Cleanroom
A cleanroom or clean room is a facility ordinarily utilized as a part of specialized industrial production or scientific research, including the manufacture of pharmaceutical items, integrated circuits, CRT, LCD, OLED and microLED displays. Cleanrooms are designed to maintain extremely low levels of particulates, such as dust, airborne organisms, or vaporized particles. Cleanrooms typically have a cleanliness level quantified by the number of particles per cubic meter at a predetermined molecule measure. The ambient outdoor air in a typical urban area contains 35,000,000 particles for each cubic meter in the size range 0.5 μm and bigger in measurement, equivalent to an ISO 9 cleanroom, while by comparison an ISO 1 cleanroom permits no particles in that size range and just 12 particles for each cubic meter of 0.3 μm and smaller.
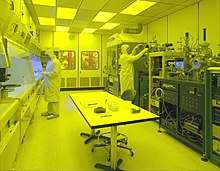
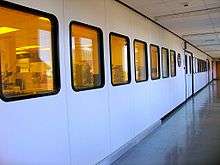
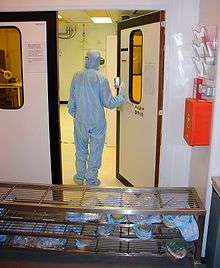
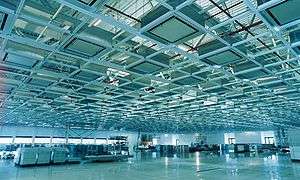
History
The modern cleanroom was invented by American physicist Willis Whitfield.[1] As employee of the Sandia National Laboratories, Whitfield created the initial plans for the cleanroom in 1960.[1] Prior to Whitfield's invention, earlier cleanrooms often had problems with particles and unpredictable airflows. Whitfield designed his cleanroom with a constant, highly filtered air flow to flush out impurities.[1] Within a few years of its invention in the 1960s, Whitfield's modern cleanroom had generated more than US$50 billion in sales worldwide (approximately $406 billion today).[2][3]
The majority of the integrated circuit manufacturing facilities in Silicon Valley were made by three companies: MicroAire, PureAire, and Key Plastics. These competitors made laminar flow units, glove boxes, clean rooms and air showers, along with the chemical tanks and benches used in the 'Wet Process' building of integrated circuits. These three companies were the pioneers of the use of Teflon for airguns, chemical pumps, scrubbers, water guns, and other devices needed for the production of integrated circuits. William (Bill) C. McElroy Jr. worked as engineering manager, drafting room supervisor, QA/QC, and designer for all three companies and his designs added 45 original patents to the technology of the time. McElroy also wrote a four-page article for MicroContamination Journal, wet processing training manuals, and equipment manuals for wet processing and clean rooms.[4]
Overview
Cleanrooms can be very large. Entire manufacturing facilities can be contained within a cleanroom with factory floors covering thousands of square meters. They are used extensively in semiconductor manufacturing, solar panel, rechargeable battery, LED, LCD and OLED display manufacturing, biotechnology, the life sciences, and other fields that are very sensitive to environmental contamination. There are also modular cleanrooms.[5]
The outside air entering a cleanroom is filtered and cooled by several outdoor Air handlers using progressively finer filters to exclude dust, and the air inside is constantly recirculated through fan filter units containing high-efficiency particulate air (HEPA), MERV 17-20 and/or ultra-low particulate air (ULPA) filters to remove internally generated contaminants. Special lighting fixtures, walls, equipment and other materials are used to minimize the generation of airborne particles. Plastic sheets can be used to restrict air turbulence. [6][7][8] The air temperature and humidity levels inside the cleanroom are tightly controlled. Static electricity may be controlled using ionizing bars. Cleanrooms may also have numerous seismic base isolation systems to prevent costly equipment malfunction.[9]
Staff enter and leave through airlocks (sometimes including an air shower stage), and wear protective clothing such as hoods, face masks, gloves, boots, and coveralls. This is to minimize the carrying of particulate by the person moving into the cleanroom.
Equipment inside the cleanroom is designed to generate minimal air contamination. Only special mops and buckets are used. Cleanroom furniture is designed to produce a minimum of particles and is easy to clean.
