Slip sheet
Slip sheets are thin pallet-sized sheets made of plastic, heavy laminated kraft paperboard, or corrugated fiberboard used in commercial shipping.[1][2][3][4] Often, these replace the use of traditional wooden pallets. The unit load is usually stretch wrapped or shrink wrapped for stability.[5]
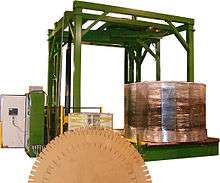
Description
The slip sheet is used as a pallet support device in vehicle delivery and transportation of products. When slip sheets are supported by a pallet board, flat load carrying surface, or a cart or fork lift truck, the structural strength of the slip sheet supports the product load's weight. With the slip sheet supported by one of these transportation devices the unit load can easily be transported both internally within a facility and externally between two facility locations. It helps to decrease the human intervention in order to provide safety and efficiency of the work.
Slip sheet types
There are several types of slip sheets that can be used for the transportation of a unit load depending upon the desired use of the sheet. The slip sheet is shaped and dimensioned to the size of the product or unit load. The type of slip sheet varies depending on both the number of lip extensions and the material from which it is manufactured.
The variation used would depend on the loading patterns, unit load parameters, and desired maneuverability of the slip sheet/unit load. Normally, the thickness of the slip sheet is less than 0.5 inches.
The slip sheet has a four to six inch lip (tab) that extends beyond one or more of the sides of the slip sheet. The lip extensions permit a push-pull device to lift the slip sheet unit load.
Single lip
The first type of slip sheet is the single lip (tab) slip sheet.
With a single lip, the lip faces the narrow part of the rectangular shaped unit load and the delivery truck door. This slip sheet variation maximizes the delivery truck’s space utilization and loading and unloading process productivity. Also, with a single lip, the travel path clearance is minimized as the lip faces the unit load carrier.[6]
Multi-lip
The second type of slip sheet is the multi-lip slip sheet. This type of slip sheet is generally used on a container placed onto a railroad car or an ocean delivery vehicle due to the necessary loading/unloading patterns. This allows a loading device to load the slip sheet unit load from one side and an unloading device to unload the load from another side depending on the number and pattern of the remaining lips.
Lip handling options
During the transportation of a slip sheet, there are several options for handling the slip sheet’s lip.
- Leave the lip extended allowing for additional clearance for the travel path.
- Tape the lip against the unit load if additional push-pull activities are required.
- Cut the lip from the slip sheet if no additional push-pull activities are required.
Slip sheet materials
Corrugated
The corrugated fiberboard consists of two kraft liner board outer surfaces with a corrugated interior that is bonded together with adhesive or glue. This bonded material provides the necessary strength for the push-pull device to clamp the slip sheet once or twice. There are several disadvantages associated with this type of slip sheet material including that it is not very durable, moisture resistant, resistant to high humidity or usable in cold storage areas. The advantages associated with this material are low cost, one-way use, and its ability to be moved by a conveyor or lift truck with a slip sheet device.
Fiberboard or solid kraftboard
The fiberboard (thick paperboard) slip sheet consists of several layers of solid kraft paperboard sheets laminated together. The bonding of layers of several flat solid kraftboard sheets increases the slip sheet’s non-tear strength. This, in return, allows the slip sheet to be used several times and in different temperatures. In addition, some fiberboard slip sheets are protected by a plastic coating to improve its use in humid environments. The disadvantages to this type of slip sheet are that it has a medium cost and is not very durable. The advantages with this material are its multiple uses, ability to withstand humid and cold environments, and ability to be handled by conveyors, AGV, or other power unit load transportation devices.
Plastic
The plastic slip sheet is made from recycled high-density polyethylene or polypropylene materials. This type of material allows for greater non-tear strength and an increased number of uses in cold and humid environments. The only disadvantage to the plastic slip sheet is the high cost. Yet, its advantages include longer sheet life, durable lips, ability to be stored in cold or humid environments, and that it can be handled by a roller conveyor, slip sheet lift truck, or powered unit load transportation devices.
Slip sheet vs. pallet
When considering the use of a slip sheet vs. a pallet, there are several advantages and disadvantages associated with both.
Slip sheet advantages
- Using slip sheets instead of wooden pallets allows for 0–30% more products in material handling containers.
- Significant reduction in material handling costs, especially on air shipments.
- Weighs 1/30 as much as wooden pallets, reducing shipping costs.
- Eliminates the need for pallet exchange.
- Reusable and reliable.
- Most are recyclable.
- Is cost-effective.
- Unlike wooden pallets slip sheets are not subject to phytosanitary restrictions.
Slip sheet disadvantages
- Pallets provide a greater clearance between the floor and the unit load, an advantage when loading extra cargo into a container, but they take up more space.
- Slip sheet usage requires special, relatively low-cost attachments on transportation devices such as a lift truck.
- When used alone, pallets provide more structural support than slip sheets.
- Pallets are easily compatible with cranes, forklifts and handjacks
- The floor clearance provided by a pallet can prevent the load from being damaged by wet floors.
- Dragging a slip sheet load across a rough or bumpy floor can damage the load.
- Lift truck attachment reduces load capacity, except when 'Roller Forks' are used.
- Increases fork lift pick up and set down times by up to 60%, when 'Roller Forks' are used.
- With Push Pull attachment could save the slip sheet, Roller Forks not.
See also
References
- US3776145A, Anderson, Mackes, "Slip pallet", published 1972
- US4042127A, Brossia, "Slip pallet and divider sheet", published 1977
- US5613447A, Tricket, "Slip sheet for transporting goods", published 1997
- US5503517A, Derby, "Slip sheet and method of use of same", published 1996
- Laundrie (1986), "Unitizing Goods on Pallets and Slipsheets, FPL-GTR-52" (PDF), US Forest Products Laboratory, retrieved 7 April 2020
- "Slipsheets". North Carolina State University. Retrieved 2017-11-29.
Further reading
- Yam, K.L., "Encyclopedia of Packaging Technology", John Wiley & Sons, 2009, ISBN 978-0-470-08704-6
- Fiedler, R. M, Distribution Packaging Technology, Institute of Packaging Professionals, 1995, OCLC 33164940
- McKinlay, A. H., Transport Packaging, 2nd ed., Institute of Packaging Professionals, 2004, OCLC 60361752
- MHIA/ANSI MH1–2005 Pallets, Slip Sheets, and Other Bases for Unit Loads
- Kay, M.G., 2012, Material Handling Equipment, Retrieved 2014-10-02.