Rebreather
A rebreather is a breathing apparatus that absorbs the carbon dioxide of a user's exhaled breath to permit the rebreathing (recycling) of the substantially unused oxygen content, and unused inert content when present, of each breath. Oxygen is added to replenish the amount metabolised by the user. This differs from open-circuit breathing apparatus, where the exhaled gas is discharged directly into the environment. The purpose is to extend the breathing endurance of a limited gas supply, and, for covert military use by frogmen or observation of underwater life, eliminating the bubbles produced by an open circuit system. A rebreather is generally understood to be a portable unit carried by the user. The same technology on a vehicle or non-mobile installation is more likely to be referred to as a life-support system.
![]() A fully closed circuit electronic rebreather (AP Diving Inspiration) | |
Acronym | CCUBA (closed circuit underwater breathing apparatus); CCR (closed circuit rebreather), SCR (semi-closed rebreather) |
---|---|
Uses | Breathing set |
Related items | Davis apparatus |
Rebreather technology may be used where breathing gas supply is limited, such as underwater or in space, where the environment is toxic or hypoxic, as in firefighting, mine rescue and high-altitude operations, or where the breathing gas is specially enriched or contains expensive components, such as helium diluent or anaesthetic gases.
Rebreathers are used in many environments: Underwater, diving rebreathers are a type of self-contained underwater breathing apparatus which have applications for primary and emergency gas supply. On land they are used in industrial applications where poisonous gases may be present or oxygen may be absent, firefighting, where firefighters may be required to operate in an IDLH atmosphere for extended periods, and in hospital anaesthesia breathing systems to supply controlled concentrations of anaesthetic gases to patients without contaminating the air that the staff breathe, and at high altitude, where the partial pressure of oxygen is low, for high altitude mountaineering. In aerospace there are applications in unpressurised aircraft and for high altitude parachute drops, and off-planet, in space suits for extra-vehicular activity. Similar technology is used in life support systems in submarines, submersibles, underwater and surface saturation habitats, spacecraft, and space stations.
The recycling of breathing gas comes at the cost of technological complexity and specific hazards, which depend on the specific application and type of rebreather used. Mass and bulk may be greater or less than open circuit depending on circumstances. Electronically controlled diving rebreathers may automatically maintain a partial pressure of oxygen between programmable upper and lower limits, or set points, and be integrated with decompression computers to monitor the decompression status of the diver and record the dive profile.
General concept
As a person breathes, the body consumes oxygen and produces carbon dioxide. Base metabolism requires about 0.25 L/min of oxygen from a breathing rate of about 6 L/min, and a fit person working hard may ventilate at a rate of 95 L/min but will only metabolise about 4 L/min of oxygen [1] The oxygen metabolised is generally about 4% to 5% of the inspired volume at normal atmospheric pressure, or about 20% of the available oxygen in the air at sea level. Exhaled air at sea level contains roughly 13.5% to 16% oxygen.[2]
The situation is even more wasteful of oxygen when the oxygen fraction of the breathing gas is higher, and in underwater diving, the compression of breathing gas due to depth makes the recirculation of exhaled gas even more desirable, as an even larger proportion of open circuit gas is wasted. Continued rebreathing of the same gas will deplete the oxygen to a level which will no longer support consciousness, and eventually life, so gas containing oxygen must be added to the breathing gas to maintain the required concentration of oxygen.
However, if this is done without removing the carbon dioxide, it will rapidly build up in the recycled gas, resulting almost immediately in mild respiratory distress, and rapidly developing into further stages of hypercapnia, or carbon dioxide toxicity. A high ventilation rate is usually necessary to eliminate the metabolic product carbon dioxide (CO2). The breathing reflex is triggered by CO2 concentration in the blood, not by the oxygen concentration, so even a small buildup of CO2 in the inhaled gas quickly becomes intolerable; if a person tries to directly rebreathe their exhaled breathing gas, they will soon feel an acute sense of suffocation, so rebreathers must chemically remove the CO2 in a component known as a carbon dioxide scrubber.
By adding sufficient oxygen to compensate for the metabolic usage, removing the carbon dioxide, and rebreathing the gas, most of the volume is conserved.
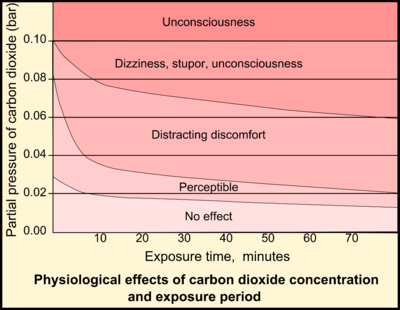
PO2 (bar) |
Application and effect |
---|---|
<0.08 | Coma ultimately leading to death |
0.08-0.10 | Unconsciousness in most people |
0.09-0.10 | Serious signs/symptoms of hypoxia |
0.14-0.16 | Initial signs/symptoms of hypoxia (normal environment oxygen in some very high altitude areas) |
0.21 | Normal environment oxygen (sea level air) |
0.35–0.40 | Normal saturation dive PO2 level |
0.50 | Threshold for whole-body effects; maximum saturation dive exposure |
1.0–1.20 | Common range for recreational closed circuit set point |
1.40 | Recommended limit for recreational open circuit bottom sector |
1.60 | NOAA limit for maximum exposure for a working diver Recreational/technical limit for decompression |
2.20 | Commercial/military "Sur-D" chamber surface decompression on 100% O2 at 12 msw |
2.40 | 40% O2 nitrox recompression treatment gas for use in the chamber at 50 msw (meters of sea water) |
2.80 | 100% O2 recompression treatment gas for use in the chamber at 18 msw |
3.00 | 50% O2 nitrox recompression treatment gas for use in the chamber at 50 msw |
History
Early history
Around 1620, in England, Cornelius Drebbel made an early oar-powered submarine. To re-oxygenate the air inside it, he likely generated oxygen by heating saltpetre (potassium nitrate) in a metal pan to emit oxygen. Heating turns the saltpetre into potassium oxide or hydroxide, which absorbs carbon dioxide from the air. That may explain why Drebbel's men were not affected by carbon dioxide build-up as much as would be expected. If so, he accidentally made a crude rebreather more than two centuries before Saint Simon Sicard's patent.[5]
The first basic rebreather based on carbon dioxide absorption was patented in France in 1808 by Pierre-Marie Touboulic from Brest, a mechanic in Napoleon's Imperial Navy. This early rebreather design worked with an oxygen reservoir, the oxygen being delivered progressively by the diver and circulating in a closed circuit through a sponge soaked in limewater.[6] Touboulic called his invention Ichtioandre (Greek for 'fish-man').[7] There is no evidence of a prototype having been manufactured.
A prototype rebreather was built in 1849 by Pierre Aimable De Saint Simon Sicard,[8] and in 1853 by Professor T. Schwann in Belgium.[9] It had a large back mounted oxygen tank with working pressure of about 13.3 bar, and two scrubbers containing sponges soaked in a caustic soda solution.
Modern rebreathers
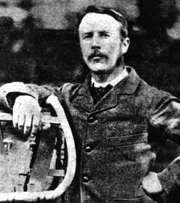
The first commercially practical closed-circuit scuba was designed and built by the diving engineer Henry Fleuss in 1878, while working for Siebe Gorman in London.[10][11] His self-contained breathing apparatus consisted of a rubber mask connected to a breathing bag, with (estimated) 50–60% O2 supplied from a copper tank and CO2 scrubbed by rope yarn soaked in a solution of caustic potash; the system giving a duration of about three hours.[11][12] Fleuss tested his device in 1879 by spending an hour submerged in a water tank, then one week later by diving to a depth of 5.5 m in open water, upon which occasion he was slightly injured when his assistants abruptly pulled him to the surface.
His apparatus was first used under operational conditions in 1880 by Alexander Lambert, the lead diver on the Severn Tunnel construction project, who was able to travel 1000 feet in the darkness to close several submerged sluice doors in the tunnel; this had defeated his best efforts with standard diving dress due to the danger of the air supply hose becoming fouled on submerged debris, and the strong water currents in the workings.[11]
Fleuss continually improved his apparatus, adding a demand regulator and tanks capable of holding greater amounts of oxygen at higher pressure. Sir Robert Davis, head of Siebe Gorman, improved the oxygen rebreather in 1910[11][12] with his invention of the Davis Submerged Escape Apparatus, the first practical rebreather to be made in quantity. While intended primarily as an emergency escape apparatus for submarine crews, it was soon also used for diving, being a handy shallow water diving apparatus with a thirty-minute endurance,[12] and as an industrial breathing set.
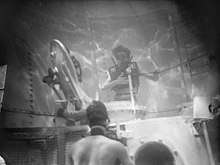
The rig comprised a rubber breathing/buoyancy bag containing a canister of barium hydroxide to scrub exhaled CO2 and, in a pocket at the lower end of the bag, a steel pressure cylinder holding approximately 56 litres of oxygen at a pressure of 120 bar. The cylinder was equipped with a control valve and was connected to the breathing bag. Opening the cylinder's valve admitted oxygen to the bag and charged it to the pressure of the surrounding water. The rig also included an emergency buoyancy bag on the front of to help keep the wearer afloat. The DSEA was adopted by the Royal Navy after further development by Davis in 1927.[13] Various industrial oxygen rebreathers such as the Siebe Gorman Salvus and the Siebe Gorman Proto, both invented in the early 1900s, were derived from it.
