Neck-through
Neck-through or neck-thru (or in full form neck through body) is a method of electric guitar or bass guitar construction that involves extending the piece (or pieces, in a laminate construction) of wood used for the neck through the entire length of the body, essentially making it the core of the body. The strings, fretboard, pickups and bridge are all mounted on this piece. So-called "ears" or "wings" (i.e. side parts of the body) are glued or laminated to the central "stick". The "wings" may be bookmatched in order to give a symmetrical appearance, and are often cut from one piece of wood.
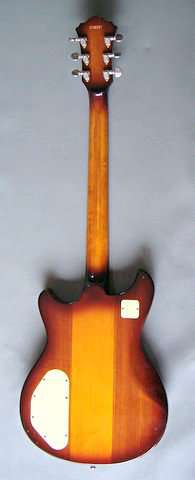
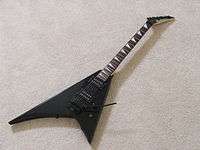
Alternative methods of construction are with a neck joint (body and neck are separate and either bolted on or glued in (set-in neck), or one-piece (body and neck are made out of a single piece of material).
History
The first electric bass guitar, the solid-body "Audiovox 736" created by Paul Tutmarc circa 1937, had a neck-through construction.
"The Log", a prototype solid-body guitar built by Les Paul in 1941, can be considered as a forerunner of neck-through designed instrument. Les Paul built the model using a recycled 4x4 fence post as the neck and body core, and mounted the disassembled parts of an Epiphone and Gibson archtop guitar onto it.
The 1952-57 Harmony H44 had this construction feature.
In 1956 Rickenbacker was one of the first guitar manufacturers to use the modern variant of this technique, although this was originally restricted exclusively to semi-hollowbody guitars.[1]
Advantages and disadvantages
Neck-through construction is significantly harder to mass-produce than bolt-on or set-in neck constructions and is primarily found on high-end guitars. It is somewhat more common in basses than in guitars. Neck-through construction allows easier access to upper frets, because there is no need for a heel — the thickened area of the neck where the body bolts onto it. Many musicians assert that neck-through construction provides greater sustain and allows the instrument to stay in tune longer.
Repairs to the neck are usually expensive and tedious. In many cases, it is usually easier to remove the old neck completely, either by taking the wings off and putting an entirely new core in, or by converting the guitar to a bolt-on or set neck by creating a heel and affixing the new neck to the core already in place, rather than to try to repair the neck itself. However, thanks to excellent stability and reaction to string tension and pressure, neck through guitars are often much more sturdy than many other guitars on the market.
Usage
This structure is used by many companies, including Parker Guitars, BC Rich, Yamaha, Cort Guitars, Ibanez (primarily on basses), Jackson, Alembic, Schecter, Carvin, ESP Guitars, and Rickenbacker. The Gibson Firebird and Thunderbird, which have had intermittent production, also sometimes use this technique, but are more commonly found as set-in neck guitars. This method of neck-to-body affixation is also popular with independent guitar builders, who can typically devote more time to such a labor-intensive neck joint than a mass-producing company could.
References
- Rickenbacker International Corporation: The Modern Era of the Electric Guitar, retrieved 14 June 2012