General Electric GE9X
The General Electric GE9X is a high-bypass turbofan developed by GE Aviation for the Boeing 777X. It first ran on ground in April 2016 and first flew on March 13, 2018; it powered the 777-9's maiden flight in early 2020. Derived from the General Electric GE90 with a larger fan, advanced materials like CMCs, higher bypass ratio and compression ratios, it should improve fuel efficiency by 10% over its predecessor. It is rated for 105,000 lbf (470 kN) of thrust.[3]
GE9X | |
---|---|
![]() | |
GE9X under the wing of the 777X during roll-out in March 2019 | |
Type | Turbofan |
National origin | United States |
Manufacturer | GE Aviation |
First run | April 2016 |
Major applications | Boeing 777X |
Program cost | Over $2 billion[1] |
Unit cost | US$41.4M list price (2016)[2] |
Developed from | General Electric GE90 |
Development
In February 2012, GE announced studies on a more efficient derivative, dubbed the GE9X, to power both the -8/9 variants of the new Boeing 777X. It was to feature the same 128 in (325 cm) fan diameter as the GE90-115B with thrust decreased by 15,800 lbf (70 kN) to a new rating of 99,500 lbf (443 kN) per engine.[4] The -8X engine was to be derated to 88,000 lbf (390 kN).[5]
In 2013, the diameter of the fan was increased by 3.5 in (9 cm) to 132 in (335 cm).[6] In 2014, thrust was increased slightly from 102,000 to 105,000 lbf (450 to 470 kN) and fan diameter to 133.5 in (339 cm).[7] The first engine was expected to be ground-tested in 2016, with flight testing to begin in 2017 and certification happening in 2018.[8] Because of the delays, the first flight test occurred in March 2018,[9] and the certification is expected to complete in late 2019.[10]
Ground testing
The first engine to test (FETT) completed its first test run in April 2016.[11] With 375 cycles and 335 test hours, validated its architecture (as a system, as opposed to a collection of modules) for aerodynamic performance, mechanical system verification and aerothermal heating validation.[12]
The GE9X went through icing tests in Winter 2017.[13] The FETT was finally used for 50 cold weather test points such as ground fog or natural icing conditions, minor modifications included tweaking parts using additive manufacturing for several pivots, used within a month; icing certification and evaluation will be finished in the 2017-2018 winter at Winnipeg, Manitoba.[12]
With testing completed to simulate high-altitude conditions, the GE9X should be free of ice crystal icing (core icing) which was an issue for the GEnx. This is now better understood as well as traditional rime ice. The improvements developed for the GEnx were the variable bypass valve doors: airflow is improved by the way they open inward into the flow path between the booster and high-pressure compressor, naturally ejecting the ice and sand to prevent them from entering the core.[12]
Minor tweaks between FETT and second engine to test (SETT) are pivotal to hit its efficiency goals: in the throat between the HP turbine outlet into the LP turbine inlet, the turbine's pinch point is altered to set the operating line of the compressor, turbine and 134.5 in (342 cm) fan. Blades at the back end of the 11-stage HP compressor are just over 1 in (25 mm) high. The HP compressor front end tip clearance was modified as the compressor was fine-tuned since initial tests in early 2013. The SETT seems to meet flow function and operability design points. Its testing started on May 16, 2017, at Peebles, Ohio, 13 months after FETT; it is the first to be built to the finalized production standard for certification.[12] During extreme test conditions for the FAA 150 hr block test, the variable stator vane (VSV) actuator lever arms failed and their redesign led to a 3–month delay.[14] It was joined by four more test engines by May 2018.[3]
The certification program began in May 2017.[13] Eight other test engines will be involved in the certification campaign, plus one for ETOPS certification configured with a Boeing nacelle. A core that will run in the Evendale, Ohio, altitude test cell for aeromechanical and vibratory testing and test engines 003, 004, and 007 are being assembled to be completed in 2017, with the fourth engine to be ground-tested in the third quarter before flying on the testbed later in the year from Victorville, California. From early 2018 eight compliance engines plus a pair of spares will be delivered for the four 777-9 flight-test aircraft.[12] Its type certification is planned for the fourth quarter of 2018.[15]