Professor Georges Jaubert invented the chemical compound Oxylithe in 1907. It was a form of sodium peroxide (Na2O2) or sodium superoxide (NaO2). As it absorbs carbon dioxide in a rebreather's scrubber it emits oxygen. This compound was first incorporated into a rebreather design by Captain S.S. Hall and Dr. O. Rees of the Royal Navy in 1909. Although intended for use as a submarine escape apparatus, it was never accepted by the Royal Navy and was instead used for shallow water diving.[12]
In 1912 the German firm Dräger began mass production of their own version of standard diving dress with the air supply from a rebreather. The apparatus had been invented some years earlier by Hermann Stelzner, an engineer at the Dräger company,[14] for mine rescue.[15]
Rebreathers during World War II
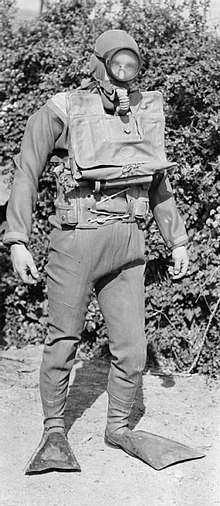
In the 1930s, Italian sport spearfishers began to use the Davis rebreather; Italian manufacturers received a license from the English patent holders to produce it. This practice soon came to the attention of the Italian Navy, which developed its frogman unit Decima Flottiglia MAS and was used effectively in World War II.[12]
During the Second World War, captured Italian frogmen's rebreathers influenced improved designs for British rebreathers.[12] Many British frogmen's breathing sets used aircrew breathing oxygen cylinders salvaged from shot-down German Luftwaffe aircraft. The earliest of these breathing sets may have been modified Davis Submerged Escape Apparatus; their fullface masks were the type intended for the Siebe Gorman Salvus, but in later operations different designs were used, leading to a fullface mask with one big face window, at first circular or oval and later rectangular (mostly flat, but the sides curved back to allow better vision sideways). Early British frogman's rebreathers had rectangular counterlungs on the chest like Italian frogman's rebreathers, but later designs had a square recess in the top of the counterlung so it could extend further up toward the shoulders. In front they had a rubber collar that was clamped around the absorbent canister.[12] Some British armed forces divers used bulky thick diving suits called Sladen suits; one version of it had a flip-up single faceplate for both eyes to let the user get binoculars to his eyes when on the surface.
The Dräger rebreathers, especially the DM20 and DM40 model series, were used by the German helmet divers and German frogmen during World War II. Rebreathers for the US Navy were developed by Dr. Christian J. Lambertsen for underwater warfare.[16][17] Lambertsen held the first closed-circuit oxygen rebreather course in the United States for the Office of Strategic Services maritime unit at the Naval Academy on 17 May 1943.[17][18]
Post-WWII
The diving pioneer Hans Hass used Dräger oxygen rebreathers in the early 1940s for underwater cinematography.
Due to the military importance of the rebreather, amply demonstrated during the naval campaigns of the Second World War, most governments were reluctant to issue the technology into the public domain. In Britain rebreather use for civilians was negligible – the BSAC even formally prohibited rebreather use by its members. The Italian firms Pirelli and Cressi-Sub at first each sold a model of sport diving rebreather, but after a while discontinued those models. Some home made rebreathers were used by cave divers to penetrate cave sumps.
Most high-altitude mountaineers use open-circuit oxygen equipment; the 1953 Everest expedition used both closed-circuit and open-circuit oxygen equipment: see bottled oxygen.
With the end of the Cold War and the subsequent collapse of the Communist Bloc, the perceived risk of attack by combat divers dwindled. Western armed forces had less reason to requisition civilian rebreather patents, and automatic and semi-automatic recreational diving rebreathers started to appear.
System variants
Oxygen rebreathers
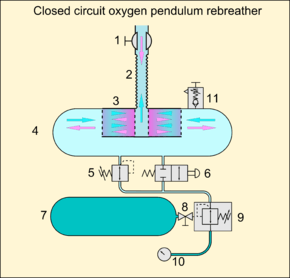
- 1 Dive/surface valve
- 2 Two way breathing hose
- 3 Scrubber (radial flow)
- 4 Counterlung
- 5 Automatic make-up valve
- 6 Manual bypass valve
- 7 Breathing gas storage cylinder
- 8 Cylinder valve
- 9 Regulator first stage
- 10 Submersible pressure gauge
- 11 Overpressure valve
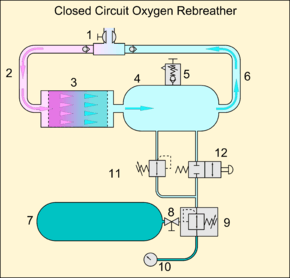
- 1 Dive/surface valve with loop non return valves
- 2 Exhaust hose
- 3 Scrubber (axial flow)
- 4 Counterlung
- 5 Overpressure valve
- 6 Inhalation hose
- 7 Breathing gas storage cylinder
- 8 Cylinder valve
- 9 Regulator first stage
- 10 Submersible pressure gauge
- 11 Automatic make-up valve
- 12 Manual bypass valve
This is the earliest type of rebreather and was commonly used by navies and for mining rescue from the early twentieth century. Oxygen rebreathers can be remarkably simple designs, and they were invented before open-circuit scuba. They only supply oxygen, so there is no requirement to control the gas mixture other than removing the carbon dioxide.[19]
Oxygen feed options
In some rebreathers, e.g. the Siebe Gorman Salvus, the oxygen cylinder has oxygen supply mechanisms in parallel. One is constant flow; the other is a manual on-off valve called a bypass valve; both feed into the same hose which feeds the counterlung.[11] In the Salvus there is no second stage and the gas is turned on and off at the cylinder.
Others such as the USN Mk25 UBA are supplied via a demand valve on the counterlung. This will add gas at any time that the counterlung is emptied and the diver continues to inhale. Oxygen can also be added manually by a button which activates the demand valve.[20]
Some simple oxygen rebreathers had no automatic supply system, but only the manual feed valve, and the diver had to operate the valve at intervals to refill the breathing bag as the volume of oxygen decreased below a comfortable level.
Semi-closed circuit rebreathers
These are generally used for underwater diving, as they are bulkier and heavier than closed circuit oxygen rebreathers. Military and recreational divers use these because they provide better underwater duration than open circuit, have a deeper maximum operating depth than oxygen rebreathers and can be fairly simple and cheap. They do not rely on electronics for control of gas composition, but may use electronic monitoring for improved safety and more efficient decompression.
Semi-closed circuit equipment generally supplies one breathing gas such as air, nitrox or trimix at a time. The gas is injected into the loop at a constant rate to replenish oxygen consumed from the loop by the diver. Excess gas must be constantly vented from the loop in small volumes to make space for fresh, oxygen-rich gas. As the oxygen in the vented gas cannot be separated from the inert gas, semi-closed circuit is wasteful of oxygen.[21]
A gas mix which has a maximum operating depth that is safe for the depth of the dive being planned, and which will provide a breathable mixture at the surface must be used, or it will be necessary to change mixtures during the dive.
As the amount of oxygen required by the diver increases with work rate, the gas injection rate must be carefully chosen and controlled to prevent unconsciousness in the diver due to hypoxia.[22] A higher gas addition rate reduces the likelihood of hypoxia but wastes more gas.
Passive addition semi-closed circuit
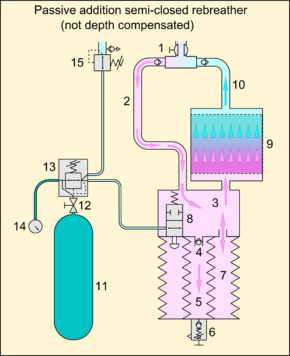
- 1 Dive/surface valve with loop non-return valves
- 2 Exhalation hose
- 3 Counterlung fore-chamber
- 4 Non-return valve to discharge bellows
- 5 Discharge bellows
- 6 Overpressure valve
- 7 Main counterlung bellows
- 8 Addition valve
- 9 Scrubber (axial flow)
- 10 Inhalation hose
- 11 Breathing gas storage cylinder
- 12 Cylinder valve
- 13 Regulator first stage
- 14 Submersible pressure gauge
- 15 Bailout demand valve
This type of rebreather works on the principle of adding fresh gas to compensate for reduced volume in the breathing circuit. A portion of the respired gas is discharged that is in some way proportional to usage. Generally it is a fixed volumetric fraction of the respiratory flow, but more complex systems have been developed which exhaust a close approximation of a ratio to the surface respiratory flow rate. These are described as depth compensated or partially depth compensated systems. Gas addition is triggered by low counterlung volume.
The simple case of a fixed ratio discharge can be achieved by concentric bellows counterlungs, where the exhaled gas expands both the counterlungs, and while the larger volume outer bellows discharges back to the loop when the diver inhales the next breath, the inner bellows discharges its contents to the surroundings, using non return valves to ensure a one-directional flow. The amount processed during each breath depends on the tidal volume of that breath.
Towards the end of inhalation the bellows bottoms out and activates an addition valve, in much the way that a regulator diaphragm activates the demand valve, to make up the gas discharged by the inner bellows. This type of rebreather therefore tends to operate at a minimal volume.
The fixed ratio systems usually discharge between 10% (1/10) and 25% (1/4) of the volume of each breath overboard. As a result, gas endurance is from 10 times to four times that of open circuit, and depends on breathing rate and depth in the same way as for open circuit. Oxygen fraction in the loop depends on the discharge ratio, and to a lesser extent on the breathing rate and work rate of the diver. As some gas is recycled after breathing, the oxygen fraction will always be lower than that of the make-up gas, but can closely approximate the make-up gas after a loop flush, so the gas is generally chosen to be breathable at maximum depth, which allows it to be used for open circuit bailout. The loop gas oxygen fraction will increase with depth, as the mass rate of oxygen used metabolically remains almost constant with a change in depth. This is the opposite tendency of what is done in a closed circuit rebreather, where the oxygen partial pressure is controlled to be more or less the same within limits throughout the dive. The fixed ratio system has been used in the DC55 and Halcyon RB80 rebreathers. Passive addition rebreathers with small discharge ratios may become hypoxic near the surface when moderate oxygen fraction supply gas is used.
The depth compensating systems discharge a portion of the diver's tidal volume which varies in inverse proportion to the absolute pressure. At the surface they generally discharge between 20% (1/5) and 33% (1/3) of each breath, but that decreases with depth, to keep the oxygen fraction in the loop approximately constant and reduce gas consumption. A fully depth compensated system will discharge a volume of gas, inversely proportional to pressure, so that the volume discharged at 90m depth (10 bar absolute pressure) will be 10% of the surface discharge. This system will provide an approximately fixed oxygen fraction regardless of depth, when used with the same make-up gas, because the effective mass discharge remains constant.
