Ice protection system
Ice protection systems are designed to keep atmospheric ice from accumulating on aircraft surfaces (particularly leading edges), such as wings, propellers, rotor blades, engine intakes, and environmental control intakes. If ice is allowed to build up to a significant thickness it can change the shape of airfoils and flight control surfaces, degrading the performance, control or handling characteristics of the aircraft. An ice protection system either prevents formation of ice, or enables the aircraft to shed the ice before it can grow to a dangerous thickness.
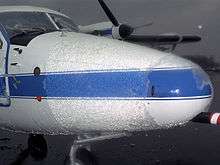
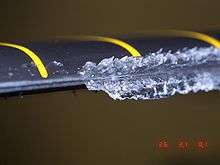
Types
Pneumatic deicing boots
The pneumatic boot is usually made of layers of rubber or other elastomers, with one or more air chambers between the layers. If multiple chambers are used, they are typically shaped as stripes aligned with the long direction of the boot. It is typically placed on the leading edge of an aircraft's wings and stabilizers. The chambers are rapidly inflated and deflated, either simultaneously, or in a pattern of specific chambers only. The rapid change in shape of the boot is designed to break the adhesive force between the ice and the rubber, and allow the ice to be carried away by the relative wind flowing past the aircraft. However, the ice must be carried away cleanly from the trailing sections of the surface, or it could re-freeze behind the protected area. Re-freezing of ice in this manner was a contributing factor to the crash of American Eagle Flight 4184.
Certain older designs of pneumatic boot were subject to a phenomenon known as ice bridging. If the ice had not accumulated to a sufficient thickness and fragility, malleable ice could be pushed into a shape out of reach of the inflatable sections of the boot. This problem is mostly solved in modern designs by increasing the speed of inflation/deflation action, and by alternating the timing of inflating/deflating adjacent chambers.[1]
The pneumatic boot is most appropriate for low and medium speed aircraft, especially those without leading edge lift devices such as slats. Therefore, this system is most commonly found on turbo propeller aircraft such as the Saab 340, Embraer EMB 120 Brasilia, and British Aerospace Jetstream 41. Pneumatic De-Icing boots are sometimes found on larger piston prop aircraft, smaller turbojets such as the Cessna Citation V, and some older turbojets. This device is rarely used on modern turbojet aircraft.
This device was invented by the Goodrich Corporation (previously known as B.F. Goodrich) in 1923.
Electro-thermal
Electro-thermal systems use resistive circuits buried in the airframe structure to generate heat when a current is applied. The heat can be generated continuously to protect the aircraft from icing (anti-ice mode), or intermittently to shed ice as it accretes on key surfaces (de-ice). De-ice operation is generally preferred due to the lower power consumption, as the system only needs to melt the contact layer of ice for the wind-shear to shed the remainder.[2]
The Boeing 787 Dreamliner is an example of a commercial airframe to use electro-thermal ice protection. In this case the resistive heating circuit is embedded inside the glass and carbon composite wing structure. Boeing claims the system uses half the energy of traditional bleed-air systems (as provided by the engines), and that drag and noise are also reduced.[3]
For metallic aircraft skin structures, etched foil resistive heating circuits have been bonded to the inside surface of skins. This approach holds the potential of enabling a lower overall power requirement than the embedded circuit approach due to its ability to operate at significantly higher power densities.[4]
The Thermawing is an electrical ice protection system for general aviation. ThermaWing uses a flexible, electrically conductive, graphite foil attached to a wing's leading edge. Electric heaters heat the foil and melt the ice.
A new proposal uses a special soot made of carbon nanotubes. A thin filament is spun on a winder to create a 10 micron-thick film, equivalent to an A4 sheet of paper. The film is a poor conductor of electricity, because of the air gaps between the nanotubes. Instead, current manifests as a near instantaneous rise in temperature. It heats up twice as fast as nichrome, the heating element of choice for in-flight de-icing, using half as much energy at one ten-thousandth the weight. The amount of material needed to cover the wings of a jumbo jet weighs 80 grams (2.8 oz). The material cost is approximately 1% of nichrome. Aerogel heaters could be left on continuously at low power, to prevent ice from forming.[5]
Bleed air
A bleed air system is the method used by most larger jet aircraft to keep flight surfaces above the freezing temperature required for ice to accumulate (called anti-icing). The hot air is "bled" off the jet engine into piccolo tubes routed through wings, tail surfaces, and engine inlets. The spent bleed air is exhausted through holes in the lower surface of the wing.
Electro-mechanical
Electro-mechanical Expulsion Deicing Systems (EMEDS) use a mechanical force to knock the ice off the flight surface. Typically, actuators are installed underneath the skin of the structure. The actuator is moved to induce a shock wave in the protected surface to dislodge the ice. Cox and Company, Inc. of Plainview, NY developed a lightweight, low-power system called EMEDS that is the first ice protection technology to receive FAA certification in 50 years, and is currently in-service on multiple commercial aircraft (FAA Part 23 and Part 25)[6][7][8] and military aircraft.[9]
Innovative Dynamics has developed a lightweight and low-power system using actuators, called EIDI.
