False brinelling
False brinelling is a bearing damage caused by fretting, with or without corrosion,[1] that causes imprints that look similar to brinelling, but are caused by a different mechanism. False brinelling may occur in bearings which act under small oscillations[2] or vibrations.[3]
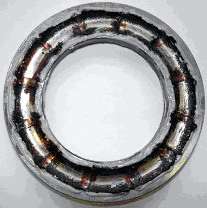
The basic cause of false brinelling is that the design of the bearing does not have a method for redistribution of lubricant without large rotational movement of all bearing surfaces in the raceway.[4] Lubricant is pushed out of a loaded region during small oscillatory movements and vibration where the bearings surfaces repeatedly do not move very far.[5] Without lubricant, wear is increased when the small oscillatory movements occur again. It is possible for the resulting wear debris to oxidize and form an abrasive compound which further accelerates wear.
Mechanism of action
In normal operation, a rolling-element bearing has the rollers and races separated by a thin layer of lubricant such as grease or oil.[6] Although these lubricants normally appear liquid (not solid), under high pressure they act as solids and keep the bearing and race from touching.[7][8]
If the lubricant is removed, the bearings and races can touch directly. While bearings and races appear smooth to the eye, they are microscopically rough. Thus, high points of each surface can touch, but "valleys" do not. The bearing load is thus spread over much less area increasing the contact stress,[9] causing pieces of each surface to break off or to become pressure-welded then break off when the bearing rolls on.
The broken-off pieces are also called wear debris. Wear debris is bad because it is relatively large compared to the surrounding surface finish and thus creates more regions of high contact stress. Worse, the steel in ordinary bearings can oxidize (rust),[10] producing a more abrasive compound which accelerates wear.
Simulation of false brinelling
The simulation of false brinelling is possible with the help of the finite element method. For the simulation, the relative displacements (slip) between rolling element and raceway as well as the pressure in the rolling contact are determined. For comparison between simulation and experiments, the friction work density is used, which is the product of friction coefficient, slip and local pressure. The simulation results can be used to determine critical application parameters or to explain the damage mechanisms.[11]

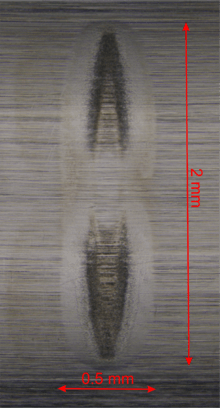
Examples
False brinelling was first mentioned by Almen in 1937.[12] Almen found that wheel bearings were damaged before they were used by customers. Furthermore, he found that the bearings were more damaged for long-distance shipping of the cars and that the season of shipping also had an influence. The reason for the damaged bearings were micro-oscillations[13] which occurred due to the shipping. Because the damage has a similar look to brinelling, it was called false brinelling.[14]
Although the auto-delivery problem has been solved, there are many modern examples. For example, generators or pumps may fail or need service, so it is common to have a nearby spare unit which is left off most of the time but brought into service when needed. Surprisingly, however, vibration from the operating unit can cause bearing failure in the unit which is switched off. When that unit is turned on, the bearings may be noisy due to damage, and may fail completely within a few days or weeks[15][16] even though the unit and its bearings are otherwise new. Common solutions include: keeping the spare unit at a distance from the one which is on and vibrating; manually rotating shafts of the spare units on a regular (for example, weekly) basis; or regularly switching between the units so that both are in regular (for example, weekly) operation.
Until recently, bicycle headsets tended to suffer from false brinelling in the "straight ahead" steering position, due to small movements caused by flexing of the fork. Good modern headsets incorporate a plain bearing to accommodate this flexing, leaving the ball race to provide pure rotational movement.
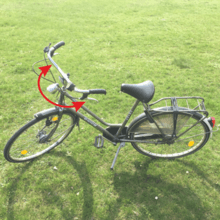
Bearings of modern wind turbines are often affected by false brinelling. Especially the pitch bearing,[17] which is used under oscillation, shows often false brinelling damages.[18]
References
- Schwack, Fabian (2017-05-25). "Time-dependent analyses of wear in oscillating bearing applications (PDF Download Available)". ResearchGate. Retrieved 2017-06-27.
