Nanolattice
A nanolattice is a synthetic porous material consisting of nanometer-size members which are patterned into an ordered lattice structure, like a space frame. Driven by the evolution of 3D printing techniques, nanolattices aiming to exploit beneficial material size effects through miniaturized lattice designs were first developed in the mid-2010s,[2][3][4][5]. Nanolattices are the smallest man-made lattice truss structures[2][6][1] and a class of metamaterials which derive their properties from both their geometry (general metamaterial definition) and the small size of their elements.[5] Therefore, they can possess effective properties which are not found in nature and may not be achieved with larger-scale lattices of the same geometry.
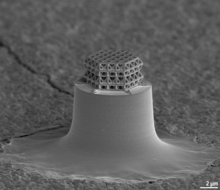
Synthesis
To produce nanolattice materials, polymer templates are manufactured by high-resolution 3D printing processes, such as multiphoton lithography, or by self-assembly techniques. Ceramic, metal or composite material nanolattices are formed by post-treatment of the polymer templates with techniques including pyrolysis, atomic layer deposition, electroplating and electroless plating.[5] Pyrolysis, which additionally shrinks the lattices by up to 90%, creates the smallest-size structures, whereby the polymeric template material transforms into carbon[1], or other ceramics[7] and metals[8], through thermal decomposition in inert atmosphere or vacuum.
Properties
Nanolattices are the strongest existing cellular materials, they are extremely light-weight, consisting of 50%-99% air, but can be as strong as steel.[2][5][1] The extremely small volume of their individual members thereby statistically nearly eliminates the material flaw population and the base material of nanolattices can reach mechanical strengths on the order of the theoretical strength of an ideal, perfect crystal. While such effects are typically limited to individual, geometrically primitive structures like nanowires, the specific architecture allows nanolattices to exploit them in complex, three-dimensional structures of notably larger overall size. Nanolattices can be designed highly deformable and recoverable,[4][9] even with ceramic base materials, and can possess mechanical metamaterial properties like auxetic or meta-fluidic behavior.[1] Nanolattices can combine mechanical resilience and ultra-low thermal conductivity and can have electromagnetic metamaterial characteristics like optical cloaking. [10]
See also
References
- Bauer, J.; Schroer, A.; Schwaiger, R.; Kraft, O. (2016). "Approaching theoretical strength in glassy carbon nanolattices". Nature Materials. 15 (4): 438–443. Bibcode:2016NatMa..15..438B. doi:10.1038/nmat4561. PMID 26828314.
- "Nanolattice engineering". Physics Today 69, 3, 76 (2016).
- "Could future spaceships be built with artificial ‘bone’?". latimes.com. 4 February 2014.
- "Ceramics don't have to be brittle: Incredibly light, strong materials recover original shape after being smashed". sciencedaily.com. 11 September 2014.
- Bauer, J.; Meza, L. R.; Schaedler, T. A.; Schwaiger, R.; Zheng, X.; Valdevit, L. (2017). "Nanolattices: An Emerging Class of Mechanical Metamaterials". Advanced Materials. 29 (40): 1701850. doi:10.1002/adma.201701850. PMID 28873250.
- "Researchers Create Smallest Ever Lattice Structure". http://www.sci-news.com. 2 February 2016.
- Bauer, J.; Crook, C.; Guell Izard, A.; Eckel, Z. C.; Ruvalcaba, N.; Schaedler, T. A.; Valdevit, L. (2019). "Additive Manufacturing of Ductile, Ultrastrong Polymer-Derived Nanoceramics". Matter. 1 (6): 1547–1556. doi:10.1016/j.matt.2019.09.009.
- Vyatskikh, A.; Delalande, S.; Kudo, A.; Zhang, X.; Portela, C. M.; Greer, J. R. (2018). "Additive manufacturing of 3D nano-architected metals". Nature Communications. 9 (1): 593. Bibcode:2018NatCo...9..593V. doi:10.1038/s41467-018-03071-9. PMID 29426947.
- Meza, L. R.; Das, S.; Greer, J. R. (2014). "Strong, lightweight, and recoverable three-dimensional ceramic nanolattices" (PDF). Science. 345 (6202): 1322–13226. Bibcode:2014Sci...345.1322M. doi:10.1126/science.1255908. PMID 25214624.
- Dou, N.G.; Jagt, R.A.; Portela, C.M.; Greer, J. R.; Minnich, A.J. (2018). "Ultralow Thermal Conductivity and Mechanical Resilience of Architected Nanolattices". Nano Letters. 18 (8): 4755–4761. Bibcode:2018NanoL..18.4755D. doi:10.1021/acs.nanolett.8b01191.