Afterburner
An afterburner (or reheat U.K.) is an additional combustion component used on some jet engines, mostly those on military supersonic aircraft. Its purpose is to increase thrust, usually for supersonic flight, takeoff, and combat. Afterburning injects additional fuel into a combustor in the jet pipe behind (i.e., "after") the turbine, "reheating" the exhaust gas. Afterburning significantly increases thrust as an alternative to using a bigger engine with its attendant weight penalty, but at the cost of very high fuel consumption (decreased fuel efficiency) which limits its use to short periods. This aircraft application of reheat contrasts with the meaning and implementation of reheat applicable to gas turbines driving electrical generators and which reduces fuel consumption.[1]
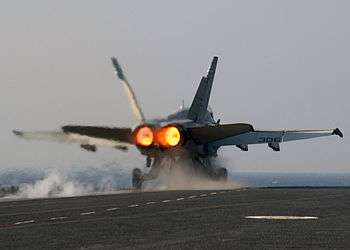
Jet engines are referred to as operating wet when afterburning is being used and dry when not.[2] An engine producing maximum thrust wet is at maximum power, while an engine producing maximum thrust dry is at military power.[3]
Principle
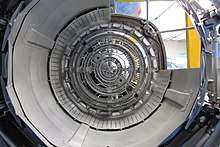
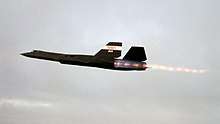
Jet-engine thrust is an application of Newton's reaction principle where the engine generates thrust because it increases the momentum of the air passing through it.[4] Thrust depends on two things: the velocity of the exhaust gas and the mass of the gas. A jet engine can produce more thrust by either accelerating the gas to a higher velocity or ejecting a greater mass of gas from the engine.[5] Designing a basic turbojet engine around the second principle produces the turbofan engine, which creates slower gas, but more of it. Turbofans are highly fuel-efficient and can deliver high thrust for long periods, but the design tradeoff is a large size relative to the power output. Generating increased power with a more compact engine for short periods can be achieved using an afterburner. The afterburner increases thrust primarily by accelerating the exhaust gas to a higher velocity.[6]
The values in the following are for an early jet engine the Pratt & Whitney J57, stationary on the runway[7] and illustrate the high values of afterburner fuel flow, gas temperature and thrust compared to those for the engine operating within the temperature limitations for its turbine.
The highest temperature in the engine (about 3,700 °F (2,040 °C)[8]) occurs in the combustor where fuel (8,520 lb/h (3,860 kg/h)) is burned completely in a relatively small proportion of the air entering the engine. The combustion products have to be diluted with air from the compressor to bring the gas temperature down to a value, called the Turbine Entry Temperature (TET) (1,570 °F (850 °C)), which gives the turbine an acceptable life.[9] Having to reduce the temperature of the combustion products by a large amount is one of the primary limitations on how much thrust can be generated (10,200 lbf (45,000 N)). Burning all the oxygen delivered by the compressor would create temperatures (3,700 °F (2,040 °C)) high enough to destroy everything in its path, but by mixing the combustion products with unburned air from the compressor at 600 °F (316 °C) a substantial amount of oxygen (fuel/air ratio 0.014 compared to a no-oxygen-remaining value 0.0687) is still available for burning large quantities of fuel (25,000 lb/h (11,000 kg/h)) in an afterburner. The gas temperature drops as it passes through the turbine to 1,013 °F (545 °C). The afterburner combustor reheats the gas but to a much higher temperature (2,540 °F (1,390 °C)) than the TET (1,570 °F (850 °C)). As a result of the temperature rise in the afterburner combustor, the gas is accelerated, firstly by the heat addition, known as Rayleigh flow, then by the nozzle to a higher exit velocity than occurs without the afterburner. The mass flow is also slightly increased by the addition of the afterburner fuel. The thrust with afterburning is 16,000 lbf (71,000 N).
The visible exhaust may show shock diamonds, which are caused by shock waves formed due to slight differences between ambient pressure and the exhaust pressure. This interaction causes oscillations in the exhaust jet diameter over a short distance and cause visible banding where the pressure and temperature is highest.
Thrust augmentation by heating bypass air
Thrust may be increased by burning fuel in a turbofan's cold bypass air, instead of the mixed cold and hot flows as in most afterburning turbofans.
An early augmented turbofan, the Pratt & Whitney TF30, used separate burning zones for the bypass and core flows with three of seven concentric spray rings in the bypass flow.[10] In comparison, the afterburning Rolls-Royce Spey used a twenty chute mixer before the fuel manifolds.
