Rail-Veyor
Rail-Veyor is a remote controlled, electrically powered light-rail haulage solution for surface and underground applications in the mining and aggregate industries. Rail-Veyor Technologies Global Inc. is a private Sudbury, Canada-based industrial bulk material handling and material haulage company that manufactures and installs Rail-Veyor systems.
Private | |
Industry | Mining, material handling, material hauling |
Founded | 1999 |
Founder | Risto Laamanen |
Headquarters | Sudbury, Ontario , |
Key people | Ron Russ, CEO Mike Dibble, Inventor Joe Capers, Inventor |
Website | Rail-Veyor |
History
Rail-Veyor's light-rail system was first demonstrated by its inventor, Mike Dibble, in conjunction with the Florida Institute of Phosphate Research from 1999-2001. Since then it has been installed commercially by Harmony Gold at its Phakisa Gold Mine in Free State, South Africa.[1] Canadian entrepreneur Risto Laamanen incorporated the business, secured the global distribution rights, and set up a second demonstration and test site with Vale S.A. at their Frood Stobie mine in Sudbury, Ontario, Canada in 2008.[2][3][4] Following successful testing of the system at the Frood Stobie test site, a Rail-Veyor system was installed at Vale's Copper Cliff Mine 114 Ore Body Mine and became operational in 2012,[5] with the intention of using the Rail-Veyor system as an enabling technology for rapid mine development and high speed production.[6]
Risto Laamanen died on July 7, 2009,[7] but the Laamanen family continue to be large investors in the private company, Rail-Veyor Technologies Global Inc., along with investors from Canada and the United States of America.
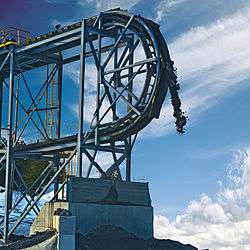
About
The Rail-Veyor system incorporates a remotely operated electrically powered series of two wheeled railcars driven by power stations located along on a light-rail track.[8] Because the cars are remotely operated and compact in size, they can be used as an enabling technology for rapid development and high speed production at the working face. The Rail-Veyor system can reduce capital costs and infrastructure, travelling below shafts and in spaces as small as 10 by 12 feet or 3.05 m by 3.66 m.[9] Using multiple train systems in tandem optimizes continuous material haulage.[10] The railcars can travel at variable speeds up to 18 mph, or 8 metres/second, and climb grades of 20%.[11] The company claims that the system combines the best features of conveyors, rail, and truck haulage, including travelling on 20% inclines, increased capacity and availability, reduced installation time, a small profile, and a short turning radius of 95 feet or 30 m.[12] The system is used for underground and surface applications in the mining and aggregate industries.
Awards
- 2013 Bell Canada Business Excellence Award for Innovation[13]
References
- Madlala, Ollie. "Harmony to install world-first railveyor system at new mine" Mining Weekly. Retrieved 2014-01-05.
- "Our History" Archived 2013-10-24 at the Wayback Machine Rail-Veyor. Retrieved 2014-01-05.
- (12 February 2013). "Profiles in Mining: Ron Russ" Skillings Mining Review. Retrieved 2014-01-05.
- Ulrichsen, Heidi. "Rail-Veyor to be demonstrated in Sudbury" Sudbury Mining Solutions Journal. Retrieved 2014-01-05.
- "Vale puts a breakthrough in mining to the test in Sudbury" Mining and Exploration. Retrieved 2014-01-05.
- "Harper Government Announces Clean Technology Projects in Ontario" Natural Resources Canada. Retrieved 2014-01-05.
- "Risto Elias Laamanen" The Globe and Mail. Retrieved 2014-01-05.
- Tarantola, Andrew. "This Robotic Mining Car Never Stops Hauling" Gizmodo. Retrieved 2014-01-05.
- "Miners take "rail-veyors" and robots to automated future" Reuters. Retrieved 2014-01-05.
- "Traveling New Ground" Retrieved 2014-01-05.
- Caulfield, Pete. "Equipment Roundup" Archived 2013-12-12 at the Wayback Machine Mining World. Retrieved 2014-01-05.
- (6 September 2012). "Vale adopts Rail-Veyor technology". International Mining.
- "Bell Business Excellence Awards 2013" Retrieved 2014-01-05.