The selection of material for the construction of the cleanroom should not generate any particle hence monolithic epoxy or polyurethane floor coating is preferred. Buffed Stainless steel or Powder-coated MS sandwich partition panels & ceiling panel are used. Corners like the wall to wall, wall to floor, wall to ceiling are avoided by providing coved surface and all joints need to be sealed with epoxy sealant to avoid any deposition or generation of particles at the joints.
Common materials such as paper, pencils, and fabrics made from natural fibers are often excluded, and alternatives used. Cleanrooms are not sterile (i.e., free of uncontrolled microbes);[10] only airborne particles are controlled. Particle levels are usually tested using a particle counter and microorganisms detected and counted through environmental monitoring methods.[11][12] Polymer tools used in cleanrooms must be carefully determined to be chemically compatible with cleanroom processing fluids [13] as well as ensured to generate a low level of particle generation.[14]
Some cleanrooms are kept at a positive pressure so if any leaks occur, air leaks out of the chamber instead of unfiltered air coming in.
Some cleanroom HVAC systems control the humidity to such low levels that extra equipment like air ionizers are required to prevent electrostatic discharge problems.
Low-level cleanrooms may only require special shoes, with completely smooth soles that do not track in dust or dirt. However, for safety reasons, shoe soles must not create slipping hazards. Access to a cleanroom is usually restricted to those wearing a cleanroom suit.
In cleanrooms in which the standards of air contamination are less rigorous, the entrance to the cleanroom may not have an air shower. An anteroom (known as a "gray room") is used to put on clean-room clothing.
Some manufacturing facilities do not use fully realized cleanrooms, but use some practices or technologies typical of cleanrooms to meet their contamination requirements.
In hospitals, theatres are similar to cleanrooms for surgical patients' operations with incisions to prevent any infections for the patient.
Air flow principles
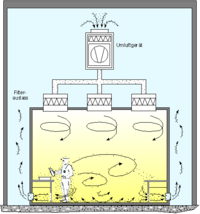
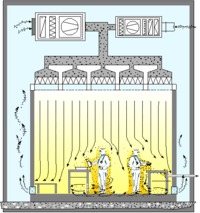
Cleanrooms maintain particulate-free air through the use of either HEPA or ULPA filters employing laminar or turbulent air flow principles. Laminar, or unidirectional, air flow systems direct filtered air downward or in horizontal direction in a constant stream towards filters located on walls near the cleanroom floor or through raised perforated floor panels to be recirculated. Laminar air flow systems are typically employed across 80% of a cleanroom ceiling to maintain constant air processing. Stainless steel or other non shedding materials are used to construct laminar air flow filters and hoods to prevent excess particles entering the air. Turbulent, or non unidirectional, air flow uses both laminar air flow hoods and nonspecific velocity filters to keep air in a cleanroom in constant motion, although not all in the same direction. The rough air seeks to trap particles that may be in the air and drive them towards the floor, where they enter filters and leave the cleanroom environment. US FDA and EU have laid down guidelines and limit for microbial contamination which is very stringent to ensure freedom from microbial contamination in pharmaceutical products.[15][16] Plenums between air handlers and fan filter units along with sticky mats may also be used.
In addition to air filters, clean rooms can also use ultraviolet light to disinfect the air.[17] UV devices can be fitted into ceiling light fixtures and irradiate air, killing potentially infectious particulates, including 99.99 percent of airborne microbial and fungal contaminants.[18] UV light has previously been used to clean surface contaminants in sterile environments such as hospital operating rooms. Their use in other clean rooms may increase as equipment becomes more affordable. Potential advantages of UV-based decontamination includes a reduced reliance on chemical disinfectants and the extension of HVAC filter life.
Personnel contamination of cleanrooms
The greatest threat to cleanroom contamination comes from the users themselves.[19] In the healthcare and pharmaceutical sectors, control of microorganisms is important, especially microorganisms likely to be deposited into the air stream from skin shedding. Studying cleanroom microflora is of importance for microbiologists and quality control personnel to assess changes in trends. Shifts in the types of microflora may indicate deviations from the "norm" such as resistant strains or problems with cleaning practices.