On November 10, 2017, it reached a record thrust of 134,300 lbf (597 kN) in Peebles, a new Guinness World Record breaking the GE90-115B 127,900 lbf (569 kN) record set in 2002.[16] By then, five engines had been test run.[17] The second engine will pass the FAA 150 hr block test at its operational limits, running at triple red-line conditions: maximum fan speed, maximum core speed, and maximum exhaust gas temperature. The third engine is in Peebles, while the fifth will travel to Winnipeg for icing tests starting by end of 2017 while three other engines are currently under assembly. The initial 777X flight-test engines will be shipped in 2018 for an initial 777-9 flight in early 2019.[18] A quarter of the certification testing was done by May 2018: icing, crosswind, inlet, fan and booster aeromechanics, HP turbine aeromechanics and thermal survey.[3]
Flight testing
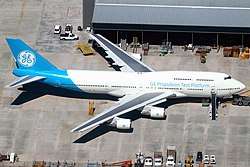
As it is larger than the GE90, for testing it fits only the 747-400 with larger main gear struts and bigger tires and not the previous -100 GE testbed, and the tested engine is tilted 5° more than the original CF6.[15] Boeing built a large, specially designed pylon for the testbed.[12] Suspended on a 19 ft (580 cm) strut, the fourth engine of the program has been mounted in November to begin flight testing at the end of 2017. The 134 in (340 cm) fan is encased in a 174 in (440 cm) nacelle, with 1.5 ft (0.46 m) of ground clearance.[18] It weighs 40,000 lb (18 t) with its custom pylon and wing strengthening, compared to 17,000 lb (7.7 t) for the CF6-80C2s and its pylon.[19]
In February 2018, the GE9X's first flight was delayed by problems discovered in the HPC variable stator vanes (VSV) lever arms. These are to be changed for the production engine, but will not affect its flow. Also a routine A Check discovered fan-case corrosion and HP turbine airfoils limits on the 747 testbed's CF6 engines.[20] It first flew on March 13 with the previous design of the VSV external lever arm.[9] In early May, the first flight test phase of two was wrapped up after 18 flights and 110 hours: after checking the aircraft and systems, the GE9X high-altitude envelope was explored and its cruise performance evaluated, the second phase is scheduled to begin in the third quarter.[3]
By October 2018, half of the certification was completed, and eight prototypes are used, mostly in Peebles, Ohio: #1 will be stored; the blade-out will be deliberately separated from the hub of #2 at takeoff power; after crosswind ground testing, #3 will be used for cyclic and load testing of the thrust reverser cascade assembly; the airborne #4 will explore more edges of the flight envelope like low altitudes for certification flight-tests from November through March; #5 will test unbalanced endurance to check vibration levels, before ETOPS certification; #6 will pass ingestion tests later in 2018; after LP turbine over-temperature tests, #7 will endure a second icing campaign in Winnipeg, Manitoba; #8 will be prepared by mid-October for the triple redline FAA 150 h endurance test. Eight compliance engines, plus two spares, are expected from November in Everett, Washington, to be installed on the first 777-9, to complete most of its flight tests in 2019 and enter service in 2020.[14]
A second phase, of 18 flights, began on 10 December to evaluate the software and hot-and-high performance until the first quarter of 2019 before its FAA certification the same year. By then, water ingestion, overheating and crosswinds tests were completed, before blade-out, hailstone, bird ingestion and block or endurance testing. Flight tests are based in Victorville, California, and stretch to Seattle, Colorado Springs, Colorado, Fairbanks, Alaska, and Yuma, Arizona.[21]
By 4 January 2019, eight test flights and 55h of run time were completed.[22] At the end of January, the case and rear turbine frame strut were damaged during the blade out test and affected components are revised. In early May, the flight test campaign was completed after 320 hours, focused on high-altitude cruise fuel burn. A compressor anomaly was detected in an engine pre-delivery test while the first engines were installed on the 777X prototype. The engines should be modified to a final certifiable configuration standard before the maiden flight, delayed after the previously expected June 26. The issue is mechanical and not aerodynamic, not affecting performance or engine configuration, and is at the front of the 11-stage high-pressure compressor. Before certification, final tests include a full durability block test, replacing the usual "triple redline" test at maximum temperatures, pressures and speeds, as modern high-bypass ratio engines cannot achieve all maximum conditions near sea level.[23] The high-pressure compressor stator redesign is likely to push engine certification into autumn, delaying the 777X first flight until 2020.[10]
On January 25, 2020, the GE9X had its first flight on the 777X, flying for 3 hours and 52 minutes, before landing at Boeing Field.