Partially depth compensating systems are part way between the fixed ratio and the depth compensating systems. They provide a high discharge ratio near the surface, but the discharge ratio is not fixed either as a proportion of respired volume or mass. Gas oxygen fraction is more difficult to calculate, but will be somewhere between the limiting values for fixed ratio and fully compensated systems. The Halcyon PVR-BASC uses a variable volume inner bellows system to compensate for depth.
Active addition semi-closed circuit
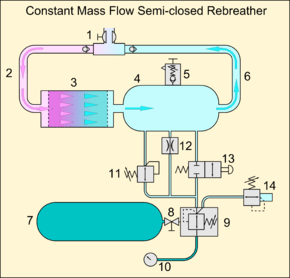
- 1 Dive/surface valve with loop non-return valves
- 2 Exhaust hose
- 3 Scrubber canister (axial flow)
- 4 Counterlung
- 5 Loop overpressure valve
- 6 Inhalation valve
- 7 Breathing gas supply cylinder
- 8 Cylinder valve
- 9 Absolute pressure regulator
- 10 Submersible pressure gauge
- 11 Automatic Diluent Valve
- 12 Constant Mass Flow metering orifice
- 13 Manual bypass valve
- 14 Bailout demand valve
An active addition system adds feed gas to the breathing circuit and excess gas is dumped to the environment. These rebreathers tend to operate near maximum volume.
Constant mass flow gas addition
The most common system of active addition of make-up gas in semi-closed rebreathers is by use of a constant mass flow injector, also known as choked flow. This is easily achieved by using a sonic orifice, as provided the pressure drop over the orifice is sufficient to ensure sonic flow, the mass flow for a specific gas will be independent of the downstream pressure.[23] The mass flow through a sonic orifice is a function of the upstream pressure and the gas mixture, so the upstream pressure must remain constant for the working depth range of the rebreather to provide a reliably predictable mixture in the breathing circuit, and a modified regulator is used which is not affected by changes in ambient pressure. Gas addition is independent of oxygen use, and the gas fraction in the loop is strongly dependent on exertion of the diver – it is possible to dangerously deplete the oxygen by excessive physical exertion.
Demand controlled gas addition
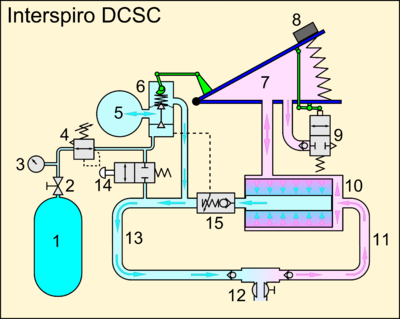
- 1 Nitrox feed gas cylinder
- 2 Cylinder valve
- 3 Pressure gauge
- 4 Feed gas first stage regulator
- 5 Dosage chamber
- 6 Dosage mechanism with control linkage from bellows cover
- 7 Hinged bellows counterlung
- 8 Bellows weight
- 9 Exhaust valve with control linkage from bellows cover
- 10 Radial flow scrubber
- 11 Exhalation hose
- 12 Mouthpiece with dive/surface valve and loop non-return valves
- 13 Inhalation hose
- 14 Manual bypass valve
- 15 Low gas warning valve
Only one model using this gas mixture control principle has been marketed. This is the Interspiro DCSC. The principle of operation is to add a mass of oxygen that is proportional to the volume of each breath. This approach is based on the assumption that the volumetric breathing rate of a diver is directly proportional to metabolic oxygen consumption, which experimental evidence indicates is close enough to work.[24]
The fresh gas addition is made by controlling the pressure in a dosage chamber proportional to the counterlung bellows volume. The dosage chamber is filled with fresh gas to a pressure proportional to bellows volume, with the highest pressure when the bellows is in the empty position. When the bellows fills during exhalation, the gas is released from the dosage chamber into the breathing circuit, proportional to the volume in the bellows during exhalation, and is fully released when the bellows is full. Excess gas is dumped to the environment through the overpressure valve after the bellows is full.[24]
The result is the addition of a mass of gas proportional to ventilation volume, and the oxygen fraction is stable over the normal range of exertion.
The volume of the dosage chamber is matched to a specific supply gas mixture, and is changed when the gas is changed. The DCSC uses two standard mixtures of nitrox: 28% and 46%.[24]
Closed circuit mixed gas rebreathers
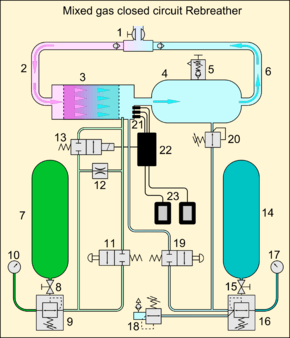
- 1 Dive/surface valve and loop non-return valves
- 2 Exhaust hose
- 3 Scrubber (axial flow)
- 4 Counterlung
- 5 Overpressure valve
- 6 Inhalation valve
- 7 Oxygen cylinder
- 8 Oxygen cylinder valve
- 9 Absolute pressure oxygen regulator
- 10 Oxygen submersible pressure gauge
- 11 Oxygen manual bypass valve
- 12 Oxygen constant mass flow metering orifice
- 13 Electronically controlled solenoid operated oxygen injection valve
- 14 Diluent cylinder
- 15 Diluent cylinder valve
- 16 Diluent regulator
- 17 Diluent submersible pressure gauge
- 18 Bailout demand valve
- 19 Manual diluent bypass valve
- 20 Automatic diluent valve
- 21 Oxygen sensor cells
- 22 Electronic control and monitoring circuits
- 23 Primary and secondary display units
Military, photographic, and recreational divers use closed circuit rebreathers because they allow long dives and produce no bubbles.[25] Closed circuit rebreathers supply two breathing gases to the loop: one is pure oxygen and the other is a diluent or diluting gas such as air, nitrox, heliox or trimix.
A major function of the closed circuit rebreather is to control the oxygen partial pressure in the loop and to warn the diver if it becomes dangerously low or high. Too low a concentration of oxygen results in hypoxia leading to unconsciousness and ultimately death. Too high a concentration of oxygen results in hyperoxia, leading to oxygen toxicity, a condition causing convulsions which can make the diver lose the mouthpiece when they occur underwater, and can lead to drowning. The monitoring system uses oxygen-sensitive electro-galvanic fuel cells to measure the partial pressure of oxygen in the loop. The partial pressure of oxygen in the loop can generally be controlled within reasonable tolerance of a fixed value. This set point is chosen to provide an acceptable risk of both long-term and acute oxygen toxicity, while minimizing the decompression requirements for the planned dive profile.
The gas mixture is controlled by the diver in manually controlled closed circuit rebreathers. The diver can manually control the mixture by adding diluent gas or oxygen. Adding diluent can prevent the loop gas mixture becoming too oxygen rich, and adding oxygen is done to increase oxygen concentration.
In fully automatic closed-circuit systems, an electronically controlled solenoid valve injects oxygen into the loop when the control system detects that the partial pressure of oxygen in the loop has fallen below the required level. Electronically controlled CCRs can be switched to manual control in the event of some control system failures.
Addition of gas to compensate for compression during descent is usually done by an automatic diluent valve.
Rebreathers using an absorbent that releases oxygen
There have been a few rebreather designs (e.g. the Oxylite) which had an absorbent canister filled with potassium superoxide, which gives off oxygen as it absorbs carbon dioxide: 4KO2 + 2CO2 = 2K2CO3 + 3O2; it had a very small oxygen cylinder to fill the loop at the start of the dive.[26] This system is dangerous because of the explosively hot reaction that happens if water gets on the potassium superoxide. The Russian IDA71 military and naval rebreather was designed to be run in this mode or as an ordinary rebreather.
Tests on the IDA71 at the United States Navy Experimental Diving Unit in Panama City, Florida showed that the IDA71 could give significantly longer dive time with superoxide in one of the canisters than without.[26]
Rebreathers which store liquid oxygen
If used underwater, the liquid-oxygen tank must be well insulated against heat coming in from the water. As a result, industrial sets of this type may not be suitable for diving, and diving sets of this type may not be suitable for use out of water. The set's liquid oxygen tank must be filled immediately before use. They include these types:
- Blackett's Aerophor
- Aerorlox[27]
Cryogenic rebreather
A cryogenic rebreather removes the carbon dioxide by freezing it out in a "snow box" by the low temperature produced as liquid oxygen evaporates to replace the oxygen used.
A cryogenic rebreather prototype called the S-1000 was built by Sub-Marine Systems Corporation. It had a duration of 6 hours and a maximum dive depth of 200 metres (660 ft). Its ppO2 could be set to anything from 0.2 to 2 bars (3 to 30 psi) without electronics, by controlling the temperature of the liquid oxygen, thus controlling the equilibrium pressure of oxygen gas above the liquid. The diluent could be either nitrogen or helium depending on the depth of the dive. The partial pressure of oxygen was controlled by temperature, which was controlled by controlling the pressure at which liquid nitrogen was allowed to boil, which was controlled by an adjustable pressure relief valve. No control valves other than the nitrogen pressure relief valve were required. Low temperature was also used to freeze out up to 230 grams of carbon dioxide per hour from the loop, corresponding to an oxygen consumption of 2 litres per minute as carbon dioxide will freeze out of the gaseous state at -43.3 °C or below. If oxygen was consumed faster due to a high workload, a regular scrubber was needed. No electronics were needed as everything followed the setting of the nitrogen release pressure from the cooling unit, and the refrigeration by evaporation of liquid nitrogen maintained a steady temperature until the liquid nitrogen was exhausted. The loop gas flow was passed through a counterflow heat exchanger, which re-heated the gas returning to the diver by chilling the gas headed for the snow box (the cryogenic scrubber). The first prototype, the S-600G, was completed and shallow-water tested in October 1967. The S1000 was announced in 1969,[28][29] but the systems were never marketed.[30]
Cryogenic rebreathers were widely used in Soviet oceanography in the period 1980 to 1990.[30][31][32]
Fields of application
- Underwater – as a self-contained breathing apparatus, where it is sometimes known as "closed circuit scuba" as opposed to "open circuit scuba" where the diver exhales breathing gas into the surrounding water.[33] Surface-supplied diving equipment may incorporate rebreather technology either as a gas reclaim system, where the surface-supplied breathing gas is returned and scrubbed at the surface, or as a gas extender carried by the diver.[34][35] Rebreathers may also be used as self-contained diver bailout systems for either scuba or surface-supplied diving.[36]
- Mine rescue and other industrial applications – where poisonous gases may be present or oxygen may be absent.