Plenum chamber burning (PCB), was developed for the vectored thrust Bristol Siddeley BS100 engine for the Hawker Siddeley P.1154. The cold bypass and hot core airflows were split between two pairs of nozzles, front and rear, in the same manner as the Rolls-Royce Pegasus, and additional fuel and afterburning was applied to the front nozzles only. It would have given greater thrust for take-off and supersonic performance in an aircraft similar to, but bigger, than the Hawker Siddeley Harrier.[11]
Duct heating was used by Pratt & Whitney for their JTF17 turbofan proposal for the U.S. Supersonic Transport Program in 1964 and a demonstrator engine was run.[12] The duct heater used an annular combustor and would be used for takeoff, climb and cruise at Mach 2.7 with different amounts of augmentation depending on aircraft weight.[13]
Design
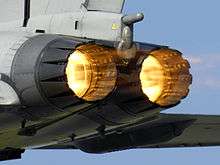
A jet engine afterburner is an extended exhaust section containing extra fuel injectors. Since the jet engine upstream (i.e., before the turbine) will use little of the oxygen it ingests, additional fuel can be burned after the gas flow has left the turbines. When the afterburner is turned on, fuel is injected and igniters are fired. The resulting combustion process increases the afterburner exit (nozzle entry) temperature significantly, resulting in a steep increase in engine net thrust. In addition to the increase in afterburner exit stagnation temperature, there is also an increase in nozzle mass flow (i.e. afterburner entry mass flow plus the effective afterburner fuel flow), but a decrease in afterburner exit stagnation pressure (owing to a fundamental loss due to heating plus friction and turbulence losses).
The resulting increase in afterburner exit volume flow is accommodated by increasing the throat area of the propulsion nozzle. Otherwise, the upstream turbomachinery rematches (probably causing a compressor stall or fan surge in a turbofan application). The first designs, e.g. Solar afterburners used on the F7U Cutlass, F-94 Starfire and F-89 Scorpion, had 2-position eyelid nozzles.[14] Modern designs incorporate not only VG nozzles but multiple stages of augmentation via separate spray bars.
To a first order, the gross thrust ratio (afterburning/dry) is directly proportional to the root of the stagnation temperature ratio across the afterburner (i.e. exit/entry).
Limitations
Due to their high fuel consumption, afterburners are only used for short duration high-thrust requirements. These include heavy-weight or short runway take-offs, assisting catapult launches from aircraft carriers, and during air combat. A notable exception is the Pratt & Whitney J58 engine used in the SR-71 Blackbird which used its afterburner for prolonged periods and was refuelled in-flight as part of every reconnaissance mission.
An afterburner has a limited life to match its intermittent use. The J58 was an exception with a continuous rating. This was achieved with thermal barrier coatings on the liner and flame holders[15] and by cooling the liner and nozzle with compressor bleed air[16] instead of turbine exhaust gas.
Efficiency
In heat engines such as jet engines, efficiency is highest when combustion occurs at the highest pressure and temperature possible, and expanded down to ambient pressure (see Carnot cycle).
Since the exhaust gas already has reduced oxygen owing to previous combustion, and since the fuel is not burning in a highly compressed air column, the afterburner is generally inefficient compared with the main combustor. Afterburner efficiency also declines significantly if, as is usually the case, the inlet and tailpipe pressure decreases with increasing altitude.
This limitation applies only to turbojets. In a military turbofan combat engine the bypass air is added into the exhaust, thereby increasing the core and afterburner efficiency. In turbojets the gain is limited to 50%, whereas in a turbofan it depends on the bypass ratio and can be as much as 70%.[17]
However, as a counterexample, the SR-71 had reasonable efficiency at high altitude in afterburning ("wet") mode owing to its high speed (mach 3.2) and correspondingly high pressure due to ram intake.
Influence on cycle choice
Afterburning has a significant influence upon engine cycle choice.
Lowering fan pressure ratio decreases specific thrust (both dry and wet afterburning), but results in a lower temperature entering the afterburner. Since the afterburning exit temperature is effectively fixed, the temperature rise across the unit increases, raising the afterburner fuel flow. The total fuel flow tends to increase faster than the net thrust, resulting in a higher specific fuel consumption (SFC). However, the corresponding dry power SFC improves (i.e. lower specific thrust). The high temperature ratio across the afterburner results in a good thrust boost.
If the aircraft burns a large percentage of its fuel with the afterburner alight, it pays to select an engine cycle with a high specific thrust (i.e. high fan pressure ratio/low bypass ratio). The resulting engine is relatively fuel efficient with afterburning (i.e. Combat/Take-off), but thirsty in dry power. If, however, the afterburner is to be hardly used, a low specific thrust (low fan pressure ratio/high bypass ratio) cycle will be favored. Such an engine has a good dry SFC, but a poor afterburning SFC at Combat/Take-off.
Often the engine designer is faced with a compromise between these two extremes.
