2005, p. 48.
- Freethy 2005, p. 121.
- Triggs, Oscar Lovell (1902). Chapters in the History of the Arts and Crafts Movement. Bohemia Guild of the Industrial Art League. Retrieved 2010-08-28.
Chapters in the History of the Arts and Crafts Movement.
- Campbell, Gordon (2006). The Grove Encyclopedia of Decorative Arts, Volume 1. Oxford University Press. ISBN 978-0-19-518948-3.
- Kaplan, Wendy; Crawford, Alan (2004). The Arts & Crafts Movement in Europe & America: Design for the Modern World. Los Angeles County Museum of Art.
- Smith, T'ai (2014). Bauhaus weaving theory: From feminine craft to mode of design. Minnesota: University of Minnesota Press.
- Winton, A.G. (2007). "The Bauhaus, 1919–1933". Heilbrunn Timeline of Art History. Metropolitan Museum of Art. Retrieved 11 December 2016.
- Albers, Anni (1965). On Weaving. Middletown, Connecticut: Wesleyan University Press.
- "An Act for continuing severall Laws therein mentioned, and for explaining the Act intituled An Act to prevent the Exportation of Wooll out of the Kingdoms of Ireland and England into Forreigne Parts and for the Incouragement of the Woollen Manufactures in the Kingdom of England". Statutes of the Realm, 1695–1701, vol. 7. 1820. pp. 600–02. Retrieved 16 February 2007.
- Garraty, John A.; Carnes, Mark C. (2000). "Chapter Three: America in the British Empire". A Short History of the American Nation (8th ed.). Longman. ISBN 0-321-07098-4.
- Dean, Bartholomew (2009). Urarina Society, Cosmology, and History in Peruvian Amazonia. Gainesville: University Press of Florida. ISBN 978-0-8130-3378-5
- Dean, Bartholomew (1994). "Multiple Regimes of Value: Unequal Exchange and the Circulation of Urarina Palm-Fiber Wealth". Museum Anthropology. 18: 3–20. doi:10.1525/mua.1994.18.1.3.
- "Parallel Thread Execution ISA Version 6.0". Developer Zone: CUDA Toolkit Documentation. NVIDIA Corporation. 22 September 2017. Archived from the original on 28 October 2017. Retrieved 27 October 2017.
Bibliography
- Backer, Patricia (10 June 2005). Technology in the Middle Ages, History of Technology. Technology and Civilization (Tech 198). San Jose, California, USA: San Jose State University. Retrieved 18 November 2011.CS1 maint: ref=harv (link)
- Bellerby, Rachel (2005). Chasing the Sixpence: The lives of Bradford Mill Folk. Ayr: Fort Publishing Ltd. ISBN 0-9547431-8-0.CS1 maint: ref=harv (link)
- Collier, Ann M (1974), A Handbook of Textiles, Pergamon Press, p. 258, ISBN 0-08-018057-4
- Dooley, William H. (1914). Textiles (Project Gutenberg ed.). Boston, USA: D.C. Heath and Co. Retrieved 30 October 2011.CS1 maint: ref=harv (link)
- Feng, Menglong (November 2001). "Stories Old and New. By Feng Menglong, translated by Shuhui Yang and Yunqin Yang. pp. 794, 10 illus. from the 1620 edition. Seattle, University of Washington Press, 2000". Journal of the Royal Asiatic Society. 11 (3): 407–409. doi:10.1017/s1356186301380343. ISSN 1356-1863.CS1 maint: ref=harv (link)
- Freethy, Ron (2005). Memories of the Lancashire Cotton Mills. Aspects of Local History. Newbury, Berkshire: Countryside Books. ISBN 978-1-84674-104-3.CS1 maint: ref=harv (link)
- Guest, Richard (1823). A compendious history of the cotton-manufacture. Manchester: Author, Printed by Joseph Pratt, Chapel Walks. Retrieved 2011-11-23.CS1 maint: ref=harv (link)
- Li, Lillian M. (1981). China's silk trade: traditional industry in the modern world, 1842–1937. 97 (1st ed.). Cambridge, Mass.: Council on East Asian Studies, Harvard University. ISBN 9780674119628. JSTOR j.ctt1tfjb18. OCLC 576853423.CS1 maint: ref=harv (link)
- Timmins, Geoffrey (1993). The last shift: the decline of handloom weaving in nineteenth-century Lancashire. Manchester University Press ND. ISBN 0-7190-3725-5.CS1 maint: ref=harv (link)
- This article incorporates text from Textiles by William H. Dooley, Boston, D.C. Heath and Co., 1914, a volume in the public domain and available online from Project Gutenberg
External links
Media related to Weaving at Wikimedia Commons- Cole, Alan Summerly (1911). Encyclopædia Britannica. 28 (11th ed.). pp. 440–455. .
- Resource collection An on-line repository of articles (4720), books (459), illustrations (271), patents (398) and periodicals (1322) relating to weaving.
- British Pathé Weaving Linen 1940-1949 Educational film
- Illustrated Guide of Tilling and Weaving: Rural Life in China from 1696