- Crewed spacecraft and space suits – outer space is, effectively, a vacuum without oxygen to support life.
- Hospital anaesthesia breathing systems – to supply controlled concentrations of anaesthetic gases to patients without contaminating the air that the staff breathe.
- Himalayan or high-altitude mountaineering. High altitude reduces the partial pressure of oxygen in the ambient air, which reduces the ability of the climber to function effectively. Mountaineering rebreathers in closed-circuit oxygen sets provide a higher partial pressure of oxygen to the climber. However most high-altitude sets are open-circuit (not closed-circuit with rebreathers).
- Submarines, underwater habitats, and saturation diving systems use a scrubber system working on the same principles as a rebreather.
- Fire fighting, where firefighters may be required to operate in an IDLH atmosphere for extended periods of time, longer than an open-circuit SCBA can provide air for.
This may be compared with some applications of open-circuit breathing apparatus:
- The oxygen enrichment systems primarily used by medical patients, high altitude mountaineers and commercial aircraft emergency systems, in which the user breathes ambient air which is enriched by the addition of pure oxygen,
- Open circuit breathing apparatus used by firefighters, underwater divers and some mountaineers, which supplies fresh gas for each breath, which is then discharged into the environment.
- Gas masks and respirators which filter contaminants from ambient air which is then breathed.
Diving rebreathers
The widest variety of rebreather types is used in diving, as the consequences of breathing under pressure complicate the requirements, and a large range of options are available depending on the specific application and available budget. A diving rebreather is safety-critical life-support equipment – some modes of failure can kill the diver without warning, others can require immediate appropriate response for survival.
Design criteria for scuba rebreathers
- Operational requirements for diving rebreathers include
- waterproof and corrosion resistant construction
- reasonably close to neutrally buoyant after ballasting
- acceptably streamlined, to minimize added swimming resistance
- low work of breathing in all diver attitudes and over the full operating depth range
- the unit should not adversely affect the diver's trim and balance
- easy and quick release of harness and unaided removal of the unit from the diver
- accessibility of control and adjustment components
- unambiguous feedback to the diver of critical information
- no critical single-point failure modes – The user should be able to deal with any single reasonably foreseeable failure without outside help
- Special applications may also require
- low noise signal
- low emission of bubbles/small bubbles
- low electromagnetic signature
- rugged construction
- light weight in air
- minimal additional task-loading for normal operation
Oxygen rebreathers for diving
As pure oxygen is toxic when inhaled at pressure, recreational diver certification agencies limit oxygen decompression to a maximum depth of 6 metres (20 ft) and this restriction has been extended to oxygen rebreathers; In the past they have been used deeper (up to 20 metres (66 ft)) but such dives were more risky than what is now considered acceptable. Oxygen rebreathers are also sometimes used when decompressing from a deep open-circuit dive, as breathing pure oxygen helps the nitrogen diffuse out of the body tissues more rapidly, and the use of a rebreather may be more convenient for long decompression stops.
- US Navy restrictions on oxygen rebreather use[20]
- Normal working limit 25 feet (7.6 m) for 240 minutes.
- Maximum working limit 50 feet (15 m) for 10 minutes.
Oxygen rebreathers are no longer commonly used in recreational diving because of the depth limit imposed by oxygen toxicity, but are extensively used for military attack swimmer applications where greater depth is not required, due to their simplicity, light weight and compact size.
Mixed gas rebreathers for diving
Semi-closed circuit rebreathers used for diving may use active or passive gas addition, and the gas addition systems may be depth compensated. They use a mixed supply gas with a higher oxygen fraction than the steady state loop gas mixture. Usually only one gas mixture is used, but it is possible to switch gas mixtures during a dive to extend the available depth range of some SCRs.
- Operational scope and restrictions of SCRs
- Non-depth compensated passive addition SCRs reduce the safe range of operating depths in inverse proportion to gas endurance extension. This can be compensated by gas switching, at the expense of complexity and increased number of potential failure points.
- Constant mass flow SCRs provide a gas mixture which is not consistent over variation in diver exertion. This also limits safe operating depth range unless gas composition is monitored, also at the expense of increased complexity and additional potential failure points.
- Demand controlled active gas addition provides reliable gas mixtures throughout the potential operating depth range, and do not require oxygen monitoring, but at the cost of more mechanical complexity.
- Depth compensated passive addition provides reliable gas mixture over the potential operating depth range, which is only slightly reduced from the open circuit operational range for the gas in use at the cost of more mechanical complexity.
Closed circuit diving rebreathers may be manually or electronically controlled, and use both pure oxygen and a breathable mixed gas diluent.
- Operational scope and restrictions of CCRs
Surface supplied diving gas reclaim systems
A helium reclaim system (or push-pull system) is used to recover helium based breathing gas after use by the diver when this is more economical than losing it to the environment in open circuit systems. The recovered gas is passed through a scrubber system to remove carbon dioxide, filtered to remove odours, and pressurised into storage containers, where it may be mixed with oxygen to the required composition for re-use.
Saturation diving life-support systems
The life support system provides breathing gas and other services to support life for the personnel under pressure in the accommodation chambers and closed diving bell. It includes the following components:[37]
- Breathing gas supply, distribution and recycling equipment: scrubbers, filters, boosters, compressors, mixing, monitoring, and storage facilities
- Chamber climate control system - control of temperature and humidity, and filtration of gas
- Instrumentation, control, monitoring and communications equipment
- Fire suppression systems
- Sanitation systems
The life support system for the bell provides and monitors the main supply of breathing gas, and the control station monitors the deployment and communications with the divers. Primary gas supply, power and communications to the bell are through a bell umbilical, made up from a number of hoses and electrical cables twisted together and deployed as a unit.[38] This is extended to the divers through the diver umbilicals.[37]
The accommodation life support system maintains the chamber environment within the acceptable range for health and comfort of the occupants. Temperature, humidity, breathing gas quality sanitation systems and equipment function are monitored and controlled.[38]
Industrial and rescue self-contained rebreathers
Different design criteria apply to SCBA rebreathers for use only out of the water:
- There is no variation in ambient pressure on the components. The counterlung may be placed for comfort and convenience.
- Cooling of the gas in the breathing loop may be desirable, as the absorbent produces heat as it reacts with carbon dioxide, and the warming of the gas is not welcome in hot industrial situations such as deep mines.
- Absorbent containers may in some cases rely on gravity for preventing channeling.
- If a full-face mask is used, it may have viewports designed for convenience or improved field of vision, and they do not need to be flat and parallel to prevent visual distortion as if underwater.
- In firefighting rebreathers, consideration must be given to making the set reasonably flame-proof and protecting it from heat and debris impacts.
- The need to ditch the set quickly, may not arise, and harness straps may not need a quick-release.
- Buoyancy is not a consideration, but weight may be critical.
- There are no constraints due to the physiological effects of breathing under pressure. Complex gas mixtures are unnecessary. Oxygen rebreathers can usually be used.
Mountaineering rebreathers
Mountaineering rebreathers provide oxygen at a higher concentration than available from atmospheric air in a naturally hypoxic environment. They need to be lightweight and to be reliable in severe cold including not getting choked with deposited frost.[39] A high rate of system failures due to extreme cold has not been solved. Breathing pure oxygen results in an elevated partial pressure of oxygen in the blood: a climber breathing pure oxygen at the summit of Mt. Everest has a greater oxygen partial pressure than breathing air at sea level. This results in being able to exert greater physical effort at altitude.
Both chemical and compressed gas oxygen have been used in experimental closed-circuit oxygen systems – the first on Mount Everest in 1938. The 1953 expedition used closed-circuit oxygen equipment developed by Tom Bourdillon and his father for the first assault team of Bourdillon and Evans; with one "dural" 800l compressed oxygen cylinder and soda lime canister (the second (successful) assault team of Hillary and Tenzing used open-circuit equipment).[40]
Atmospheric diving suits
An atmospheric diving suit is a small one-man articulated submersible of roughly anthropomorphic form, with limb joints which allow articulation under external pressure while maintaining an internal pressure of one atmosphere. Breathing gas supply may be surface supplied by umbilical, or from a rebreather carried on the suit. An emergency gas supply rebreather may also be fitted to a suit with either surface supply or rebreather for primary breathing gas.
Rebreathers for unpressurised aircraft and high altitude parachuting
Similar requirement and working environment to mountaineering, but weight is less of a problem. The Soviet IDA-71 rebreather was also manufactured in a high altitude version, which was operated as an oxygen rebreather.
Anaesthesia systems
Anaesthetic machines can be configured as rebreathers to provide oxygen and anaesthetic gases to a patient during surgery or other procedures that require sedation. An absorbent is present in the machine to remove the carbon dioxide from the loop.[41]
Both semi-closed and fully closed circuit systems may be used for anaesthetic machines, and both push-pull (pendulum) two directional flow and one directional loop systems are used.[42] The breathing circuit of a loop configured machine has two unidirectional valves so that only scrubbed gas flows to the patient while expired gas goes back to the machine.[41]
The anaesthetic machine can also provide gas to ventilated patients who cannot breathe on their own.[43] A waste gas scavenging system removes any gasses from the operating room to avoid environmental contamination.[44]
Anaesthesia personnel train for equipment failures using medical simulation techniques.[45][46]
Space suits
One of the functions of a space suit is to provide the wearer with breathing gas. This can be done via an umbilical from the life-support systems of the spacecraft or habitat, or from a primary life support system carried on the suit. Both of these systems involve rebreather technology as they both remove carbon dioxide from the breathing gas and add oxygen to compensate for oxygen used by the wearer. Space suits usually use oxygen rebreathers as this allows a lower pressure in the suit which gives the wearer better freedom of movement.
