Road surface
A road surface, or pavement, is the durable surface material laid down on an area intended to sustain vehicular or foot traffic, such as a road or walkway. In the past, gravel road surfaces, cobblestone and granite setts were extensively used, but thet have mostly been replaced by asphalt or concrete laid on a compacted base course. Asphalt mixtures have been used in pavement construction since the beginning of the 20th century and are of two types: metalled roads and unmetalled roads. Metalled roadways are made to sustain vehicular load and so are usually made on frequently-used roads. Unmetalled roads, also known as gravel roads, are rough and can sustain less weight. Road surfaces are frequently marked to guide traffic.
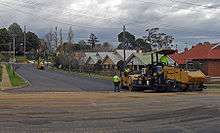
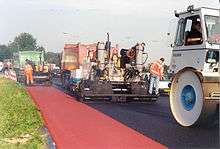
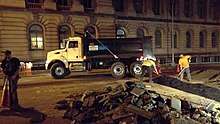
Today, permeable paving methods are beginning to be used for low-impact roadways and walkways. Pavements are crucial to countries such as United States and Canada, which heavily depend on road transportation. Therefore, research projects such as Long-Term Pavement Performance have been launched to optimize the life cycle of different road surfaces.[1][2][3][4]
Asphalt
.jpg)
Asphalt (specifically, asphalt concrete), sometimes called flexible pavement due to the nature in which it distributes loads, has been widely used since the 1920s. The viscous nature of the bitumen binder allows asphalt concrete to sustain significant plastic deformation, although fatigue from repeated loading over time is the most common failure mechanism. Most asphalt surfaces are laid on a gravel base, which is generally at least as thick as the asphalt layer, although some 'full depth' asphalt surfaces are laid directly on the native subgrade. In areas with very soft or expansive subgrades such as clay or peat, thick gravel bases or stabilization of the subgrade with Portland cement or lime may be required. Polypropylene and polyester geosynthetics have also been used for this purpose[5] and in some northern countries, a layer of polystyrene boards have been used to delay and minimize frost penetration into the subgrade.[6]
Depending on the temperature at which it is applied, asphalt is categorized as hot mix, warm mix, half warm mix, or cold mix.[7] Hot mix asphalt is applied at temperatures over 300 °F (150 °C) with a free floating screed. Warm mix asphalt is applied at temperatures of 200–250 °F (95–120 °C), resulting in reduced energy usage and emissions of volatile organic compounds.[8] Cold mix asphalt is often used on lower-volume rural roads, where hot mix asphalt would cool too much on the long trip from the asphalt plant to the construction site.[9] An asphalt concrete surface will generally be constructed for high-volume primary highways having an average annual daily traffic load greater than 1200 vehicles per day.[10] Advantages of asphalt roadways include relatively low noise, relatively low cost compared with other paving methods, and perceived ease of repair. Disadvantages include less durability than other paving methods, less tensile strength than concrete, the tendency to become slick and soft in hot weather and a certain amount of hydrocarbon pollution to soil and groundwater or waterways.
In the mid-1960s, rubberized asphalt was used for the first time, mixing crumb rubber from used tires with asphalt.[11] While a potential use for tires that would otherwise fill landfills and present a fire hazard, rubberized asphalt has shown greater incidence of wear in freeze-thaw cycles in temperate zones due to non-homogeneous expansion and contraction with non-rubber components. The application of rubberized asphalt is more temperature-sensitive, and in many locations can only be applied at certain times of the year.
Study results of the long-term acoustic benefits of rubberized asphalt are inconclusive. Initial application of rubberized asphalt may provide 3–5 decibels (dB) reduction in tire-pavement source noise emissions; however, this translates to only 1–3 decibels (dB) in total traffic noise level reduction (due to the other components of traffic noise). Compared to traditional passive attenuating measures (e.g., noise walls and earth berms), rubberized asphalt provides shorter-lasting and lesser acoustic benefits at typically much greater expense.