In assessing cleanroom microorganisms, the typical flora are primarily those associated with human skin (Gram-positive cocci), although microorganisms from other sources such as the environment (Gram-positive rods) and water (Gram-negative rods) are also detected, although in lower number. Common bacterial genera include Micrococcus, Staphylococcus, Corynebacterium, and Bacillus, and fungal genera include Aspergillus and Penicillium.[12]
Cleanroom classification and standardization
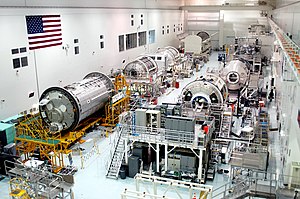
Cleanrooms are classified according to the number and size of particles permitted per volume of air. Large numbers like "class 100" or "class 1000" refer to FED-STD-209E, and denote the number of particles of size 0.5 μm or larger permitted per cubic foot of air. The standard also allows interpolation; for example SNOLAB is maintained as a class 2000 cleanroom.
A discrete, light-scattering airborne particle counter is used to determine the concentration of airborne particles, equal to and larger than the specified sizes, at designated sampling locations.
Small numbers refer to ISO 14644-1 standards, which specify the decimal logarithm of the number of particles 0.1 μm or larger permitted per m3 of air. So, for example, an ISO class 5 cleanroom has at most 105 particles/m3.
Both FS 209E and ISO 14644-1 assume log-log relationships between particle size and particle concentration. For that reason, zero particle concentration does not exist. Some classes do not require testing some particle sizes, because the concentration is too low or too high to be practical to test for, but such blanks should not be read as zero.
Because 1 m3 is about 35 ft3, the two standards are mostly equivalent when measuring 0.5 μm particles, although the testing standards differ. Ordinary room air is around class 1,000,000 or ISO 9.[21]
ISO 14644-1 and ISO 14698
ISO 14644-1 and ISO 14698 are non-governmental standards developed by the International Organization for Standardization (ISO).[22] The former applies to clean rooms in general (see table below); the latter to cleanrooms where biocontamination may be an issue.
ISO 14644-1 defines the maximum concentration of particles per class and per particle size with the following formula[23]
Where is the maximum concentration of particles in a volume of 1m of airborne particles that are equal to, or larger, than the considered particle size which is rounded to the nearest whole number, using no more than three significant figures, is the ISO class number, is the size of the particle in m and 0.1 is a constant expressed in m. The result for standard particle sizes is expressed in the following table.
Class | Maximum particles/m3 a | FED STD 209E equivalent | |||||
---|---|---|---|---|---|---|---|
≥0.1 μm | ≥0.2 μm | ≥0.3 μm | ≥0.5 μm | ≥1 μm | ≥5 μm | ||
ISO 1 | 10b | d | d | d | d | e | |
ISO 2 | 100 | 24b | 10b | d | d | e | |
ISO 3 | 1,000 | 237 | 102 | 35b | d | e | Class 1 |
ISO 4 | 10,000 | 2,370 | 1,020 | 352 | 83b | e | Class 10 |
ISO 5 | 100,000 | 23,700 | 10,200 | 3,520 | 832 | d,e,f | Class 100 |
ISO 6 | 1,000,000 | 237,000 | 102,000 | 35,200 | 8,320 | 293 | Class 1,000 |
ISO 7 | c | c | c | 352,000 | 83,200 | 2,930 | Class 10,000 |
ISO 8 | c | c | c | 3,520,000 | 832,000 | 29,300 | Class 100,000 |
ISO 9 | c | c | c | 35,200,000 | 8,320,000 | 293,000 | Room air |
a All concentrations in the table are cumulative, e.g. for ISO Class 5, the 10 200 particles shown at 0,3 μm include all particles equal to and greater than this size. b These concentrations will lead to large air sample volumes for classification. Sequential sampling procedure may be applied; see Annex D. |
US FED STD 209E
US FED-STD-209E was a United States federal standard. It was officially cancelled by the General Services Administration on November 29, 2001,[24][25] but is still widely used.[26]
Class | Maximum particles/ft3 | ISO equivalent | ||||
---|---|---|---|---|---|---|
≥0.1 μm | ≥0.2 μm | ≥0.3 μm | ≥0.5 μm | ≥5 μm | ||
1 | 35 | 7.5 | 3 | 1 | 0.007 | ISO 3 |
10 | 350 | 75 | 30 | 10 | 0.07 | ISO 4 |
100 | 3,500 | 750 | 300 | 100 | 0.7 | ISO 5 |
1,000 | 35,000 | 7,500 | 3000 | 1,000 | 7 | ISO 6 |
10,000 | 350,000 | 75,000 | 30,000 | 10,000 | 70 | ISO 7 |
100,000 | 3.5×106 | 750,000 | 300,000 | 100,000 | 830 | ISO 8 |
Current regulating bodies include: ISO, USP 800, US FED STD 209E (previous standard, still used)
- Drug Quality and Security Act (DQSA) created in Nov. 2013 in response to drug compounding deaths and serious adverse events.
