Game of Thrones Tapestry
The Game of Thrones Tapestry is a hand-woven tapestry which currently stands at 66 m (217 ft) long, which was opened to the public on 21 July 2017 at the Ulster Museum in Belfast, Northern Ireland.[1] Once finished, it will be longer than its inspiration, the Bayeux Tapestry, at 77 m (253 ft).[2] The tapestry tells the entire story of the television show, Game of Thrones. It consists of six 11 metre long panels of hand-woven fabric, and one 10.5 metre panel. The seven panels depict scenes from each episode of the aired seasons. After season 8 is aired in 2019, the tapestry is planned to grow to reflect that season's six episodes.[3]
Game of Thrones Tapestry | |
---|---|
![]() | |
Year | July 2017 |
Dimensions | 70 cm × 8210 cm (28 in × 3,230 in) |
Location | Ulster Museum Belfast |
Website | http://www.ireland.com/tapestry |
Season . Episode | Length (m) | Total length (m) | Total length (ft) |
---|---|---|---|
1 | 10.70 | 10.70 | 35.10 |
2 | 10.63 | 21.33 | 69.89 |
3 | 10.75 | 32.08 | 105.25 |
4 | 11.40 | 43.48 | 142.65 |
5 | 11.64 | 55.12 | 180.84 |
6 | 11.30 | 66.42 | 217.91 |
7.1 | 1.70 | 68.12 | 223.49 |
7.2 | 1.50 | 69.62 | 228.41 |
7.3 | 1.47 | 71.09 | 223.23 |
7.4 | 1.53 | 72.62 | 238.25 |
7.5 | 1.53 | 74.15 | 243.27 |
7.6 | 1.57 | 75.72 | 248.43 |
7.7 | 2.23 | 77.95 | 255.74 |
Campaign background
The Game of Thrones Tapestry is a campaign which celebrates Northern Ireland and its historic contribution to the legacy linen mills which once was the largest linen and textile industry of its time. At the end of the 19th century, it had been estimated that over 100,000 people in the north of Ireland were employed in the manufacture and decoration of linen.[4]
Today, the Irish linen and textile industry is much smaller, whereas a growing number of the Northern Irish have found direct or indirect employment in the Game of Thrones tourism industry.[5]
The tapestry was commissioned by Tourism Ireland and HBO.[6] Publicis London, the advertising agency, generated this campaign to help a global audience understand this shift in employment.
The tapestry was made from material which represents that of the late 18th century (linen) and a technique passed on from generations (embroidery). The tapestry was hand-embroidered by some of the last few people remaining in the industry in Northern Ireland.
Game of Thrones influence
Traditional tapestries tell the stories of times gone by and have represented history and heritage from as far back as 3rd Century BC. The typical medieval style of Game of Thrones, along with many iconic scenes, have been used to influence and craft the illustrative style of tapestry. As some garments worn in the show have been supplied by the Irish textile trade, the tapestry also contains these same woven yarns. The yarns used in the tapestry have been supplied by Thomas Ferguson and Co. Ltd of Banbridge in associations with the Irish Linen Guild.[7]
The style of characters has been carefully designed to reflect those from the show. Publicis London worked closely with HBO ensuring all characters were true to show and their role during that particular scene.[8] The tapestry has drawn some controversy around famous cameos and whether they have also been included.
In July 2017 the online website www.ireland.com/tapestry was launched. The site allows those who are not able to visit the tapestry, to see the entire tapestry in incredible detail. Users can scroll the entire length of the tapestry and even zoom in to see each individual stitch. The website was updated as each new section was woven. The site carefully plots the filming locations (Castle Ward, Shillanavogy Valley, Inch Abbey, Dark Hedges, Downhill Beach, Ballintoy Harbour, Cushendun Caves, Audley's Field Pollnagollum Caves) famous to Northern Ireland and presents further key facts within the show and each location. The site encourages users to share their favourite key scenes.
