Compressor
A compressor is a mechanical device that increases the pressure of a gas by reducing its volume. An air compressor is a specific type of gas compressor.
Compressors are similar to pumps: both increase the pressure on a fluid and both can transport the fluid through a pipe. As gases are compressible, the compressor also reduces the volume of a gas. Liquids are relatively incompressible; while some can be compressed, the main action of a pump is to pressurize and transport liquids.
Many compressors can be staged, that is, the fluid is compressed several times in steps or stages, to increase discharge pressure. Often, the second stage is physically smaller than the primary stage, to accommodate the already compressed gas. Each stage further compresses the gas and increases pressure. Those that are powered by an electric motor can also be controlled using a VFD or power inverter, however many (hermetic and semi-hermetic) compressors can only work at certain speeds, since they may include built-in oil pumps. The oil pumps are connected to the same shaft that drives the compressor and forces oil into the compressor and motor bearings. At low speeds, insufficient quantities or no oil is forced into the bearings, eventually leading to bearing failure, while at high speeds, excessive amounts of oil may be lost from the bearings and compressor and potentially into the discharge line due to splashing. Eventually the oil runs out and the bearings are left unlubricated, again leading to failure, and the oil may contaminate the refrigerant, air or other working gas. [1]
Types
The main and important types of gas compressors are illustrated and discussed below:

Positive displacement
A positive displacement compressor is the system which compresses the air by the displacement of a mechanical linkage reducing the volume (since the reduction in volume due to a piston in thermodynamics is considered as positive displacement of the piston).
Put another way, a positive displacement compressor is one which operates by drawing in a discrete volume of gas from its inlet then forcing that gas to exit via the compressor's outlet. The increase in the pressure of the gas is due, at least in part, to the compressor pumping it at a mass flow rate which cannot pass through the outlet at the lower pressure and density of the inlet.
Reciprocating compressors

Reciprocating compressors use pistons driven by a crankshaft. They can be either stationary or portable, can be single or multi-staged, and can be driven by electric motors or internal combustion engines.[2][3][4] Small reciprocating compressors from 5 to 30 horsepower (hp) are commonly seen in automotive applications and are typically for intermittent duty. Larger reciprocating compressors well over 1,000 hp (750 kW) are commonly found in large industrial and petroleum applications. Discharge pressures can range from low pressure to very high pressure (>18000 psi or 180 MPa). In certain applications, such as air compression, multi-stage double-acting compressors are said to be the most efficient compressors available, and are typically larger, and more costly than comparable rotary units.[5] Another type of reciprocating compressor, usually employed in automotive cabin air conditioning systems, is the swash plate or wobble plate compressor, which uses pistons moved by a swash plate mounted on a shaft (see axial piston pump).
Household, home workshop, and smaller job site compressors are typically reciprocating compressors 1½ hp or less with an attached receiver tank.
A linear compressor is a reciprocating compressor with the piston being the rotor of a linear motor.
This type of compressor can compress a wide range of gases, including refrigerant, hydrogen, and natural gas. Because of this, it finds use in a wide range of applications in many different industries and can be designed to a wide range of capacities, by varying size, number of cylinders, and cylinder unloading. However, it suffers from higher losses due to clearance volumes, resistance due to discharge and suction valves, weighs more, is difficult to maintain due to having a large number of moving parts, and it has inherent vibration. [6]
Ionic liquid piston compressor
An ionic liquid piston compressor, ionic compressor or ionic liquid piston pump is a hydrogen compressor based on an ionic liquid piston instead of a metal piston as in a piston-metal diaphragm compressor.[7]
Rotary screw compressors

Rotary screw compressors use two meshed rotating positive-displacement helical screws to force the gas into a smaller space.[2][8][9] These are usually used for continuous operation in commercial and industrial applications and may be either stationary or portable. Their application can be from 3 horsepower (2.2 kW) to over 1,200 horsepower (890 kW) and from low pressure to moderately high pressure (>1,200 psi or 8.3 MPa).
