Warp knitting
Warp knitting is a family of knitting methods in which the yarn zigzags along the length of the fabric; i.e., following adjacent columns, or wales, of knitting, rather than a single row, or course. For comparison, knitting across the width of the fabric is called weft knitting.
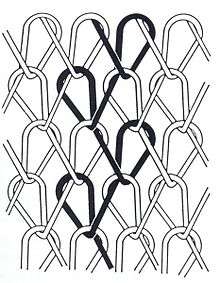
Since warp knitting requires that the number of separate strands of yarn, or ends, equals the number of stitches in a row, warp knitting is almost always done by machine rather than by hand.
History
Credit for the invention is usually given to a mechanic called Josiah Crane in 1775. He likely sold his invention to Richard March who patented (No. 1186) a warp frame in 1778. In the intervening three years March likely had discussed the device with Morris who submitted a similar patent (No.1282) for a twisting machine for making Brussels point lace. These early machines were modifications of the stocking frame with an additional warp beam.[1]
In 1795, the machine was successfully used to make lacey fabrics.[2] Warp frames could be used with any thread, and the warps provided a fixed anchor for the transverse threads. In 1786, Flint invented the point bar which kept the threads at a fixed distance. In 1796, Dawson introduced cams to move the bars, and regulate the twist. Brown and Copstake succeeded in imitating Mechlen net. Lindley invented the bobbin in 1799, and Irving and Skelton the regulator spring. In 1802, Robert Brown of New Radford patented the first twist-frame, a knitter that could produce wide net.
Whittaker's frame of 1804 had half its thread mounted on a warp beam and half wound on bobbins mounted on a carriage.[3]
Heathcote's 1808 improvement of Whittaker's frame was essentially a warp knitting frame. The bobbin carrying beam was reduced to the same size as the machine- he called it a bobbinet.[3] Heathcote's second patent, in 1809, was for a bobbinet that could produce wide fabrics; this was the Old Loughborough.[4]
Types
Warp knitting comprises several types of knitted fabrics. All warp-knit fabrics are resistant to runs and relatively easy to sew. Raschel lace (a common type of machine made lace) is a warp knit fabric but using many more guide-bars (12+) than the usual machines which mostly have three or four bars.
Tricot
Tricot is very common in lingerie. The right side of the fabric has fine lengthwise ribs while the reverse has crosswise ribs.[5] The properties of these fabrics include having a soft and 'drapey' texture with some lengthwise stretch and almost no crosswise stretch.[5]
Milanese knit
Milanese is stronger, more stable, smoother and more expensive than tricot and, hence, is used in better lingerie. These knit fabrics are made from two sets of yarn knitted diagonally, which results in the face fabric having a fine vertical rib and the reverse having a diagonal structure, and results in these fabrics being lightweight, smooth, and run-resistant.[5] Milanese is now virtually obsolete.
Raschel knit
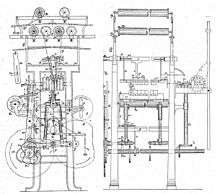
In 1855, Redgate combined the principles of a circular loom with those of warp knit. A German firm used this machine to produce "Raschel" shawls, named after the French actress Élisabeth Félice Rachel. In 1859 Wilhelm Barfuss improved the machine to create the Raschel machines.[6] The Jacquard apparatus was adapted to it in the 1870s. The Raschel machine could work at higher speeds than the Leavers machine and proved the most adaptable to the new synthetic fibres, such as nylon and polyester, in the 1950s. Most contemporary machine-made lace is made on Raschel machines.[7]
Raschel knits do not stretch significantly and are often bulky; consequently, they are often used as an unlined material for coats, jackets, straight skirts and dresses. These fabrics can be made out of conventional or novelty yarns which allows for interesting textures and designs to be created.[5] The qualities of these fabrics range from "dense and compact to open and lofty [and] can be either stable or stretchy, and single-faced or reversible.[5] The largest outlet for the Raschel warp knitting machine is for lace fabric and trimmings. Raschel knitting is also used in outdoors and military fabrics for products such as backpacks. It is used to provide a ventilated mesh next to the user's body (covering padding) or mesh pockets and pouches to facilitate visibility of the contents (MIL-C-8061).
