Induction generator
An induction generator or asynchronous generator is a type of alternating current (AC) electrical generator that uses the principles of induction motors to produce electric power. Induction generators operate by mechanically turning their rotors faster than synchronous speed. A regular AC induction motor usually can be used as a generator, without any internal modifications. Induction generators are useful in applications such as mini hydro power plants, wind turbines, or in reducing high-pressure gas streams to lower pressure, because they can recover energy with relatively simple controls.
An induction generator usually draws its excitation power from an electrical grid. Because of this, induction generators cannot usually black start a de-energized distribution system. Sometimes, however, they are self-excited by using phase-correcting capacitors.
Principle of operation
An induction generator produces electrical power when its rotor is turned faster than the synchronous speed. For a typical four-pole motor (two pairs of poles on stator) operating on a 60 Hz electrical grid, the synchronous speed is 1800 rotations per minute (rpm). The same four-pole motor operating on a 50 Hz grid will have a synchronous speed of 1500 RPM. The motor normally turns slightly slower than the synchronous speed; the difference between synchronous and operating speed is called "slip" and is usually expressed as per cent of the synchronous speed. For example, a motor operating at 1450 RPM that has a synchronous speed of 1500 RPM is running at a slip of +3.3%.
In normal motor operation, the stator flux rotation is faster than the rotor rotation. This causes the stator flux to induce rotor currents, which create a rotor flux with magnetic polarity opposite to stator. In this way, the rotor is dragged along behind stator flux, with the currents in the rotor induced at the slip frequency.
In generator operation, a prime mover (turbine or engine) drives the rotor above the synchronous speed (negative slip). The stator flux still induces currents in the rotor, but since the opposing rotor flux is now cutting the stator coils, an active current is produced in stator coils and the motor now operates as a generator, sending power back to the electrical grid.
Excitation
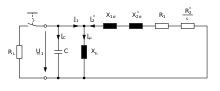
An induction machine requires an externally-supplied armature current. Because the rotor field always lags behind the stator field, the induction machine always consumes reactive power, regardless of whether it is operating as a generator or a motor.
A source of excitation current for magnetizing flux (reactive power) for the stator is still required, to induce rotor current. This can be supplied from the electrical grid or, once it starts producing power, from the generator itself. The generating mode for induction motors is complicated by the need to excite the rotor, which begins with only residual magnetization. In some cases, that residual magnetization is enough to self-excite the motor under load. Therefore, it is necessary to either snap the motor and connect it momentarily to a live grid or to add capacitors charged initially by residual magnetism and providing the required reactive power during operation. Similar is the operation of the induction motor in parallel with a synchronous motor serving as a power factor compensator. A feature in the generator mode in parallel to the grid is that the rotor speed is higher than in the driving mode. Then active energy is being given to the grid.[1]Another disadvantage of induction motor generator is that it consumes a significant magnetizing current I0 = (20-35)%.
An induction machine can be started by charging the capacitors, with a DC source, while the generator is turning typically at or above generating speeds. Once the DC source is removed the capacitors will provide the magnetization current required to begin producing voltage.
An induction machine that has recently been operating may also spontaneously produce voltage and current due to residual magnetism left in the core.
Active power
Active power delivered to the line is proportional to slip above the synchronous speed. Full rated power of the generator is reached at very small slip values (motor dependent, typically 3%). At synchronous speed of 1800 rpm, generator will produce no power. When the driving speed is increased to 1860 rpm (typical example), full output power is produced. If the prime mover is unable to produce enough power to fully drive the generator, speed will remain somewhere between 1800 and 1860 rpm range.
Required capacitance
A capacitor bank must supply reactive power to the motor when used in stand-alone mode. The reactive power supplied should be equal or greater than the reactive power that the machine normally draws when operating as a motor.
Torque vs. slip
The basic fundamental of induction generators is the conversion from mechanical energy to electrical energy. This requires an external torque applied to the rotor to turn it faster than the synchronous speed. However, indefinitely increasing torque doesn't lead to an indefinite increase in power generation. The rotating magnetic field torque excited from the armature works to counter the motion of the rotor and prevent over speed because of induced motion in the opposite direction. As the speed of the motor increases the counter torque reaches a max value of torque (breakdown torque) that it can operate until before the operating conditions become unstable. Ideally, induction generators work best in the stable region between the no-load condition and maximum torque region.
Rated current
The maximum power that can be produced by an induction motor operated as a generator is limited by the rated current of the machine's windings.
Grid and stand-alone connections
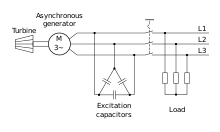
In induction generators, the reactive power required to establish the air gap magnetic flux is provided by a capacitor bank connected to the machine in case of stand-alone system and in case of grid connection it draws reactive power from the grid to maintain its air gap flux. For a grid-connected system, frequency and voltage at the machine will be dictated by the electric grid, since it is very small compared to the whole system. For stand-alone systems, frequency and voltage are complex function of machine parameters, capacitance used for excitation, and load value and type.
Uses
Induction generators are often used in wind turbines and some micro hydro installations due to their ability to produce useful power at varying rotor speeds. Induction generators are mechanically and electrically simpler than other generator types. They are also more rugged, requiring no brushes or commutators.
Limitations
An induction generator connected to a capacitor system can generate sufficient reactive power to operate on its own. When the load current exceeds the capability of the generator to supply both magnetization reactive power and load power the generator will immediately cease to produce power. The load must be removed and the induction generator restarted with either a DC source, or if present, residual magnetism in the core.[2]
Induction generators are particularly suitable for wind generating stations as in this case speed is always a variable factor. Unlike synchronous motors, induction generators are load-dependent and cannot be used alone for grid frequency control.
Example application
As an example, consider the use of a 10 hp, 1760 r/min, 440 V, three-phase induction motor as an asynchronous generator. The full-load current of the motor is 10 A and the full-load power factor is 0.8.
Required capacitance per phase if capacitors are connected in delta:
- Apparent power S = √3 E I = 1.73 × 440 × 10 = 7612 VA
- Active power P = S cos θ = 7612 × 0.8 = 6090 W
- Reactive power Q = = 4567 VAR
For a machine to run as an asynchronous generator, capacitor bank must supply minimum 4567 / 3 phases = 1523 VAR per phase. Voltage per capacitor is 440 V because capacitors are connected in delta.
- Capacitive current Ic = Q/E = 1523/440 = 3.46 A
- Capacitive reactance per phase Xc = E/Ic = 127 Ω
Minimum capacitance per phase:
- C = 1 / (2*π*f*Xc) = 1 / (2 * 3.141 * 60 * 127) = 21 microfarads.
If the load also absorbs reactive power, capacitor bank must be increased in size to compensate.
Prime mover speed should be used to generate frequency of 60 Hz:
Typically, slip should be similar to full-load value when machine is running as motor, but negative (generator operation):
- if Ns = 1800, one can choose N=Ns+40 rpm
- Required prime mover speed N = 1800 + 40 = 1840 rpm.
See also
Notes
- Citation error. See inline comment how to fix.
- Huassain, Ashfaq. Electric Machines. Dhanpat Rai and Co. p. 411.
References
- Electrical Machines, Drives, and Power Systems, 4th edition, Theodore Wildi, Prentice Hall, ISBN 0-13-082460-7, pages 311–314.