The classifications of rotary screw compressors vary based on stages, cooling methods, and drive types among others.[10] Rotary screw compressors are commercially produced in Oil Flooded, Water Flooded and Dry type. The efficiency of rotary compressors depends on the air drier, and the selection of air drier is always 1.5 times volumetric delivery of the compressor.[11]
Designs with a single screw[12] or three screws[13] instead of two exist.
Screw compressors have less components and a simpler structure, larger capacity, higher efficiency, less vibration and surging, can operate at lower speeds for capacity adjustment, but small sizes are impractical due to inherent leaks between the compression cavities and the casing of the compressor. [6]
Rotary vane compressors
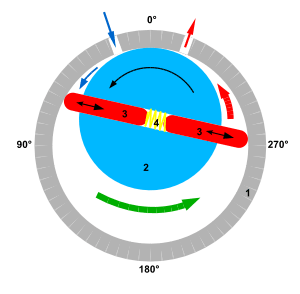
Rotary vane compressors consist of a rotor with a number of blades inserted in radial slots in the rotor. The rotor is mounted offset in a larger housing that is either circular or a more complex shape. As the rotor turns, blades slide in and out of the slots keeping contact with the outer wall of the housing.[2] Thus, a series of increasing and decreasing volumes is created by the rotating blades. Rotary Vane compressors are, with piston compressors one of the oldest of compressor technologies.
With suitable port connections, the devices may be either a compressor or a vacuum pump. They can be either stationary or portable, can be single or multi-staged, and can be driven by electric motors or internal combustion engines. Dry vane machines are used at relatively low pressures (e.g., 2 bar or 200 kPa or 29 psi) for bulk material movement while oil-injected machines have the necessary volumetric efficiency to achieve pressures up to about 13 bar (1,300 kPa; 190 psi) in a single stage. A rotary vane compressor is well suited to electric motor drive and is significantly quieter in operation than the equivalent piston compressor.
Rotary vane compressors can have mechanical efficiencies of about 90%.[14]
Rolling piston

The Rolling piston in a rolling piston style compressor plays the part of a partition between the vane and the rotor.[15] Rolling piston forces gas against a stationary vane.
2 of these compressors can be mounted on the same shaft to increase capacity and reduce vibration and noise.[16] A design without a spring is known as a swing compressor.[17]
In refrigeration and air conditioning, this type of compressor is also known as a rotary compressor, with rotary screw compressors being also known simply as screw compressors.
It offers higher efficiency than reciprocating compressors due to less losses from the clearance volume between the piston and the compressor casing, its 40% to 50% smaller and lighter for a given capacity (which can impact material and shipping costs when used in a product), causes less vibration, has fewer components and is more reliable than a reciprocating compressor. But its structure does not allow capacities beyond 5 refrigeration tons, is less reliable than other compressor types, and is less efficient than other compressor types due to losses from the clearance volume. [6]
Scroll compressors
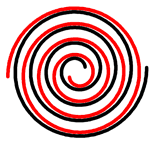
A scroll compressor, also known as scroll pump and scroll vacuum pump, uses two interleaved spiral-like vanes to pump or compress fluids such as liquids and gases. The vane geometry may be involute, archimedean spiral, or hybrid curves.[18][19][20] They operate more smoothly, quietly, and reliably than other types of compressors in the lower volume range.
Often, one of the scrolls is fixed, while the other orbits eccentrically without rotating, thereby trapping and pumping or compressing pockets of fluid between the scrolls.
Due to minimum clearance volume between the fixed scroll and the orbiting scroll, these compressors have a very high volumetric efficiency.
These compressors are extensively used in air conditioning and refrigeration because they are lighter, smaller and have fewer moving parts than reciprocating compressors and they are also more reliable. They are more expensive though, so peltier coolers or rotary and reciprocating compressors may be used in applications where cost is the most important or one of the most important factors to consider when designing a refrigeration or air conditioning system.