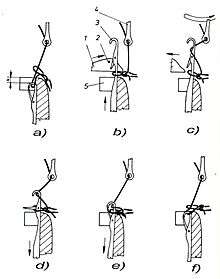
- Golden lace
- Lace appliqué
- Raschel lace
Stitch-bonding
Stitch-bonding is a special form of warp knitting[8] and is commonly used for the production of composite materials and technical textiles. As a method of production, stitch-bonding is efficient, and is one of the most modern ways to create reinforced textiles and composite materials [9] for industrial use. The advantages of the stitch-bonding process include its high productivity rate and the scope it offers for functional design of textiles, such as fiber-reinforced plastics.[9] Stitch-bonding involves layers of threads and fabric being joined together with a knitting thread, which creates a layered structure called a multi-ply.[10] This is created through a warp-knitting thread system, which is fixed on the reverse side of the fabric with a sinker loop, and a weft thread layer.[9] A needle with the warp thread passes through the material, which requires the warp and knitting threads to be moving both parallel and perpendicular to the vertical/warp direction of the stitch-bonding machine.[10] Stitch-bonded fabrics are currently being used in such fields as wind energy generation and aviation.[9] Research is currently being conducted into the usage and benefits of stitch-bonded fabrics as a way to reinforce concrete. Fabrics produced with this process offer the potential of using "sensitive fiber materials such as glass and carbon with only little damage, non-crimp fiber orientation and variable distance between threads".[9]
In the extended stitch-bonding process (or the extended warp-knitting process), the compound needle that pierces the piles is shifted laterally according to the yarn guides.[8] This then makes it possible for the layers of the stitch-bonded fabric to be arranged freely and be made symmetrical in one working step.[8] This process is advantageous to the characteristics of the composite as the "residual stresses resulting from asymmetric alignment of the layers are avoided, [while] the tensile strength and the impact strength of the composite are improved."[11]
Needle shift
Needle shift technique is when “Both outer warp layers [are] secured in one procedure by incorporating a shift of the needle bar during the stitching process, creating endless possibilities for the arrangement and patterns in the stitch-bonding process.[8]
Advantages
Producing textiles through the warp knitting process has the following advantages:[12]
- higher productivity rates than weaving
- variety of fabric constructions
- large working widths
- low stress rate on the yarn that allows for use of fibers such as glass, aramid and carbon
- the creation of three-dimensional structures that can be knitted on double needle bar raschels
Applications
Warp knitted fabrics have several industrial uses, including producing mosquito netting, tulle fabrics, sports wear, shoe fabric, fabrics for printing and advertising, coating substrates and laminating backgrounds.[13]
Research is also being conducted into the use of warp knitted fabrics for industrial applications (for example, to reinforce concrete), and for the production of biotextiles.
Warp knitting and biotextiles
The warp knitting process is also being used to create biotextiles. For example, a warp knitted polyester cardiac support device has been created to attempt to limit the growth of diseased hearts by being installed tightly around the diseased heart. Current research on animals "have confirmed that … the implantation of the device reverses the disease state, which makes this an alternative innovative therapy for patients who have side effects from traditional drug remedies".[14]
References
- Notes
- Earnshaw 1986, p. 30.
- Rosatto 1948, p. 9.
- Rosatto 1948, p. 10.
- Rosatto 1948, p. 11.
- Sarah Veblen, "Samplings of Weft and Warp Knit Fabrics", Threads Issue #97, 2012
- Silva, Marcos (2008). MALHARIA - BASES DE FUNDAMENTAÇÃO. Universidade Federal do Rio Grande do Norte. p. 2. Retrieved 22 December 2014.
- Farrell 2007.
- J.Hausding and C.Cherif, "Improvements in the warp-knitting process and new patterning techniques for stitch-bonded textiles", Journal of the Textile Institute, 2012
- Hausding, Jan, Lorenz, Enrico, Ortlepp, Regine, Lundahl, Anna. Application of stitch-bonded multi-plies made by using the extended warp knitting process: reinforcements with symmetrical layer arrangement for concrete. Journal of the Textile Institute, 2011, p. 1.
- Gokarneshan, N., Varadarajan, B., Sentil kumar, CB., Balamurugan, K. and Rachel, A. Engineering knits for versatile technical applications: Some insights on recent researches. Journal of the Textile Institute, 2011, p. 68.
- Hausding, J. Widulle, C., Paul, C., Cherif, C., "Manufacturing method for symmetric laminates for improves stitch bonded multi-plies"], 13th European Conference on Composite Materials", June 2008
- Kiron, M.M.I, http://textilelearner.blogspot.ca/2011/05/defination-and-properties-of-warp_8342.html, "Introduction of Warp Knitting|Principle of Warp Knitting|Properties of Warp Knitted Structures",
- http://www.warpknitting4u.com/, 2011
- R.D. Sumanasinghe and M.W. King, "New Trends in Biotextiles-The Challenge of Tissue Engineering", The Journal of Textile and Apparel, Technology and Management, 2003
- Bibliography
- Earnshaw, Pat (1986). Lace Machines and Machine Laces. Batsford. ISBN 978-0713446845.
- Farrell, Jeremy (2007). "Identifying Handmade and Machine Lace" (PDF). DATS (Dress and Textile Specialists) in partnership with the V&A.
- Cooper, B., (1983) Transformation of a Valley: The Derbyshire Derwent, Heinneman, republished 1991 Cromford: Scarthin Books, ISBN 0907758177
- Rosatto, Vittoria (1948). Leavers Lace:A Handbook of the American Leavers Lace Industry (PDF). Providence, RI: American Lace Manufacturers Association. Retrieved 8 December 2016.
- Shaeffer, Claire (1989). Claire Shaeffer's fabric sewing guide (Updated ed.). Radnor, Pa.: Chilton Book Co. ISBN 978-0-8019-7802-9.
External links
![]() |
Wikimedia Commons has media related to |