- The Federal Food, Drug, and Cosmetic Act (FD&C Act) created specific guidelines and policies for human compounding.
- 503A addresses compounding by state or federally licensed facility by licensed personnel (pharmacist/ physicians)
- 503B pertaining to outsourcing facilities need direct supervision from a licensed pharmacist and do not need to be a licensed pharmacy. Facility is licensed through the Food and Drug Administration (FDA) [27]
EU GMP classification
EU GMP guidelines are more stringent than others, requiring cleanrooms to meet particle counts at operation (during manufacturing process) and at rest (when manufacturing process is not carried out, but room AHU is on).
Class | Maximum particles/m3[28] | |||
---|---|---|---|---|
At Rest | In Operation | |||
0.5 μm | 5 μm | 0.5 μm | 5 μm | |
Grade A | 3,520 | 20 | 3520 | 20 |
Grade B | 3,520 | 29 | 352,000 | 2,900 |
Grade C | 352,000 | 2,900 | 3,520,000 | 29,000 |
Grade D | 3,520,000 | 29,000 | Not defined | Not defined |
BS 5295
BS 5295 is a British Standard.
Class | Maximum particles/m3 | |||||
---|---|---|---|---|---|---|
≥0.5 μm | ≥1 μm | ≥5 μm | ≥10 μm | ≥25 μm | ||
Class 1 | 3,000 | 0 | 0 | 0 | ||
Class 2 | 300,000 | 2,000 | 30 | |||
Class 3 | 1,000,000 | 20,000 | 4,000 | 300 | ||
Class 4 | 200,000 | 40,000 | 4,000 | |||
BS 5295 Class 1 also requires that the greatest particle present in any sample can not exceed 5 μm.[29] BS 5295 has been superseded, withdrawn since the year 2007 and replaced with "BS EN ISO 14644-6:2007".[30]
USP <800> Standards
USP 800 is a United States standard developed by the United States Pharmacopeial Convention (USP) with an effective date of December 1, 2019.[31]
See also
- Air ionizer
- Air quality index
- Contamination control
- Data recovery lab
- Particle counter
- Pneumatic filter
- Secure environment
- Semiconductor device fabrication
References
- Yardley, William (2012-12-04). "Willis Whitfield, Clean Room Inventor, Dies at 92". The New York Times. Retrieved 2013-06-22.
- "Sandia physicist, cleanroom inventor dies at 92". KWES. Associated Press. 2012-11-26. Retrieved 2012-12-03.
- "Willis Whitfield - Father of the Cleanroom" (PDF). Cleanroom online. September 2015. Retrieved 2016-05-18.
- William (Bill) C. McElroy Jr., MicroAire Engineering Manager and acting VP; Kay Plastics Engineering Manager; PureAire Drafting Room Manager
- "What is a Cleanroom? | Mecart". MECART Cleanrooms. August 16, 2016.
- "Kenall Cleanroom and Containment Lighting". kenall.com.
- "Fitting lights in cleanrooms". www.cleanroomtechnology.com.
