19-inch rack
A 19-inch rack is a standardized frame or enclosure for mounting multiple electronic equipment modules. Each module has a front panel that is 19 inches (482.6 mm) wide. The 19 inch dimension includes the edges or "ears" that protrude from each side of the equipment, allowing the module to be fastened to the rack frame with screws. Common uses include computer servers, telecommunications equipment and networking hardware, and audiovisual production and scientific equipment.
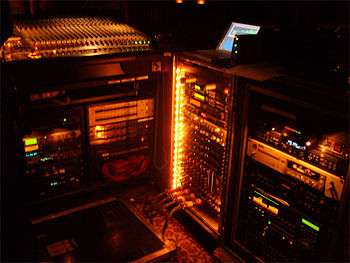
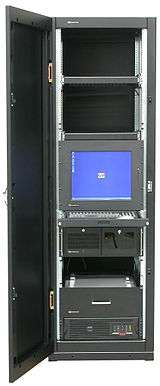
Overview and history
Equipment designed to be placed in a rack is typically described as rack-mount, rack-mount instrument, a rack-mounted system, a rack-mount chassis, subrack, rack-mountable, or occasionally simply shelf. The height of the electronic modules is also standardized as multiples of 1.75 inches (44.45 mm) or one rack unit or U (less commonly RU). The industry standard rack cabinet is 42U tall.[1], however, 45U racks are also common.
The term relay rack appeared first in the world of telephony.[2]
By 1911, the term was also being used in railroad signaling.[3] There is little evidence that the dimensions of these early racks were standardized.
.png)
The 19-inch rack format with rack-units of 1.75 inches (44.45 mm) was established as a standard by AT&T around 1922 in order to reduce the space required for repeater and termination equipment in a telephone company central office. The earliest repeaters from 1914 were installed in ad-hoc fashion on shelves, in wooden boxes and cabinets. Once serial production started, they were built into custom-made racks, one per repeater. But in light of the rapid growth of the toll network, the engineering department of AT&T undertook a systematic redesign, resulting in a family of modular factory-assembled panels all "designed to mount on vertical supports spaced 191⁄2 inches between centers. The height of the different panels will vary, ... but ... in all cases to be a whole multiple of 13⁄4 inches".[4]
By 1934, it was an established standard with holes tapped for 12-24 screws with alternating spacings of 1.25 inches (31.75 mm) and 0.5 inches (12.70 mm) [5] The EIA standard was revised again in 1992 to comply with the 1988 public law 100-418, setting the standard U as 15.875 mm (0.625 in) + 15.875 mm (0.625 in) + 12.7 mm (0.500 in), making each "U" 44.45 millimetres (1.75 in).[6]
The 19-inch rack format has remained constant while the technology that is mounted within it has changed considerably and the set of fields to which racks are applied has greatly expanded. The 19-inch (482.6 mm) standard rack arrangement is widely used throughout the telecommunication, computing, audio, video, entertainment and other industries, though the Western Electric 23-inch standard, with holes on 1-inch (25.4 mm) centers, is still used in legacy ILEC/CLEC facilities.
Nineteen-inch racks in two-post or four-post form hold most equipment in modern data centers, ISP facilities, and professionally designed corporate server rooms. They allow for dense hardware configurations without occupying excessive floorspace or requiring shelving.
Nineteen-inch racks are also often used to house professional audio and video equipment, including amplifiers, effects units, interfaces, headphone amplifiers, and even small scale audio mixers. A third common use for rack-mounted equipment is industrial power, control, and automation hardware.
Typically, a piece of equipment being installed has a front panel height 1⁄32 inch (0.03125 inches or 0.794 millimetres) less than the allotted number of Us. Thus, a 1U rackmount computer is not 1.75 inches (44.45 mm) tall but is 1.71875 inches (43.66 mm) tall. If n is number of rack units, the ideal formula for panel height is h = (1.75n − 0.031) for calculating in inches, and h = (44.45n − 0.794) for calculating in millimetres. This gap allows a bit of room above and below an installed piece of equipment so it may be removed without binding on the adjacent equipment.