Design
The GE9X should increase fuel efficiency by 10% over the GE90.[4] Its 61:1 overall pressure ratio should help provide a 5% lower thrust specific fuel consumption (TSFC) than the XWB-97 with maintenance costs comparable to the GE90-115B.[8] The initial thrust of 105,000 lbf (470 kN) will be followed by 102,000 and 93,000 lbf (450 and 410 kN) derated variants.[3] GE invested more than $2 billion for its development. Its nacelle is 184 in (4,700 mm) wide.[1]
Most efficiency increase comes from the better propulsion efficiency of the higher-bypass-ratio fan.[14] The bypass ratio is planned for 10:1.[5] The fan diameter is 134 in (340 cm).[24] It has only 16 blades, whereas the GE90 has 22 and the GEnx has 18. This makes the engine lighter, and allows the low pressure (LP) fan and booster to spin faster to better match its speed with the LP turbine. The fan blades feature steel leading edges and glass-fibre trailing edges to better absorb bird impacts with more flexibility than carbon fiber.[2] Fourth generation carbon fiber composite materials, comprising the bulk of the fan blades, make them lighter, thinner, stronger, and more efficient.[25] Using a composite fan case will also reduce weight.[26]
The high pressure (HP) compressor is up to 2% more efficient.[14] As the 129.5 in (329 cm) GE90 fan left little room to improve the bypass ratio, GE looked for additional efficiency by upping the overall pressure ratio from 40 to 60, focusing on boosting the high-pressure core's ratio from 19:1 to 27:1 by using 11 compressor stages instead of 9 or 10, and a third-generation, twin-annular pre-swirl (TAPS) combustor instead of the previous dual annular combustor. Able to endure hotter temperatures, ceramic matrix composites (CMC) are used in two combustor liners, two nozzles, and the shroud up from the CFM International LEAP stage 2 turbine shroud. CMCs are not used for the first-stage turbine blades, which have to endure extreme heat and centrifugal forces. These are improvements planned for the next iteration of engine technology.[27]
The first-stage HP turbine shroud, the first- and second-stage HP turbine nozzles and the inner and outer combustor linings are made from CMCs, only static components, operating 500 °F (260 °C) hotter than nickel alloys with some cooling.[14] CMCs have twice the strength and one-third the weight of metal. The compressor is designed with 3D aerodynamics and its first five stages are blisks, combined bladed-disk. The combustor is lean burning for greater efficiency and 30% NOx margin to CAEP/8. The compressor and high pressure turbine are made from powdered metal. The low-pressure turbine airfoils made of titanium aluminide (TiAl) are stronger, lighter, and more durable than nickel-based parts.[24] 3D printing is used to manufacture parts that would otherwise be impossible to make using traditional manufacturing processes.[25] CMCs need 20% less cooling.[8]
Specifications
Variant | 105B1A |
---|---|
Application | 777-9/777-8 (future) |
Type | Dual rotor, axial flow, high bypass turbofan |
Compressor | 1 fan, 3-stage LP, 11-stage HP |
Turbine | 2-stage HP, 6-stage LP |
Fan diameter | 134 in (340 cm) |
Takeoff thrust | 105,000 lbf (470 kN) |
Bypass ratio | 10:1 |
Overall pressure ratio | 60:1 |
Weight | 40,000 lb (18 t), complete with test pylon[19] |
See also
Related development
Comparable engines
- Rolls-Royce Trent XWB
- Rolls-Royce Advance (Future)
Related lists
References
- Dominic Gates (January 4, 2019). "The biggest jet engines ever seen are set to roar on Boeing's 777X". Seattle Times.