History
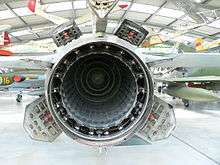
Early British reheat work included flight tests on a Rolls-Royce W2/B23 in a Gloster Meteor I in late 1944 and ground tests on a Power Jets W2/700 engine in mid-1945. This engine was destined for the Miles M.52 supersonic aircraft project.[18]
Early US research on the concept was done by NACA, in Cleveland, OH, leading to the publication of the paper "Theoretical Investigation of Thrust Augmentation of Turbojet Engines by Tail-pipe Burning" in January 1947.[19]
US work on afterburners in 1948 resulted in installations on early straight-wing jets such as the Pirate, Starfire and Scorpion.[20]
The new Pratt & Whitney J48 turbojet, at 8,000 lbf (36 kN) thrust with afterburner, would power the Grumman swept-wing fighter F9F-6, which was about to go into production. Other new Navy fighters with afterburners included the Chance Vought F7U-3 Cutlass, powered by two 6,000 lbf (27 kN) thrust Westinghouse J46 engines.
In the 1950s several large reheated engines were developed, such as the Orenda Iroquois, and the British de Havilland Gyron and Rolls-Royce Avon RB.146 variants. The Rolls-Royce Avon RB.146 variants powered the English Electric Lightning, the first supersonic aircraft in RAF service. The Bristol-Siddeley Rolls-Royce Olympus was fitted with reheat for the TSR-2. This system was designed and developed jointly by Bristol Siddeley and Solar of San Diego.[21] The reheat system for the Concorde was developed by Snecma.
Afterburners are generally used only in military aircraft, and are considered standard equipment on fighter aircraft. The handful of civilian planes that have used them include some NASA research aircraft, the Tupolev Tu-144, Concorde and the White Knight of Scaled Composites. Concorde flew long distances at supersonic speeds. Sustained high speeds would be impossible with the high fuel consumption of reheat, and the plane used afterburners at takeoff and to minimize time spent in the high-drag transonic flight regime. Supersonic flight without afterburners is referred to as supercruise.
A turbojet engine equipped with an afterburner is called an "afterburning turbojet", whereas a turbofan engine similarly equipped is sometimes called an "augmented turbofan".
A "dump-and-burn" is an airshow display feature where fuel is jettisoned, then intentionally ignited using the afterburner. A spectacular flame combined with high speed makes this a popular display for airshows, or as a finale to fireworks. Fuel dumping is used primarily to reduce the weight of an aircraft to avoid a heavy, high-speed landing. Other than for safety or emergency reasons, fuel dumping does not have a practical use.
See also
References
- Gas Turbine Design, Components and System Design Integration, Meinhard T. Schobeiri, ISBN 978 3 319 58376 1, p. 12/24
- Ronald D. Flack (2005). Fundamentals of jet propulsion with applications. Cambridge, UK: Cambridge University Press. ISBN 0-521-81983-0.
- Graham, Richard H. (July 15, 2008). Flying the SR-71 Blackbird: In the Cockpit on a Secret Operational Mission. MBI Publishing Company. p. 56. ISBN 9781610600705.
- "General Thrust Equation". www.grc.nasa.gov. Retrieved 19 March 2018.
- Lloyd Dingle; Michael H Tooley (23 September 2013). Aircraft Engineering Principles. Routledge. pp. 189–. ISBN 978-1-136-07278-9.
- Otis E. Lancaster (8 December 2015). Jet Propulsion Engines. Princeton University Press. pp. 176–. ISBN 978-1-4008-7791-1.
- The Aircraft Gas Turbine Engine and its operation, Part No. P&W 182408, P&W Operating Instruction 200, revised December 1982, United Technologies Pratt & Whitney, Figure 6-4
- AGARD-LS-183, Steady and Transient Performance Prediction, May 1982, ISBN 92 835 0674 X, section 2-3
- Zellman Warhaft (1997). An Introduction to Thermal-Fluid Engineering: The Engine and the Atmosphere. Cambridge University Press. pp. 97–. ISBN 978-0-521-58927-7.
- https://ntrs.nasa.gov/archive/nasa/casi.ntrs.nasa.gov/19720019364.pdf, Figure 2 schematic of afterburner
- "1962 | 2469 | Flight Archive". Flightglobal.com. Retrieved 2018-11-09.
- The Engines of Pratt & Whitney: A Technical History, Jack Connors2009, ISBN 978 1 60086 711 8. p.380
- https://apps.dtic.mil/dtic/tr/fulltext/u2/378365.pdf
- SAE 871354 "The First U.S. Afterburner Development"
- https://ntrs.nasa.gov/archive/nasa/casi.ntrs.nasa.gov/19840004244.pdf, p.5
- http://roadrunnersinternationale.com/pw_tales.htm, p.3
- "Basic Study of the Afterburner" Yoshiyuki Ohya, NASA TT F-13,657
- "Fast Jets-the history of reheat development at Derby" Cyril Elliott ISBN 1 872922 20 1 p14,16
- Bohanon, H R. "Theoretical investigation of thrust augmentation of turbojet engines by tail-pipe burning" (PDF). ntrs.nasa.gov.
- "Afterburning: A Review of Current American Practice" Flight magazine 21 November 1952 p648
- "Bristol/Solar reheat" Flight magazine 20 September 1957 p472
External links
![]() |
Wikimedia Commons has media related to Afterburners. |