Construction 3D printing
Construction 3D Printing (c3Dp) or 3D construction Printing (3DCP) refers to various technologies that use 3D printing as a core method to fabricate buildings or construction components. Alternative terms are also in use, such as additive construction,[1][2] Autonomous Robotic Construction System (ARCS),[3] Large scale Additive Manufacturing (LSAM), or Freeform construction (FC), also to refer to sub-groups, such as '3D Concrete', used to refer to concrete extrusion technologies.
There are a variety of 3D printing methods used at construction scale, with the main ones being extrusion (concrete/cement, wax, foam, polymers), powder bonding (polymer bond, reactive bond, sintering), and additive welding. 3D printing at a construction scale will have a wide variety of applications within the private, commercial, industrial and public sectors. Potential advantages of these technologies include faster construction, lower labor costs, increased complexity and/or accuracy, greater integration of function, and less waste produced.
A number of different approaches have been demonstrated to date, which include on-site and off-site fabrication of buildings and construction components, using industrial robots, gantry systems and tethered autonomous vehicles. Demonstrations of construction 3D printing technologies to date have included fabrication of housing, construction components (cladding and structural panels and columns), bridges and civil infrastructure,[4][5] artificial reefs, follies, and sculptures.
The technology has seen a significant increase in popularity in recent years with many new companies, including some backed by prominent names from the construction industry and academia. This led to several important milestones, such as the first 3D printed building, the first 3D printed bridge, the first 3D printed part in a public building, the first living 3D printed building in Europe and CIS, and the first 3D printed building in Europe fully approved by the authorities (COBOD International), among many others.
History
Seeding technologies 1950–1995
Robotic bricklaying was conceptualized and explored in the 1950s and related technology development around automated construction began in the 1960s, with pumped concrete and isocyanate foams.[6] Development of automated fabrication of entire buildings using slip forming techniques and robotic assembly of components, akin to 3D printing, were pioneered in Japan to address the dangers of building high rise buildings by Shimizu and Hitachi in the 1980s and 1990s.[7] Many of these early approaches to on-site automation foundered because of the construction 'bubble', their inability to respond to novel architectures and the problems of feeding and preparing materials to the site in built up areas.
Early developments 1995–2000
Early construction 3D printing development and research have been under way since 1995. Two methods were invented, one by Joseph Pegna[8] which was focused on a sand/cement forming technique which utilized steam to selectively bond the material in layers or solid parts, though this technique was never demonstrated.
The second technique, Contour Crafting by Behrohk Khoshnevis, initially began as a novel ceramic extrusion and shaping method, as an alternative to the emerging polymer and metal 3D printing techniques, and was patented in 1995.[9] Khoshnevis realized that this technique could exceed these techniques where "current methods are limited to fabrication of part dimensions that are generally less than one meter in each dimension". Around 2000, Khoshnevis's team at USC Vertibi began to focus on construction scale 3D printing of cementitious and ceramic pastes, encompassing and exploring automated integration of modular reinforcement, built-in plumbing and electrical services, within one continuous build process. This technology has only been tested at lab scale to date and controversially and allegedly formed the basis for recent efforts in China.
First generation 2000–2010
In 2003, Rupert Soar secured funding and formed the freeform construction group at Loughborough University, UK, to explore the potential for up-scaling existing 3D printing techniques for construction applications. Early work identified the challenge of reaching any realistic break-even for the technology at the scale of construction and highlighted that there could be ways into the application by massively increasing the value proposition of integrated design (many functions, one component). In 2005, the group secured funding to build a large-scale construction 3D printing machine using 'off the shelf' components (concrete pumping, spray concrete, gantry system) to explore how complex such components could be and realistically meet the demands for construction.
In 2005 Enrico Dini, Italy, patented the D-Shape technology, employing a massively scaled powder jetting/bonding technique over an area approximately 6m x 6m x 3m.[10] This technique although originally developed with epoxy resin bonding system was later adapted to use inorganic bonding agents.[11] This technology has been used commercially for a range of projects in construction and other sectors including for [artificial reefs].[12]
One of the most recent developments has been the printing of a bridge, the first of this kind in the world, in collaboration with IaaC and Acciona.
In 2008 3D Concrete Printing began at Loughborough University, UK, headed by Richard Buswell and colleagues to extend the groups prior research and look to commercial applications moving from a gantry based technology[13] to an industrial robot, which they succeeded in licensing the technology to Skanska in 2014.
