Food packaging
Food packaging is packaging for food. A package provides protection, tampering resistance, and special physical, chemical, or biological needs. It may bear a nutrition facts label and other information about food being offered for sale.

History
Packaging of food products have seen a vast transformation in technology usage and application from the stone age to the industrial revolution
7000 BC: The adoption of pottery and glass which saw industrialization around 1500 BC [1]
1800: Nicolas Appert in response to extending shelf life of food for the French Army employed the use of glass bottles in thermal food treatment which was later replaced by metal cans[2]
1870: The use of paper board was launched and corrugated materials patented[3]
1880s: First cereal packaged in a folding box by Quaker Oats[4]
1890s: Crown cap for glass bottles was patented by William Painter [5]
1940s: Aerosol was first used by the marines during the world war II in pesticides application[6]
1960s: Development of the two-piece drawn and wall-ironed metal cans in the USA, the ring- pull opener and the Tetra Brik Aseptic carton package[7]
1970s: 1970 Bar code system was introduced in the retail and manufacturing industry. PET plastic blow-mold bottle technology widely used in the beverage industry was introduced[6]
1990s: The application of digital printing on food packages became widely adopted
Plastic packaging saw its inaugural use during the world war II even though materials employed in its manufacturing such as cellulose nitrate, styrene and vinyl chloride were discovered in the 1800s[8]
Functions
Packaging and package labeling have several objectives[9] [10]
- Physical protection - The food enclosed in the package may require protection from, among , shock, vibration, compression, temperature, bacteria, etc.
- Barrier protection - A barrier from oxygen, water vapor, dust, etc., is often required. Permeation is a critical factor in design. Some packages contain desiccants or oxygen absorbers to help extend shelf life. Modified atmospheres or controlled atmospheres are also maintained in some food packages. Keeping the contents clean, fresh, and safe for the intended shelf life is a primary function.
- Containment or agglomeration - Small items are typically grouped together in one package to allow efficient handling. Liquids, powders, and granular materials need containment.
- Information transmission - Packages and labels communicate how to use, transport, recycle, or dispose of the package or product. Some types of information are required by governments.
- Marketing - The packaging and labels can be used by marketers to encourage potential buyers to purchase the product. Aesthetically pleasing and eye-appealing food presentations can encourage people to consider the contents. Package design has been an important and constantly evolving phenomenon for several decades. Marketing communications and graphic design are applied to the surface of the package and (in many cases) the point of sale display. The colour of the package plays a significant role in evoking emotions that persuade the consumer to make the purchase.[11]
- Security - Packaging can play an important role in reducing the security risks of shipment. Packages can be made with improved tamper resistance to deter tampering and also can have tamper-evident features to help indicate tampering. Packages can be engineered to help reduce the risks of package pilferage; some package constructions are more resistant to pilferage and some have pilfer-indicating seals. Packages may include authentication seals to help indicate that the package and contents are not counterfeit. Packages also can include anti-theft devices, such as dye packs, RFID tags, or electronic article surveillance tags, that can be activated or detected by devices at exit points and require specialized tools to deactivate. Using packaging in this way is a means of retail loss prevention.
- Convenience - Packages can have features which add convenience in distribution, handling, stacking, display, sale, opening, reclosing, use, and reuse.
- Portion control - Single-serving packaging has a precise amount of contents to control usage. Bulk commodities (such as salt) can be divided into packages that are a more suitable size for individual households. It also aids the control of inventory: selling sealed one-liter bottles of milk, rather than having people bring their own bottles to fill themselves.
Types
The above materials are fashioned into different types of food packages and containers such as:[12]
Packaging Type | ||
---|---|---|
Aseptic processing | Primary | Liquid whole eggs or dairy products |
Trays | Primary | Portion of fish or meat |
Bags | Primary | Potato chips, apples, rice |
Boxes | Secondary | Corrugated box of primary packages: box of cereal cartons, frozen pizzas |
Cans | Primary | Can of tomato soup |
Cartons, coated paper | Primary | Carton of eggs, milk or juice cartons |
Flexible packaging | Primary | Bagged salad |
Pallets | Tertiary | A series of boxes on a single pallet used to transport from the manufacturing plant to a distribution center |
Wrappers | Tertiary | Used to wrap the boxes on the pallet for transport |
Primary packaging is the main package that holds the food that is being processed. Secondary packaging combines the primary packages into one box being made. Tertiary packaging combines all of the secondary packages into one pallet.