- Schwack, Fabian; Poll, Gerhard. "Service Life of Blade Bearings - Problems Faced in Service Life Estimation of Blade Bearings". ResearchGate. Retrieved 2017-06-27.
- Pittroff, Hans (1965-09-01). "Fretting Corrosion Caused by Vibration With Rolling Bearings Stationary". Journal of Basic Engineering. 87 (3): 713–723. doi:10.1115/1.3650657. ISSN 0098-2202.
- Schwack, Fabian; Bader, Norbert; Leckner, Johan; Demaille, Claire; Poll, Gerhard (2020-08-15). "A study of grease lubricants under wind turbine pitch bearing conditions". Wear. 454-455: 203335. doi:10.1016/j.wear.2020.203335. ISSN 0043-1648.
- Feng, Chen; Maruyama, Taisuke; Saito, Tsuyoshi (2009). "Oil Film Behavior under Minute Vibrating Conditions in EHL Point Contacts". Advanced Tribology. Springer, Berlin, Heidelberg. pp. 42–43. doi:10.1007/978-3-642-03653-8_16. ISBN 978-3-642-03652-1.
- Maruyama, Taisuke; Saitoh, Tsuyoshi; Yokouchi, Atsushi (2017-05-04). "Differences in Mechanisms for Fretting Wear Reduction between Oil and Grease Lubrication". Tribology Transactions. 60 (3): 497–505. doi:10.1080/10402004.2016.1180469. ISSN 1040-2004.
- Godfrey, Douglas. "Fretting Corrosion or False Brinelling | Wear | Surface Science". Scribd. Retrieved 2017-06-27.
- Errichello, Robert (April 2004). "Another perspective: False brinelling and fretting corrosion (PDF Download Available)". Lubrication Engineering. 60: 34–36. Retrieved 2017-06-27.
- Tonazzi, D.; Komba, E. Houara; Massi, F.; Le Jeune, G.; Coudert, J. B.; Maheo, Y.; Berthier, Y. (2017-04-15). "Numerical analysis of contact stress and strain distributions for greased and ungreased high loaded oscillating bearings". Wear. 21st International Conference on Wear of Materials. 376–377, Part B: 1164–1175. doi:10.1016/j.wear.2016.11.037.
- Tomlinson, G. A. (1927-07-01). "The Rusting of Steel Surfaces in Contact". Proceedings of the Royal Society of London A: Mathematical, Physical and Engineering Sciences. 115 (771): 472–483. Bibcode:1927RSPSA.115..472T. doi:10.1098/rspa.1927.0104. ISSN 1364-5021.
- Schwack, F.; Prigge, F.; Poll, G. (October 2018). "Finite element simulation and experimental analysis of false brinelling and fretting corrosion". Tribology International. 126: 352–362. doi:10.1016/j.triboint.2018.05.013. ISSN 0301-679X.
- Almen, J.O. (1937). "Lubricants and False Brinelling of Ball and Roller Bearings". Mechanical Engineering. 59 (6): 415–422.
- Pittroff, Hans (1965). "Fretting Corrosion Caused by Vibration With Rolling Bearings Stationary". Journal of Basic Engineering. 87 (3): 713–723. doi:10.1115/1.3650657.
- Schwack, Fabian; Poll, Gerhard. "Service Life of Blade Bearings - Problems Faced in Service Life Estimation of Blade Bearings". ResearchGate. Retrieved 2017-06-27.
- Schwack, Fabian (2016). "Comparison of Life Calculations for Oscillating Bearings Considering Individual Pitch Control in Wind Turbines". Journal of Physics: Conference Series. 753 (753): 11. Bibcode:2016JPhCS.753k2013S. doi:10.1088/1742-6596/753/11/112013.
- Ecotrib (3, 2011 (2011). False brinelling standstill marks on roller bearings - Technische Informationsbibliothek (TIB). www.tib.eu. ISBN 9783901657382. Retrieved 2017-06-27.CS1 maint: numeric names: authors list (link)
- Stammler, Matthias (March 2015). "Blade bearings: Damage mechanisms and test strategies". CWD 2015: 371–379.
- Schwack, Fabian (2017). "Time-depending analyses of wear in oscillating bearings". STLE (72th).