Concrete
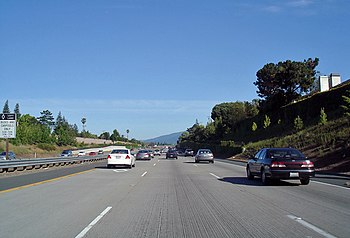
Concrete surfaces (specifically, Portland cement concrete) are created using a concrete mix of Portland cement, coarse aggregate, sand, and water. In virtually all modern mixes there will also be various admixtures added to increase workability, reduce the required amount of water, mitigate harmful chemical reactions and for other beneficial purposes. In many cases there will also be Portland cement substitutes added, such as fly ash. This can reduce the cost of the concrete and improve its physical properties. The material is applied in a freshly mixed slurry, and worked mechanically to compact the interior and force some of the cement slurry to the surface to produce a smoother, denser surface free from honeycombing. The water allows the mix to combine molecularly in a chemical reaction called hydration.
Concrete surfaces have been classified into three common types: jointed plain (JPCP), jointed reinforced (JRCP) and continuously reinforced (CRCP). The one item that distinguishes each type is the jointing system used to control crack development.
One of the major advantages of concrete pavements is they are typically stronger and more durable than asphalt roadways. They also can be grooved to provide a durable skid-resistant surface. A notable disadvantage is that they typically can have a higher initial cost, and can be more time-consuming to construct. This cost can typically be offset through the long life cycle of the pavement. Concrete pavement can be maintained over time utilizing a series of methods known as concrete pavement restoration which include diamond grinding, dowel bar retrofits, joint and crack sealing, cross-stitching, etc. Diamond grinding is also useful in reducing noise and restoring skid resistance in older concrete pavement.[12][13]
The first street in the United States to be paved with concrete was Court Avenue in Bellefontaine, Ohio in 1893.[14][15] The first mile of concrete pavement in the United States was on Woodward Avenue in Detroit, Michigan in 1909.[16] Following these pioneering uses, the Lincoln Highway Association, established in October 1913 to oversee the creation of one of the United States' earliest east-west transcontinental highways for the then-new automobile, began to establish "seedling miles" of specifically concrete-paved roadbed in various places in the American Midwest, starting in 1914 west of Malta, Illinois, while using concrete with the specified concrete "ideal section" for the Lincoln Highway in Lake County, Indiana during 1922 and 1923.[17]
Concrete roadways may produce more noise than asphalt, due to tire noise on cracks and expansion joints. A concrete pavement composed of multiple slabs of uniform size will produce a periodic sound and vibration in each vehicle as its tires pass over each expansion joint. These monotonous repeated sounds and vibrations can cause a fatiguing or hypnotic effect upon the driver over the course of a long journey.
Composite pavement
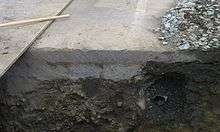
Composite pavements combine a Portland cement concrete sublayer with an asphalt overlay. They are usually used to rehabilitate existing roadways rather than in new construction.
Asphalt overlays are sometimes laid over distressed concrete to restore a smooth wearing surface.[18] A disadvantage of this method is that movement in the joints between the underlying concrete slabs, whether from thermal expansion and contraction, or from deflection of the concrete slabs from truck axle loads, usually causes reflective cracks in the asphalt. To decrease reflective cracking, concrete pavement is broken apart through a break and seat, crack and seat, or rubblization process. Geosynthetics can be used for reflective crack control.[19] With break and seat and crack and seat processes, a heavy weight is dropped on the concrete to induce cracking, then a heavy roller is used to seat the resultant pieces into the subbase.
The main difference between the two processes is the equipment used to break the concrete pavement and the size of the resulting pieces. The theory is frequent small cracks will spread thermal stress over a wider area than infrequent large joints, reducing the stress on the overlying asphalt pavement. "Rubblization" is a more complete fracturing of the old, worn-out concrete, effectively converting the old pavement into an aggregate base for a new asphalt road.[20]
The whitetopping process uses Portland cement concrete to resurface a distressed asphalt road.
