Toughness
In materials science and metallurgy, toughness is the ability of a material to absorb energy and plastically deform without fracturing.[1] One definition of material toughness is the amount of energy per unit volume that a material can absorb before rupturing. This measure of toughness is different from that used for fracture toughness, which describes load bearing capabilities of materials with flaws.[2] It is also defined as a material's resistance to fracture when stressed.
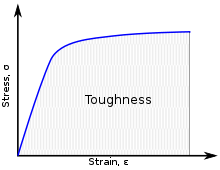
Toughness and strength
Toughness is related to the area under the stress–strain curve. In order to be tough, a material must be both strong and ductile. For example, brittle materials (like ceramics) that are strong but with limited ductility are not tough; conversely, very ductile materials with low strengths are also not tough. To be tough, a material should withstand both high stresses and high strains. Generally speaking, strength indicates how much force the material can support, while toughness indicates how much energy a material can absorb before rupturing.
Mathematical definition
Toughness can be determined by integrating the stress-strain curve.[1] It is the energy of mechanical deformation per unit volume prior to fracture. The explicit mathematical description is:[3]
where
- is strain
- is the strain upon failure
- is stress
Another definition is the ability to absorb mechanical energy up to the point of failure. The area under the stress-strain curve is called toughness.
If the upper limit of integration up to the yield point is restricted, the energy absorbed per unit volume is known as the modulus of resilience. Mathematically, the modulus of resilience can be expressed by the product of the square of the yield stress divided by two times the Young's modulus of elasticity. That is,
- Modulus of resilience = Yield stress2/2 (Young's modulus)
Toughness tests
The toughness of a material can be measured using a small specimen of that material. A typical testing machine uses a pendulum to strike a notched specimen of defined cross-section and deform it. The height from which the pendulum fell, minus the height to which it rose after deforming the specimen, multiplied by the weight of the pendulum is a measure of the energy absorbed by the specimen as it was deformed during the impact with the pendulum. The Charpy and Izod notched impact strength tests are typical ASTM tests used to determine toughness.
Unit of toughness
Tensile toughness (or, deformation energy, UT) is measured in units of joule per cubic metre (J·m−3) in the SI system and inch-pound-force per cubic inch (in·lbf·in−3) in US customary units.
1.00 N·m.m−3 ≃ 0.000145 in·lbf·in−3 and 1.00 in·lbf·in−3 ≃ 6.89 kN·m.m−3.
In the SI system, the unit of tensile toughness can be easily calculated by using area underneath the stress–strain (σ–ε) curve, which gives tensile toughness value, as given below:[4]
- UT = Area underneath the stress–strain (σ–ε) curve = σ × ε
- UT [=] Pa × ΔL/L = (N·m−2)·(unitless)
- UT [=] N·m·m−3
- UT [=] J·m−3
See also
References
- "Toughness", NDT Education Resource Center, Brian Larson, editor, 2001–2011, The Collaboration for NDT Education, Iowa State University
- Askeland, Donald R.,. The science and engineering of materials. Wright, Wendelin J., (Seventh ed.). Boston, MA. p. 208. ISBN 978-1-305-07676-1. OCLC 903959750.CS1 maint: extra punctuation (link)
- Soboyejo, W. O. (2003). "12.3 Toughness and Fracture Process Zone". Mechanical properties of engineered materials. Marcel Dekker. ISBN 0-8247-8900-8. OCLC 300921090.
- O.Balkan and H.Demirer (2010). "Polym. Compos". 31: 1285. ISSN 1548-0569. Cite journal requires
|journal=
(help)