Equipment mounting

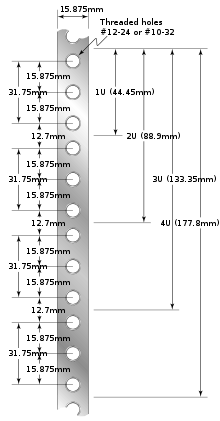
Fastening
Originally, the mounting holes were tapped with a particular screw thread. When rack rails are too thin to tap, rivnuts or other threaded inserts can be used, and when the particular class of equipment to be mounted is known in advance, some of the holes can be omitted from the mounting rails.[7]
Threaded mounting holes in racks where the equipment is frequently changed are problematic because the threads can be damaged or the mounting screws can break off; both problems render the mounting hole unusable. Tapping large numbers of holes that may never be used is expensive; nonetheless tapped-hole racks are still in use, generally for hardware that rarely changes. Examples include telephone exchanges, network cabling panels, broadcast studios and some government and military applications.
The tapped-hole rack was first replaced by clearance-hole (Round Hole, Round Unthreaded Holes,[8] and Versa Rail[9]) racks. The holes are large enough to permit a bolt to be freely inserted through without binding, and bolts are fastened in place using cage nuts. In the event of a nut being stripped out or a bolt breaking, the nut can be easily removed and replaced with a new one. Production of clearance-hole racks is less expensive because tapping the holes is eliminated and replaced with fewer, less expensive, cage nuts.
The next innovation in rack design has been the square-hole rack. Square-hole racks allow boltless mounting, such that the rack-mount equipment only needs to insert through and hook down into the lip of the square hole. Installation and removal of hardware in a square hole rack is very easy and boltless, where the weight of the equipment and small retention clips are all that is necessary to hold the equipment in place. Older equipment meant for round-hole or tapped-hole racks can still be used, with the use of cage nuts made for square-hole racks.
Structural support
Rack-mountable equipment is traditionally mounted by bolting or clipping its front panel to the rack. Within the IT industry, it is common for network/communications equipment to have multiple mounting positions, including table-top and wall mounting, so rack-mountable equipment will often feature L-brackets that must be screwed or bolted to the equipment prior to mounting in a 19-inch rack. With the prevalence of 23-inch racks in the Telecoms industry, the same practice is also common, but with equipment having 19-inch and 23-inch brackets available, enabling them to be mounted in existing racks.
A key structural weakness of front-mounted support is the shear stress placed on the mounting rails and the leading edge of the equipment. As a result, 4-post racks have become common, with such racks featuring a mirrored pair of rear mounting posts. Since the spacing between the front and rear mounting posts may differ between rack vendors and/or the configuration of the rack (some racks may incorporate front and rear rails that may be moved forwards and backwards, i.e. APC SX-range racks), it is common for equipment that features 4-post mounting brackets to have an adjustable rear bracket.
Servers and deep pieces of equipment are often mounted using rails that are bolted to the front and rear posts (as above, it is common for such rails to have an adjustable depth), allowing the equipment to be supported by four posts, while also enabling it to be easily installed and removed.
Although there is no standard for the depth of equipment, nor specifying the outer width and depth of the rack enclosure itself (incorporating the structure, doors and panels that contain the mounting rails), there is a tendency for 4-post racks to be 600 mm (23.62 in) or 800 mm (31.50 in) wide, and for them to be 600 mm (23.62 in), 800 mm (31.50 in) or 1,010 mm (39.76 in) deep. This of course varies by manufacturer, the design of the rack and its purpose, but through common constraining factors (such as raised floor tile dimensions), these dimensions have become quite common. The extra width and depth enables cabling to be routed with ease (also helping to maintain bend-radius for fibre and copper cables) and deeper equipment to be utilised. A common feature in IT racks are mounting positions for "Zero-U" accessories, such as PDUs (power distribution units) and vertical cable managers/ducts, that utilise the space between the rear rails and the side of the rack enclosure.