Recycling
Distressed road materials can be reused when rehabilitating a roadway. The existing pavement is ground or broken up into small pieces, through a process called milling. It can then be transported to an asphalt or concrete plant and incorporated into new pavement, or recycled in place to form the base or subbase for new pavement. Some methods used include:
In-place recycling
- Rubblizing of concrete pavement. Existing concrete pavement is broken into gravel-sized particles. Any steel reinforcing is removed, then the remaining gravel-sized particles are compacted and overlaid with asphalt pavement.[21]
- Cold in-place recycling. Bituminous pavement is ground or milled into small particles. The asphalt millings are blended with a small amount of asphalt emulsion or foamed bitumen, paved and compacted, allowed to cure for seven to ten days, then overlaid with asphalt.[22]
- Hot in-place recycling. Bituminous pavement is heated to 250 to 300 °F (120 to 150 °C), milled, combined with a rejuvenating agent or virgin asphalt binder, and compacted. It may then be overlaid with a new asphalt overlay. This process only recycles the top two inches (50 mm) or less, so it can be used to correct rutting, polishing or other surface defects. It is not a good procedure for roads with structural failures. It also generates high heat and vapor emissions, and may not be a good candidate for built-up areas.[22]
- Full depth reclamation is a process which pulverizes the full thickness of the asphalt pavement and some of the underlying material to provide a uniform blend of material. A binding agent may be mixed in to form a base course for the new pavement, or it may be left unbound to form a subbase course. Common binding agents include asphalt emulsion, fly ash, Portland cement or calcium chloride. It can also be mixed with aggregate, recycled asphalt millings, or crushed Portland cement to improve the gradation of the material, and can provide a design life cycle of 30 years with proper lab testing and field verification.[22][23]
Bituminous surface
Bituminous surface treatment (BST) or chipseal is used mainly on low-traffic roads, but also as a sealing coat to rejuvenate an asphalt concrete pavement. It generally consists of aggregate spread over a sprayed-on asphalt emulsion or cut-back asphalt cement. The aggregate is then embedded into the asphalt by rolling it, typically with a rubber-tired roller. This type of surface is described by a wide variety of regional terms including "chip seal", "tar and chip", "oil and stone", "seal coat", "sprayed seal"[24], "surface dressing",[25] "microsurfacing"[26] or as simply "bitumen."
BST is used on hundreds of miles of the Alaska Highway and other similar roadways in Alaska, the Yukon Territory, and northern British Columbia. The ease of application of BST is one reason for its popularity, but another is its flexibility, which is important when roadways are laid down over unstable terrain that thaws and softens in the spring.
Other types of BSTs include micropaving, slurry seals and Novachip. These are laid down using specialized and proprietary equipment. They are most often used in urban areas where the roughness and loose stone associated with chip seals is considered undesirable.
Thin membrane surface
A thin membrane surface (TMS) is an oil-treated aggregate which is laid down upon a gravel road bed, producing a dust-free road.[27] A TMS road reduces mud problems and provides stone-free roads for local residents where loaded truck traffic is negligible. The TMS layer adds no significant structural strength, and so is used on secondary highways with low traffic volume and minimal weight loading. Construction involves minimal subgrade preparation, following by covering with a 50-to-100-millimetre (2.0–3.9 in) cold mix asphalt aggregate.[10] The Operation Division of the Ministry of Highways and Infrastructure in Saskatchewan has the responsibility of maintaining 6,102 kilometres (3,792 mi) of thin membrane surface (TMS) highways.[28]
Gravel surface
Gravel is known to have been used extensively in the construction of roads by soldiers of the Roman Empire (see Roman road) but in 1998 a limestone-surfaced road, thought to date back to the Bronze Age, was found at Yarnton in Oxfordshire, Britain.[30] Applying gravel, or "metalling", has had two distinct usages in road surfacing. The term road metal refers to the broken stone or cinders used in the construction or repair of roads or railways,[31] and is derived from the Latin metallum, which means both "mine" and "quarry".[32] The term originally referred to the process of creating a gravel roadway. The route of the roadway would first be dug down several feet and, depending on local conditions, French drains may or may not have been added. Next, large stones were placed and compacted, followed by successive layers of smaller stones, until the road surface was composed of small stones compacted into a hard, durable surface. "Road metal" later became the name of stone chippings mixed with tar to form the road-surfacing material tarmac. A road of such material is called a "metalled road" in Britain, a "paved road" in Canada and the US, or a "sealed road" in parts of Canada, Australia and New Zealand.[33]
A granular surface can be used with a traffic volume where the annual average daily traffic is 1,200 vehicles per day or less. There is some structural strength if the road surface combines a sub base and base and is topped with a double-graded seal aggregate with emulsion.[10][34] Besides the 4,929 kilometres (3,063 mi) of granular pavements maintained in Saskatchewan, around 40% of New Zealand roads are unbound granular pavement structures.[28][35]
The decision whether to pave a gravel road or not often hinges on traffic volume. It has been found that maintenance costs for gravel roads often exceed the maintenance costs for paved or surface-treated roads when traffic volumes exceed 200 vehicles per day.[36]
Some communities are finding it makes sense to convert their low-volume paved roads to aggregate surfaces.[37]
Other surfaces
Pavers (or paviours), generally in the form of pre-cast concrete blocks, are often used for aesthetic purposes, or sometimes at port facilities that see long-duration pavement loading. Pavers are rarely used in areas that see high-speed vehicle traffic.