Second generation 2010–present
On January 18, 2015 the company gained further press coverage with the unveiling of 2 further buildings, a mansion style villa and a 5 storey tower, using 3D printed components.[14] Detailed photographic inspection indicates that the buildings were fabricated with both precast and 3D printed components. The buildings stand as the first complete structures of their kind fabricated using construction 3D printing technologies. In May 2016 a new 'office building' was opened in Dubai.[15] The 250-square-metre space (2,700 square foot) is what Dubai's Museum of the Future project is calling the world's first 3D-printed office building. In 2017 an ambitious project to build a 3D printed skyscraper in the United Arab Emirates was announced.[16] Cazza construction would help to build the structure. At present there are no specific details, such as the buildings height or exact location.[17]
FreeFAB Wax™,[18] invented by James B Gardiner and Steven Janssen at Laing O'Rourke (construction company). The patented technology has been in development since March 2013.[19] The technique uses construction scale 3D printing to print high volumes of engineered wax (up to 400L/hr) to fabricate a 'fast and dirty' 3D printed mould for precast concrete, glass fibre reinforced concrete (GRC) and other sprayable/cast-able materials. The mould casting surface is then 5 axis milled removing approximately 5mm of wax to create a high quality mould (approximately 20 micron surface roughness).[20] After the component has cured, the mould is then either crushed or melted-off and the wax filtered and re-used, significantly reducing waste compared to conventional mould technologies. The benefits of the technology are fast mould fabrication speeds, increased production efficiencies, reduced labour and virtual elimination of waste by re-use of materials for bespoke moulds compared to conventional mould technologies.[21]
The system was originally demonstrated in 2014 using an industrial robot.[22] The system was later adapted to integrate with a 5 axis high speed gantry to achieve the high speed and surface milling tolerances required for the system. The first industrialized system is installed at a Laing O'Rourke factory in the United Kingdom and is due to start industrial production for a prominent London project in late 2016.
The US Army Corps of Engineers, Engineer Research Development Center, led by the Construction Engineering Research Laboratory (ERDC-CERL) in Champaign, IL USA, began research in deployable construction 3D printer technology starting in September 2015. Success in this work has led to the development of an additive construction program at ERDC-CERL. The pilot project, Automated Construction for Expeditionary Structures (ACES), focused on concrete 3D printing and covered a broad range of research areas. Topics included printing systems, printable concrete materials, structural design and testing, and construction methods. The ACES project resulted in 3 demonstrations: An Entry Control Point,[23] the first Reinforced Additively Constructed Concrete Barracks,[24] and the printing of civil and military infrastructure (Jersey barriers, T-walls, culverts, bunkers, and fighting position) at the US Army Manuver Support, Sustainment, and protection Experiments (MSSPIX).[25] In 2017 ERDC CERL began working with the US Marine Corps, resulting in the first demonstration of concrete 3D printing by military personnel, a structurally enhanced reinforced 3D printed concrete Barracks Hut,[26][27] the first 3D printed bridge in the Americas,[28] and the first demonstration of printing with a 3 inch nozzle.[29] Through this work ERDC and the Marines were able to test structural performance of reinforced 3D printed concrete wall assemblies and bridge beams, print system resilience and maintenance cycles, extended printing operations, the publicized 24 hour building claim,[30] and develop viable reinforcement and construction methods using conventionally accepted practices.[2] ERDC's work has excelled the readiness and ruggedness of deployable 3D printing technology in terms of personnel training and unassisted operation, printer transport and mobility, extended system use, all weather printing, uneven surface printing, locally available materials, and construction practices.
MX3D Metal founded by Loris Jaarman and team has developed two 6 axis robotic 3D printing systems, the first uses a thermoplastic which is extruded, notably this system allows the fabrication of freeform non-planar beads. The second is a system that relies on additive welding (essentially spot welding on previous spot welds) the additive welding technology has been developed by various groups in the past, however the MX3D metal system is the most accomplished to date. MX3D are currently working toward the fabrication and installation of a metal bridge in Amsterdam.[31]
BetAbram is a simple gantry based concrete extrusion 3D printer developed in Slovenia. This system is available commercially, offering 3 models (P3, P2 and P1) to consumers since 2013. The largest P1 can print objects up to 16m x 9m x 2.5m.[32] Total Custom concrete 3D printer developed by Rudenko[33] is a concrete deposition technology mounted in a gantry configuration, the system has a similar output to Winsun and other concrete 3D printing technologies, however it uses a lightweight truss type gantry. The technology has been used to fabricate a backyard scale version of a castle[34] and a hotel room in the Philippines[35]
The world's first serial production of construction printers was launched by SPECAVIA company, based in Yaroslavl (Russia). In May 2015, the company introduced the first model of a construction 3d printer and announced the start of sales. As of the beginning of 2018 the group of companies "AMT-SPEСAVIA" produces 7 models of portal construction printers: from small format (for printing small architectural forms) to large scale (for printing buildings up to 3 floors) printers. Today, the construction 3D printers of Russian production under the "AMT" trademark are operating in several countries, including, in August 2017 the first construction printer was delivered to Europe - for 3DPrinthuset (Denmark). This printer was used Copenhagen for the construction of the first 3D printed building in the EU (office-hotel of 50 m2).