This type of compressor was used as the supercharger on Volkswagen G60 and G40 engines in the early 1990s.
When compared with reciprocating and rolling piston compressors, scroll compressors are more reliable since they have fewer components and have a simpler structure, is more efficient since they have no clearance volume nor valves, has less surging and it doesn't vibrate as much. But, when compared with screw and centrifugal compressors, scroll compressors have lower efficiencies and smaller capacities. [6]
Diaphragm compressors
A diaphragm compressor (also known as a membrane compressor) is a variant of the conventional reciprocating compressor. The compression of gas occurs by the movement of a flexible membrane, instead of an intake element. The back and forth movement of the membrane is driven by a rod and a crankshaft mechanism. Only the membrane and the compressor box come in contact with the gas being compressed.[2]
The degree of flexing and the material constituting the diaphragm affects the maintenance life of the equipment. Generally stiff metal diaphragms may only displace a few cubic centimeters of volume because the metal can not endure large degrees of flexing without cracking, but the stiffness of a metal diaphragm allows it to pump at high pressures. Rubber or silicone diaphragms are capable of enduring deep pumping strokes of very high flexion, but their low strength limits their use to low-pressure applications, and they need to be replaced as plastic embrittlement occurs.
Diaphragm compressors are used for hydrogen and compressed natural gas (CNG) as well as in a number of other applications.

The photograph on the right depicts a three-stage diaphragm compressor used to compress hydrogen gas to 6,000 psi (41 MPa) for use in a prototype compressed hydrogen and compressed natural gas (CNG) fueling station built in downtown Phoenix, Arizona by the Arizona Public Service company (an electric utilities company). Reciprocating compressors were used to compress the natural gas. The reciprocating natural gas compressor was developed by Sertco.[21]
The prototype alternative fueling station was built in compliance with all of the prevailing safety, environmental and building codes in Phoenix to demonstrate that such fueling stations could be built in urban areas.
Dynamic
Air bubble compressor
Also known as a trompe. A mixture of air and water generated through turbulence is allowed to fall into a subterranean chamber where the air separates from the water. The weight of falling water compresses the air in the top of the chamber. A submerged outlet from the chamber allows water to flow to the surface at a lower height than the intake. An outlet in the roof of the chamber supplies the compressed air to the surface. A facility on this principle was built on the Montreal River at Ragged Shutes near Cobalt, Ontario in 1910 and supplied 5,000 horsepower to nearby mines.[22]
Centrifugal compressors
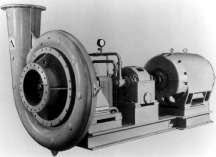

Centrifugal compressors use a rotating disk or impeller in a shaped housing to force the gas to the rim of the impeller, increasing the velocity of the gas. A diffuser (divergent duct) section converts the velocity energy to pressure energy. They are primarily used for continuous, stationary service in industries such as oil refineries, chemical and petrochemical plants and natural gas processing plants.[2][23][24] Their application can be from 100 horsepower (75 kW) to thousands of horsepower. With multiple staging, they can achieve high output pressures greater than 1,000 psi (6.9 MPa).
This type of compressor, along with screw compressors, are extensively used in large refrigeration and air conditioning systems. Magnetic bearing (magnetically levitated) and air bearing centrifugal compressors exist.
Many large snowmaking operations (like ski resorts) use this type of compressor. They are also used in internal combustion engines as superchargers and turbochargers. Centrifugal compressors are used in small gas turbine engines or as the final compression stage of medium-sized gas turbines.