Gallery
- Bagged cake mix
- Biscuit components: plastic bottles, paper bag
- Container for bulk vegetable oil
- Frozen processed food freezer in supermarket
- Bag in box; box wine
- Glass milk bottle and paperboard milk carton
- Silk tea bag
- Coffee beans in burlap bags, gunny sacks
- Bushel baskets of fruit
- Tea tin, can with removable cover
- Folding cartons of cereal
- Drink boxes
- Packaged apples
- Fresh fish in plastic shrink-wrapped tray
- Shrink-wrapped frozen pork
- Military MRE, bean and rice burrito in retort pouch
- Condiments and spices
- Aluminum can with an easy-open, full pull-out end
- A Dip & Squeeze ketchup container
Packaging machines
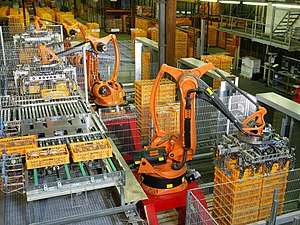
A choice of packaging machinery requires consideration of technical capabilities, labor requirements, worker safety, maintainability, serviceability, reliability, ability to integrate into the packaging line, capital cost, floorspace, flexibility (change-over, materials, etc.), energy usage, quality of outgoing packages, qualifications (for food, pharmaceuticals, etc.), throughput, efficiency, productivity, and ergonomics, at a minimum.
Packaging machines may be of the following general types:
- Autocoding label and date verification
- Blister-, skin- and vacuum-packaging machines
- Capping, over-capping, lidding, closing, seaming and sealing machines
- Cartoning machines
- Case and tray forming, packing, unpacking, closing and sealing Machines
- Check weighing machines
- Cleaning, sterilizing, cooling and drying machines
- Conveying and accumulating machines
- Feeding, orienting, and placing machines
- Filling machines for liquid and powdered products
- Package filling and closing Machines
- Form, fill and seal machines
- Inspecting, detecting and checkweighing machines
- Palletizing, depalletizing, and pallet unitizing machines
- Labeling, marking, and other product identification machines
- Wrapping machines
- Converting machines
Reducing food packaging
Reduced packaging and sustainable packaging are becoming more frequent. The motivations can be government regulations, consumer pressure, retailer pressure, and cost control. Reduced packaging often saves packaging costs.
In the UK, a Local Government Association survey produced by the British Market Research Bureau compared a range of outlets to buy 29 common food items and found that small local retailers and market traders "produced less packaging and more that could be recycled than the larger supermarkets."[14]
Recycling of food packaging
After use, organic matter that is still in the food packaging needs to be separated from the packaging. This may also require rinsing of the food packaging.
Food packaging is created through the use of a wide variety of plastics and metals, papers, and glass materials. Recycling these products differs from the act of literally reusing them in the manner that the recycling process has its own algorithm which includes collecting, sourcing, processing, manufacturing and marketing these products. According to the Environmental Protection Agency of the United States the recycling rate has been steadily on the rise with data reporting that in 2005 40% of the food packaging and containers that were created were recycled and not just thrown away.
Trends in food packaging
- Numerous reports industry associations agree that use of smart indicators will increase. There are a number of different indicators with different benefits for food producers, consumers and retailers.
- Temperature recorders are used to monitor products shipped in a cold chain and to help validate the cold chain. Digital temperature data loggers measure and record the temperature history of food shipments. They sometimes have temperatures displayed on the indicator or have other output (lights, etc.): The data from a shipment can be downloaded (cable, RFID, etc.) to a computer for further analysis. These help identify if there has been temperature abuse of products and can help determine the remaining shelf life.[15] They can also help determine the time of temperature extremes during shipment so corrective measures can be taken.
- Time temperature indicators integrate the time and temperature experienced by the indicator and adjacent foods. Some use chemical reactions that result in a color change while others use the migration of a dye through a filter media. To the degree that these physical changes in the indicator match the degradation rate of the food, the indicator can help indicate probable food degradation.[16]
- Radio Frequency Identification is applied to food packages for supply chain control and has shown a significant benefit in allowing food producers and retailers create full real time visibility of their supply chain.
- Plastic packaging being used is usually non-biodegradable due to possible interactions with the food. Also, biodegradable polymers often require special composting conditions to properly degrade. Normal sealed landfill conditions do not promote biodegradation. Biodegradable plastics includes biodegradable films and coatings synthesized from organic materials and microbial polymers. Some package materials are edible. For example, pharmaceuticals are sometimes in capsules made of gelatin, starch, potato or other materials. Newer bioplastics, films and products are being developed.[17]
- Barcodes have been used for decades in packaging many products. 2D barcodes used in Autocoding are increasingly applied to food packaging to ensure products are correctly packaged and date coded.
