Loom
A loom is a device used to weave cloth and tapestry. The basic purpose of any loom is to hold the warp threads under tension to facilitate the interweaving of the weft threads. The precise shape of the loom and its mechanics may vary, but the basic function is the same.
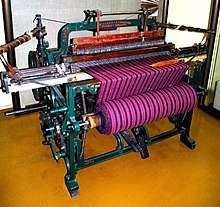
Etymology
The word "loom" is derived from the Old English geloma, formed from ge-(perfective prefix) and loma, a root of unknown origin; this meant a utensil, tool, or machine of any kind. In 1404 it was used to mean a machine to enable weaving thread into cloth.[1] By 1838, it had gained the meaning of a machine for interlacing thread.
Weaving
Weaving is done by intersecting the longitudinal threads, the warp, i.e. "that which is thrown across",[2] with the transverse threads, the weft, i.e. "that which is woven".
The major components of the loom are the warp beam, heddles, harnesses or shafts (as few as two, four is common, sixteen not unheard of), shuttle, reed and takeup roll. In the loom, yarn processing includes shedding, picking, battening and taking-up operations. These are the principal motions.
- Shedding. Shedding is the raising of part of the warp yarn to form a shed (the vertical space between the raised and unraised warp yarns), through which the filling yarn, carried by the shuttle, can be inserted, forming the weft. On the modern loom, simple and intricate shedding operations are performed automatically by the heddle or heald frame, also known as a harness. This is a rectangular frame to which a series of wires, called heddles or healds, are attached. The yarns are passed through the eye holes of the heddles, which hang vertically from the harnesses. The weave pattern determines which harness controls which warp yarns, and the number of harnesses used depends on the complexity of the weave. Two common methods of controlling the heddles are dobbies and a Jacquard Head.
- Picking. As the harnesses raise the heddles or healds, which raise the warp yarns, the shed is created. The filling yarn is inserted through the shed by a small carrier device called a shuttle. The shuttle is normally pointed at each end to allow passage through the shed. In a traditional shuttle loom, the filling yarn is wound onto a quill, which in turn is mounted in the shuttle. The filling yarn emerges through a hole in the shuttle as it moves across the loom. A single crossing of the shuttle from one side of the loom to the other is known as a pick. As the shuttle moves back and forth across the shed, it weaves an edge, or selvage, on each side of the fabric to prevent the fabric from raveling.
- Battening. Between the heddles and the takeup roll, the warp threads pass through another frame called the reed (which resembles a comb). The portion of the fabric that has already been formed but not yet rolled up on the takeup roll is called the fell. After the shuttle moves across the loom laying down the fill yarn, the weaver uses the reed to press (or batten) each filling yarn against the fell. Conventional shuttle looms can operate at speeds of about 150 to 160 picks per minute.[3]
There are two secondary motions, because with each weaving operation the newly constructed fabric must be wound on a cloth beam. This process is called taking up. At the same time, the warp yarns must be let off or released from the warp beams. To become fully automatic, a loom needs a tertiary motion, the filling stop motion. This will brake the loom if the weft thread breaks.[3] An automatic loom requires 0.125 hp to 0.5 hp to operate.
Types of looms
Back strap loom
The back strap loom is a simple loom that has its roots in ancient civilizations. The Andes Textiles, still made today with the back strap loom, originated thousands of years ago with the same back strap loom process. It consists of two sticks or bars between which the warps are stretched. One bar is attached to a fixed object and the other to the weaver, usually by means of a strap around the back. The weaver leans back and uses her body weight to tension the loom. On traditional looms, the two main sheds are operated by means of a shed roll over which one set of warps pass, and continuous string heddles which encase each of the warps in the other set. To open the shed controlled by the string heddles, the weaver relaxes tension on the warps and raises the heddles. The other shed is usually opened by simply drawing the shed roll toward the weaver.