The strength required of the mounting posts means they are invariably not merely flat strips but actually a wider folded strip arranged around the corner of the rack. The posts are usually made of steel of around 2 mm thickness (the official standard recommends a minimum of 1.9 mm), or of slightly thicker aluminum.
Racks, especially two-post racks, are often secured to the floor or adjacent building structure so as not to fall over. This is usually required by local building codes in seismic zones. According to Telcordia Technologies Generic Requirements document GR-63-CORE, during an earthquake, telecommunications equipment is subjected to motions that can over-stress equipment framework, circuit boards, and connectors. The amount of motion and resulting stress depends on the structural characteristics of the building and framework in which the equipment is contained, and the severity of the earthquake. Seismic racks rated according to GR-63, NEBS Requirements: Physical Protection, are available,[10] with Zone 4 representing the most demanding environment.[11][12] GR-3108, Generic Requirements for Network Equipment in the Outside Plant (OSP), specifies the usable opening of seismic-compliant 19-inch racks.
Rails (slides)
Heavy equipment or equipment which is commonly accessed for servicing, for which attaching or detaching at all four corners simultaneously would pose a problem, is often not mounted directly onto the rack but instead is mounted via rails (or slides). A pair of rails is mounted directly onto the rack, and the equipment then slides into the rack along the rails, which support it. When in place, the equipment may also then be bolted to the rack. The rails may also be able to fully support the equipment in a position where it has been slid clear of the rack; this is useful for inspection or maintenance of equipment which will then be slid back into the rack.[13] Some rack slides even include a tilt mechanism allowing easy access to the top or bottom of rack-mounted equipment when it is fully extended from the rack.[14]
Slides or rails for computers and other data processing equipment such as disk arrays or routers often need to be purchased directly from the equipment manufacturer, as there is no standardization on such equipment's thickness (measurement from the side of the rack to the equipment) or means for mounting to the rail.
A rails kit may include a cable management arm (or CMA), which folds the cables attached to the server and allows them to expand neatly when the server is slid out, without being disconnected.
Computer mounting
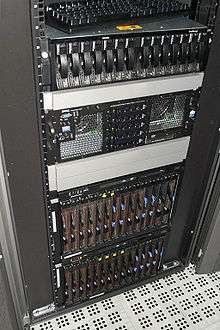
Computer servers designed for rack-mounting can include a number of extra features to make the server easy to use in the rack:
- The sliding rails can lock in various extended positions to prevent the equipment from moving when extended out from the rack for service.
- The server itself might have locking pins on the sides that just drop into slots on the extended rail assembly, in a manner similar to a removable kitchen drawer. This permits very easy server installation and removal since there is no need for the server to be held in midair while someone fastens each rail to the sides of the server with screws.
- Some manufacturers of rack-mount hardware include a folding cable tray behind the server, so that the cables are held into a neat and tidy folded channel when inside the rack, but can unfold out into a long strip when pulled out of the rack, allowing the server to continue to be plugged in and operating normally even while fully extended and hanging in mid-air in front of the rack. This piece of equipment thus simplifies maintenance, but at the cost of providing a restriction to airflow.
- Rack-optimized servers might duplicate indicator lights on the front and rear of the rack to help identify a machine needing attention, or provide separate "identify" LED indicators on both sides of the server (which can be turned on in software or by pushing an associated button). Since some configurations permit over fifty 1U servers in a single rack, this provides a simple method to determine exactly which machine is having a problem when at the rear of the rack.
- A handle may be provided at the rear of the server rails, to help pull or push the server without having to pull on the cables.
