Slewing bearing
A slewing bearing or slew[ing] ring is a rotational rolling-element bearing that typically supports a heavy but slow-turning or slow-oscillating load, often a horizontal platform such as a conventional crane, a swing yarder, or the wind-facing platform of a horizontal-axis windmill. (To "slew" means to turn without change of place.)
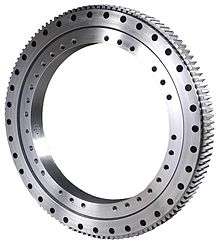
Compared to other rolling-element bearings, slewing bearings are thin in section and are often made in diameters of a metre or more; the slewing bearings on the Falkirk Wheel are 4 metres diameter and fit over a 3.5 metre axle.
Slewing bearings often use two rows of rolling elements. They often use three race elements, such as an inner ring and two outer ring "halves" that clamp together axially.
Slewing bearings are often made with gear teeth integral with the inner or outer race, used to drive the platform relative to the base.
As for other bearings that reciprocate, rather than rotating continuously, lubrication can be difficult. The oil wedge built up in a continuously rotating bearing is disrupted by the stop start motion of slewing. Instead, a hydrostatic bearing with pumped oil flow may be used.
Standards
The American Society of Mechanical Engineers (ASME) publishes the following Standard:
- ASME SRB-1 on Design, Installation, Maintenance, and Application of Ball Slewing Ring Bearings