Centrifugal compressors are the largest available compressors, offer higher efficiencies under partial loads, may be oil-free when using air or magnetic bearings which increases the heat transfer coefficient in evaporators and condensers, weigh up to 90% less and occupy 50% less space than reciprocating compressors, are reliable and cost less to mantain since less components are exposed to wear, and only generate minimal vibration. But, their initial cost is higher, require highly precise CNC machining, the impeller needs to rotate at high speeds making small compressors impractical, and surging becomes more likely. [6] Surging is gas flow reversal, meaning that the gas goes from the discharge to the suction side, which can cause serious damage, specially in the compressor bearings and its drive shaft. It is caused by a pressure on the discharge side that is higher than the output pressure of the compressor. This can cause gases to flow back and forth between the compressor and whatever is connected to its discharge line, causing oscillations. [6]
Diagonal or mixed-flow compressors
Diagonal or mixed-flow compressors are similar to centrifugal compressors, but have a radial and axial velocity component at the exit from the rotor. The diffuser is often used to turn diagonal flow to an axial rather than radial direction.[25] Comparative to the conventional centrifugal compressor (of the same stage pressure ratio), the value of the speed of the mixed flow compressor is 1.5 times larger.[26]
Axial compressors
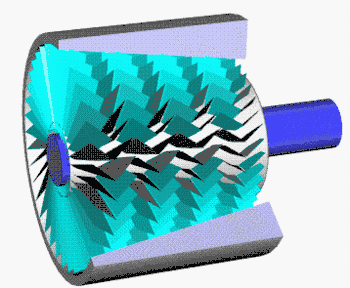
Axial compressors are dynamic rotating compressors that use arrays of fan-like airfoils to progressively compress a fluid. They are used where high flow rates or a compact design are required.
The arrays of airfoils are set in rows, usually as pairs: one rotating and one stationary. The rotating airfoils, also known as blades or rotors, accelerate the fluid. The stationary airfoils, also known as stators or vanes, decelerate and redirect the flow direction of the fluid, preparing it for the rotor blades of the next stage.[2] Axial compressors are almost always multi-staged, with the cross-sectional area of the gas passage diminishing along the compressor to maintain an optimum axial Mach number. Beyond about 5 stages or a 4:1 design pressure ratio a compressor will not function unless fitted with features such as stationary vanes with variable angles (known as variable inlet guide vanes and variable stators), the ability to allow some air to escape part-way along the compressor (known as interstage bleed) and being split into more than one rotating assembly (known as twin spools, for example).
Axial compressors can have high efficiencies; around 90% polytropic at their design conditions. However, they are relatively expensive, requiring a large number of components, tight tolerances and high quality materials. Axial compressors are used in medium to large gas turbine engines, natural gas pumping stations, and some chemical plants.
Hermetically sealed, open, or semi-hermetic
Compressors used in refrigeration systems are often described as being either hermetic, open, or semi-hermetic, to describe how the compressor and motor drive are situated in relation to the gas or vapor being compressed. The industry name for a hermetic is hermetically sealed compressor, while a semi-hermetic is commonly called a semi-hermetic compressor.
In hermetic and most semi-hermetic compressors, the compressor and motor driving the compressor are integrated, and operate within the pressurized gas envelope of the system. The motor is designed to operate in, and be cooled by, the refrigerant gas being compressed.
The difference between the hermetic and semi-hermetic, is that the hermetic uses a one-piece welded steel casing that cannot be opened for repair; if the hermetic fails it is simply replaced with an entire new unit. A semi-hermetic uses a large cast metal shell with gasketed covers with screws that can be opened to replace motor and compressor components.
The primary advantage of a hermetic and semi-hermetic is that there is no route for the gas to leak out of the system. Open compressors rely on shaft seals to retain the internal pressure, and these seals require a lubricant such as oil to retain their sealing properties.
An open pressurized system such as an automobile air conditioner can be more susceptible to leak its operating gases. Open systems rely on lubricant in the system to splash on pump components and seals. If it is not operated frequently enough, the lubricant on the seals slowly evaporates, and then the seals begin to leak until the system is no longer functional and must be recharged. By comparison, a hermetic or semi-hermetic system can sit unused for years, and can usually be started up again at any time without requiring maintenance or experiencing any loss of system pressure.
