Hydrothermal carbonization
Hydrothermal carbonization (HTC) (also referred to as "aqueous carbonization at elevated temperature and pressure") is a chemical process for the conversion of organic compounds to structured carbons. It can be used to make a wide variety of nanostructured carbons, simple production of brown coal substitute, synthesis gas, liquid petroleum precursors and humus from biomass with release of energy. Technically the process imitates, within a few hours, the brown coal formation process (German "Inkohlung" literally "to coal process") which takes place in nature over enormously longer geological time periods of 50,000 to 50 million years. It was investigated by Friedrich Bergius and first described in 1913.[1]
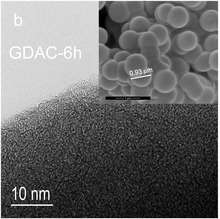
Motivation
The carbon efficiency of most processes to convert organic matter to fuel is relatively low. I.e. the proportion of carbon contained in the biomass, which is later contained in the usable end product is relatively low:
Process | Carbon efficiency |
---|---|
alcoholic fermentation | 67% |
gasification to H2 or CH4 | 60% |
gasification and Fischer-Tropsch synthesis | 50% |
anaerobic conversion to biogas | 50% |
wood charcoal production | 30% |
production of humus by composting | 5% to 10% |
In poorly designed systems the unused carbon escapes into the atmosphere as carbon dioxide, or when fermented as methane. Both gases are considered to be climate-damaging. In addition, heat is released in these processes, which is not generally used. Advanced modern system capture nearly all the gases and use the heat as part of the process or for district heating.
The problem with the production of biodiesel from oil plants is the fact that only the energy contained in the fruit can be used. If the entire plant could be used for fuel production, the energy yield could be increased by a factor of three to five with the same cultivation area when growing fast-growing plants such as willow, poplar, miscanthus, hemp, reeds or forestry, while simultaneously reducing energy, fertilizer and herbicide use, with the possibility of using - for current energy plant cultivation - poor soil. Hydrothermal carbonization makes it possible - similar to the biomass-to-liquid process - to use almost all of the carbon contained in the biomass for fuel generation. It is a new variation of an old field (biomass conversion to biofuel) that has recently been further developed in Germany.[2] It involves moderate temperatures and pressures over an aqueous solution of biomass in a dilute acid for several hours. The resulting matter reportedly captures 100% of the carbon in a "biocoal" powder that could provide feedsource for soil amendment (similar to biochar) and further studies in economic nanomaterial production.[3]
Process
Biomass is heated together with water to 180 °C in a pressure vessel, in particular vegetable material (in the following reaction equation, simplified as sugar with the formula C6H12O6. The pressure rises to about 1 MPa (10 bar). During the reaction, oxonium ions are also formed which reduce the pH to pH 5 and lower. This step can be accelerated by adding a small amount of citric acid.[4] In this case, at low pH values, more carbon passes into the aqueous phase. The effluent reaction is exothermic, that is, energy is released. After 12 hours, the carbon of the reactants is completely reacted, 90 to 99% of the carbon is present as an aqueous sludge of porous brown coal spheres (C6H2O) with pore sizes between 8 and 20 nm as a solid phase, the remaining 1 to 10% of carbon is either dissolved in the aqueous phase or converted to carbon dioxide. The reaction equation for the formation of brown coal is:
The reaction can be stopped in several stages with incomplete elimination of water, giving different intermediate products. After a few minutes, liquid intermediate lipophilic substances are formed, but their handling is very difficult because of their high reactivity. Subsequently, these substances polymerize and peat-like structures are formed, which are present as intermediates after about 8 hours.
Theoretically, the reaction with certain metal particles could be catalyzed, but these would be added very quickly with the products and lose their function.
Efficiency
As a result of the exothermic reaction of hydrothermal carbonization, about 3/8 of the calorific value of the biomass based on the dry mass is released (with a high lignin, resin and / or oil content at least 1/4). If the process is managed properly, it is possible to use this waste heat from wet biomass to produce dry biocoal and to use some of the converted energy for energy generation.