- The ability of a package to fully empty or dispense a viscous food is somewhat dependent on the surface energy of the inner walls of the container. The use of superhydrophobic surfaces is useful but can be further improved by using new lubricant-impregnated surfaces.[18]
Food safety and public health
It is critical to maintain food safety during processing[19] , packaging, storage, logistics (including cold chain), sale, and use. Conformance to applicable regulations is mandatory. Some are country specific such as the US Food and Drug Administration and the US Department of Agriculture; others are regional such as the European Food Safety Authority. Certification programs such as the Global Food Safety Initiative are sometimes used. Food packaging considerations may include: use of hazard analysis and critical control points, verification and validation protocols, Good manufacturing practices, use of an effective quality management system, track and trace systems, and requirements for label content. Special food contact materials are used when the package is in direct contact with the food product. Depending on the packaging operation and the food, packaging machinery often needs specified daily wash-down and cleaning procedures.[20]
Health risks of materials and chemicals used in food packaging need to be carefully controlled. Carcinogens, toxic chemicals, mutagens etc. need to be eliminated from food contact and potential migration into foods.[21][22] Besides these, the consumers need to be aware of certain chemical products that are packaged exactly like food products to attract them. Most of them have pictures of fruits and the containers also resemble food packages. However, they can get consumed by kids or careless adults which can lead to poisoning.[23]
Manufacturing
Packaging lines may have a variety of equipment types: integration of automated systems can be a challenge.[24] All aspects of food production, including packaging, are tightly controlled and have regulatory requirements. Uniformity, cleanliness and other requirements are needed to maintain Good Manufacturing Practices.
Product safety management is vital. A complete Quality Management System must be in place. Hazard analysis and critical control points is one methodology which has been proven useful. Verification and validation involves collecting documentary evidence of all aspects of compliance. Quality assurance extends beyond the packaging operations through distribution and cold chain management.
See also
- Codex Alimentarius
- Dietary supplement
- Autocoding
- Food and Bioprocess Technology
- Calabash
- Food fortification
- Food grading
- Food preservation
- Food rheology
- Food safety
- Food storage
- Food waste
- ISO 22000
- Nutraceutical
- Packaging waste
- Food labeling regulations
- United Kingdom food labeling regulations
- Packaging industry
- Washdown
Notes and references
- "A Brief History of Packaging". ufdc.ufl.edu. Retrieved 22 May 2019.
- Encyclopedia of food science and technology. Francis, F. J. (Frederick John), 1921- (2nd. ed.). New York: Wiley. 2000. ISBN 0471192856. OCLC 41143092.CS1 maint: others (link)
- Bi, Liu Ju (June 2012). "Research on Corrugated Cardboard and its Application". Advanced Materials Research. 535-537: 2171–2176. doi:10.4028/www.scientific.net/AMR.535-537.2171. ISSN 1662-8985.
- Hine, Thomas, 1947- (1995). The total package : the evolution and secret meanings of boxes, bottles, cans, and tubes (1st ed.). Boston: Little, Brown. ISBN 0316364800. OCLC 31288019.CS1 maint: multiple names: authors list (link)
- Opie, Robert, 1947- (1989). Packaging source book. Macdonald Orbis. ISBN 0356176657. OCLC 19776457.CS1 maint: multiple names: authors list (link)
- Arvanitoyannis, Is (30 April 2005). "Food packaging technology. Edited by R Coles, D McDowell and MJ Kirwan. Blackwell Publishing, CRC Press, Oxford, 2003. 346 pp ISBN 0-849-39788-X". Journal of the Science of Food and Agriculture. 85 (6): 1072. doi:10.1002/jsfa.2089. ISSN 0022-5142.
- Arvanitoyannis, IS (2005). "Food packaging technology. Edited by R Coles, D McDowell and MJ Kirwan. Blackwell Publishing, CRC Press, Oxford, 2003. 346 pp ISBN 0-8493-9788-X". Journal of the Science of Food and Agriculture. 85 (6): 1072. doi:10.1002/jsfa.2089. ISSN 0022-5142.
- Risch, Sara J. (23 September 2009). "Food Packaging History and Innovations". Journal of Agricultural and Food Chemistry. 57 (18): 8089–8092. doi:10.1021/jf900040r. ISSN 0021-8561. PMID 19719135.
- Bix, L; Nora Rifon; Hugh Lockhart; Javier de la Fuente (2003). The Packaging Matrix: Linking Package Design Criteria to the Marketing Mix (PDF). IDS Packaging. Archived from the original (PDF) on 17 December 2008. Retrieved 11 December 2008.