XtreeE has developed a multi-component printing system, mounted on top of a 6-axis robotic arm. The project has started in July 2015, and boasts collaboration and investments from strong names in the construction industry, such as Saint Gobain, Vinci,[36] and LafargeHolcim.[37] 3DPrinthuset, a successful Danish 3DPrinting startup, has also branched into construction with its sister company COBOD International, which made its own gantry-based printer in October 2017. With the collaboration of strong names in the scandinavian region, such as NCC and Force Technology, the company's spin-off has quickly gained traction by constructing the first 3DPrinted house in Europe. The Building on Demand (BOD) project, as the structure is called, is a small office hotel in Copenhagen, Nordhavn area, with walls and part of the foundation fully printed, while the rest of the construction is made in traditional construction. As of November 2017, the building is in the final phase of applying fixtures and roofing, while all the 3DPrinted parts have been fully completed.[38]
SQ4D was recognized as the best 3D homebuilder of 2019 with its first of its kind unlimited footprint design S-Squared ARCS VVS NEPTUNE with its Gantry system 9.1 x 4.4 x ∞ from the United States.[39] S-Squared 3D Printers Inc is a 3D printer manufacturing and retail company based in Long Island, New York. The company was founded in 2014 and makes 3D printers for hobbyists, libraries and STEM programs. In 2017, the company launched a new division, S-Squared 4D Commercial, to construct homes and commercial buildings with their 3D printing rig called Autonomous Robotic Construction System (ARCS).[40] This bootstrapped company is co-founded by Robert Smith and Mario Szczepanski and has 13 employees.[41][42]
Autonomous Robotic Construction System (ARCS) is a 20-feet by 40-feet eco-friendly concrete printer that can build a 1,490-square-foot home in 36 hours.[43][44] The system can build homes, commercial buildings, roads and bridges.[45] ARCS can complete projects from 500 square feet to more than one million square feet.[46][47]
Design
Architect James Bruce Gardiner[48] pioneered architectural design for Construction 3D Printing with two projects. The first Freefab Tower 2004 and the second Villa Roccia 2009–2010. FreeFAB Tower[49] was based on the original concept to combine a hybrid form of construction 3D printing with modular construction. This was the first architectural design for a building focused on the use of Construction 3D Printing. Influences can be seen in various designs used by Winsun, including articles on the Winsun's original press release[50] and office of the future.[51] The FreeFAB Tower project also depicts the first speculative use of multi-axis robotic arms in construction 3D printing, the use of such machines within construction has grown steadily in recent years with projects by MX3D[52] and Branch Technology.[53]
The Villa Roccia 2009–2010[54] took this pioneering work a step further with the a design for a Villa at Porto Rotondo, Sardinia, Italy in collaboration with D-Shape. The design for the Villa focused on the development of a site specific architectural language influenced by the rock formations on the site and along the coast of Sardinia, while also taking into account the use of a panellised prefabricated 3D printing process. The project went through prototyping and didn't proceed to full construction.
Francios Roche (R&Sie) developed the exhibition project and monograph 'I heard about' in 2005[55] which explored the use of a highly speculative self propelling snake like autonomous 3D printing apparatus and generative design system to create high rise residential towers. The project although impossible to put into practice with current or contemporary technology demonstrated a deep exploration of the future of design and construction. The exhibition showcased large scale CNC milling of foam and rendering to create the freeform building envelopes envisaged.
Dutch architect Janjaap Ruijssenaars's performative architecture 3D-printed building was planned to be built by a partnership of Dutch companies.[56] [57] The house was planned to be built in the end of 2014, but this deadline wasn't met. The companies have said that they are still committed to the project.[58]
The Building On Demand, or BOD, a small office hotel 3D printed by 3D Printhuset (now COBOD International) and designed by architect Ana Goidea, has incorporated curved walls and a rippling effects on their surface, to showcase the design freedom that 3D printing allows in the horizontal plane.
Structures
3D printed buildings
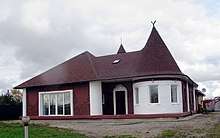
The 3D Print Canal House was the first full-scale construction project of its kind to get off the ground. In just a short space of time, the Kamermaker has been further developed to increase its production speed by 300%. However, progress has not been swift enough to claim the title of 'World's First 3D Printed House'.[59]
The first residential building in Europe and the CIS, constructed using the 3D printing construction technology, was the home in Yaroslavl (Russia) with the area of 298,5 sq. meters. The walls of the building were printed by the company SPECAVIA in December 2015. 600 elements of the walls were printed in the shop and assembled at the construction site. After completing the roof structure and interior decoration, the company presented a fully finished 3D building in October 2017.[60]
The peculiarity of this project is that for the first time in the world the entire technological cycle of construction has been passed:
- design,
- obtaining a building permit,
- registration of the building,
- connection of all engineering systems.
An important feature of the 3D house in Yaroslavl, that also distinguishes this project from other implemented ones - this is not a presentation structure, but rather a full-fledged residential building. Today it is home of a real, ordinary, family.
Dutch and Chinese demonstration projects are slowly constructing 3D-printed buildings in China,[61] Dubai[62] and the Netherlands.[63] Using the effort to educate the public to the possibilities of the new plant-based building technology and to spur greater innovation in 3D printing of residential buildings.[64][65] A small concrete house was 3D-printed in 2017.[66]
The Building on Demand (BOD), the first 3D printed house in Europe, is a project led by COBOD International (formerly known as 3DPrinthuset, now its sister company) for a small 3D printed office hotel in Copenhagen, Nordhavn area. The building is also the first 3D printed permanent building, with all permits in place and fully approved by the authorities.[67] As of 2018, the building stands fully completed and furbished.[68]
3D printed bridges
In Spain, the first pedestrian bridge printed in 3D in the world (3DBRIDGE) was inaugurated 14 December 2016 in the urban park of Castilla-La Mancha in Alcobendas, Madrid.[69] The 3DBUILD technology used was developed by ACCIONA, who was in charge of the structural design, material development and manufacturing of 3D printed elements.[70] The bridge has a total length of 12 meters and a width of 1.75 meters and is printed in micro-reinforced concrete. Architectural design was done by Institute of Advanced Architecture of Catalonia (IAAC).