In a large-scale technical implementation of hydrothermal carbonization of sewage sludge, it has been shown that about 20% of the fuel energy content contained in 90% end-dried HTC coal is required to heat the process. Furthermore, approximately 5% of the generated energy content is necessary for electrical operation of the plant. It has proved particularly beneficial in the case of the HTC process that, with mechanical dehydration, more than 60% of the dry substance content can be achieved in the raw carbon, and thus the energy and equipment expenditure for the final drying of the coal is low compared to conventional drying methods of these slurries.[5]
Compared to sludge digestion with subsequent drying, the energy requirement of the HTC is lower by approximately 20% of the electrical energy and approximately 70% of the thermal energy. The amount of energy produced by the HTC as a storable coal is simultaneously 10% higher.[6] Compared to conventional thermal drying of sewage sludge, the HTC saves 62% of electricity and 69% of thermal energy due to its significantly simpler drainage.[7]
Benefits
An exothermic process design would be advantageous in which the carbon content remains biologically, chemically or thermally convertible without further oxidation of the biomass. This could lead to a specific reduction in CO2 release .
According to Markus Antonietti, the most important point is "... that one has a simple method of transforming atmospheric CO2 via the detour of biomass into a stable and safe storage form, a carbon sink." With hydrothermal carbonization, as well as with other methods for the coking of biomass, a large quantity of carbon could be stored decently all over the world. Essentially safer than the currently discussed liquid or gaseous sequestration of carbon dioxide. With sufficient chemical stability of the coal, it could also be used very well for the improvement of soils (see also Terra preta ).
The artificial humus could be used for the re- greening of eroded surfaces. Due to the increased plant growth in this way, additional carbon dioxide could be bound from the atmosphere so that a carbon efficiency of more than 1 or a negative CO2 balance could be achieved. The resulting carbon sludge could be used to burn or operate novel fuel cell types with a 60% efficiency, as currently being researched at Harvard University. In order to produce conventional fuels, the carbon-water mixture would have to be heated more intensively, so that so-called synthesis gas, a gas mixture of carbon monoxide and hydrogen, is formed:
This synthesis gas could be used to produce gasoline via the Fischer-Tropsch process. Alternatively, the liquid intermediates that are formed during the incomplete conversion of the biomass could be used for fuel and plastic production.
In addition, the resulting carbon mud can be briquetted and marketed as an environmentally friendly carbon dioxide-neutral "natural carbon" - Compared with the starting biomass, this can be dried by means of deposition or filtering or pressing with a lower energy consumption and, due to its higher energy content per volume or mass, reduce transport costs and require smaller storage areas.
An advantage of hydrothermal carbonization is that the usability of plant biomass is not restricted to plants with low moisture contents and the energy that can be obtained without carbon dioxide emission is not reduced by necessary drying measures or is usable directly for drying the end products. For example, even scarcely usable plant material, such as waste from gardens and urban green areas, can be used to produce energy,[8] carbon dioxide is also being saved, which, together with even more climate-damaging methane, would otherwise be produced by bacterial conversion of the biomass.
In recent years HTC was applied as upstream conditioning technology for phosphorus recovery from sewage sludge with the benefit of higher yields.[9]
Problems
The major problem in the production of synthesis gas from biomass is the formation of tar, which can be avoided during hydrothermal process management. However, it is not easy to see why this is the best way to process biocarbon. A biomass slurry should be decomposed into CO2 and H2 under supercritical conditions at 400 °C and a pressure of at least 221.2 bar (critical temperature of water is 374 °C), which requires a high energy input.
An appropriate process management as well as problems in the collection, transportation and storage of accumulated biomass are unresolved in this problem. These processes also require energy, which should be less than is released by hydrothermal carbonation.
An advantage over dry thermal processes of refining biofuels with low moisture content is not so obvious. Even at the end of the 19th century, a weakly pyrolysed charcoal, which still contains at least 4/5 of the calorific value of the wood, was propagated for thermal processes.
Current application intentions
In Relzow near Anklam (Mecklenburg-Western Pomerania), a hydrothermal carbonisation plant was officially inaugurated in the middle of November 2017 in "Innovation Park Vorpommern". According to the company, the HTC plant in Relzow represents a "new stage in the field of hydrothermal carbonisation" [6]. AVA is also the first company in the world to establish a HTC plant on industrial level in 2010.[7]
Already in Summer 2016 a HTC plant for the treatment of sewage sludge was put in operation in Jining/China to produce renewable fuel for the local coal fired power plant. According to the manufacturer TerraNova Energy, it is in continuous operation with an annual capacity of 14.000 tons.[10]
See also
External links
- Movie of commercial HTC installation by TerraNova Energy GmbH auf YouTube, abgerufen am 25. März 2019
- Hydrothermale Carbonisierung HTC auf kompostverband.ch, abgerufen am 22. Januar 2017.