When there is a large number of computers in a single rack, it is impractical for each one to have its own separate keyboard, mouse, and monitor. Instead, a KVM switch or LOM software is used to share a single keyboard/video/mouse set amongst many different computers.
Since the mounting hole arrangement is vertically symmetric, it is possible to mount rack-mountable equipment upside-down. However, not all equipment is suitable for this type of mounting. For instance, most optical disc players will not work upside-down because the driving motor mechanism does not grip the disc.
Rack types
19-inch server racks can vary in qualities. A standard 19-inch server rack cabinet is typically 42u in height, 600 millimetres (24 in) wide, and 36 inches (914.40 mm) deep [15]. Newer server rack cabinets come with adjustable mounting rails allowing the user to place the rails at a shorter depth if needed. There are a multitude of specialty server racks including soundproof server racks, air conditioned server racks, NEMA rated, seismic rated, open frame, narrow, and even miniature 19-inch racks for smaller applications. Cabinets are generally sized to be no wider than the standard 24-inch-wide (610 mm) floor tiles used in most data centers.
Racks carrying telecom equipment like routers and switches often have extra width to accommodate the many cables on the sides.
Four-post cabinet racks
Four-post racks allow for mounting rails to support the equipment at the front and rear. These racks may be open in construction without sides or doors, or may be enclosed by front and/or rear doors, side panels, and tops.[16] Most data centers use four-post racks.
Two-post relay racks
Two-post racks provide two vertical posts. These posts are typically heavy gauge metal or extruded aluminum. A top bar and wide foot connect the posts and allow the rack to be securely attached to the floor and/or roof for seismic safety. Equipment can be mounted either close to its center of gravity (to minimize load on its front panel), or via the equipment's front panel holes.[17] The Relay Racks name comes from early two-post racks which housed telephone relay and switching equipment. Two-post racks are most often used for telecommunication installations.
ATA road case racks
19-inch equipment that needs to be moved often or protected from harsh treatment can be housed in an Air Transport Association of America (ATA) approved road case sometimes also referred to as flight case. Road cases are typically made from polyvinyl chloride (PVC) laminated plywood sides, joined by extruded aluminum edging, steel corners, handles and latches. Larger cases typically have wheels for easy transport. Road case racks come in different heights based on the 1U standard and different depths. Non-isolated cases simply mount 19-inch mounting rails inside the case. To protect equipment from shock and vibration road rack cases use an inner and outer case. These cases can be isolated by thick layers of foam or may use spring-loaded shock mounting. Touring musicians, theatrical productions and sound and light companies use road case racks.[18]
Fiberglass reinforced plastic case racks
In 1965, a durable fiber reinforced plastic 19-inch rackmount case was patented by ECS Composites and became widely used in military and commercial applications for electronic deployment and operation. State-of-the-art rackmount cases are now also constructed of thermo stamped composite, carbon fiber, and DuPont’s Kevlar for demanding military and commercial uses.
Polyethylene molded case racks
Portable rack cases using a rotary-molded polyethylene outer shell are a lower-cost alternative to the more durable ATA-approved case. These cases are marketed to musicians and entertainers for equipment not subject to frequent transportation and rough handling. The polyethylene shell is not fiberglass reinforced and is not rigid. The shape of small cases is maintained by the rack rails and the cover seal extrusions alone. Larger cases are further reinforced with additional plywood or sheet metal. The outer shell is frequently embossed in a self-mating pattern to combat the tendency for stacked cases to deform slightly creating a slope that encourages the upper case to slide off. The cases typically use extruded aluminum bands at the ends of the body with tongue-and-groove mating to like bands for the covers. End covers are typically secured with either a simple draw latch or a rotary cam "butterfly" latch, named for the shape of the twist handle.
Cooling
There is no standard for airflow and cooling of rack-mounted equipment. A variety of airflow patterns can be found, including front intakes and rear exhausts, as well as side intakes and exhausts. Low-wattage devices may not employ active cooling, but use only passive thermal radiation and convection to dissipate heat.