Brick, cobblestone, sett, wood plank, and wood block pavements such as Nicolson pavement, were once common in urban areas throughout the world, but fell out of fashion in most countries, due to the high cost of labor required to lay and maintain them, and are typically only kept for historical or aesthetic reasons. In some countries, however, they are still common in local streets. In the Netherlands, brick paving has made something of a comeback since the adoption of a major nationwide traffic safety program in 1997. From 1998 through 2007, more than 41,000 km of city streets were converted to local access roads with a speed limit of 30 km/h, for the purpose of traffic calming.[38] One popular measure is to use brick paving - the noise and vibration slows motorists down. At the same time, it is not uncommon for cycle paths alongside a road to have a smoother surface than the road itself.[39][40]
Likewise, macadam and tarmac pavements can still sometimes be found buried underneath asphalt concrete or Portland cement concrete pavements, but are rarely constructed today.
There are also other methods and materials to create pavements that have appearance of brick pavements. The first method to create brick texture is to heat an asphalt pavement and use metal wires to imprint a brick pattern using a compactor to create stamped asphalt. A similar method is to use rubber imprinting tools to press over a thin layer of cement to create decorative concrete. Another method is to use a brick pattern stencil and apply a surfacing material over the stencil. Materials that can be applied to give the color of the brick and skid resistance can be in many forms. An example is to use colored polymer-modified concrete slurry which can be applied by screeding or spraying.[41] Another material is aggregate-reinforced thermoplastic which can be heat applied to the top layer of the brick-pattern surface.[42] Other coating materials over stamped asphalt are paints and two-part epoxy coating.[43]
- Concrete pavers
- Polymer cement overlaying to change asphalt pavement to brick texture and color to create decorative crosswalk
Acoustical implications
Roadway surfacing choices are known to affect the intensity and spectrum of sound emanating from the tire/surface interaction.[44] Initial applications of noise studies occurred in the early 1970s. Noise phenomena are highly influenced by vehicle speed.
Roadway surface types contribute differential noise effects of up to 4 dB, with chip seal type and grooved roads being the loudest, and concrete surfaces without spacers being the quietest. Asphaltic surfaces perform intermediately relative to concrete and chip seal. Rubberized asphalt has been shown to give a marginal 3–5 dB reduction in tire-pavement noise emissions, and a marginally discernible 1–3 dB reduction in total road noise emissions when compared to conventional asphalt applications.
- Cobbles
- Rectangles
- Decorative wavy pattern on La Rambla
- Decorative mock-brick pattern
- More decorative brickwork patterns
Surface deterioration
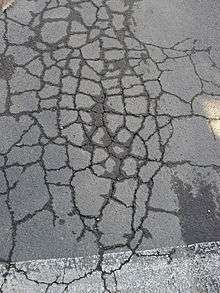
As pavement systems primarily fail due to fatigue (in a manner similar to metals), the damage done to pavement increases with the fourth power of the axle load of the vehicles traveling on it. According to the AASHO Road Test, heavily loaded trucks can do more than 10,000 times the damage done by a normal passenger car. Tax rates for trucks are higher than those for cars in most countries for this reason, though they are not levied in proportion to the damage done.[45] Passenger cars are considered to have little practical effect on a pavement's service life, from a materials fatigue perspective.
Other failure modes include aging and surface abrasion. As years go by, the binder in a bituminous wearing course gets stiffer and less flexible. When it gets "old" enough, the surface will start losing aggregates, and macrotexture depth increases dramatically. If no maintenance action is done quickly on the wearing course, potholes will form. The freeze-thaw cycle in cold climates will dramatically accelerate pavement deterioration, once water can penetrate the surface. Clay and fumed silica nanoparticles may potentially be used as efficient UV-anti aging coatings in asphalt pavements.[46]
If the road is still structurally sound, a bituminous surface treatment, such as a chipseal or surface dressing can prolong the life of the road at low cost. In areas with cold climate, studded tires may be allowed on passenger cars. In Sweden and Finland, studded passenger car tires account for a very large share of pavement rutting.[47]
The physical properties of a stretch of pavement can be tested using a falling weight deflectometer.