The disadvantage of hermetic compressors is that the motor drive cannot be repaired or maintained, and the entire compressor must be replaced if a motor fails. A further disadvantage is that burnt-out windings can contaminate whole systems, thereby requiring the system to be entirely pumped down and the gas replaced (This can also happen in semi hermetic compressors where the motor operates in the refrigerant). Typically, hermetic compressors are used in low-cost factory-assembled consumer goods where the cost of repair and labor is high compared to the value of the device, and it would be more economical to just purchase a new device or compressor. Semi-hermetic compressors are used in mid-sized to large refrigeration and air conditioning systems, where it is cheaper to repair the compressor rather than buying and installing a new one. A hermetic compressor is simpler and cheaper to build than a semi-hermetic compressor.
An advantage of open compressors is that they can be driven by non-electric power sources, such as an internal combustion engine or turbine. However, open compressors that drive refrigeration systems are generally not totally maintenance-free throughout the life of the system, since some gas leakage will occur over time.
Thermodynamics of gas compression
Isentropic compressor
A compressor can be idealized as internally reversible and adiabatic, thus an isentropic steady state device, meaning the change in entropy is 0.[27] By defining the compression cycle as isentropic, an ideal efficiency for the process can be attained, and the ideal compressor performance can be compared to the actual performance of the machine. Isotropic Compression as used in ASME PTC 10 Code refers to a reversible, adiabatic compression process[28]
Isentropic efficiency of Compressors:
Minimizing work required by a compressor
Comparing reversible to irreversible compressors
Comparison of the differential form of the energy balance for each device
Let be heat, be work, be kinetic energy and be potential energy.
Actual Compressor:
Reversible Compressor:
The right hand side of each compressor type is equivalent, thus:
re-arranging:
By substituting the know equation into the last equation and dividing both terms by T:
Furthermore, and T is [absolute temperature] () which produces:
or
Therefore, work-consuming devices such as pumps and compressors (work is negative) require less work when they operate reversibly.[27]
Effect of cooling during the compression process
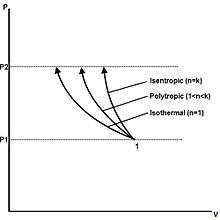
isentropic process: involves no cooling,
polytropic process: involves some cooling
isothermal process: involves maximum cooling
By making the following assumptions the required work for the compressor to compress a gas from to is the following for each process:
Assumptions:
- and
- All processes are internally reversible
- The gas behaves like an ideal gas with constant specific heats
Isentropic (, where ):
Polytropic ():
Isothermal ( or ):
By comparing the three internally reversible processes compressing an ideal gas from to , the results show that isentropic compression () requires the most work in and the isothermal compression( or ) requires the least amount of work in. For the polytropic process () work in decreases as the exponent, n, decreases, by increasing the heat rejection during the compression process. One common way of cooling the gas during compression is to use cooling jackets around the casing of the compressor.[27]
Compressors in ideal thermodynamic cycles
Ideal Rankine Cycle 1->2 Isentropic compression in a pump
Ideal Carnot Cycle 4->1 Isentropic compression
Ideal Otto Cycle 1->2 Isentropic compression
Ideal Diesel Cycle 1->2 Isentropic compression
Ideal Brayton Cycle 1->2 Isentropic compression in a compressor
Ideal Vapor-compression refrigeration Cycle 1->2 Isentropic compression in a compressor
NOTE: The isentropic assumptions are only applicable with ideal cycles. Real world cycles have inherent losses due to inefficient compressors and turbines. The real world system are not truly isentropic but are rather idealized as isentropic for calculation purposes.
Temperature
Compression of a gas increases its temperature.
where
or
and
so
in which p is pressure, V is volume, n takes different values for different compression processes (see below), and 1 & 2 refer to initial and final states.