For rack-mounted computer servers, devices generally intake air on the front and exhaust on the rear. This prevents circular airflows where hot exhaust air is recirculated through an adjacent device and causes overheating.
Although open-frame racks are the least expensive, they also expose air-cooled equipment to dust, lint, and other environmental contamination. An enclosed sealed cabinet with forced air fans permits air filtration to protect equipment from dust.
Large server rooms will often group rack cabinets together so that racks on both sides of an aisle are either front-facing or rear-facing, which simplifies cooling by supplying cool air to the front of the racks and collecting hot air from the rear of the racks. These aisles may themselves be enclosed into a cold air containment tunnel so that cooling air does not travel to other parts of the building where it is not needed or mixes with hot air, making it less efficient. Raised or false floor cooling in server rooms can serve a similar purpose; they permit cooling airflow to equipment through the underfloor space to the underside of enclosed rack cabinets.[19]
A difficulty with forced air fan cooling in rack equipment is that fans can fail due to age or dust. The fans themselves can be difficult to replace. In the case of network equipment, it may be necessary to unplug 50 or more cables from the device, remove the device from the rack, and then disassemble the device chassis to replace the fans.
However, some rack equipment has been designed to make fan replacement easy, using quick-change fan trays that can be accessed without removing the cabling or the device from the rack, and in some cases without turning off the device so that operation is uninterrupted during replacement.
Specifications
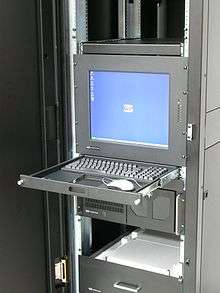
The formal standards for a 19-inch (482.6 mm) rack are available from the following:
- Electronic Industries Alliance EIA-310-D, Cabinets, Racks, Panels, and Associated Equipment, dated September 1992. (Latest Standard Now REV E 1996)
- Consumer Electronics Association CEA-310-E design requirements for Cabinets, Panels, Racks and Subracks., dated December 14, 2005
- International Electrotechnical Commission - Multiple documents are available in French and English versions.
- IEC 60297 Mechanical structures for electronic equipment - Dimensions of mechanical structures of the 482,6 mm (19 in) series
- IEC 60297-1 Replaced by IEC 60297-3-100
- IEC 60297-2 Replaced by IEC 60297-3-100
- IEC 60297-3-100 Part 3-100: Basic dimensions of front panels, subracks, chassis, racks and cabinets
- IEC 60297-3-101 Part 3-101: Subracks and associated plug-in units
- IEC 60297-3-102 Part 3-102: Injector/extractor handle
- IEC 60297-3-103 Part 3-103: Keying and alignment pin
- IEC 60297-3-104 Part 3-104: Connector dependent interface dimensions of subracks and plug-in units
- IEC 60297-3-105 Part 3-105: Dimensions and design aspects for 1U chassis
- IEC 60297-4 Replaced by IEC 60297-3-102
- IEC 60297-5 Multiple documents, -100, 101, 102, ... 107, replaced by IEC 60297-3-101
- IEC 60297 Mechanical structures for electronic equipment - Dimensions of mechanical structures of the 482,6 mm (19 in) series
- Deutsches Institut für Normung DIN 41494 - Multiple documents in German but some documents are available in English.
- DIN 41494 Equipment practices for electronic equipment; mechanical structures of the 482,6 mm (19 inch) series
- DIN 41494-7 Dimensions of cabinets and suites of racks.