Several design methods have been developed to determine the thickness and composition of road surfaces required to carry predicted traffic loads for a given period of time. Pavement design methods are continuously evolving. Among these are the Shell Pavement design method, and the American Association of State Highway and Transportation Officials (AASHTO) 1993/98 "Guide for Design of Pavement Structures". A mechanistic-empirical design guide was developed through the NCHRP process, resulting in the Mechanistic Empirical Pavement Design Guide (MEPDG), which was adopted by AASHTO in 2008, although MEPDG implementation by state departments of transportation has been slow.[48]
Further research by University College London into pavements has led to the development of an indoor, 80-sq-metre artificial pavement at a research centre called Pedestrian Accessibility and Movement Environment Laboratory (PAMELA). It is used to simulate everyday scenarios, from different pavement users to varying pavement conditions.[49] There also exists a research facility near Auburn University, the NCAT Pavement Test Track, that is used to test experimental asphalt pavements for durability.
In addition to repair costs, the condition of a road surface has economic effects for road users. Rolling resistance increases on rough pavement, as does wear and tear of vehicle components. It has been estimated that poor road surfaces cost the average US driver $324 per year in vehicle repairs, or a total of $67 billion. Also, it has been estimated that small improvements in road surface conditions can decrease fuel consumption between 1.8 and 4.7%.[50]
Markings
Road surface markings are used on paved roadways to provide guidance and information to drivers and pedestrians. It can be in the form of mechanical markers such as cat's eyes, botts' dots and rumble strips, or non-mechanical markers such as paints, thermoplastic, plastic and epoxy.
See also
Notes
- Nehme, Jean (14 July 2017). "About Long-Term Pavement Performance". Federal Highway Administration. Retrieved 22 October 2017.
- Raab, Robert (n.d.). "Long-Term Pavement Performance Studies". Transportation Research Board. Retrieved 22 October 2017.
- "Ford, K., Arman, M., Labi, S., Sinha, K.C., Thompson, P.D., Shirole, A.M., and Li, Z. 2012. NCHRP Report 713 : Estimating life expectancies of highway assets. In Transportation Research Board, National Academy of Sciences, Washington, DC. Transportation Research Board, Washington DC" (PDF).
- "Piryonesi, S. M., & El-Diraby, T. (2018). Using Data Analytics for Cost-Effective Prediction of Road Conditions: Case of The Pavement Condition Index:[summary report] (No. FHWA-HRT-18-065). United States. Federal Highway Administration. Office of Research, Development, and Technology". Archived from the original on 2 February 2019.
- "NUAE Geosynthetics Ltd. News: Project Scout Moor Wind farm" (PDF). NUAE. May 2007. Archived from the original (PDF) on 8 December 2015. Retrieved 2 November 2008.
- Anon (June 1991). "Highway construction/ Ground insulation" (PDF). Styropor: Technical information. Archived from the original (PDF) on 2 October 2018. Retrieved 29 January 2010.
- Cheraghian, Goshtasp; Cannone Falchetto, Augusto; You, Zhanping; Chen, Siyu; Kim, Yun Su; Westerhoff, Jan; Moon, Ki Hoon; Wistuba, Michael P. (18 May 2020). "Warm mix asphalt technology: An up to date review". Journal of Cleaner Production: 122128. doi:10.1016/j.jclepro.2020.122128.
- "Warm Mix Asphalt Technologies and Research". Federal Highway Administration. 29 October 2008. Retrieved 4 August 2010.
- "Hot, Warm, Luke Warm and Cold Mix Asphalt" (PDF). Cornell Local Roads Program. June 2009. Archived from the original (PDF) on 21 October 2012. Retrieved 4 August 2010.
- Gerbrandt, Ron; Tim Makahoniuk; Cathy Lynn Borbely; Curtis Berthelot (2000). "Guidelines must be followed strictly – No exceptions" (PDF). Effect of Cold-in-place recycling on the Heavyweight Trucking Industry. 6th International Conference on Heavy Vehicle Weights and Dimension Proceedings. Retrieved 25 January 2009.
- David Jones; John Harvey; Imad L. Al-Qadi; Angel Mateos (2012). Advances in Pavement Design through Full-scale Accelerated Pavement Testing. CRC Press. ISBN 978-0-203-07301-8.