Hybrid Electro-Mechanical Expulsion Deicing Systems combine an EMEDS de-icer with an electrical heating element anti-icer. The heater prevents ice accumulation on the leading edge of the airfoil and the actuators of the EMED system remove ice that accumulates aft of the heated portion of the airfoil.[10] Cox and Company, Inc. of Plainview, NY has developed multiple versions of Hybrid EMED systems referred to as Thermo-Mechanical Expulsion Deicing System (TMEDS).
TKS Ice Protection
The TKS[11] Ice Protection System, manufactured by CAV Ice Protection, is a fluid-based ice protection system used to help aircraft safely exit in-flight icing conditions. The system uses a glycol-based fluid to cover the critical surfaces of an aircraft and prevent the risk of any ice forming on the leading edges of the wings. The system can also break the ice that has accumulated (chemically). Developed by Tecalemit-Kilfrost-Sheepbridge Stokes (TKS), the system was primarily used during World War II by the British. During World War II, it was used for the safety and security of Royal Air Force (RAF) bombers in icing conditions.[12]
Ice Protection with the TKS Ice Protection system is achieved by mounting laser-drilled titanium porous panels on the leading edges of the airframe. The panel skin is perforated with laser-drilled holes 1⁄400 inch (0.064 mm) in diameter, with 800 holes per square inch (120/cm2).[13] TKS fluid exudes through the panels on the leading edges of the wings, horizontal stabilizers. Fluid is also thoroughly distributed from the slinger-ring on the propeller and from the windshield spraybar. Secondary fairings or structures such as lift struts can also be protected. Engine inlets may be protected, as well. The fluid is pumped from a tank by an electrically-driven metering pump through a microfilter to proportioning units. Proportioning units contain calibrated capillary tubes that divide the flow to the individual needs of the porous panels and the slinger ring. One metering pump is provided for inadvertent systems. For systems certified for flight into known icing conditions (FIKI), two pumps are installed for redundancy and can be selected individually. Fluid for the windshield spraybar system is provided by an on-demand gear pump. One or two windshield pumps are provided depending on the certification basis. As the TKS Ice Protection system is used, any accumulation of debris is flushed out. Glycol has cleaning properties and will not harm the paint finish of the aircraft.
Passive
Passive systems employ hydrophobic surfaces. Appropriately designed textiles, characterised by a high level of water resistance and natural self-cleaning effect can stop the adhesion of water[14] , thereby eliminating ability for ice build-up.
Another passive system makes use of the amount of time that a water drop needs to be in touch with frozen material before the drop freezes and sticks. Rough surfaces, with ridges shorten the time that water stays in contact. When a drop hits any surface, it flattens into a pancake, then regains a round shape and bounces up. Ridges split large drops into smaller ones. The smaller drops re-formed and bounced away up to 40 percent quicker than the larger drops. Nature employs this concept, as shown in the difference between lotus and nasturtiums. The latter's leaves are rougher and ice less than the smoother lotus.[15]
Aircraft icing accidents result from a combination of increased weight, increased drag, decrease or loss of lift, and decrease or loss of thrust from ice accumulation on the airframe, airfoil(s), propellers (if present) and or wings, depending on the type of ice that forms (e.g. rime ice, clear ice, etc.), which is a function of the specific meteorological conditions. Also, induction ice can cause power losses in icing conditions either externally at air intakes (either turbine or piston aircraft), or locally in the induction system within the engine (e.g. the carburetor of a non-fuel injected reciprocating engine).
When ice builds up by either freezing upon impingement on the leading edge or freezing as runback on aerodynamic lift or thrust surfaces, such as the wing, tailplane, and propeller blades, the modification of airflow changes the aerodynamic performance of the surfaces by modifying either their shape and/or their surface characteristics. When this happens, it results in an increase of both primary and induced drag, and decrease of lifting force or thrust. Depending on whether the net lift of a tailplane airfoil was downward or upward, then the loss of tailplane lift (upward or downward) can cause a change in pitch (often to a more nose down pitch) or, if the critical angle of attack of the tailplane is exceeded, a tailplane aerodynamic "stall".
Both a decrease in lift on the wing due to an altered airfoil shape, and the increase in weight of the aircraft directly caused by the ice load will usually result in the pilot having to fly at a greater angle of attack of the airfoil to make up for the loss of lift needed to maintain an assigned altitude, or chosen rate of descent/ascent, notwithstanding power changes that are available and the airspeed desired. If the greater angle of attack exceeds the critical angle of attack, an aerodynamic stall will occur, which can occur at any airspeed and at any flight attitude, an oft-overlooked fact (even by pilots). In summary, depending on whether the icing event occurs on the wing or horizontal stabilizer/stabilator, the lifting force that is deceased can result in a pitch up or pitch down.