- DIN 41494-8 Components on front panels; mounting conditions, dimensions
- DIN IEC 60297-3-100 (see above in IEC section)
- DIN 41494 Equipment practices for electronic equipment; mechanical structures of the 482,6 mm (19 inch) series
A rack's mounting fixture consists of two parallel metal strips (also referred to as "posts" or "panel mounts") standing vertically. The posts are each 0.625 inches (15.88 mm) wide, and are separated by a gap of 17.75 inches (450.85 mm), giving an overall rack width of 19 inches (482.60 mm). The posts have holes in them at regular intervals, with both posts matching, so that each hole is part of a horizontal pair with a center-to-center distance of 18.312 inches (465.12 mm).[20]
The holes in the posts are arranged vertically in repeating sets of three, with center-to-center separations of 0.5 inches (12.70 mm), 0.625 inches (15.88 mm), 0.625 inches (15.88 mm). The hole pattern thus repeats every 1.75 inches (44.45 mm).
Holes so arranged can either be tapped (usually 10-32 UNF thread, or, less often, 6mm metric) or have square holes for cage nuts.
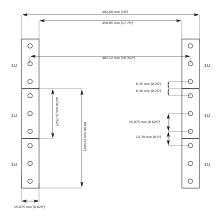
Rack unit
Racks are vertically divided into regions, 44.45 millimetres (1.75 in) in height, within which there are three complete hole pairs on each side, the holes centered 6.35 millimetres (0.25 in), 22.25 millimetres (0.88 in), and 38.15 millimetres (1.50 in) from the top or bottom of the region. Such a region is commonly known as a U, for unit, RU for rack unit or, in German, HE, for Höheneinheit, and heights within racks are measured by this unit. Rack-mountable equipment is usually designed to occupy some integer number of U. For example, an oscilloscope might be 4U high, and rack-mountable computers and servers are mostly between 1U and 4U high. A blade server enclosure might require 10U.
Occasionally, one may see fractional U devices such as a 1.5U server or devices that are just 22.5 or 15cm in width, allowing for 2 or 3 such devices to be installed side by side, but these are much less common.
The height of a rack can vary from a few inches, such as in a broadcast console, to a floor mounted rack whose interior is 45 rack units (200.2 centimetres or 78.82 inches) high, with 42U being a common configuration. Many wall-mounted industrial equipment enclosures have 19-inch rack rails to support mounting of equipment.
Related standards
10-inch rack
Some telco/networking equipment is available in a narrower 10" format with the same unit-height as a standard 19"-rack.
11-foot frame
Frames for holding rotary-dial telephone equipment were generally 11 feet 6 inches (3.51 m) high. A series of studies led to the adoption of frames 7 feet (2.1 m) high, with modular widths in multiples of 1 foot 1 inch (0.33 m)—most often 2 feet 2 inches (0.66 m) wide.[21]
ETSI rack

The ETSI rack is defined by the European Telecommunications Standards Institute (ETS 300 119). The distance of the right edge of the right mounting rail to the left edge of the left mounting rail is 535 millimetres (21.1 in). As 535 mm is very close to 21 inches, these racks are sometimes called 21-inch racks. The gap between the posts is 500 millimetres (19.69 in). As 19-inch equipment has a maximum width of 17 1⁄4 inches (438.15 mm), they can easily be mounted in an ETSI rack by means of an ETSI bracket or adapter plate.
In contrast to the "19-inch world", ETSI also defined the size of the rack enclosure: the four allowed widths are 150, 300, 600, 900 millimetres (5.9, 11.8, 23.6, 35.4 in) and two allowed depths are 300 and 600 millimetres (12 and 24 in). Hole spacing is 25 millimetres (0.98 in).
23-inch rack
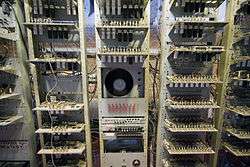
A 23-inch (580 mm) rack is used for housing telephone (primarily), computer, audio, and other equipment though is less common than the 19-inch rack. The size denotes the width of the faceplate for the installed equipment. The rack unit is a measure of vertical spacing and is common to both the 19 and 23 inch racks.
Hole spacing is either on 1-inch (25 mm) centers (Western Electric standard), or the same as for 19-inch (482.6 mm) racks (0.625 in or 15.9 mm spacing).