Both simple and complex textiles can be woven on this loom. Width is limited to how far the weaver can reach from side to side to pass the shuttle. Warp faced textiles, often decorated with intricate pick-up patterns woven in complementary and supplementary warp techniques are woven by indigenous peoples today around the world. They produce such things as belts, ponchos, bags, hatbands and carrying cloths. Supplementary weft patterning and brocading is practiced in many regions. Balanced weaves are also possible on the backstrap loom. Today, commercially produced backstrap loom kits often include a rigid heddle.
Warp-weighted loom
The warp-weighted loom is a vertical loom that may have originated in the Neolithic period. The earliest evidence of warp-weighted looms comes from sites belonging to the Starčevo culture in modern Serbia and Hungary and from late Neolithic sites in Switzerland.[6] This loom was used in Ancient Greece, and spread north and west throughout Europe thereafter.[7] Its defining characteristic is hanging weights (loom weights) which keep bundles of the warp threads taut. Frequently, extra warp thread is wound around the weights. When a weaver has reached the bottom of the available warp, the completed section can be rolled around the top beam, and additional lengths of warp threads can be unwound from the weights to continue. This frees the weaver from vertical size constraint.
Drawloom
A drawloom is a hand-loom for weaving figured cloth. In a drawloom, a "figure harness" is used to control each warp thread separately.[8] A drawloom requires two operators, the weaver and an assistant called a "drawboy" to manage the figure harness. The earliest confirmed drawloom fabrics come from the State of Chu and date c. 400 BC.[9] Most scholars attribute the invention of the drawloom to the ancient Chinese, although some speculate an independent invention from ancient Syria since drawloom fabrics found in Dura-Europas are thought to date before 256 AD.[9][10] The draw loom for patterned weaving was invented in ancient China during the Han Dynasty.[11] Chinese weavers and artisans used foot-powered multi-harness looms and jacquard looms for silk weaving and embroidery; both of which were cottage industries with imperial workshops.[12] The Chinese-invented drawloom enhanced and sped up the production of silk and play a significant role in Chinese silk weaving. The loom was later introduced to Persia, India, and Europe.[11] https://cdn.britannica.com/37/60537-004-F2311987/Drawloom-Diderot-Encyclopedie.jpg
Handloom
Elements of a foot-treadle floor loom |
![]() |
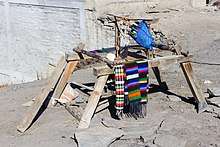
A handloom is a simple machine used for weaving. In a wooden vertical-shaft looms, the heddles are fixed in place in the shaft. The warp threads pass alternately through a heddle, and through a space between the heddles (the shed), so that raising the shaft raises half the threads (those passing through the heddles), and lowering the shaft lowers the same threads — the threads passing through the spaces between the heddles remain in place. This was a great invention in the 13th century.
Flying shuttle
Hand weavers could only weave a cloth as wide as their armspan. If cloth needed to be wider, two people would do the task (often this would be an adult with a child). John Kay (1704–1779) patented the flying shuttle in 1733. The weaver held a picking stick that was attached by cords to a device at both ends of the shed. With a flick of the wrist, one cord was pulled and the shuttle was propelled through the shed to the other end with considerable force, speed and efficiency. A flick in the opposite direction and the shuttle was propelled back. A single weaver had control of this motion but the flying shuttle could weave much wider fabric than an arm's length at much greater speeds than had been achieved with the hand thrown shuttle.
The flying shuttle was one of the key developments in weaving that helped fuel the Industrial Revolution. The whole picking motion no longer relied on manual skill and it was just a matter of time before it could be powered.
Haute-lisse and basse-lisse looms
Looms used for weaving traditional tapestry are classified as haute-lisse looms, where the warp is suspended vertically between two rolls. In basse-lisse looms, however, the warp extends horizontally between the two rolls.