Habitat life-support systems
Submarines, underwater habitats, bomb shelters, space stations, and other living spaces occupied by several people over medium to long periods on a limited gas supply, are equivalent to closed circuit rebreathers in principle, but generally rely on mechanical circulation of breathing gas through the scrubbers.
Architecture of a rebreather
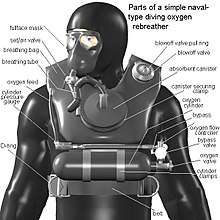
Although there are several design variations of diving rebreather, all types have a gas-tight loop that the diver inhales from and exhales into. The loop consists of several components sealed together. The diver breathes through a mouthpiece or a fullface mask. This is connected to one or more tubes ducting inhaled and exhaled gas between the diver and a counterlung or breathing bag. This holds gas when it is not in the diver's lungs. The loop also includes a scrubber containing carbon dioxide absorbent to remove the carbon dioxide exhaled by the diver. Attached to the loop there will be at least one valve allowing addition of gases, such as oxygen and perhaps a diluting gas, from a gas storage into the loop. There may be valves allowing venting of gas from the loop.
Breathing gas passage configuration
There are two basic gas passage configurations: The loop and the pendulum.
The loop configuration uses a one directional circulation of the breathing gas which on exhalation leaves the mouthpiece, passes through a non-return valve into the exhalation hose, and then through the counterlung and scrubber, to return to the mouthpiece through the inhalation hose and another non-return valve when the diver inhales.
The pendulum configuration uses a two-directional flow. Exhaled gas flows from the mouthpiece through a single hose to the scrubber, into the counterlung, and on inhalation the gas is drawn back through the scrubber and the same hose back to the mouthpiece. The pendulum system is structurally simpler, but inherently contains a larger dead space of unscrubbed gas in the combined exhalation and inhalation tube, which is rebreathed. There are conflicting requirements for minimising the volume of dead space while minimising the flow resistance of the breathing passages.
Mouthpiece
The diver breathes from the rebreather circuit through a bite-grip mouthpiece or an oro-nasal mask which may be part of a full-face mask or diving helmet. The mouthpiece is connected to the rest of the rebreather by breathing hoses. The mouthpiece of a diving rebreather will usually include a shutoff valve, and may incorporate a dive/surface valve or a bailout valve or both. On loop configured rebreathers the mouthpiece is usually the place where the non-return valves for the loop are fitted.
Dive/Surface valve
The Dive/Surface valve (DSV) is a valve on the mouthpiece which can switch between the loop and ambient surroundings. It is used to close the loop at the surface to allow the diver to breathe atmospheric air, and may also be used underwater to isolate the loop so that it will not flood if the mouthpiece is taken out of the mouth.
Bailout valve
A dive/surface valve which can be switched to close the loop and simultaneously open a connection to an open circuit demand valve is known as a bailout valve, as its function is to switch over to open circuit bailout without having to remove the mouthpiece. An important safety device when carbon dioxide poisoning occurs.[47]
Breathing hoses
Flexible corrugated synthetic rubber hoses are used to connect the mouthpiece to the rest of the breathing circuit, as these allow free movement of the diver's head. These hoses are corrugated to allow greater flexibility while retaining a high resistance to collapse. The hoses are designed to provide low resistance to flow of the breathing gas. A single breathing hose is used for pendulum (push-pull) configuration, and two hoses for a one-way loop configuration.
Counterlungs
The counterlung is a part of the loop which is designed to change in volume by the same amount as the user's tidal volume when breathing. This lets the loop expand and contract when the user breathes, letting the total volume of gas in the lungs and the loop remain constant throughout the breathing cycle. The volume of the counterlung should allow for the maximum likely breath volume of a user, but does not generally need to match the vital capacity of all possible users.
Underwater, the position of the counterlung – on the chest, over the shoulders, or on the back – has an effect on the hydrostatic work of breathing. This is due to the pressure difference between the counterlung and the diver's lung caused by the vertical distance between the two.
Recreational, technical and many professional divers will spend most of their time underwater swimming face down and trimmed horizontally. Counterlungs should function well with low work of breathing in this position, and with the diver upright.
- Front mounted: When horizontal they are under greater hydrostatic pressure than the diver's lungs. Easier to inhale, harder to exhale.
- Back mounted: When horizontal they are under less hydrostatic pressure than the diver's lungs. The amount varies, as some are closer to the back than others. Harder to inhale, easier to exhale.
- Over the shoulder: The hydrostatic pressure will vary depending on how much gas is in the counterlungs, and increases as the volume increases and the lowest part of the gas space moves downward. The resistive work of breathing often negates the gains of good positioning close to the lung centroid.
The design of the counterlungs can also affect the swimming diver's streamlining due to location and shape of the counterlungs themselves.
For use out of water, counterlung position does not affect work of breathing and it can be positioned wherever convenient. For example, in an industrial version of the Siebe Gorman Salvus the breathing bag hangs down by the left hip.
A rebreather which uses rubber counterlungs which are not in an enclosed casing should be sheltered from sunlight when not in use, to prevent the rubber from perishing due to ultraviolet light.
Concentric bellows counterlungs
Most passive addition semi-closed diving rebreathers control the gas mixture by removing a fixed volumetric proportion of the exhaled gas, and replacing it with fresh feed gas from a demand valve, which is triggered by low volume of the counterlung.
This is done by using concentric bellows counterlungs – the counterlung is configured as a bellows with a rigid top and bottom, and has a flexible corrugated membrane forming the side walls. There is a second, smaller bellows inside, also connected to the rigid top and bottom surfaces of the counterlung, so that as the rigid surfaces move towards and away from each other, the volumes of the inner and outer bellows change in the same proportion.
The exhaled gas expands the counterlungs, and some of it flows into the inner bellows. On inhalation, the diver only breathes from the outer counterlung – return flow from the inner bellows is blocked by a non-return valve. The inner bellows also connects to another non-return valve opening to the outside environment, and thus the gas from the inner bellows is dumped from the circuit in a fixed proportion of the volume of the inhaled breath. If the counterlung volume is reduced sufficiently for the rigid cover to activate the feed gas demand valve, gas will be added until the diver finishes that inhalation.
Carbon dioxide scrubber
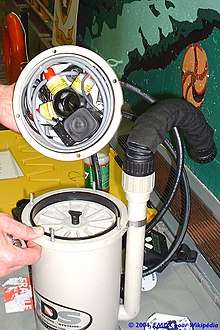
The exhaled gases are directed through the chemical scrubber, a canister full of a suitable carbon dioxide absorbent such as a form of soda lime, which removes the carbon dioxide from the gas mixture and leaves the oxygen and other gases available for re-breathing.[48]
Some of the absorbent chemicals are produced in granular format for diving applications, such as Atrasorb Dive, Sofnolime, Dragersorb, or Sodasorb. Other systems use a prepackaged Reactive Plastic Curtain (RPC) based cartridge:[49] The term Reactive Plastic Curtain was originally used to describe Micropore's absorbent curtains for emergency submarine use by the US Navy, and more recently RPC has been used to refer to their [50] Reactive Plastic Cartridges.
The carbon dioxide passing through the scrubber absorbent is removed when it reacts with the absorbent in the canister; this chemical reaction is exothermic. This reaction occurs along a "front" which is a region across the flow of gas through the soda-lime in the canister. This front moves through the scrubber canister, from the gas input end to the gas output end, as the reaction consumes the active ingredients. This front would be a zone with a thickness depending on the grain size, reactivity, and gas flow velocity because the carbon dioxide in the gas going through the canister needs time to reach the surface of a grain of absorbent, and then time to penetrate to the middle of each grain of absorbent as the outside of the grain becomes exhausted. Eventually gas with remaining carbon dioxide will reach the far end of the canister and "breakthrough" will occur. After this the carbon dioxide content of the scrubbed gas will tend to rise as the effectiveness of the scrubber falls until it becomes noticeable to the user, then unbreathable.
In larger systems, such as recompression chambers, a fan is used to pass gas through the canister.
Scrubber effectiveness
In rebreather diving, the typical effective duration of the scrubber will be half an hour to several hours of breathing, depending on the granularity and composition of the soda lime, the ambient temperature, the design of the rebreather, and the size of the canister. In some dry open environments, such as a recompression chamber or a hospital, it may be possible to put fresh absorbent in the canister when break through occurs.
Gas venting
Overpressure valve
During ascent the gas in the breathing circuit will expand, and must have some way of escape before the pressure difference causes injury to the diver or damage to the loop. The simplest way to do this is for the diver to allow excess gas to escape around the mouthpiece or through the nose, but a simple overpressure valve is reliable and can be adjusted to control the permitted overpressure. The overpressure valve is typically mounted on the counterlung and in military diving rebreathers it may be fitted with a diffuser.
Diffuser
Some military diving rebreathers have a diffuser over the blowoff valve, which helps to conceal the diver's presence by masking the release of bubbles, by breaking them up to sizes which are less easily detected.[51] A diffuser also reduces bubble noise.
Loop drainage
Many rebreathers have "water traps" in the counterlungs or scrubber casing, to stop large volumes of water from entering the scrubber media if the diver removes the mouthpiece underwater without closing the valve, or if the diver's lips get slack and let water leak in.
Some rebreathers have manual pumps to remove water from the water traps, and a few of the passive addition SCRs automatically pump water out along with the gas during the exhaust stroke of the bellows counterlung.
Work of breathing
Work of breathing is the effort required to breathe. Part of the work of breathing is due to inherent physiological factors, part is due to the mechanics of the external breathing apparatus, and part is due to the characteristics of the breathing gas. A high work of breathing may result in carbon dioxide buildup in the diver, and reduces the diver's ability to produce useful physical effort. In extreme cases work of breathing may exceed the aerobic work capacity of the diver, with fatal consequences.