The 3D printer used to build the footbridge was manufactured by D-Shape. The 3D printed bridge reflects the complexities of nature’s forms and was developed through parametric design and computational design, which allows to optimize the distribution of materials and allows to maximize the structural performance, being able to dispose the material only where it is needed, with total freedom of forms. The 3D printed footbridge of Alcobendas represented a milestone for the construction sector at international level, as large scale 3D printing technology has been applied in this project for the first time in the field of civil engineering in a public space.
3D printed architectural forms
In August 2018 in Palekh (old town in Russia) was the world's first application of additive technology for сreating the fountain.[71]
The fountain "Snop" (Sheaf) was originally created in the middle of the 20th century by famous sculptor Nikolai Dydykin. Nowadays, during the restoration of the fountain, it was changed from a rectangular to a round shape. The backlight system has also been updated. The renovated fountain now is 26 meters in diameter and 2.2 meters deep. The parapet of the 3D fountain with internal communication channels was printed by the AMT construction printer produced by AMT-SPETSAVIA group.
Extraterrestrial printed structures
The printing of buildings has been proposed as a particularly useful technology for constructing off-Earth habitats, such as habitats on the Moon or Mars. As of 2013, the European Space Agency was working with London-based Foster + Partners to examine the potential of printing lunar bases using regular 3D printing technology.[72] The architectural firm proposed a building-construction 3D-printer technology in January 2013 that would use lunar regolith raw materials to produce lunar building structures while using enclosed inflatable habitats for housing the human occupants inside the hardshell printed lunar structures. Overall, these habitats would require only ten percent of the structure mass to be transported from Earth, while using local lunar materials for the other 90 percent of the structure mass.[73] The dome-shaped structures would be a weight-bearing catenary form, with structural support provided by a closed-cell structure, reminiscent of bird bones.[74] In this conception, "printed" lunar soil will provide both "radiation and temperature insulation" for the Lunar occupants.[73] The building technology mixes lunar material with magnesium oxide which will turn the "moonstuff into a pulp that can be sprayed to form the block" when a binding salt is applied that "converts [this] material into a stone-like solid."[73] A type of sulfur concrete is also envisioned.[74]
Tests of 3D printing of an architectural structure with simulated lunar material have been completed, using a large vacuum chamber in a terrestrial lab.[75] The technique involves injecting the binding liquid under the surface of the regolith with a 3D printer nozzle, which in tests trapped 2 millimetres (0.079 in)-scale droplets under the surface via capillary forces.[74] The printer used was the D-Shape.
A variety of lunar infrastructure elements have been conceived for 3D structural printing, including landing pads, blast protection walls, roads, hangars and fuel storage.[74] In early 2014, NASA funded a small study at the University of Southern California to further develop the Contour Crafting 3D printing technique. Potential applications of this technology include constructing lunar structures of a material that could consist of up to 90-percent lunar material with only ten percent of the material requiring transport from Earth.[76]
NASA is also looking at a different technique that would involve the sintering of lunar dust using low-power (1500 watt) microwave energy. The lunar material would be bound by heating to 1,200 to 1,500 °C (2,190 to 2,730 °F), somewhat below the melting point, in order to fuse the nanoparticle dust into a solid block that is ceramic-like, and would not require the transport of a binder material from Earth as required by the Foster+Partners, Contour Crafting, and D-shape approaches to extraterrestrial building printing. One specific proposed plan for building a lunar base using this technique would be called SinterHab, and would utilize the JPL six-legged ATHLETE robot to autonomously or telerobotically build lunar structures.[77]
Concrete printing
Large-scale, cement-based 3D printing disposes the need for conventional molding by precisely placing, or solidifying, specific volumes of material in sequential layers by a computer controlled positioning process.[78] This 3D printing approach consist of three general stages: data preparation, concrete preparation and component printing.[79]
For path and data generation, a variety of methods are implemented for the generation of robotic building paths. A general approach is to slice a 3D shape into flat thin layers with a constant thickness which can be stacked up onto each other. In this method, each layer consists of a contour line and a filling pattern which can be implemented as honeycomb structures or space-filling curves. Another method is the tangential continuity method which produces 3-dimensional building paths with locally varying thicknesses. This method results in creating constant contact surfaces between two layers, therefore, the geometrical gaps between two layers which often limits the 3D printing process will be avoided.[80]
The material preparation stage includes mixing and placing the concrete into the container. Once the fresh concrete has been placed into the container, it can be conveyed through the pump–pipe– nozzle system to print out self-compacting concrete filaments, which can build layer-by-layer structural components.[81] In the additive processes, pumpability and the stability of the extrusion is important for the applications of mortars. These properties will all vary depending on the concrete mix design, the delivery system, and the deposition device. General specifications of wet concrete 3D printing are categorized into four main characteristics:[79]
- Pumpability: The ease and reliability with which material is moved through the delivery system
- Printability: The ease and reliability of depositing material through a deposition device
- Buildability: The resistance of a deposited wet material to deformation under load
- Open time: The period where the above properties are consistent within acceptable tolerances.