Ribbon weaving
Traditional looms
Several other types of hand looms exist, including the simple frame loom, pit loom, free-standing loom, and the pegged loom. Each of these can be constructed, and provide work and income in developing economies.[13]
The earliest evidence of a horizontal loom is found on a pottery dish in ancient Egypt, dated to 4400 BC. It was a frame loom, equipped with foot pedals to lift the warp threads, leaving the weaver's hands free to pass and beat the weft thread.[14]
Power looms
Edmund Cartwright built and patented a power loom in 1785, and it was this that was adopted by the nascent cotton industry in England. The silk loom made by Jacques Vaucanson in 1745 operated on the same principles but was not developed further. The invention of the flying shuttle by John Kay was critical to the development of a commercially successful power loom.[15] Cartwright's loom was impractical but the ideas behind it were developed by numerous inventors in the Manchester area of England where, by 1818, there were 32 factories containing 5,732 looms.[16]
Horrocks loom was viable, but it was the Roberts Loom in 1830 that marked the turning point.[17] Incremental changes to the three motions continued to be made. The problems of sizing, stop-motions, consistent take-up, and a temple to maintain the width remained. In 1841, Kenworthy and Bullough produced the Lancashire Loom[18] which was self-acting or semi-automatic. This enables a youngster to run six looms at the same time. Thus, for simple calicos, the power loom became more economical to run than the hand loom – with complex patterning that used a dobby or Jacquard head, jobs were still put out to handloom weavers until the 1870s. Incremental changes were made such as the Dickinson Loom, culminating in the Keighley-born inventor Northrop, who was working for the Draper Corporation in Hopedale producing the fully automatic Northrop Loom. This loom recharged the shuttle when the pirn was empty. The Draper E and X models became the leading products from 1909. They were challenged by synthetic fibres such as rayon.[19] By 1942, faster, more efficient, and shuttleless Sulzer and rapier looms had been introduced.[20] Modern industrial looms can weave at 2,000 weft insertions per minute.[21]
Weft insertion
Different types of looms are most often defined by the way that the weft, or pick, is inserted into the warp. Many advances in weft insertion have been made in order to make manufactured cloth more cost effective. There are five main types of weft insertion and they are as follows:
- Shuttle: The first-ever powered looms were shuttle-type looms. Spools of weft are unravelled as the shuttle travels across the shed. This is very similar to projectile methods of weaving, except that the weft spool is stored on the shuttle. These looms are considered obsolete in modern industrial fabric manufacturing because they can only reach a maximum of 300 picks per minute.
- Air jet: An air-jet loom uses short quick bursts of compressed air to propel the weft through the shed in order to complete the weave. Air jets are the fastest traditional method of weaving in modern manufacturing and they are able to achieve up to 1,500 picks per minute. However, the amounts of compressed air required to run these looms, as well as the complexity in the way the air jets are positioned, make them more costly than other looms.
- Water jet: Water-jet looms use the same principle as air-jet looms, but they take advantage of pressurized water to propel the weft. The advantage of this type of weaving is that water power is cheaper where water is directly available on site. Picks per minute can reach as high as 1,000.
- Rapier loom: This type of weaving is very versatile, in that rapier looms can weave using a large variety of threads. There are several types of rapiers, but they all use a hook system attached to a rod or metal band to pass the pick across the shed. These machines regularly reach 700 picks per minute in normal production.
- Projectile: Projectile looms utilize an object that is propelled across the shed, usually by spring power, and is guided across the width of the cloth by a series of reeds. The projectile is then removed from the weft fibre and it is returned to the opposite side of the machine so it can get reused. Multiple projectiles are in use in order to increase the pick speed. Maximum speeds on these machines can be as high as 1,050 ppm.
Shedding
Dobby looms
A dobby loom is a type of floor loom that controls the whole warp threads using a dobby head. Dobby is a corruption of "draw boy" which refers to the weaver's helpers who used to control the warp thread by pulling on draw threads. A dobby loom is an alternative to a treadle loom, where multiple heddles (shafts) were controlled by foot treadles – one for each heddle.