Work of breathing of a rebreather has two main components: Resistive work of breathing is due to the flow restriction of the gas passages causing resistance to flow of the breathing gas, and exists in all applications where there is no externally powered ventilation. Hydrostatic work of breathing is only applicable to diving applications, and is due to difference in pressure between the lungs of the diver and the counterlungs of the rebreather. This pressure difference is generally due to a difference in hydrostatic pressure caused by a difference in depth between lung and counterlung, but can be modified by ballasting the moving side of a bellows counterlung.
Resistive work of breathing is the sum of all the restrictions to flow due to bends, corrugations, changes of flow direction, valve cracking pressures, flow through scrubber media, etc., and the resistance to flow of the gas, due to inertia and viscosity, which are influenced by density, which is a function of molecular weight and pressure. Rebreather design can limit the mechanical aspects of flow resistance, particularly by the design of the scrubber, counterlungs and breathing hoses. Diving rebreathers are influenced by the variations of work of breathing due to gas mixture choice and depth. Helium content reduces work of breathing, and increased depth increases work of breathing.
Work of breathing can also be increased by excessive wetness of the scrubber media, usually a consequence of a leak in the breathing loop, or by using a grain size of absorbent that is too small.
The semi-closed rebreather systems developed by Drägerwerk in the early 20th century as a scuba gas supply for helmet divers, using oxygen or nitrox, and the US Navy Mark V Heliox helmet developed in the 1930s for deep diving, circulated the breathing gas through the helmet and scrubber by using an injector system where the added gas entrained the loop gas and produced a stream of processed gas past the diver inside the helmet, which eliminated external dead space and equipment work of breathing but was not suitable for high breathing rates.[35]
Gas sources
A rebreather must have a source of oxygen to replenish that which is consumed by the diver. Depending on the rebreather design variant, the oxygen source will either be pure or a breathing gas mixture which is almost always stored in a gas cylinder. In a few cases oxygen is supplied as liquid oxygen or from a chemical reaction.
Pure oxygen is not considered to be safe for recreational diving deeper than 6 meters, so recreational rebreathers and many professional diving rebreathers also have a cylinder of diluent gas. This diluent cylinder may be filled with compressed air or another diving gas mix such as nitrox, trimix, or heliox. The diluent reduces the percentage of oxygen breathed and increases the maximum operating depth of the rebreather. The diluent is not an oxygen-free gas, such as pure nitrogen or helium, and is breathable as it will be used in an emergency either to flush the loop with breathable gas of a known composition or as a bailout.
Gas addition valves
Gas must be added to the breathing loop if the volume gets too small or if it is necessary to change the gas composition.
Automatic diluent valve (ADV)
This has a similar function to an open circuit demand valve. It adds gas to the circuit if the volume in the circuit is too low. The mechanism is either operated by a dedicated diaphragm like in a scuba second stage, or may be operated by the top of a bellows type counterlung reaching the bottom of its travel.
Manual addition
Closed circuit rebreathers usually allow the diver to add gas manually. In oxygen rebreathers this is just oxygen, but mixed gas rebreathers usually have a separate manual addition valve for oxygen and diluent, as either might be required to correct the composition of the loop mixture, either as the standard operating method for manually controlled CCRs, or as a backup system on electronically controlled CCRs. The manual diluent addition is sometimes by a purge button on the ADV.
Constant mass flow
Constant mass flow gas addition is used on active addition semi-closed rebreathers, where it is the normal method of addition at constant depth, and in many closed circuit rebreathers, where it is the primary method of oxygen addition, at a rate less than metabolically required by the diver at rest, and the rest is made up by the control system through a solenoid valve, or manually by the diver.
Constant mass flow is achieved by sonic flow through an orifice. The flow of a compressible fluid through an orifice is limited to the flow at sonic velocity in the orifice. This can be controlled by the upstream pressure and the orifice size and shape, but once the flow reached the speed of sound in the orifice, any further reduction of downstream pressure has no influence on the flow rate. This requires a gas source at a fixed pressure, and it only works at depths which have a low enough ambient pressure to provide sonic flow in the orifice.
Regulators which have their control components isolated from the ambient pressure are used to supply gas at a pressure independent of the depth.
Passive addition
In passive addition semi-closed rebreathers, gas is usually added by a demand type valve actuated by the bellows counterlung when the bellows is empty. This is the same actuation condition as the automatic diluent valve of any rebreather, but the actual trigger mechanism is slightly different. A passive rebreather of this type does not need a separate ADV as the passive addition valve already serves this function.
Electronically controlled (solenoid valves)
Electronically controlled closed circuit mixed gas rebreathers may have part of the oxygen feed provided by a constant mass flow orifice, but the fine control of partial pressure is done by solenoid operated valves actuated by the control circuits. Timed opening of the solenoid valve will be triggered when the oxygen partial pressure in the loop mix drops below the lower set-point.
If the constant mass flow orifice is compromised and does not deliver the correct flow, the control circuit will compensate by firing the solenoid valve more often.
Control of the breathing gas mix
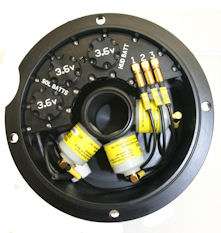
The fundamental requirements for the control of the gas mixture in the breathing circuit for any rebreather application are that the carbon dioxide is removed, and kept at a tolerable level, and that the partial pressure of oxygen is kept within safe limits. For rebreathers which are used at normobaric or hypobaric pressures, this only requires that there is sufficient oxygen, which is easily achieved in an oxygen rebreather. Hyperbaric applications, as in diving, also require that the maximum partial pressure of oxygen is limited, to avoid oxygen toxicity, which is technically a more complex process, and may require dilution of the oxygen with metabolically inert gas.
If not enough oxygen is added, the concentration of oxygen in the loop may be too low to support life. In humans, the urge to breathe is normally caused by a build-up of carbon dioxide in the blood, rather than lack of oxygen. Hypoxia can cause blackout with little or no warning, followed by death.
The method used for controlling the range of oxygen partial pressure in the breathing loop depends on the type of rebreather.
- In an oxygen rebreather, once the loop has been thoroughly flushed, the mixture is effectively static at 100% oxygen, and the partial pressure is a function only of ambient pressure.
- In a semi-closed rebreather the loop mix depends on a combination of factors:
- the type of gas addition system and its setting, combined with the gas mixture in use, which control the rate of oxygen added.
- work rate, and therefore the oxygen consumption rate, which controls the rate of oxygen depletion, and therefore the resulting oxygen fraction.
- ambient pressure, as partial pressure in proportion to ambient pressure and oxygen fraction.
- In manually controlled closed circuit rebreathers the user controls the gas mixture and volume in the loop by injecting each of the different available gases to the loop and by venting the loop.
- Most electronically controlled closed-circuit diving rebreathers have electro-galvanic oxygen sensors and electronic control circuits, which monitor the ppO2, injecting more oxygen if necessary and issuing an audible, visual and/or vibratory warning to the diver if the ppO2 reaches dangerously high or low levels.
The volume in the loop is usually controlled by a pressure controlled automatic diluent valve, which works on the same principle as a demand valve. This adds diluent when the pressure in the loop is reduced below ambient pressure, such as during descent or if gas is lost from the loop. The set may also have a manual addition valve, sometimes called a bypass. In some early oxygen rebreathers the user had to manually open and close the valve to the oxygen cylinder to refill the counterlung each time the volume got low.
Configuration
Arrangement
The parts of a rebreather (bag, absorbent canister, cylinder(s)) can be arranged on the wearer's body in many ways, more so than with open-circuity air scuba. For example:
- In the early Russian Epron-1 rebreather, the scrubber canister, the counterlung and the oxygen cylinder are parallel on the chest, from left to right, with the breathing tube loop from the end of the canister to the bag.[52]
- In this old German industrial rebreather, the working parts are on the user's left waist and it has one long breathing tube.[53]
- Some are back mounted. Some are worn on the chest. Some have a hard casing. If used underwater, the counterlung must be near the user's lungs. The use duration on a fill varies widely with make.
Casing
Many rebreathers have their main components in a hard backpack casing for support, protection and/or streamlining. This casing must be vented to let surrounding water or air in and out to allow for volume changes as the breathing bag inflates and deflates. A diving rebreather needs fairly large holes, including a hole at the bottom to drain the water out when the diver comes out of water. The SEFA, which is used for mine rescue, to keep grit and stones out of its working, is completely sealed, except for a large vent panel covered with metal mesh, and holes for the oxygen cylinder's on/off valve and the cylinder pressure gauge. Underwater the casing also serves for streamlining, e.g. in the IDA71 and Cis-Lunar.
Safety
There are several safety issues with rebreather equipment, and these tend to be more severe in diving rebreathers.
Hazards
Some of the hazards are due to the way the equipment works, while others are related to the environment in which the equipment is used.
Hypoxia
Hypoxia can occur in any rebreather which contains enough inert gas to allow breathing without triggering automatic gas addition.
In an oxygen rebreather this can occur if the loop is not sufficiently purged at the start of use. Purging should be done while breathing off the unit so that the inert gas in the user's lungs is also removed from the system.
Carbon dioxide buildup
Carbon dioxide buildup will occur if the scrubber medium is absent, badly packed, inadequate or exhausted. The normal human body is fairly sensitive to carbon dioxide partial pressure, and a buildup will be noticed by the user. However, there is not often much that can be done to rectify the problem except changing to another breathing gas supply until the scrubber can be repacked. Continued use of a rebreather with an ineffective scrubber is not possible for very long, as the levels will become toxic and the user will experience extreme respiratory distress, followed by loss of consciousness and death. The rate at which these problems develop depends on the volume of the circuit and the metabolic rate of the user.
Carbon dioxide buildup can also occur when a combination of exertion and work of breathing exceeds the capacity of the user. If this occurs where the user cannot reduce exertion sufficiently, it may be impossible to correct. This problem is more likely to occur with diving rebreathers at depths where the density of the breathing gas is severely elevated.