- "Concrete Pavement Restoration" (PDF). Archived from the original (PDF) on 17 April 2012. Retrieved 7 April 2012.
- "Concrete Pavement Rehabilitation Guide for Diamond Grinding". Retrieved 7 April 2012.
- "Bellefontaine, Ohio: Court Avenue photo". City Profile. 17 February 2011. Retrieved 2 April 2018.
- Lee, B. J.; Lee, H. (2004). "Position-Invariant Neural Network for Digital Pavement Crack Analysis". Computer-Aided Civil and Infrastructure Engineering. 19 (2): 105–118. doi:10.1111/j.1467-8667.2004.00341.x.
- Kulsea, Bill; Shawver, Tom; Kach, Carol (1980). Making Michigan Move: A History of Michigan Highways and the Michigan Department of Transportation. Lansing, Michigan: Michigan Department of Transportation. OCLC 8169232.
- Weingroff, Richard F. (7 April 2011). "The Lincoln Highway". fhwa.dot.gov. Federal Highway Administration. Retrieved 25 September 2017.
The LHA also sponsored short concrete "Seedling Mile" object lesson roads in many locations (the first, built in the fall of 1914, was just west of Malta, Illinois). The "Seedling Miles," according to the LHA's 1924 guide, were intended "to demonstrate the desirability of this permanent type of road construction" and "crystallize public sentiment" for "further construction of the same character." Generally, the LHA worked with the Portland Cement Association to arrange donations of cement for the seeding mileage...The most famous "seedling" and one of the most talked about portions of the Lincoln Highway was the 1.3-mile "Ideal Section" between Dyer and Schererville in Lake County, Indiana. In 1920, the LHA decided to develop a model section of road that would be adequate not only for current traffic but for highway transportation over the following 2 decades. The LHA assembled 17 of the country's foremost highway experts for meetings in December 1920 and February 1921 to decide design details of the Ideal Section. They agreed on such features as: A 110-foot right-of-way; A 40-foot wide concrete pavement 10 inches thick (maximum loads of 8,000 pounds per wheel were the basis for the pavement design); Minimum radius for curves of 1,000 feet, with guardrail at all embankments; Curves superelevated (i.e., banked) for a speed of 35 miles per hour; No grade crossings or advertising signs; and A footpath for pedestrians.
- Khazanovich, L.; Lederle, R.; Tompkins, D.; Harvey, J.T.; Signore, J. (2012). "Guidelines for the Rehabilitation of Concrete Pavements Using Asphalt Overlays (FHWA TPF-5(149) Final Report)". Cite journal requires
|journal=
(help) - Moghadas Nejad, Fereidoon; Noory, Alireza; Toolabi, Saeed; Fallah, Shahab (8 August 2014). "Effect of using geosynthetics on reflective crack prevention". International Journal of Pavement Engineering. 16 (6): 477–487. doi:10.1080/10298436.2014.943128.
- Lavin, Patrick (2003). Asphalt Pavements: A Practical Guide to Design, Production and Maintenance for Engineers and Architects. CRC Press. ISBN 9780203453292.
- Rubblizing with Bituminous Concrete Overlay – 10 Years' Experience in Illinois, Illinois Department of Transportation, April 2002,
- "Asphalt Paving Principles". www.clrp.cornell.edu. Cornell Local Roads Program. March 2004. Retrieved 5 October 2016.
- Budd, Godfrey. "An end to summer highway construction delays?". www.albertaconstructionmagazine.com. Retrieved 5 October 2016.
- Sprayed Seal, Local Government & Municipal Knowledge Base, accessed 29 January 2010
- Gransberg, Douglas D.; James, David M. B. (2005). Chip Seal Best Practices. National Cooperative Highway. Transportation Research Board. pp. 13–20. ISBN 978-0-309-09744-4.
- https://dpw.lacounty.gov/gmed/lacroads/TreatmentMicrosurfacing.aspx
- Lazic, Zvjezdan; Ron Gerbrandt (2004). "Feasibility of Alternative salt storage structures in Saskatchewan Neilburg case study" (PDF). Measuring performance indicators for decision-making in winter maintenance operations. 2004 Annual conference of the Transportation Association of Canada. Saskatchewan Highways and Transportation. Archived from the original (PDF) on 18 March 2009. Retrieved 25 February 2009.
- "Highways and Infrastructure — Government of Saskatchewan". Archived from the original on 8 February 2008. Retrieved 15 April 2008.