- Marsh, K (2007). "Food Packaging—Roles, Materials, and Environmental Issues" (PDF). Journal of Food Science. 72 (3): 39–54. Retrieved 21 September 2018.
- "Importance of Product Packaging in Marketing".
- Shaw, Randy (16 February 2013). "Food Packaging: 9 Types and Differences Explained". Assemblies Unlimited. Retrieved 19 June 2015.
- Claudio, Luz (2012). "Our Food: Packaging & Public Health". Environmental Health Perspectives. 120 (6): A232–A237. doi:10.1289/ehp.120-a232. JSTOR 41549064. PMC 3385451. PMID 22659036.
- "Farmer markets better at reducing waste".
- Meyers, T (June 2007). "RFID Shelf-life Monitoring Helps Resolve Disputes". RFID Journal.
- Riva, Marco; Piergiovanni, Schiraldi, Luciano; Schiraldi, Alberto (January 2001). "Performances of time-temperature indicators in the study of temperature exposure of packaged fresh foods". Packaging Technology and Science. 14 (1): 1–39. doi:10.1002/pts.521.
- EDIBLE COATINGS TO IMPROVE FOOD QUALITY AND FOOD SAFETY AND MINIMIZE PACKAGING COST, USDA, 2011, retrieved 18 March 2013
- Smith, J D; Rajeev Dhiman; Sushant Anand; Ernesto Reza-Garduno; Robert E. Cohen; Gareth H. McKinley; Kripa K. Varanasi (2013). "Droplet mobility on lubricant-impregnated surfaces". Soft Matter. 19 (6): 1972–1980. Bibcode:2013SMat....9.1772S. doi:10.1039/c2sm27032c. hdl:1721.1/79068.
- Hron, J; T. Macák; A. Jindrova (2012). "Evaluation of economic efficiency of process improvement in food packaging" (PDF). Acta Universitatis Agriculturae et Silviculturae Mendelianae Brunensis. LX (2): 115–120. doi:10.11118/actaun201260040115. Archived from the original (PDF) on 20 April 2014. Retrieved 20 April 2014.
- "Regulation of the U.S. Food Processing Sector". NDSU. Retrieved 19 June 2015.
- Stephens, Pippa (19 February 2014). "Food packaging health risk 'unknown'". BBC News – via www.bbc.com.
- Claudio, L (2012). "Our food: packaging & public health". Environ. Health Perspect. 120 (6): A232–7. doi:10.1289/ehp.120-a232. PMC 3385451. PMID 22659036.
- Basso, F.; Bouillé, J.; Le Goff, K.; Robert-Demontrond, P.; Oullier, O. (31 March 2016). "Assessing the Role of Shape and Label in the Misleading Packaging of Food Imitating Products: From Empirical Evidence to Policy Recommendation". Frontiers in Psychology. 7: 450. doi:10.3389/fpsyg.2016.00450. PMC 4814518. PMID 27065919.
- Mahalik, N P (2009). "Processing and packaging automation systems: a review". Sens. & Instrumen. Food Qual. 3: 12–25. doi:10.1007/s11694-009-9076-2.
Bibliography
- Hans-Jürgen Bässler und Frank Lehmann : Containment Technology: Progress in the Pharmaceutical and Food Processing Industry. Springer, Berlin 2013, ISBN 978-3642392917
- Heldman, D.R. ed (2003). "Encyclopedia of Agricultural, Food, and Biological Engineering". New York: Marcel Dekker
- Potter, N.N. and J.H. Hotchkiss. (1995). "Food Science", Fifth Edition.New York: Chapman & Hall. pp. 478–513.
- Robertson, G. L. (2013). "Food Packaging: Principles & Practice". CRC Press. ISBN 978-1-4398-6241-4
- Selke, S, (1994). "Packaging and the Environment". ISBN 1-56676-104-2
- Selke, S, (2004) "Plastics Packaging", ISBN 1-56990-372-7
- Soroka, W. (2009). "Fundamentals of Packaging Technology". Institute of Packaging Professionals. ISBN 1-930268-28-9
- Stillwell, E. J, (1991) "Packaging for the Environment", A. D. Little, 1991, ISBN 0-8144-5074-1
- Yam, K. L., "Encyclopedia of Packaging Technology", John Wiley & Sons, 2009, ISBN 978-0-470-08704-6
External links
- "Food Packaging -- Roles, Materials, and Environmental Issues - IFT.org". www.ift.org. Retrieved 3 December 2018.