- Adiabatic - This model assumes that no energy (heat) is transferred to or from the gas during the compression, and all supplied work is added to the internal energy of the gas, resulting in increases of temperature and pressure. Theoretical temperature rise is:[29]
with T1 and T2 in degrees Rankine or kelvins, p2 and p1 being absolute pressures and ratio of specific heats (approximately 1.4 for air). The rise in air and temperature ratio means compression does not follow a simple pressure to volume ratio. This is less efficient, but quick. Adiabatic compression or expansion more closely model real life when a compressor has good insulation, a large gas volume, or a short time scale (i.e., a high power level). In practice there will always be a certain amount of heat flow out of the compressed gas. Thus, making a perfect adiabatic compressor would require perfect heat insulation of all parts of the machine. For example, even a bicycle tire pump's metal tube becomes hot as you compress the air to fill a tire. The relation between temperature and compression ratio described above means that the value of for an adiabatic process is (the ratio of specific heats).
- Isothermal - This model assumes that the compressed gas remains at a constant temperature throughout the compression or expansion process. In this cycle, internal energy is removed from the system as heat at the same rate that it is added by the mechanical work of compression. Isothermal compression or expansion more closely models real life when the compressor has a large heat exchanging surface, a small gas volume, or a long time scale (i.e., a small power level). Compressors that utilize inter-stage cooling between compression stages come closest to achieving perfect isothermal compression. However, with practical devices perfect isothermal compression is not attainable. For example, unless you have an infinite number of compression stages with corresponding intercoolers, you will never achieve perfect isothermal compression.
For an isothermal process, is 1, so the value of the work integral for an isothermal process is:
When evaluated, the isothermal work is found to be lower than the adiabatic work.
- Polytropic - This model takes into account both a rise in temperature in the gas as well as some loss of energy (heat) to the compressor's components. This assumes that heat may enter or leave the system, and that input shaft work can appear as both increased pressure (usually useful work) and increased temperature above adiabatic (usually losses due to cycle efficiency). Compression efficiency is then the ratio of temperature rise at theoretical 100 percent (adiabatic) vs. actual (polytropic). Polytropic compression will use a value of between 0 (a constant-pressure process) and infinity (a constant volume process). For the typical case where an effort is made to cool the gas compressed by an approximately adiabatic process, the value of will be between 1 and .
Staged compression
In the case of centrifugal compressors, commercial designs currently do not exceed a compression ratio of more than 3.5 to 1 in any one stage (for a typical gas). Since compression raises the temperature, the compressed gas is to be cooled between stages making the compression less adiabatic and more isothermal. The inter-stage coolers typically result in some partial condensation that is removed in vapor-liquid separators.
In the case of small reciprocating compressors, the compressor flywheel may drive a cooling fan that directs ambient air across the intercooler of a two or more stage compressor.
Because rotary screw compressors can make use of cooling lubricant to reduce the temperature rise from compression, they very often exceed a 9 to 1 compression ratio. For instance, in a typical diving compressor the air is compressed in three stages. If each stage has a compression ratio of 7 to 1, the compressor can output 343 times atmospheric pressure (7 × 7 × 7 = 343 atmospheres). (343 atm or 34.8 MPa or 5.04 ksi)
Drive motors
There are many options for the motor that powers the compressor:
- Gas turbines power the axial and centrifugal flow compressors that are part of jet engines.
- Steam turbines or water turbines are possible for large compressors.
- Electric motors are cheap and quiet for static compressors. Small motors suitable for domestic electrical supplies use single-phase alternating current. Larger motors can only be used where an industrial electrical three phase alternating current supply is available.
- Diesel engines or petrol engines are suitable for portable compressors and support compressors.
- In automobiles and other types of vehicles (including piston-powered airplanes, boats, trucks, etc.), diesel or gasoline engines power output can be increased by compressing the intake air, so that more fuel can be burned per cycle. These engines can power compressors using their own crankshaft power (this setup known as a supercharger), or, use their exhaust gas to drive a turbine connected to the compressor (this setup known as a turbocharger).