- "The Art Of Engineering: The World's Largest Jet Engine Shows Off Composite Curves". GE reports. General Electric Company. April 28, 2016.
- Stephen Trimble (May 29, 2018). "GE9X completes first phase of flight testing". Flightglobal.
- Jon Ostrower (14 September 2011). "Next generation 777 comes into focus". Flight Global. Reed Business Information.
- "GE plans 10% fuel burn improvement for GE9X engine". Flightglobal. March 7, 2012.
- Alcock, Charles (June 16, 2013). "GE Pushes Envelope With GE9X for new Boeing 777". Aviation International News. Retrieved November 24, 2018.
- "777X Configuration Changes Revealed". Aviation Week. June 9, 2014.
- Scott Fancher, Randy Tinseth, Bill Fitzgerald (November 18, 2013). "777X Overview" (PDF). Boeing Commercial Airplanes, GE Aviation.CS1 maint: multiple names: authors list (link)
- Stephen Trimble (15 March 2018). "GE9X enters flight test phase". Flightglobal.
- Hemmerdinger, Jon (24 July 2019). "GE9X engine issue pushes 777X first flight to 2020". Flightglobal.
- "Start your engines…First full GE9X engine begins testing" (Press release). GE Aviation. April 11, 2016.
- Norris, Guy (May 18, 2017). "GE Testing For Boeing 777X Engine Moves Into High Gear". Aviation Week & Space Technology.
- GE9X: The world’s biggest fan of ice. YouTube. GE Aviation. May 15, 2017.
- Norris, Guy (October 9, 2018). "GE9X For Boeing 777X Delivered For Final Flying Testbed Certification". Aviation Week & Space Technology.
- Norris, Guy (May 20, 2016). "Preparing To Test The World's Largest Engine". Aviation Week & Space Technology.
- "GE9X Breaks GUINNESS WORLD RECORDS™ Title for Thrust" (Press release). GE Aviation. July 12, 2019.
- Stephen Trimble (November 12, 2017). "Boeing achieves 90% drawing milestone on 777-9". Flightglobal.
- Norris, Guy (November 27, 2017). "World's Largest Engine Readied For Flight". Aviation Week Network.
- "GE Ramps Up For GE9X Flight Certification Tests". Aviation Week & Space Technology. October 9, 2018.
- Norris, Guy (February 2, 2018). "Boeing 777X Engine Flight Test Facing Delay". Aviation Week & Space Technology.
- Jon Hemmerdinger (11 December 2018). "GE begins second round of GE9X flight testing". Flightglobal.
- Jon Hemmerdinger (7 January 2019). "Boeing installs GE9X engines on 777X test aircraft". Flightglobal.
- Guy Norris (June 6, 2019). "GE9X Engine Anomaly Likely To Delay Boeing 777X First Flight". Aviation Week Network.
- "GE9X Commercial Aircraft Engine". GE Aviation.
- GE Aviation (July 13, 2014). See inside the GE9X, GE's newest game-changer. YouTube.
- "GE Fans Out on Testing of New GE9X Fan Blades" (Press release). GE Aviation. August 21, 2013.
- Stephen Trimble (30 May 2017). "After six years, 777X engine starts certification tests". Flightglobal.
Notes
External links
![]() |
Wikimedia Commons has media related to General Electric GE9X. |
- Official website
- GE9X Press
- "In Pictures: Flight-Testing The GE9X, The World's Largest Engine". Aviation Week Network. June 14, 2019.