To execute the printing process, a control system is required. These systems can be generally split into two categories: gantry systems and robotic arm systems. The gantry system drives a manipulator mounted onto an overhead to locate the print nozzle in XYZ cartesian coordinates while robotic arms offer additional degrees of freedom to the nozzle, allowing more accurate printing workflows such as printing with tangential continuity method.[80] Regardless of the system used for printing (gantry crane or robotic arm), the coordination between the nozzle travel speed and the material flow rate is crucial to the outcome of the printed filament.[82] In some cases, multiple 3D printing robotic arms can be programmed to run simultaneously resulting in decreased construction time.[83] Finally, automated post-processing procedures can also be applied in scenarios which require the removal of support structures or any surface finishing.[79]
Construction speed
Claims have been made by Behrokh Khoshnevis since 2006 for 3D printing a house in a day,[84] with further claims to notionally complete the building in approximately 20 hours of "printer" time.[85] By January 2013, working versions of 3D-printing building technology were printing 2 metres (6 ft 7 in) of building material per hour, with a follow-on generation of printers proposed to be capable of 3.5 metres (11 ft) per hour, sufficient to complete a building in a week.[73]
The Chinese company WinSun has built several houses using large 3D printers using a mixture of quick drying cement and recycled raw materials. Ten demonstration houses were said by Winsun to have been built in 24 hours, each costing US $5000 (structure not including, footings, services, doors/windows and fitout).[86] However, construction 3D printing pioneer Dr. Behrokh Khoshnevis claims this was faked and that WinSun stole his intellectual property.[87]
Research and public knowledge
There are several research projects dealing with 3D Construction printing, such as the 3D concrete printing (3DCP) project at the Eindhoven University of Technology,[88] or the various projects at the Institute for Advanced Architecture of Catalonia (Pylos, Mataerial, and Minibuilders). The list of research projects is expanding even more in the last couple of years, thanks to a growing interest in the field.[89]
State-of-the-art research
The majority of the projects have been focused on researching the physical aspects behind the technology, such as the printing technology, material technology, and the various issues related to them. COBOD International (formerly known as 3DPrinthuset, now its sister company) has recently led a research oriented towards exploring the current state of the technology worldwide, by visiting more than 35 different 3D Construction printing related projects. For each project, a research report has been issued, and the gathered data has been used to unify all the various technologies into a first attempt at a common standardized categorization and terminology.
The researchers at Purdue University[90] have pioneered a 3D printing process known as Direct-ink-Writing[91] for fabrication of architectured cement-based materials for the first time.[92] They demonstrated using 3D-printing, bio-inspired designs of cement-based materials is feasible and novel performance characteristics such as flaw-tolerance and compliance can be achieved.
First 3D Construction printing conference
Along with the research, 3DPrinthuset (now known as COBOD International) has organized two international conferences on 3D Construction printing (February[93] and November[94] 2017 respectively), aimed at bringing together the strongest names in this emerging industry to discuss the potentials and challenges that lie ahead. The conferences were the first of this kind, and have brought together names such as D-Shape, Contour Crafting, Cybe Construction, Eindhoven's 3DCP research, Winsun, and many more. Along the 3D Construction printing specialists, there has also been a strong presence from the traditional construction industry key players for the first time, with names such as Sika AG, Vinci , Royal BAM Group, NCC, among others. A general idea emerged that the 3D Construction printing field needs a more unified platform where ideas, applications, issues and challenges can be shared and discussed.
Media interest
Although the first steps have been made nearly three decades ago, 3D construction printing has struggled to reach out for years. The first technologies to achieve some media attention were Contour Crafting and D-Shape, with a few sporadic articles in 2008–2012[95][96][97] and a 2012 TV report.[98] D-Shape has also been featured in an independent documentary dedicated to its creator Enrico Dini, called "The man who prints houses".[99]
One important break-through has been seen with the announcement of the first 3D printed building, using a prefabricated 3D printed components made by Winsun, which claimed to be able to print 10 houses in a day with its technology.[100] Although the claims were still to be confirmed, the story has created a wide traction and a growing interest in the field. In a matter of months, many new companies began to emerge. This led to many new endeavors that reached the media, such as, in 2017, the first pedestrian 3d printed bridge[101] and the first cyclist 3d printed bridge,[102] plus an early structural element made with 3d printing in 2016,[103] among many others.
Recently, COBOD International, formerly known as 3DPrinthuset (its sister company) has gained wide media attention with their first permanent 3D printed building, the first of its kind in Europe.[104][105][105][106] The project set an important precedent for being the first 3D printed building with a building permit and documentation in place, and a full approval from the city authorities, a crucial milestone for a wider acceptance in the construction field. The story gained extensive coverage, both on national and international media, appearing on TV in Denmark, Russia, Poland, Lithuania, among many others.
See also
References
- Labonnote, Nathalie; Rønnquist, Anders; Manum, Bendik; Rüther, Petra (December 2016). "Additive construction: State-of-the-art, challenges and opportunities". Automation in Construction. 72: 347–366. doi:10.1016/j.autcon.2016.08.026.
- Kreiger, Eric L.; Kreiger, Megan A.; Case, Michael P. (August 2019). "Development of the construction processes for reinforced additively constructed concrete". Additive Manufacturing. 28: 39–49. doi:10.1016/j.addma.2019.02.015.