- "Cleanroom LED". Philips.
- "Semiconductor Technology at TSMC, 2011" – via www.youtube.com.
- In NASA’s Sterile Areas, Plenty of Robust Bacteria New York Times, 9. October 2007
- Sandle, T (November 2012). "Application of quality risk management to set viable environmental monitoring frequencies in biotechnology processing and support areas". PDA J Pharm Sci Technol. 66 (6): 560–79. doi:10.5731/pdajpst.2012.00891. PMID 23183652.
- Sandle, T (November 2011). "A review of cleanroom microflora: types, trends, and patterns". PDA J Pharm Sci Technol. 65 (4): 392–403. doi:10.5731/pdajpst.2011.00765. PMID 22293526.
- Heikkinen, Ismo T.S.; Kauppinen, Christoffer; Liu, Zhengjun; Asikainen, Sanja M.; Spoljaric, Steven; Seppälä, Jukka V.; Savin, Hele (October 2018). "Chemical compatibility of fused filament fabrication-based 3-D printed components with solutions commonly used in semiconductor wet processing" (PDF). Additive Manufacturing. 23: 99–107. doi:10.1016/j.addma.2018.07.015. ISSN 2214-8604.
- Pasanen, T.P.; von Gastrow, G.; Heikkinen, I.T.S.; Vähänissi, V.; Savin, H.; Pearce, J.M. (January 2019). "Compatibility of 3-D printed devices in cleanroom environments for semiconductor processing". Materials Science in Semiconductor Processing. 89: 59–67. doi:10.1016/j.mssp.2018.08.027. ISSN 1369-8001.
- "Clean Room Classification".
- "Cleanroom Air Flow Principles". www.thomasnet.com.
- Guimera, Don; Trzil, Jean; Joyner, Joy; Hysmith, Nicholas D. (2018-02-01). "Effectiveness of a shielded ultraviolet C air disinfection system in an inpatient pharmacy of a tertiary care children's hospital". American Journal of Infection Control. 46 (2): 223–225. doi:10.1016/j.ajic.2017.07.026. ISSN 0196-6553.
- outsourcing-pharma.com. "UV helps maintain cleanroom air quality". outsourcing-pharma.com. Retrieved 2020-04-15.
- "Cleanroom and Controlled Environment Attire - ANSI Blog". The ANSI Blog. 2015-07-15. Retrieved 2018-11-24.
- "Space Station Processing Facility (SSPF)". science.ksc.nasa.gov.
- "Cleanroom Classification / Particle Count / FS209E / ISO TC209 /". Archived from the original on 2008-02-14. Retrieved 2008-03-05.
- "ISO 14644-1:2015 - Cleanrooms and associated controlled environments -- Part 1: Classification of air cleanliness by particle concentration". ISO. Retrieved 2016-09-12.
- W. Whyte (17 October 2001). Cleanroom Technology: Fundamentals of Design, Testing and Operation. John Wiley & Sons. ISBN 978-0-471-86842-2.
- "Federal Standard 209E Cancellation". www.iest.org.
- "Archived copy" (PDF). Archived from the original (PDF) on 2008-05-28. Retrieved 2008-04-17.CS1 maint: archived copy as title (link), page 148
- "NUFAB SAFETY & PROTOCOL" (PDF). Retrieved 24 February 2016.
- Research, Center for Drug Evaluation and (2019-02-09). "FD&C Act Provisions that Apply to Human Drug Compounding". FDA.
- "Understanding Cleanroom Classifications". Archived from the original on 2016-06-01. Retrieved 2015-08-21.
- Market Venture Philippines Inc. web site (2006-04-19). "What is a Clean Room?". Archived from the original on 2012-08-28. Retrieved 2007-06-02.
- "BS 5295-0:1989 - Environmental cleanliness in enclosed spaces. General introduction, terms and definitions for clean rooms and clean air devices". 2016. Retrieved 2016-04-18.
- "USP 800 | USP". www.usp.org. Retrieved 2020-04-13.
External links
![]() |
Wikimedia Commons has media related to Cleanrooms. |