- Max-Planck-Gesellschaft: Zauberkohle aus dem Dampfkochtopf auf mpg.de, abgerufen am 22. Januar 2017.
- Chemical reactions under high pressure Vorlesung von Friedrich Bergius anlässlich der Verleihung des Nobelpreises 1931, (PDF-Datei; 781 kB), auf nobelprize.org, abgerufen am 22. Januar 2017.
- Kraftstoff aus Orangen auf sueddeutsche.de, abgerufen am 22. Januar 2017.
- Weiterführende Informationen zum AVA-HTC-Reaktor mit interessanter Diskussion auf ithaka-journal.net, abgerufen am 22. Januar 2017.
- Official launch of the AVA HTC plant in Relzow November, 2017
- In 2010, AVA became the first company in the world to operate a HTC plant on an industrial scale In 2010
Literature
- Tobias Helmut Freitag: Hydrothermale Karbonisierung. Studienarbeit, Grin, 2011, ISBN 978-3-656-07822-7.
- X. J. Cui, M. Antonietti, S. H. Yu: Structural effects of iron oxide nanoparticles and iron ions on the hydrothermal carbonization of starch and rice carbohydrates. In: Small. 2 (6): 756-759, 2006.
- S. H. Yu, X. J. Cui, L. L. Li, K. Li, B. Yu, M. Antonietti, H. Colfen: From starch to metal/carbon hybrid nanostructures: Hydrothermal metal-catalyzed carbonization. In: Advanced Materials. 16 (18): 1636, 2004.
References
- Friedrich Carl Rudolf Bergius: Anwendung hoher Drucke bei chemischen Vorgängen und die Nachbildung des Entstehungsprozesses der Steinkohle. W. Knapp, Halle a.S. 1913, OCLC 250146190.
- Maria-Magdalena Titirici, Arne Thomas and Markus Antonietti, New J. Chem., 2007, 31, 787-789. "Back in the black: hydrothermal carbonization of plant material as an efficient chemical process to treat the CO2 problem?"
- Back in the black: hydrothermal carbonization of plant material as an efficient chemical process to treat the 2problem?
- Peter Brandt: Die „Hydrothermale Carbonisierung“: eine bemerkenswerte Möglichkeit, um die Entstehung von CO2 zu minimieren oder gar zu vermeiden? In: J. Verbr. Lebensm. 4 (2009): S. 151–154, doi:10.1007/s00003-009-0472-7.
- Marc Buttmann: Klimafreundliche Kohle durch HTC von Biomasse. (PDF; 7,0 MB). In: Chemie Ingenieur Technik, 2011, 83, 11, 1890-1896. Abgerufen am 4. Juli 2012.
- P. Jeitz, O. Deiss: Neue Wege in der Klärschlammaufbereitung. (PDF; 1,1 MB). In: Aqua & Gas. 2012, 4, 42-45. Abgerufen am 4. Juli 2012.
- T. Kläusli: Studie bestätigt Vorteile der hydrothermalen Carbonisierung von Klärschlamm. (PDF; 1,1 MB). In: Müll und Abfall. März 2014.
- Tobias Wittmann: Biomasse zu Brennstoff veredeln. Archived 2012-09-11 at Archive.today In: Energy 2.0. Ausgabe 01/2011.
- Deutsche Phosphor Plattform e.V. (Deutsche Phosphor Plattform e.V.). "TerraNova® Ultra Phosphorus Recovery Process" (PDF). www.deutsche-phosphor-plattform.de. Archived from the original (PDF) on 2018-10-17. Retrieved 2019-03-25. Check date values in:
|date=
(help) - Santos, Dorothee dos (2017-11-17). "Positive Zwischenbilanz für TerraNova Ultra Verfahren zur Klärschlammbehandlung". EUWID Neue Energie Nachrichten (in German). Retrieved 2019-03-26.