Jacquard looms
The Jacquard loom is a mechanical loom, invented by Joseph Marie Jacquard in 1801, which simplifies the process of manufacturing textiles with complex patterns such as brocade, damask and matelasse.[22][23] The loom is controlled by punched cards with punched holes, each row of which corresponds to one row of the design. Multiple rows of holes are punched on each card and the many cards that compose the design of the textile are strung together in order. It is based on earlier inventions by the Frenchmen Basile Bouchon (1725), Jean Baptiste Falcon (1728) and Jacques Vaucanson (1740).[24] To call it a loom is a misnomer, a Jacquard head could be attached to a power loom or a hand loom, the head controlling which warp thread was raised during shedding. Multiple shuttles could be used to control the colour of the weft during picking. The Jacquard loom is the predecessor to the computer punched card readers of the 19th and 20th centuries.[25]
- Battening on a jacquard loom in Łódź.
- A female worker changing jacquard cards in a lace machine in a Nottingham factory (1918 (First World War).
- Boy next to two weaving looms with the weaving pattern on reams of paper (India).
- Following the pattern, holes are punched in the appropriate places on a jacquard card.
- Manual loom with double width and jacquard loom, Colegio del Arte Mayor de la Seda of Valencia.
- The Jacquard cards control the healds on a loom.
Circular looms
A circular loom is used to create a seamless tube of fabric for products such as hosiery, sacks, clothing, fabric hose (such as fire hose) and the like. Circular looms can be small jigs used for circular knitting[26] or large high-speed machines for modern garments.[27] Modern circular looms use up to ten shuttles driven from below in a circular motion by electromagnets for the weft yarns, and cams to control the warp threads. The warps rise and fall with each shuttle passage, unlike the common practice of lifting all of them at once.
Symbolism and cultural significance
The loom is a symbol of cosmic creation and the structure upon which individual destiny is woven. This symbolism is encapsulated in the classical myth of Arachne who was changed into a spider by the goddess Athena, who was jealous of her skill at the godlike craft of weaving.[28] In Maya civilization the goddess Ixchel taught the first woman how to weave at the beginning of time.[29]
Gallery
- Model of Navajo Loom, late 19th century, Brooklyn Museum.jpg
- An early nineteenth century Japanese loom with several heddles, which the weaver controls with her foot
- A Jakaltek Maya brocades a hair sash on a back strap loom.
- Hand loom at Hjerl Hede, Denmark, showing grayish warp threads (back) and cloth woven with red filling yarn (front)
- Oaxacan artisan Alberto Sanchez Martinez at loom
- Hand loom at the Korkosz Croft in Czarna Góra, Poland, 19th century
See also
- Bunkar: The Last of the Varanasi Weavers (documentary film)
- Fashion and Textile Museum
- Textile manufacturing
- Timeline of clothing and textiles technology
- Weaving (mythology)
References
- "loom - Origin and meaning of loom by Online Etymology Dictionary". www.etymonline.com.
- "warp - Search Online Etymology Dictionary". www.etymonline.com.
- Collier 1970, p. 104.
- Lush, Emily. "Making of: T'nalak Weaving, Philippines". The Textile Atlas. Retrieved 3 April 2019.
- "Abaca". White Champa. Retrieved 3 April 2019.
- Barber 1991, pp. 93–96.
- Crowfoot 1937, p. 36.
- Burnham 1980, p. 48.
- Broudy 1979, p. 124.
- Forbes 1987, pp. 218, 220.
- Ceccarelli, Marco; López-Cajún, Carlos (2012). Explorations in the History of Machines and Mechanisms: Proceedings of HMM2012 (History of Mechanism and Machine Science). Springer. pp. 219–220. ISBN 978-9400799448.
- Usher, Abbott Payson (2011). A History of Mechanical Inventions. Dover Publications. p. 54. ISBN 978-0486255934.
- Koster, Joan (1978). Handloom Construction: A Practical Guide for the Non-Expert. Volunteers in Technical Assistance, Inc. Archived from the original on 2 March 2014.
- Bruno, Leonard C.; Olendorf, Donna (1997). Science and technology firsts. Gale Research. p. 2. ISBN 9780787602567.
4400 B.C. Earliest evidence of the use of a horizontal loom is its depiction on a pottery dish found in Egypt and dated to this time. These first true frame looms are equipped with foot pedals to lift the warp threads, leaving the weaver's hands free to pass and beat the weft thread.