Applications
Gas compressors are used in various applications where either higher pressures or lower volumes of gas are needed:
- In pipeline transport of purified natural gas from the production site to the consumer, a compressor is driven by a motor fueled by gas bled from the pipeline. Thus, no external power source is necessary.
- Petroleum refineries, natural gas processing plants, petrochemical and chemical plants, and similar large industrial plants require compressing for intermediate and end-product gases.
- Refrigeration and air conditioner equipment use compressors to move heat in refrigerant cycles (see vapor-compression refrigeration).
- Gas turbine systems compress the intake combustion air.
- Small-volume purified or manufactured gases require compression to fill high pressure cylinders for medical, welding, and other uses.
- Various industrial, manufacturing, and building processes require compressed air to power pneumatic tools.
- In the manufacturing and blow moulding of PET plastic bottles and containers.
- Some aircraft require compressors to maintain cabin pressurization at altitude.
- Some types of jet engines—such as turbojets and turbofans—compress the air required for fuel combustion. The jet engine's turbines power the combustion air compressor.
- In SCUBA diving, hyperbaric oxygen therapy, and other life support devices, compressors put breathing gas into small volume containers, such as diving cylinders.[30][31]
- In surface supplied diving, an air compressor frequently supplies low pressure air (10 to 20 bar) for breathing.
- Submarines use compressors to store air for later use in displacing water from buoyancy chambers to adjust depth.
- Turbochargers and superchargers are compressors that increase internal combustion engine performance by increasing the mass flow of air inside the cylinder, so the engine can burn more fuel and hence produce more power.
- Rail and heavy road transport vehicles use compressed air to operate rail vehicle or road vehicle brakes—and various other systems (doors, windscreen wipers, engine, gearbox control, etc.).
- Service stations and auto repair shops use compressed air to fill pneumatic tires and power pneumatic tools.
- Fire pistons and heat pumps exist to heat air or other gasses, and compressing the gas is only a means to that end.
- Rotary lobe compressors are often used to provide air in pneumatic conveying lines for powder or solids. Pressure reached can range from 0.5 to 2 bar g.[32]
- Diving air compressor in noise reduction cabinet
See also
- Axial compressor
- Cabin pressurization
- Centrifugal fan
- Compressed air
- Compressed air dryer
- Electrochemical hydrogen compressor
- Energy-saving rotary Blade compressor Patent numbers: EP0933500
- Fire piston
- Foil bearing
- Gas compression heat pump
- Guided rotor compressor
- Hydrogen compressor
- Linear compressor
- Liquid ring compressor
- Hydride compressor
- Natterer compressor
- Pneumatic cylinder
- Pneumatic tube
- Reciprocating compressor (piston compressor)
- Roots blower (a lobe-type compressor)
- Slip factor
- Trompe
- Vapor-compression refrigeration
- Variable speed air compressor
References
- "Toshiba Science Museum : World's First Residential Inverter Air Conditioner". toshiba-mirai-kagakukan.jp.
- Perry, R.H.; Green, D.W., eds. (2007). Perry's Chemical Engineers' Handbook (8th ed.). McGraw Hill. ISBN 978-0-07-142294-9.
- Bloch, H.P.; Hoefner, J.J. (1996). Reciprocating Compressors, Operation and Maintenance. Gulf Professional Publishing. ISBN 0-88415-525-0.
- Reciprocating Compressor Basics Archived 2009-04-18 at the Wayback Machine Adam Davis, Noria Corporation, Machinery Lubrication, July 2005
- "Machinery, Tools & Supplies Articles on ThomasNet". www.thomasnet.com. Archived from the original on April 28, 2010.
- https://download.schneider-electric.com/files?p_Doc_Ref=SPD_VAVR-AE7T7G_EN
- {{|date=November 2019 |bot=KAP03 |fix-attempted=yes }}
- Screw Compressor Archived 2008-01-10 at the Wayback Machine Describes how screw compressors work and include photographs.