- Sisson, Patrick (8 January 2019). "Can this startup 3D-print a home in 30 hours?". Curbed.
- "World's First 3D Printed Bridge Opens in Spain". ArchDaily. 7 February 2017.
- France-Presse, Agence (18 October 2017). "World's first 3D-printed bridge opens to cyclists in Netherlands". The Guardian.
- Papanek (1971). Design for the Real World. ISBN 978-0897331531.
- Architectural Design (2008). Versatility and Vicissitude. ISBN 9780470516874.
- J.B.Gardiner PhD Thesis - Exploring the Emerging Design Territory of Construction 3D Printing (p80), 2011
- Khoshnevis, Original Contour Crafting Patent US5529471 A
- Patent by Dini et. al, "Method and Device for Building Automatically Conglomerate Structures. Patent number US20080148683 A1" web cited 2016-07-18
- J.B.Gardiner PhD thesis "Exploring the Emerging Design Territory of Construction 3D Printing, 2011 (p89) web cited 2016-07-18
- J.B.Gardiner PhD thesis "Exploring the Emerging Design Territory of Construction 3D Printing, 2011" (p337) web cited 2016-07-18
- J.B.Gardiner PhD thesis "Exploring the Emerging Design Territory of Construction 3D Printing, 2011 (p81) web cited 2016-07-18
- "https://3dprint.com/38144/3d-printed-apartment-building/" web cited 2016-09-14
- "https://3dprint.com/126426/3d-printed-museum-office/" web cited 2016-09-14
- "Cazza to build world's first 3D printed skyscraper". Jochebed Menon, Construction Week Online, March 12, 2017. Retrieved July 17, 2017
- "Dubai and Cazza Construction Technologies Announce Plans to Build World's First 3D Printed Skyscrape". Claire Scott, 3D Print. March 13, 2017. Retrieved July 17, 2017
- "FreeFAB Website". Retrieved 21 February 2017.
- "https://link.springer.com/chapter/10.1007/978-3-319-04663-1_9" RobArch 2014 conference proceedings, Springer web cited September 14, 2016
- ""Freefab: Development of a construction-scale robotic formwork 3D printer", Vimeo 2014".
- "http://www.iaarc.org/publications/fulltext/ISARC2016-Paper095.pdf, ISARC 2016"
- Laing O'Rourke (9 October 2014). "Laing O'Rourke's FreeFAB Technology" – via YouTube.
- USACE ERDC, Entry Control Point (ECP), 2016, https://www.youtube.com/watch?v=BodasNDLYzU
- ERDC, First 3D printed Concrete Barracks, 2017, https://www.youtube.com/watch?v=-qmqN1G5x4w
- News Leader, Army shows off next-level tech at Fort Leonard Wood, 2018, https://amp.news-leader.com/amp/503766002
- Engineer News Record, Army Researchers Refine 3D-Printed Concrete Barracks, https://www.enr.com/articles/45002-army-researchers-refine-3d-printed-concrete-barracks
- Fox News, Marine Corps 3D print 500-square-foot concrete barrack, 2018, https://video.foxnews.com/v/5828338937001
- Marine Corps System Command, Tactical Tuesday: 3D Printed Concrete Bridge, 2019, https://www.youtube.com/watch?v=vEN1x5Hc4qA
- 3D printing Media Network, US Marines 3D print concrete structure using a three-inch nozzle, 2019, https://www.3dprintingmedia.network/us-marines-3d-print/
- Diggs-McGee et al, Print time vs. elapsed time: A temporal analysis of a continuous printing operation for additive constructed concrete, Additive Manufacturing, 2019
- "Construction of World's 1st 3D Printed Bridge Begins in Amsterdam".
- "https://3dprintingindustry.com/news/emerges-first-manufacturer-3d-house-printers-38801/" 3D Industry article
- "Total Custom Website". Retrieved 21 February 2017.
- "World's First 3D Printed Castle is Complete". 3DPrint.com. Retrieved 21 February 2017.
- "EXCLUSIVE: Lewis Grand Hotel Erects World's First 3D Printed Hotel". Retrieved 21 February 2017.
- "VINCI Construction signs a partnership agreement with XtreeE and acquires a stake in the company, a leader in 3D concrete printing". www.vinci-construction.com. Retrieved 2017-12-05.
- "LafargeHolcim innovates with 3D concrete printing". LafargeHolcim.com. 2016-08-05. Retrieved 2017-12-05.
- "The construction of Europe's first 3D printed building has begun. - 3D Printhuset". 3D Printhuset (in Danish). Retrieved 2017-12-05.
- https://www.aniwaa.com/house-3d-printer-construction/
- Ocasio, Victor (January 13, 2019). "LI firm testing huge 3D printer that could make a house in 48 hours". Newsday. Retrieved January 13, 2019.
- Sisson, Patrick (January 8, 2019). "Can this startup 3D-print a home in 30 hours?". Curbed. Vox Media. Retrieved January 8, 2019.
- Fuentes, Nicole (February 9, 2018). "3D printing concrete to build homes". The Long Island Advance. Retrieved February 9, 2018.