- Marsden 1895, p. 57.
- Guest 1823, p. 46.
- Marsden 1895, p. 76.
- Marsden 1895, p. 94.
- Mass 1990.
- Collier 1970, p. 111.
- Rajagopalan, S. "Advances in Weaving Technology and Looms". S.S.M. College of Engineering, Komarapalayam. Archived from the original on 29 November 2010 – via Pdexcil.org.
- Hobsbawm, Eric (2008) [1962]. The Age of Revolution. London. p. 45.
- "Fabric Glossary". Christina Lynn. Archived from the original on 5 January 2009. Retrieved 21 November 2008.
- Razy 1913, p. 120.
- Geselowitz, Michael N. (18 July 2016). "The Jacquard Loom: A Driver of the Industrial Revolution". The Institute: The IEEE news source. IEEE. Archived from the original on 1 April 2018. Retrieved 31 March 2018.
- Jocelyn C. (22 December 2008). How to: Cast on/Knit using a Circular Loom. Retrieved 27 June 2016 – via YouTube.
- "Circular Looms". Starlinger. Retrieved 27 June 2016.
- Tresidder, Jack (1997). The Hutchinson Dictionary of Symbols. London: Helicon Publishers. p. 127. ISBN 1-85986-059-1.
- Rosenbaum, Brenda P. (1990). "Mayan Women, Weaving and Ethnic Identity: a Historical Essay". Guatemala: Museo Ixchel del Traje Indigena: 157–169.
Bibliography
- Barber, E. J. W. (1991). Prehistoric Textiles. Princeton University Press. ISBN 0-691-00224-X.CS1 maint: ref=harv (link)
- Broudy, Eric (1979). The Book of Looms: A History of the Handloom from Ancient Times to the Present. Hanover and London: University Press of New England. ISBN 9780874516494.CS1 maint: ref=harv (link)
- Burnham, Dorothy K. (1980). Warp and Weft: A Textile Terminology. Royal Ontario Museum. ISBN 0-88854-256-9.CS1 maint: ref=harv (link)
- Collier, Ann M. (1970). A Handbook of Textiles. Pergamon Press. ISBN 0-08-018057-4.CS1 maint: ref=harv (link)
- Crowfoot, Grace (November 1937). "Of the Warp-Weighted Loom". The Annual of the British School at Athens. 37: 36–47. doi:10.1017/s0068245400017950.CS1 maint: ref=harv (link)
- Forbes, R. J. (1987). Studies in Ancient Technology, Volume 4. Leiden / New York: E. J. Brill. ISBN 9004083073.CS1 maint: ref=harv (link)
- Guest, Richard (1823). The Compendious History of Cotton-Manufacture. Retrieved 15 February 2009.CS1 maint: ref=harv (link)
- Marsden, Richard (1895). Cotton Weaving: Its Development, Principles, and Practice. George Bell & Sons. Archived from the original on 2018-06-29. Retrieved 2009-04-19.CS1 maint: ref=harv (link)
- Mass, William (1990). "The Decline of a Technology Leader:Capability, strategy and shuttleless Weaving" (PDF). Business and Economic History. ISSN 0894-6825.CS1 maint: ref=harv (link)
- Razy, C. (1913). Étude analytique des petits modèles de métiers exposés au musée des tissus (in French). Lyon, France: Musée historique des tissus.CS1 maint: ref=harv (link)
- Ventura, Carol (2003). Maya Hair Sashes Backstrap Woven in Jacaltenango, Guatemala, Cintas Mayas tejidas con el telar de cintura en Jacaltenango, Guatemala. Carol Ventura. ISBN 0-9721253-1-0.CS1 maint: ref=harv (link)
External links
![]() |
Look up loom in Wiktionary, the free dictionary. |
![]() |
Wikimedia Commons has media related to Looms. |
- Loom demonstration video
- "Caring for your loom" article
- "The Art and History of Weaving"
- The Medieval Technology Pages: "The Horizontal Loom"