Bushing (isolator)
A bushing or rubber bushing is a type of vibration isolator. It provides an interface between two parts, damping the energy transmitted through the bushing. A common application is in vehicle suspension systems, where a bushing made of rubber (or, more often, synthetic rubber or polyurethane) separates the faces of two metal objects while allowing a certain amount of movement. This movement allows the suspension parts to move freely, for example, when traveling over a large bump, while minimizing transmission of noise and small vibrations through to the chassis of the vehicle. A rubber bushing may also be described as a flexible mounting or antivibration mounting.
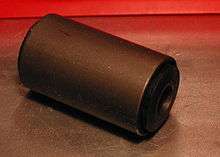
These bushings often take the form of an annular cylinder of flexible material inside a metallic casing or outer tube. They might also feature an internal crush tube which protects the bushing from being crushed by the fixings which hold it onto a threaded spigot. Many different types of bushing designs exist. An important difference compared with plain bearings is that the relative motion between the two connected parts is accommodated by strain in the rubber, rather than by shear or friction at the interface. Some rubber bushings, such as the D block for a sway bar, do allow sliding at the interface between one part and the rubber.
Advantages and disadvantages
The main advantage of a bushing, as compared to a solid connection, is less noise and vibration are transmitted. Another advantage is that they require little to no lubrication.
Disadvantages include that the rubber bushings can deteriorate quickly in the presence of oils (e.g., motor oil, mineral oil) and extreme heat and cold. Also, the flexibility of rubber also introduces an element of play in the suspension system. This may result in camber, caster, or toe changes in the wheels of the vehicle during high-load conditions (cornering and braking), adversely affecting the vehicle's handling. For this reason, a popular aftermarket performance upgrade is the replacement of rubber suspension bushings with bushings made of more rigid materials, such as polyurethane. Polyurethane bushings are also available for many vehicles with approximately the same characteristics as the manufacturers original bushings, but with greatly increased durability. This is useful on vehicles that have a reputation for wearing out standard rubber bushings, but for which harder bushings with increased harshness of ride are not wanted.
Applications
- As shock mounts
- In vehicles:
- Anti-roll bar (US Sway bar) links and mountings
- Shock absorber mountings
- Double wishbone suspension assemblies
- Gear stick for vehicles with a manual transmission
- Most high-speed inline internal combustion engines are prone to torsional vibration of their crankshafts; the straight six and straight eight engines being particularly prone to this problem due to their long crankshaft length. Although straight eight engines faded from the marketplace in the 1950s, many straight six engines have and still do feature crankshaft vibration damping utilizing rubber bushes. The 3,442 cc Jaguar XK 6-cylinder engine of 1948 and most subsequent versions of the ubiquitous Jaguar XK engine used a proprietary Metalastik vibration damper to protect their crankshafts from potentially damaging torsional vibrations. To quote William Heynes,[1] "The Metalastik damper consists of a steel plate to which is bonded, through a thick rubber disk, a malleable iron floating weight. Variations of the weight, rubber volume and mix, give these dampers a very wide field over which they can operate."
- In skateboards, bushings enable the tilting of the trucks, thus allowing the board to turn.
- In fastening, bushings are also used to transfer loads from a fastening to a much larger area in the underlying structure, the object being to reduce the strain on individual fibers within the underlying structure. (See also grommet.)
History
Charles E. Sorensen credits Walter Chrysler as being a leader in encouraging the adoption of rubber vibration-isolating mounts. In his memoir (1956), he says that, on March 10, 1932, Chrysler called at Ford headquarters to show off a new Plymouth model.
- "The most radical feature of his car was the novel suspension of its six-cylinder engine so as to cut down vibration. The engine was supported on three points and rested on rubber mounts. Noise and vibration were much less. There was still a lot of movement of the engine when idling, but under a load it settled down. Although it was a great success in the Plymouth, Henry Ford did not like it. For no given reason, he just didn't like it, and that was that. I told Walter that I felt it was a step in the right direction, that it would smooth out all noises and would adapt itself to axles and springs and steering-gear mounts, which would stop the transfer of road noises into the body. Today rubber mounts are used on all cars. They are also found on electric-motor mounts, in refrigerators, radios, television sets—wherever mechanical noises are apparent, rubber is used to eliminate them. We can thank Walter Chrysler for a quieter way of life. Mr. Ford could have installed this new mount at once in the V‑8, but he missed the value of it. Later Edsel and I persuaded him. Rubber mounts are now found also in doors, hinges, windshields, fenders, spring hangers, shackles, and lamps—all with the idea of eliminating squeaks and rattles."[2]
Lee Iacocca credits Chrysler's chief of engineering during that era, Frederick Zeder, with leading the effort.[3] Iacocca said that Zeder "was the first man to figure out how to get the vibrations out of cars. His solution? He mounted their engines on a rubber base."[3]
Chrysler's novel engine-mounting method was marketed as "Floating Power". Its basic idea soon became the conventional method throughout the automotive industry.
See also
References
- Heynes, WM. The Jaguar Engine, a paper presented to the Institution of Mechanical Engineers on 27 February 1953.
- Sorensen 1956, pp. 226–227 .
- Iacocca 1984, p. 149 .
Bibliography
- Iacocca, Lido A.; William Novak (1984), Iacocca: An Autobiography, Bantam Books, ISBN 978-0553051025, LCCN 84045174.
- Sorensen, Charles E.; with Williamson, Samuel T. (1956), My Forty Years with Ford, New York, New York, USA: Norton, LCCN 56010854. Various republications, including ISBN 9780814332795.
- DeSilva, C. W., "Vibration and Shock Handbook", CRC, 2005, ISBN 0-8493-1580-8
- Harris, C. M., and Peirsol, A. G. "Shock and Vibration Handbook", 2001, McGraw Hill, ISBN 0-07-137081-1