Open Rack
Open Rack is a mounting system designed by Facebook's Open Compute Project that has the same outside dimensions as typical 19-inch racks (e.g. 600 mm width), but supports wider equipment modules of 547 millimetres (21.5 in).[23]
Gallery
Pictures of 19 inch racks
- A server rack seen from the rear
- Wikimedia Foundation servers as seen from the front
- Wikimedia Foundation servers as seen from the rear
- Wikimedia Foundation servers as seen from the rear
See also
- Data center
- Horizontal pitch
- Rack unit
- Transit case, for rack cases
- Open Compute Project, wider, deeper rack design
References
- West, Jill; Dean, Tamara; Andrews, Jean (2015). "Structured Cabling and Networking Elements". Network+ Guide to Networks (Seventh ed.). Boston, MA: Engage Learning. p. 169. ISBN 9781305480865. Retrieved 9 December 2019.
Racks are measured in rack units (RU or U) with the industry standard being 42U tall — about 6 feet.
- Lowenthal, Max (February 2, 1899). "The New Exchange of the Central New York Telephone and Telegraph Co. at Syracuse, N.Y." The Electrical Engineer. XXVII (561): 142–147. Retrieved 9 December 2019.
- "New Electric Interlocking at Allentown, PA". The Signal Engineer. Vol. 4 no. 9. Chicago: The Railroad Gazette. September 1911. pp. 344–345. Retrieved 9 December 2019.
- Demarest, Charles S. (July 1923). "Telephone Equipment for Long Cable Circuits". Bell System Technical Journal. Vol. 2 no. 3. New York: American Telephone and Telegraph Company. p. 112–140. Retrieved 9 December 2019.
- Mezger, G. Robert (November 1934). "The Relay Rack in Amateur Construction". QST. American Radio Relay League. pp. 27–30.
- ANSI/EIA-310-D-1992
- The Computer Rack section of The University of Iowa's DEC PDP-8, documents a relay rack made in 1965; Nov. 2011.
- "Define: Rack Hole Types". server-racks.com.
- "What is a Versa Rail". server-racks.com.
- Telcordia GR-63-CORE, NEBS™ Requirements: Physical Protection
- "Telcordia GR-1502-CORE, Central Office/Network Environment Detail Engineering Generic Requirements". Archived from the original on 2011-07-16. Retrieved 2009-07-27.
- Seismic Enclosures Provide an Extra Measure of Protection
- William B. George, Chassis Slide Mechanism, U.S. Patent 3,092,429, granted June 4, 1963.
- Scott F. Herbert, Electronic Assembly Chassis Supporting Track, U.S. Patent 2,809,085, granted Oct. 8, 1957.
- https://www.apc.com/shop/th/en/products/NetShelter-SX-42U-600mm-Wide-x-1070mm-Deep-Enclosure-with-Sides-Black/P-AR3100
- "Telcordia GR-3108-CORE, NEBS™ Requirements for Telecommunications Data Center Equipment and Spaces". Archived from the original on 2009-08-28. Retrieved 2009-07-24.
- "Aluminum Relay Rack" (PDF). Bud Industries. Retrieved 2017-12-26.
- "Standard Rack Mount Cases". Anvil Case. Archived from the original on 2018-02-26. Retrieved 2017-12-26.
- "Data Center Cooling | Pentair". schroff.pentair.com. Retrieved 2017-08-27.
- "The Server Rack FAQ - Define EIA-310". server-racks.com.
- Keller, A. C. (January 1964). "Recent Developments in Bell System Relays — Particularly Sealed Contact and Miniature Relays". Bell Labs Technical Journal. 43: 15–44. doi:10.1002/j.1538-7305.1964.tb04057.x.
- The Manchester Baby : The First Stored Program Computer. Google. 2013.
- "Open Rack 1.0 Specification Available Now". Open Compute.