- Technical Centre Archived 2007-12-13 at the Wayback Machine Discusses oil-flooded screw compressors including a complete system flow diagram
- ICS. "How Does a Rotary Screw Air Compressor Work?". Archived from the original on 2017-08-17. Retrieved 2017-08-16.
- Cheremisinoff, Nicholas P.; Davletshin, Anton (2015-01-28). Hydraulic Fracturing Operations: Handbook of Environmental Management Practices. John Wiley & Sons. ISBN 9781119100003. Archived from the original on 2017-12-24.
- "Single Screw Compressor". Daikin Applied UK.
- Jacobs, John S. (2006), Variable Speed Tri-Rotor Screw Compression Technology, International Compressor Engineering Conference. Paper 1825.
- Inc, Mattei Compressors. "Rotary Vane Compressors and the Vane Compressor - Compressors for stationary industrial and OEM applications - Mattei". www.matteicomp.com. Archived from the original on May 9, 2010.
- "Motion of Rolling Piston in Rotary Compressor". Purdue University. Archived from the original on 2017-08-16. Retrieved 2017-08-16.
- "What the New Samsung Mini Rotary Compressor Means". news.samsung.com.
- "High Efficiency Compressor to Achieve a High COP | Air Conditioning and Refrigeration | Daikin Global". www.daikin.com.
- Tischer, J., Utter, R: “Scroll Machine Using Discharge Pressure For Axial Sealing,” U.S. Patent 4522575, 1985.
- Caillat, J., Weatherston, R., Bush, J: “Scroll-Type Machine With Axially Compliant Mounting,” U.S. Patent 4767293, 1988.
- Richardson, Jr., Hubert: “Scroll Compressor With Orbiting Scroll Member Biased By Oil Pressure,” U.S. Patent 4875838, 1989.
- Eric Slack (Winter 2016). "Sertco". Energy and Mining International. Phoenix Media Corporation. Archived from the original on March 4, 2016. Retrieved February 27, 2016.
- Maynard, Frank (November 1910). "Five thousand horsepower from air bubbles". Popular Mechanics: 633. Archived from the original on 2017-03-26.
- Dixon S.L. (1978). Fluid Mechanics, Thermodynamics of Turbomachinery (Third ed.). Pergamon Press. ISBN 0-08-022722-8.
- Aungier, Ronald H. (2000). Centrifugal Compressors A Strategy for Aerodynamic design and Analysis. ASME Press. ISBN 0-7918-0093-8.
- Cheremisinoff, Nicholas P. (2016-04-20). Pollution Control Handbook for Oil and Gas Engineering. John Wiley & Sons. ISBN 9781119117889. Archived from the original on 2017-12-24.
- Kano, Fumikata. "Development of High Specific Speed Mixed Flow Compressors" (PDF). Texas A&M University. Archived from the original (PDF) on 2014-08-11. Retrieved 2017-08-16.
- Cengel, Yunus A., and Michaeul A. Boles. Thermodynamics: An Engineering Approach. 7th Edition ed. New York: Mcgraw-Hill, 2012. Print.
- "PTC-10 Performance Test Code on Compressors & Exhausters - ASME". www.asme.org. Archived from the original on June 19, 2015.
- Perry's Chemical Engineer's Handbook 8th edition Perry, Green, page 10-45 section 10-76
- Millar IL, Mouldey PG (2008). "Compressed breathing air – the potential for evil from within". Diving and Hyperbaric Medicine. South Pacific Underwater Medicine Society. 38 (2): 145–51. PMID 22692708. Archived from the original on 2010-12-25. Retrieved 2009-02-28.
- Harlow, V (2002). Oxygen Hacker's Companion. Airspeed Press. ISBN 0-9678873-2-1.
- "Blowers (Roots)". Engineering resources for powder processing industries. www.powderprocess.net. Archived from the original on 14 August 2017. Retrieved 15 August 2017.