Manufacturing process
Creative design
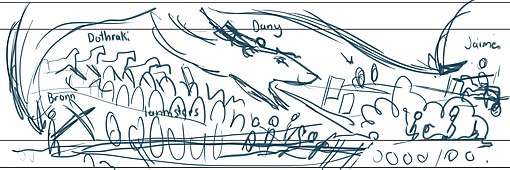
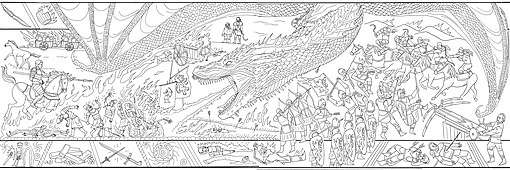
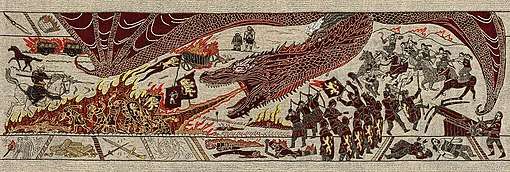
The tapestry began production with a set of avid Game of Thrones fans in Publicis London who employed a group of illustrators from an established animation/illustration studio in London called Jelly London. The illustrators, also huge fans, would start by creating an outline sketch using both pen, paper and digital touch screen. Sketches would be in black and white with the aim of identifying the correct style, tone of voice, scale and detail, for approval by HBO and Tourism Ireland. Once approved, the line drawings would pass through the colourisation phase. The colourisation phase is a lengthy process of converting the monochrome designs into a coloured piece of illustrated artwork. This process considers line widths, contrasts and resolution and also identifies the correct colour palette to use per section.
Weaving
The illustrated artwork is then passed to a hand-weaving specialist. The artists at Dash & Miller started the weaving process by setting up their loom to the required specification. Several tests were carried during the early stages of the campaign to determine the design density and range of colours possible. A specialist software is used to help translate the artwork into a format readable by the loom. Once programmed, the team at Dash & Miller begin weaving, using the colour palettes instructed by the loom. The average speed of weaving is 4 hours per metre. To capture the weekly episodes, a camera was installed above the loom: it was set to take regular shots during the weaving process, which were then stitched together to create a weekly time-lapse.
Embroidery
Once woven, the 11-metre section of tapestry would be shipped to Belfast to be embroidered. The Ulster Folk and Transport Museum, near Holywood, County Down, was used as the secret location for this work. Key areas on the tapestry was selected to be embroidered by a team of 30 stitchers working in groups of 6 and 9 at a time. The team included six staff from the museum.
The work relied heavily on the help of volunteers drawn from textiles guilds that have a thirty-year relationship with the museum. Members of the Northern Ireland Lace Guild, Patchwork Guild, and Embroidery Guild responded to the call for help with embroidery and joined staff at the museum to stitch on a daily basis for over three weeks. The volunteers ranged from a recent textiles graduate in her mid-twenties to an 82-year-old with a background in the garment stitching industry.
Loom setup and programming
Machine set-up and weaving
The jacquard loom used for weaving the tapestry is a hand-operated TC2 weaving loom[9] from Digital Weaving Norway. This loom is the latest technology in hand-woven jacquard design and allows the hand-weaver to create intricate and complex patterns by hand.
The black and white cotton warp threads first need to be wound onto the loom. This is done in 64m lengths, and the threads are wound onto the back beam of the loom. The warp has 60 threads per inch and is approximately 20 inches wide, each thread needs to be threaded through a heddle in the middle of the loom, and then through the reed at the front of the loom. This threading process is done by hand using a threading hook. Once the machine is threaded up, the warp threads are secured at the front of the loom onto the front beam. The loom then needs to be calibrated to advance the warp threads at the correct speed to weave 84 threads per inch.
To begin the weaving process, Dash & Miller weave 1 or 2 inches of plain weave at the beginning of the warp. This spaces out the warp threads properly and also evens out any tension issues. They can then begin weaving the tapestry, passing the 3 colours of thread by hand through the shed created by lifting the warp threads up and down. The computer controls which threads are lifted up and down, but the weft yarns are passed through the shed by hand. Weaving builds up at a rate of approximately 11 inches per hour, and the weaving is stored on the cloth storage beam at the front of the weaving loom.
Once the weaving is completed, they weave another 1 or 2 inch plain weave border before cutting the weaving off the loom, ensuring the warp threads are still threaded so they can tie on and begin the process again for the next panel.