- Manins, Rosie (28 February 2009). "New dust suppression method". Otago Daily Times. Retrieved 5 November 2011.
- Anon (July 1998). "Bronze Age metalled road near Oxford". British Archaeology: News (36). Retrieved 29 January 2010.
- Anon. "Road metal". Merriam-Webster online dictionary. Merriam Webster inc. Retrieved 29 January 2010.
- Anon. "Metal". Online etymological dictionary. 2001 Douglas Harper. Retrieved 29 January 2010.
- Anon. "Metalled Road". World Web Online. WordWeb Software. Retrieved 29 January 2010.
- "Surfacing Aggregate" (PDF). Product brochure. Afrisam.com South Africa. 2008. Archived from the original (PDF) on 18 March 2009. Retrieved 25 January 2009.
- Oeser, Markus; Sabine Werkmeister; Alvaro Gonzales; David Alabaster (2008). "Experimental and numerical simulation of loading impact on modified granular pavements" (PDF). 8th World Congress on Computational Mechanics 5th European Congrss on computational methods in applied sciences and engineering ECCOMAS. 6th International Conference on Heavy Vehicle Weights and Dimension Proceedings. Archived from the original (PDF) on 18 March 2009. Retrieved 25 January 2009.
- Mary C. Rukashaza-Mukome; et al. (2003). "Cost Comparison of Treatments Used to Maintain or Upgrade Aggregate Roads" (PDF). Proceedings of the 2003 Mid-Continent Transportation Research Symposium. Iowa State University. Retrieved 16 September 2011.
- "Roads to Ruin: Towns Rip Up the Pavement". Wall Street Journal. 17 July 2010. Retrieved 16 September 2011.
- De balans opgemaakt: Duurzaam Veilig 1998–2007 [Sustainable Safety in the Netherlands - 1998–2007] (PDF) (in Dutch). SWOV, Dutch Institute for Road Safety Research. 2009. p. 6 (English abstract). ISBN 978-90-73946-06-4. Retrieved 13 July 2014.
- Hembrow, David (25 April 2011). "Road noise, cobbles and smooth asphalt". A view from the cycle path. Retrieved 14 August 2014.
- Fred Young (23 February 2013). What can Seattle learn from Dutch street design? (presentation video). Seattle Neighborhood Greenways. Event occurs at 3:49 and 9:19 min. Retrieved 14 August 2014.
... the cycle track is asphalt (...) and the lane for cars is brick ...
- "Endurablend Systems for Color Surfacing - Colors, Seals, Textures and Protects to Extend Service Life of Asphalt and Concrete Pavement Surfaces" (PDF). Retrieved 13 November 2014.
- High-Performance Crosswalks (PDF). Alternative Paving Concepts. Retrieved 13 November 2014.
- "Decorative Stamped Asphalt". ThermOTrack. Retrieved 13 November 2014.
- Hogan, C. Michael (September 1973). "Analysis of highway noise". Water, Air, and Soil Pollution. 2 (3): 387–392. Bibcode:1973WASP....2..387H. doi:10.1007/BF00159677.
- Statement Of Garth Dull For The Senate Epw Committee
- Cheraghian, Goshtasp; Wistuba, Michael P. (8 July 2020). "Ultraviolet aging study on bitumen modified by a composite of clay and fumed silica nanoparticles". Scientific Reports. 10 (1): 1–17. doi:10.1038/s41598-020-68007-0.
- "Land Clearing". MN Land Clearing. 11 January 2019. Retrieved 10 October 2019.
- Li, Qiang; Xiao, Danny X.; Wang, Kelvin C. P.; Hall, Kevin D.; Qiu, Yanjun (27 September 2013). "Mechanistic-empirical pavement design guide (MEPDG): a bird's-eye view". Journal of Modern Transportation. 19 (2): 114–133. doi:10.1007/bf03325749.
- "Scientists walk on tech pavement". BBC News. 12 September 2006. Retrieved 22 May 2010.
- "The Value of Smooth". Better Roads. Randall Reilly. August 2011.
External links
![]() |
Wikimedia Commons has media related to Pavements. |
- PaveShare - Concrete Paver Education
- "Pavements" website of the US Department of Transportation's Federal Highway Administration
- Long-life Surfacings for Roads. ITF Research Reports. 2017. doi:10.1787/9789282108116-en. ISBN 9789282108109.