One "trick" employed by pilots wishing to improve both the airspeed and load carrying performance of aircraft in both icing and non-icing conditions is to load the aircraft closer to its rear CG (center of gravity) limit, and/or fly with rearward (nose up) trim. This causes the pilot to have to push forward on the elevator controls, increasing the camber of the upper surface of the horizontal stabilizer/elevator (tailplane) surface. The resulting decrease in loading on the front wing then allows the front wing to fly at a lower angle of attack, farther away from an aerodynamic "stall". This can also allow less induced drag by the wing, and hence a greater cruise speed for a given power setting. Even if the aircraft loading is not changed to a more rearward CG, flying with the elevator trimmed for nose up results in having to hold forward force on the controls, which causes the elevator trim tab to increase the camber of the tailplane upper surface (albeit tiring, and therefore employed only in unusual or temporary circumstances, say during takeoff or in icing conditions), and hence lower the tailplane angle of attack.
Rotary-surface icing
Ice can also accumulate on helicopter rotor blades and aircraft propellers. The accretion causes weight and aerodynamic imbalances that are amplified due to the rapid rotation of the propeller or rotor.
Engine-inlet icing
.jpg)
Ice accumulation on the leading edge (lip) of engine inlets causes flow problems and can lead to ice ingestion. In turbofan engines, laminar airflow is required at the face of the fan. Because of this, most engine ice protection systems are anti-ice systems (prevent build up).
Icephobic materials
In order to minimize ice accretion on the various surfaces of the aircraft, researchers have during the course of history sought to find icephobic materials for usage in aeronautical applications. Examples of such materials are carbon nanotubes and slippery liquid infused porous surfaces (SLIPS).[16]
Weeping wing
A weeping wing is a chemical aircraft airborne ice protection system wherein a glycol-based chemical is released onto the wing surface using small orifices on the leading edge of the wing. This system provides both ice formation prevention (anti-ice) and removal of ice which has already formed (de-ice).
System components
- Fluid reservoir
- Fluid pump
- Fluid Ducting
- Fluid
- Calibrated orifices
- Activation Circuit
Operation
The system is activated using a switch in the cockpit. This turns on the fluid pump, which pumps fluid out of the reservoir, through the ducting and out onto the calibrated orifices on the wing leading edge. As the fluid flows along the airstream (both on the top and bottom surfaces of the wing), a thin coat of fluid is left that protects the surface from icing. The excess fluid then leaves the wing surface and slides out behind the wing's trailing edge.
See also
Icing accidents
- Aero Caribbean Flight 883 (2010)
- Air Algérie Flight 5017 (2014)
- Air Florida Flight 90 (1982)
- Air France Flight 447 (2009)
- Arrow Air Flight 1285 (1985)
- Colgan Air Flight 3407 (2009)
- Comair Flight 3272 (1997)
- Loganair Flight 670 (2001)
- Scandinavian Airlines Flight 751 (1991)
- United Express Flight 2415 (1989)
- West Caribbean Airways Flight 708 (2005)
References
- "FAA Information for Operators 09005" (PDF).
- Sloan, Jeff. "787 integrates new composite wing deicing system". www.compositesworld.com.
- "AERO - 787 No-Bleed Systems". www.boeing.com.
- http://papers.sae.org/2009-01-3165/ | Capitalizing on the Increased Flexibility that Comes from High Power Density Electrothermal Deicing
- "De-icing aeroplanes: Sooty skies". The Economist. 2013-07-26. Retrieved 2013-12-11.
- "Low Power Ice Protection Systems - Cox & Company, Inc". Cox & Company, Inc. 2014. Archived from the original on 2017-04-21. Retrieved 2014-12-17.
- "How They Work: Ice Protection Systems". Aviation Week. 2010.
- "Electro- mechanical Deicing". Air & Space Magazine. 2004.
- "CUTAWAY: P-8A Poseidon - A Boeing with boost of bravado". Flight International. 2010.
- "Deicing and Anti-Icing Unite". NASA STI. 2002.
- "flight april | april iith | fluid system | 1946 | 0710 | Flight Archive". Flightglobal.com. Retrieved 2013-12-11.
- "De-Icing for To-day".
- E. McMann, Michael. "TKS Ice Protection: Flying year-round becomes a possibility with the TKS Ice Protection system". Plane & Pilot Magazine. Werner Publishing Corporation. Retrieved 17 October 2014.
- Aryeh Ben-Na'im Hydrophobic Interaction Plenum Press, New York, ISBN 0-306-40222-X
- Gorman, James (2013-12-03). "Using a Rough Surface to Stay Dry". The New York Times.
- Kim, Philseok; Wong, Tak-Sing; Alvarenga, Jack; Kreder, Michael J.; Adorno-Martinez, Wilmer E.; Aizenberg, Joanna (28 August 2012). "Liquid-Infused Nanostructured Surfaces with Extreme Anti-Ice and Anti-Frost Performance". ACS Nano. 6 (8): 6569–6577. doi:10.1021/nn302310q – via ACS Publications.
External links
- SAE paper on Electro-Thermal Ice Protection by Strehlow, R. and Moser, R.