CAD design and colour palettes
Using specialist weaving software from Pointcarre, the illustrators' artwork first needs to be calibrated for the jacquard loom, taking into consideration the weave construction and warp and weft yarns. The warp yarns are 2/30NE Cotton in black and white end-on-end, and the weft yarns are 1/10NM Flax and Linen.
The construction of the fabric are combinations of double-cloth and double-faced satins and sateen structures over 4 ends. The combinations of 3/1 and 1/3 satin structures, together with blending of warp and weft colours allow us to create different shades within a colour spectrum that bring depth and intricacy to the weave.
The illustrators' artwork is converted into a weave file by first defining the colours within the 4 colour palettes. The weave uses 3 weft colours throughout the piece, and this is split into colour palette in the following way:

- Colour palette 1: Natural Linen, Red and Blue Flax
- Colour palette 2: Natural Linen, Red and Green Flax
- Colour palette 3: Natural Linen, Green and Blue Flax
- Colour palette 4: Natural Linen, Red and Yellow Flax
During the weaving process Dash & Miller blend 3 colours together in the weft, so the illustrators clearly mark which sections of the design should be woven in each colour palette. They then manually swap between colour palette during the weaving process.
The weave has 84 threads per cm in the weft, and to ensure the scale is kept true to the designs the artwork then needs to be stretched and rotated. The CAD is stretched by 140% to allow the weaving to come out at the same scale as the original illustrators artwork. The artwork is rotated by 90 degrees counter-clockwise so that the piece can be woven as a continuous length on the loom.
Once the artwork has been scaled and the colours defined, Dash & Miller allocate weave structures to each colour in the CAD using Pointcarre Jacquard software. Each colour within the 4 colour palettes has its own weave structure. Dash & Miller also add in borders and selvedge to the weave to ensure clean edges to the design. Once the weave file has been generated, the computer is able to read the pattern to begin hand-weaving.
Thomas Fergusons Irish Linen
Fergusons was first established in Banbridge, County Down, for the hand-weaving of linen fabric. In 1867 the firm introduced power driven jacquard looms for the weaving of linen damask. John England (Banbridge) Ltd, since 2015 a sister company of Fergusons, regularly supplies fabrics for major theatrical and film productions, including Game of Thrones.
Jacquard looms
The loom used to create the panels is a small modern version of that developed by Frenchman Joseph Marie Jacquard, the son of a Lyonnais silk weaver, in 1804. His development based on earlier work by fellow Frenchmen Basile Bouchon in 1725, Jean Baptiste Falcon in 1728, and Jacques de Vaucanson in 1741. A jacquard loom is one in which a series of punched cards each corresponds to a row of the design to be woven, allowing for a greater definition of motifs. The punched cards operate a mechanism attached to the loom, controlling the pick-up of weft threads as the design evolves. In the case of the Game of Thrones Tapestry, it has allowed the weavers to introduce a rich palette of colours and considerable level of detail throughout the work.
Jacquard looms have often been credited with inspiring the development of the very first computers. The English mathematician, engineer, and inventor Charles Babbage (1791–1871) is believed to have been inspired by jacquard loom mechanisms in his development of the first digital programmable computer.
References
- Campbell, Felicity (25 July 2017). "Northern Ireland unveils giant Game of Thrones tapestry". The National. Retrieved 18 August 2017.
- Elderkin, Beth (20 July 2017). "This Giant, Breathtaking Game Of Thrones Tapestry Weaves Through The Entire Series". Gizmodo. Retrieved 18 August 2017.
- "Game of Thrones touring exhibition to open in Belfast". Winter is Coming. 11 December 2018.
- "The Belfast linen industry - OpenLearn - Open University". www.open.edu. Retrieved 17 August 2017.
- "What has Game of Thrones done for Northern Ireland? | Ulster Craic".
- "Tourism Ireland Launch New Game Of Thrones Campaign In UK". Hospitality Ireland. 17 August 2017. Retrieved 18 August 2017.
- "Winter is looming as Game Of Thrones tapestry goes on show at Ulster Museum". Irish Examiner. 23 July 2017. Retrieved 18 August 2017.
- Diaz, Ann-Christine (18 July 2017). "See the Entire 'Game of Thrones' Saga in One Massive Tapestry". creativity-online.com. Retrieved 18 August 2017.
- "TC2 Loom". Tronrud Engineering. Vibeke Vestby. Retrieved 10 August 2017.