Leakage of toxic gases into the breathing loop
Industrial rebreathers are often used where the ambient air is contaminated, and may be toxic. Parts of the loop will be at a slightly lower than external ambient pressure during inhalation, and if the circuit is not airtight external gases may leak in. This is a particular issue around the edge of a full-face mask, where the rubber mask skirt must seal against the user's face.
Fire hazards of high concentration of oxygen
High partial pressures of oxygen greatly increase fire hazard, and many materials which are self-extinguishing in atmospheric air will burn continuously in a high oxygen concentration. This is more of a hazard for terrestrial applications such as rescue and firefighting than for diving, where the ignition risk is relatively low.
Failure modes
Scrubber failure
The term "break through" means the failure of the "scrubber" to continue removing suffient carbon dioxide from the exhaled gas mix. There are several ways that the scrubber may fail or become less efficient:
- Complete consumption of the active ingredient ("break through").
- The scrubber canister has been incorrectly packed or configured. This allows the exhaled gas to bypass the absorbent. In a rebreather, the soda lime must be packed tightly so that all exhaled gas comes into close contact with the granules of soda lime and the loop is designed to avoid any spaces or gaps between the soda lime and the loop walls that would let gas avoid contact with the absorbent. If any of the seals, such as O-rings, or spacers that prevent bypassing of the scrubber, are not cleaned or lubricated or fitted properly, the scrubber will be less efficient, or outside water or gas may get in circuit. This failure mode is also called "tunneling"
- When the gas mix is under pressure caused by depth, the inside of the canister is more crowded by other gas molecules (oxygen or diluent) and the carbon dioxide molecules are not so free to move around to reach the absorbent. In deep diving with a nitrox or other gas-mixture rebreather, the scrubber needs to be bigger than is needed for a shallow-water or industrial oxygen rebreather, because of this effect.
- Carbon dioxide absorbent, or sorb can be caustic and can cause burns to the eyes, mucous membranes and skin. A mixture of water and absorbent occurs when the scrubber floods and depending on the chemicals used, can produce a chalky taste or a burning sensation if the contaminated water reaches the mouthpiece, which should prompt the diver to switch to an alternative source of breathing gas and rinse his or her mouth out with water. This is known to rebreather divers as a caustic cocktail. Many modern diving rebreather absorbents are designed not to produce this if they get wet.
- In below-freezing operation (primarily mountain climbing) the wet scrubber chemicals can freeze when oxygen bottles are changed, thus preventing carbon dioxide from reaching the scrubber material.
Failure prevention
- An indicating dye in the soda lime. It changes the colour of the soda lime after the active ingredient is consumed. For example, a rebreather absorbent called "Protosorb" supplied by Siebe Gorman had a red dye, which was said to go white when the absorbent was exhausted. Colour indicating dye was removed from US Navy fleet use in 1996 when it was suspected of releasing chemicals into the circuit.[54] With a transparent canister, this may be able to show the position of the reaction "front". This is useful in dry open environments, but is not always useful on diving equipment, where the canister is usually out of sight of the user, e.g. inside the breathing bag or inside a backpack box.
- Temperature monitoring. As the reaction between carbon dioxide and soda lime is exothermic, temperature sensors, along the length of the scrubber can be used to measure the position of the front and therefore the estimated remaining life of the scrubber.[55][56]
- Diver training. Divers are trained to monitor and plan the exposure time of the soda lime in the scrubber and replace it within the recommended time limit. At present, there is no effective technology for detecting the end of the life of the scrubber or a dangerous increase in the concentration of carbon dioxide causing carbon dioxide poisoning. The diver must monitor the exposure of the scrubber and replace it when necessary.
- While carbon dioxide gas sensors exist, such systems are not useful as a tool for monitoring scrubber life when underwater as the onset of scrubber "break through" occurs quite rapidly. Such systems should be used as an essential safety device to warn divers to bail off the loop immediately.
Sport diving rebreather technological innovations
Rebreather technology has advanced considerably, often driven by the growing market in recreational diving equipment. Innovations include:
- Bailout valves – a device in the mouthpiece of the loop which connects to a bailout demand valve and can be switched to provide gas from either the loop or the demand valve without the diver taking the mouthpiece from their mouth. An important safety device when carbon dioxide poisoning occurs.[47]
- Integrated decompression computers – input to a dive computer from the oxygen sensors of the rebreather allow divers to take advantage of the actual partial pressure of oxygen to generate an optimised schedule for decompression.
- Carbon dioxide scrubber life monitoring systems – temperature sensors monitor the progress of the reaction of the soda lime and provide an indication of when the scrubber will be exhausted.[55]
- Carbon dioxide monitoring systems – Gas sensing cell and interpretive electronics which detect the concentration of carbon dioxide in the rebreather loop downstream from the scrubber.
Images
- Viper SCR
- Aerorlox rebreather in a coal mining museum
- Mine rescue rebreathers in museum
- Mannequin wearing Finnish Navy combat diver equipment. The chest rebreather is likely Viper S-10.
List of rebreather manufacturers and models
- The Blackett's Aerophor is a nitrox semi-closed-circuit rebreather with liquid gas storage made in England from 1910 onwards for use in mine rescue and other industrial uses.
- CDBA: Clearance Diver's Breathing Apparatus.
- Siebe Gorman CDBA: also CDMBA, SCBA, SCMBA, UBA
- A type introduced in 1999 in the British Navy, being an update of the BioMarine/Carleton MK16:[57]
- In the British Navy the Carleton CDBA is (as at June 2007) planned to be superseded by the CDLSE "Clearance Divers' Life Support Equipment" made by Divex in Aberdeen in Scotland. It is an electronic closed circuit rebreather allowing diving to 60 metres (200 ft).[58]
- The Davis Submerged Escape Apparatus was the first or nearly the first rebreather to be made in quantity.
- FROGS (Full Range Oxygen Gas System) manufactured by Aqualung is the frogman's oxygen rebreather which has been used in France since 15 October 2002:.[59]
- Poseidon MkVI, the world's first fully automatic closed circuit rebreather for recreational use, developed by Poseidon Diving Systems based on the Cis-Lunar MK5 design and further developed into the Poseidon SE7EN.
- Russian IDA71 military and naval rebreather
- The KISS ("Keep It Simple, Stupid") line of manually operated closed circuit rebreathers designed by Gordon Smith of Jetsam Technologies.:[60]
- Some military rebreathers (for example the US Navy MK-25 and the MK-16 mixed-gas rebreather), and the Phibian CCS50 and CCS100 rebreathers, were developed by Oceanic. (Stuart Clough of Undersea Technologies developed the Phibian's electronics package.[61]
- Siebe Gorman Salvus
- The Savox was made by Siebe Gorman,[27] It was an oxygen rebreather with a use duration of 45 minutes. It had no hard casing and was worn in front of the body.
- SDBA is a type of frogman's oxygen rebreather. It has a nitrox variant called ONBA.
- SEFA (Selected Elevated Flow Apparatus) is an industrial oxygen rebreather formerly made by Sabre Safety with 2 hours duration on a filling.
- Siva and Viper military rebreathers made by Carleton Life Support and the Viper E made by Carleton and Juergensen Defense Corporation
- The Porpoise, Ted Eldred's oxygen rebreather.[62]
- The "Universal" rebreather was a long-dive derivative of the Davis Submerged Escape Apparatus, intended to be used with the Sladen Suit.
- The current US Navy Mark 16 Mod 2 (Explosive Ordnance Disposal) and Mark 16 Mod 3 (Naval Special Warfare) units use the Juergensen Defense Corporation Mark V Control System.
- AP Diving's "Inspiration" rebreather series is one of the first electronic closed circuit rebreathers to be mass produced for the recreational market.
- The Orca ECR is one example of a modern CCR design that has both CO2 and O2 monitoring [63]
- The JJ CCR was built to mount large cylinders enabling carrying larger quantities of bailout gas.
- The Prism 2. Notable for a radial scrubber and high-current oxygen cells from the Navy MK15 unit enabling an analogue gauge to read the oxygen levels.
- The Megalodon
- The rEvo III
- The O2ptima CM
See also
- Escape set – Self contained breathing apparatus providing gas to escape from a hazardous environment
- Self-contained breathing apparatus (SCBA) – Emergency breathing air supply system carried by the user (surface-only (industrial) breathing sets including rebreathers)
- Primary life support system, also known as Portable Life Support System – life support device for a space suit
- Carbon dioxide scrubber – Device which absorbs carbon dioxide from circulated gas
References
- NOAA Diving Program (U.S.) (28 Feb 2001). Joiner, James T. (ed.). NOAA Diving Manual, Diving for Science and Technology (4th ed.). Silver Spring, Maryland: National Oceanic and Atmospheric Administration, Office of Oceanic and Atmospheric Research, National Undersea Research Program. ISBN 978-0-941332-70-5. CD-ROM prepared and distributed by the National Technical Information Service (NTIS)in partnership with NOAA and Best Publishing Company
- P.S.Dhami; G.Chopra; H.N. Shrivastava (2015). A Textbook of Biology. Jalandhar, Punjab: Pradeep Publications. pp. V/101.
- James W. Miller, ed. (1979). "Fig 2.4". NOAA Diving Manual (2nd ed.). Washington, DC.: US Dept of Commerce - National Oceanographic and Atmospheric Administration. pp. 2–7.
- "Cornelius Drebbel: inventor of the submarine". Dutch Submarines. Archived from the original on 2012-05-30. Retrieved 2008-02-23.
- Bahuet, Eric (19 October 2003). "Avec ou sans bulles? (With or without bubbles)". La Plongée Souterrain (in French). plongeesout.com. Introduction. Retrieved 5 February 2017.
- Ichtioandre's technical drawing.
- Saint Simon Sicard's invention as mentioned by the Musée du Scaphandre website (a diving museum in Espalion, south of France)
- Bech, Janwillem. "Theodor Schwann". Retrieved 2008-02-23.
- "Henry Albert Fleuss". scubahalloffame.com. Archived from the original on 2015-01-12.