- Fuentes, Nicole (December 27, 2018). "S-Squared gets printing". The Long Island Advance. Retrieved December 27, 2018.
- Goldberg, Jodi (January 17, 2019). "Machine could build home in 2 days". Fox 5 NY. Fox 5. Retrieved January 17, 2019.
- Vialva, Tia. "S-SQUARED 3D PRINTERS DEBUTS LARGE AUTONOMOUS ROBOTIC CONSTRUCTION SYSTEM". 3D Printing Industry. Retrieved December 7, 2018.
- Cruz, Veronica (January 13, 2019). "S-Squared presents ARCS – the world's largest 3D printer". Market Business News. MBN. Retrieved January 13, 2019.
- S., Michelle. "S-Squared 3D printers creates 3D XXL printer for construction". 3D Natives. Retrieved January 8, 2019.
- "Linkedin Profile". Linkedin.
- Gardiner, James Bruce. "Exploring the Emerging Design Territory of Construction 3D Printing" (PDF). RMIT Research bank. Retrieved 21 February 2017. (pp. 176–202), 2011
- "How a Chinese Company 3D-Printed Ten Houses In a Single Day". Gizmodo. Retrieved 2017-02-21.
- "Office of the Future is 3D printed in Dubai". Treehugger. Retrieved 2017-02-21.
- Kira. "Construction of world's first 3D printed metal bridge begins today in Red Light District of Amsterdam". 3ders. Retrieved 21 February 2017.
- Clark, Corey. "Branch Technology unveils SHoP Architects' 3D printed pavilion at Design Miami". 3D Printing Industry. Retrieved 21 February 2017.
- Gardiner, James Bruce. "Exploring the Emerging Design Territory of Construction 3D Printing" (PDF). RMIT Research bank. Retrieved 21 February 2017. (p203-279), 2011
- "R&Sie (n) I've Heard About" (PDF). Retrieved 21 February 2017.
- "EeStairs Founding Father of the Landscape House". www.eestairs.com.
- "The World's First 3D-Printed Building Will Arrive In 2014". TechCrunch. 2012-01-20. Retrieved 2013-02-08.
- UniverseArchitecture (15 September 2014). "Landscape House Forum & Workshop Sept 3rd 2014_NRC Cafe_Amsterdam" – via YouTube.
- "Archived copy". Archived from the original on 2015-05-27. Retrieved 2015-05-27.CS1 maint: archived copy as title (link)
- Benedict. "AMT-SPECAVIA builds Europe's first habitable 3D printed building". 3ders.org. Retrieved 24 October 2017.
- "Shanghai-based WinSun 3D Prints 6-Story Apartment Building and an Incredible Home". 3DPrint.com. Retrieved 21 February 2017.
- "Dubai debuts world's first fully 3D-printed building". Inhabitat. Retrieved 21 February 2017.
- "U.S. President Obama viewed world's first 3D Print Canal House". 3Ders. Retrieved 21 February 2017.
- "How Dutch team is 3D-printing a full-sized house". BBC. 2014-05-03. Retrieved 2014-06-10.
- The plan to print actual houses shows off the best and worst of 3D printing (2014-06-26), James Robinson, PandoDaily
- "A San Francisco startup 3D printed a whole house in 24 hours". Engadget.
- "The construction of Europe's first 3D printed building has begun - 3D Printhuset". 3D Printhuset (in Danish). Retrieved 2018-02-11.
- COBOD (2018-09-26), Europe's first 3D printed building, The BOD, retrieved 2018-10-09
- "Spain unveils world's first 3D printed pedestrian bridge made of concrete". 3ders.org. Retrieved 2017-06-16.
- IN(3D)USTRY (2016-08-09), Acciona | José Daniel García | Architecture & Habitat Panel | IN(3D)USTRY, retrieved 2017-06-16
- Davide Sher. "Ancient water fountain in Russia fully restored using 3D printing by AMT SPETSAVIA". 3dprintingmedia.network. Retrieved 2018-10-08.
- "Building a lunar base with 3D printing / Technology / Our Activities / ESA". Esa.int. 2013-01-31. Retrieved 2014-03-13.
- Diaz, Jesus (2013-01-31). "This Is What the First Lunar Base Could Really Look Like". Gizmodo. Retrieved 2013-02-01.
- "3D Printing of a lunar base using lunar soil will print buildings 3.5 meters per hour". Newt Big Future. 2013-09-19. Archived from the original on 2013-09-23. Retrieved 2013-09-23.
- "3D printed moon building designs revealed". BBC News. 2013-02-01. Retrieved 2013-02-08.
- "NASA's plan to build homes on the Moon: Space agency backs 3D print technology which could build base". TechFlesh. 2014-01-15. Retrieved 2014-01-16.
- Steadman, Ian. "Giant Nasa spider robots could 3D print lunar base using microwaves (Wired UK)". Wired.co.uk. Retrieved 2014-03-13.
- Buswell, R.A.; Leal de Silva, W.R.; Jones, S.Z.; Dirrenberger, J. (October 2018). "3D printing using concrete extrusion: A roadmap for research". Cement and Concrete Research. 112: 37–49. doi:10.1016/j.cemconres.2018.05.006. ISSN 0008-8846.