- Davis, RH (1955). Deep Diving and Submarine Operations (6th ed.). Tolworth, Surbiton, Surrey: Siebe Gorman & Company Ltd. p. 693.
- Quick, D. (1970). "A History Of Closed Circuit Oxygen Underwater Breathing Apparatus". Royal Australian Navy, School of Underwater Medicine. RANSUM-1-70. Retrieved 2009-03-03.
- Paul Kemp (1990). The T-Class submarine – The Classic British Design. Arms and Armour. p. 105. ISBN 0-85368-958-X.
- "Dräger diving helmets". Drägerwerk. www.divingheritage.com. Retrieved 12 December 2016.
- Bech, Janwillem (ed.). "Photos Draeger 1907 Rescue Apparatus". Retrieved 19 December 2017.
- Vann RD (2004). "Lambertsen and O2: beginnings of operational physiology". Undersea Hyperb Med. 31 (1): 21–31. PMID 15233157. Retrieved 2008-04-25.
- Butler FK (2004). "Closed-circuit oxygen diving in the U.S. Navy". Undersea Hyperb Med. 31 (1): 3–20. PMID 15233156. Retrieved 2008-04-25.
- Hawkins T (Jan–Mar 2000). "OSS Maritime". The Blast. 32 (1).
- Older, P. (1969). "Theoretical Considerations in the Design of Closed Circuit Oxygen Rebreathing Equipment". Royal Australian Navy, School of Underwater Medicine. RANSUM-4-69. Retrieved 2008-06-14.
- US Navy (2006). "Chapter 19: Closed-Circuit Oxygen UBA Diving". US Navy Diving Manual, 6th revision. United States: US Naval Sea Systems Command. p. 19–9. Retrieved 2008-06-15.
- "What is a "Rebreather"?". bishopmuseum.org. Archived from the original on 2019-06-11.
- Elliott, David (1997). "Some limitations of semi-closed rebreathers". South Pacific Underwater Medicine Society Journal. 27 (1). ISSN 0813-1988. OCLC 16986801. Retrieved 2008-06-14.
- Daucherty, RL; Franzini, JB (1977). Fluid Mechanics with Engineering Applications (7th ed.). Kogakusha: McGraw-Hill. pp. 257–261. ISBN 0-07-085144-1.
- Larsson, A. (2000). "The Interspiro DCSC". www.teknosofen.com. Retrieved 30 April 2013.
- Shreeves, K & Richardson, D (2006). "Mixed-Gas Closed-Circuit Rebreathers: An Overview of Use in Sport Diving and Application to Deep Scientific Diving". In: Lang, MA and Smith, NE (Eds.). Proceedings of Advanced Scientific Diving Workshop. Smithsonian Institution, Washington, DC. OCLC 70691158. Retrieved 2008-06-14.
- Kelley, JS; Herron, JM; Dean, WW; Sundstrom, EB (1968). "Mechanical and Operational Tests of a Russian 'Superoxide' Rebreather". US Navy Experimental Diving Unit Technical Report. NEDU-Evaluation-11-68. Retrieved 2009-01-31.
- Robinson, Brian. Taylor, Fionn (ed.). "Breathing Apparatus". Bob's History of Mining. Retrieved 27 December 2013.
- Fischel, H. (1970). "Closed circuit cryogenic SCUBA". Equipment for the Working Diver - 1970 Symposium. Washington, DC: Marine Technology Society: 229–244.
- Cushman, L. (1979) [June 1969]. "Cryogenic Rebreather". Skin Diver Magazine: 29–31, 85–87 – via Aqua Corps magazine, N7, 28. Also available online via the Rebreather Site
- Bech, JW. "S-600 G and SS100 cryogenic rebreather". therebreathersite.nl. Retrieved 28 May 2019.
- "Popular mechanics (ru), №7(81) June 2009". Retrieved 2009-07-17.
- "Sportsmen-podvodnik journal, 1977" (PDF). Retrieved 2008-07-17.
- Richardson, Drew; Menduno, Michael; Shreeves, Karl (1996). "Proceedings of Rebreather Forum 2.0". Diving Science and Technology Workshop.: 286. Retrieved 2008-08-20.
- "DESCO 29019 U.S. Navy Helium Diving Helmet w/Double Exhaust Valve". DESCO. Retrieved 2 July 2019.
- "Going deep". divingheritage.com. Retrieved 2 July 2019.
- "The OBS A/S reclaim helmet". DiveScrap Index - the scrapbook of diving history. Retrieved 2 July 2019.
- Crawford, J. (2016). "8.5.1 Helium recovery systems". Offshore Installation Practice (revised ed.). Butterworth-Heinemann. pp. 150–155. ISBN 9781483163192.
- Staff, US Navy (2006). "15". US Navy Diving Manual, 6th revision. United States: US Naval Sea Systems Command. Retrieved 15 June 2008.
- Hendricks, David M; Pollock, Neal W; Natoli, Michael J; Hobbs, Gene W; Gabrielova, Ivana; Vann, Richard D (1999). "Mountaineering oxygen mask efficiency at 4572 m.". In: Roach RC, Wagner PD, Hackett PH. Hypoxia: Into the Next Millennium (Advances in Experimental Medicine and Biology Series). Kluwer Academic: New York: 387–388.
- Hunt, John (1953). The Ascent of Everest. London: Hodder & Stoughton. pp. 257–262.
- staff (2003-08-18). "Breathing Circuit". University of Florida. Retrieved 2013-04-25.
- Ravishankar, M. "Anesthesia breathing machines: an in-depth review". www.capnography.com. Archived from the original on 17 May 2013. Retrieved 30 April 2013.
- staff (2003-08-18). "Mechanical and Manual Ventilation Systems". University of Florida. Retrieved 2013-04-25.
- staff (2003-08-18). "The Scavenging System". University of Florida. Retrieved 2013-04-25.
- staff (2011-02-14). "The Anesthesia Machine". University of Florida. Retrieved 2013-04-25.
- Fischler IS, Kaschub CE, Lizdas DE, Lampotang S (2008). "Understanding of anesthesia machine function is enhanced with a transparent reality simulation". Simul Healthc. 3 (1): 26–32. doi:10.1097/SIH.0b013e31816366d3. PMID 19088639. Retrieved 2013-04-25.
- "OC – DSV – BOV – FFM page". www.therebreathersite.nl. 8 November 2010. Retrieved 2010-12-29.
- Reynolds, Glen Harlan (December 2006). "Seeking New Depths". Popular Mechanics. 183 (12): 58.
- Norfleet, W & Horn, W (2003). "Carbon Dioxide Scrubbing Capabilities of Two New Non-Powered Technologies". US Naval Submarine Medical Research Center Technical Report. NSMRL-TR-1228. Retrieved 2008-06-13.
- ExtendAir-brand - www.microporeinc.com
- Chapple, JCB; Eaton, David J. "Development of the Canadian Underwater Mine Apparatus and the CUMA Mine Countermeasures dive system". Defence R&D Canada Technical Report. Defence R&D Canada (DCIEM 92–06). Retrieved 2009-03-31. section 1.2.a
- Bech, Janwillem (ed.). "Early Russian Epron-1 rebreather". Retrieved 19 December 2017.
- Bech, Janwillem (ed.). "Photos Selbstretter Modell 180". Retrieved 19 December 2017.
- Lillo RS, Ruby A, Gummin DD, Porter WR, Caldwell JM (March 1996). "Chemical safety of U.S. Navy Fleet soda lime". Undersea and Hyperbaric Medicine Journal. 23 (1): 43–53. PMID 8653065. Retrieved 2008-06-09.
- Warkander, Dan E (2007). "Development of a scrubber gauge for closed-circuit diving". Undersea and Hyperbaric Medicine Abstract. 34. Retrieved 2008-04-25.
- "Ambient Pressure Diving Ltd". apdiving.com. Archived from the original on 2013-11-06.
- Historical Diving Times #42 Summer 2007, p27
- Staff. "Equipements des Commandos Marine" (in French). Archived from the original on 26 May 2013. Retrieved 11 October 2013.
- "KISS Closed Circuit Rebreather". Archived from the original on 2008-09-19. Retrieved 2013-10-09.
- http://www.ukdiving.co.uk/equipment/articles/phibian.html
- Williams, Des. "Ted Eldred's Porpoise Oxygen Rebreather 1946". Historical Diving Times, No. 38 Winter 2006. Historical Diving Society. pp. 5–8. Retrieved 12 December 2016 – via www.therebreathersite.nl.
- "Carbon Dioxide Monitoring". Lungfish Dive Systems.
Information sources
- Vann, R.D.; Denoble, P.J.; Pollock, N.W., eds. (2014). Rebreather Forum 3 Proceedings. AAUS / DAN / PADI (PDF) (Report). Durham, North Carolina. ISBN 978-0-9800423-9-9.
- Rebreather Forum 3 Free lectures online recorded at Rebreather Forum 3
- RebreatherPro Free searchable multimedia resource for rebreather divers
- Rebreather Scuba Diving Rebreather world contains further information on rebreathers. The site includes a Rebreather library and Rebreather Forums, and Rebreather Trips, Vacations, and Holidays.
- Richard Pyle's rebreather page (archived)
- The Rebreather Site Information on many makes of rebreathers
- Shallow Water Blackout
- Teknosofen homepage Åke's Rebreather Related Page
- Quick, D (May 1970). A History Of Closed Circuit Oxygen Underwater Breathing Apparatus (Report) – via Rubicon Research Repository.
- US Navy (1 December 2016). U.S. Navy Diving Manual Revision 7 SS521-AG-PRO-010 0910-LP-115-1921 (PDF). Washington, DC.: US Naval Sea Systems Command.
External links
- Anesthesia breathing systems
- NIOSH Docket # 123, titled "Reevaluation of NIOSH limitations on and precaution for safe use of positive-pressure closed-circuit SCBA" is available at the link https://web.archive.org/web/20121025064311/http://www.cdc.gov/niosh/review/public/123/default.html
![]() |
Wikimedia Commons has media related to Rebreathers. |