- Lim, S.; Buswell, R.A.; Le, T.T.; Austin, S.A.; Gibb, A.G.F.; Thorpe, T. (January 2012). "Developments in construction-scale additive manufacturing processes". Automation in Construction. 21: 262–268. doi:10.1016/j.autcon.2011.06.010. ISSN 0926-5805.
- Gosselin, C.; Duballet, R.; Roux, Ph.; Gaudillière, N.; Dirrenberger, J.; Morel, Ph. (2016-06-15). "Large-scale 3D printing of ultra-high performance concrete – a new processing route for architects and builders" (PDF). Materials & Design. 100: 102–109. doi:10.1016/j.matdes.2016.03.097. ISSN 0264-1275.
- Le, T. T.; Austin, S. A.; Lim, S.; Buswell, R. A.; Gibb, A. G. F.; Thorpe, T. (2012-01-19). "Mix design and fresh properties for high-performance printing concrete". Materials and Structures. 45 (8): 1221–1232. doi:10.1617/s11527-012-9828-z. ISSN 1359-5997.
- Tay, Yi Wei Daniel; Li, Mingyang; Tan, Ming Jen (2019). "Effect of printing parameters in 3D concrete printing: Printing region and support structures". Journal of Materials Processing Technology. 271: 261–270. doi:10.1016/j.jmatprotec.2019.04.007.
- Zhang, Xu; Li, Mingyang; Lim, Jian Hui; Weng, Yiwei; Tay, Yi Wei Daniel; Pham, Hung; Pham, Quang-Cuong (November 2018). "Large-scale 3D printing by a team of mobile robots". Automation in Construction. 95: 98–106. doi:10.1016/j.autcon.2018.08.004. ISSN 0926-5805.
- "Contour Crafting". YouTube. 2006-04-27. Retrieved 2016-07-18.
- "3D printer can build a house in 20 hours". YouTube. 2012-08-13. Retrieved 2014-03-13.
- "China: Firm 3D prints 10 full-sized houses in a day". www.bbc.com. Retrieved 2014-04-28.
- "Exclusive: How Winsun Stole IP from Contour Crafting and Is "Faking" Their 3D Printed Homes & Apartments - 3DPrint.com - The Voice of 3D Printing / Additive Manufacturing". 3dprint.com.
- "Archived copy". Archived from the original on 2017-12-12. Retrieved 2017-12-11.CS1 maint: archived copy as title (link)
- Tay, Yi Wei Daniel; Bianchi, Pand; Paul, Suvash Chandra; Mohamed, Nisar; Tan, Ming Jen; Leong, Kah Fai (2017). "3D printing Trends in building and construction industry: A review". Virtual and Physical Prototyping. 12 (3): 261–276. doi:10.1080/17452759.2017.1326724.
- "European Institutions to Gather in Copenhagen for a Look at How 3D Printing is Disrupting Construction | 3DPrint.com | The Voice of 3D Printing / Additive Manufacturing". 3dprint.com. Retrieved 2017-12-11.
- "3D Printhuset organises second 3D Construction Printing Conference". TCT Magazine. 2017-11-06. Retrieved 2017-12-11.
- "USC's 'print-a-house' construction technology". Retrieved 2018-02-11.
- "3-D Printing Whole Buildings in Stone…in Space: This Printer Rocks". Fast Company. 2010-03-11. Retrieved 2018-02-11.
- "D-Shape: a 3D printer printing houses - 3D Printing". 3D Printing. 2012-04-12. Retrieved 2018-02-11.
- DShape3DPrinting (2012-09-25), Discovery Channel Covers DShape 3D Printing, retrieved 2018-02-11
- "The Man Who Prints Houses - Documentary about Enrico Dini and his heart and soul in 3D printing buildings". 3ders.org. Retrieved 2018-02-11.
- Campbell-Dollaghan, Kelsey. "How a Chinese Company 3D-Printed Ten Houses In a Single Day". Gizmodo. Retrieved 2018-02-11.
- "The World's First 3D-Printed Pedestrian Bridge Inaugurated In Madrid". Wonderful Engineering. 2017-01-31. Retrieved 2018-02-11.
- France-Presse, Agence (2017-10-18). "World's first 3D-printed bridge opens to cyclists in Netherlands". the Guardian. Retrieved 2018-02-11.
- "LafargeHolcim and XtreeE successfully 3D print Europe's first concrete structural element". 3ders.org. Retrieved 2018-02-11.
- "3D Printhuset Breaks Ground on 3D Printed Building in Copenhagen | 3DPrint.com | The Voice of 3D Printing / Additive Manufacturing". 3dprint.com. Retrieved 2018-02-11.
- "The Copenhagen Post - Danish News in English". cphpost.dk (in Danish). Retrieved 2018-02-11.
- "'Europe's first 3D-printed building' arrives in Copenhagen". Construction News. Retrieved 2018-02-11.
- "NASA - 3D Printing In Zero-G Technology Demonstration". Nasa.gov. 2014-03-04. Retrieved 2014-03-13.
External links
- Contour Crafting Project from USC, 2004
- Future of Construction Process: 3D Concrete Printing, 2010.
- Lunar Base Using 3D Printing, video, 2013.
- 3D Printing of a lunar base using lunar soil will print buildings at 3.5 meters per hour, NextBigFuture, 2013