Factory automation infrastructure
Factory automation infrastructure is a more recently coined phrase that is used to describe the process of incorporating automation into the manufacturing process of end products.[1] With this infrastructure, the manufacturing environment is defined by its ability to manufacture and/or assemble goods chiefly by machines, integrated assembly lines, and robotic arms. The automated environments are also defined by their coordination with (and usually their systematic integration with) the required automatic equipment to form a complete system. The intention of factory automation is to decrease the risks associated with laborious and dangerous work faced by human workers.[2] This system is essentially a solution for the automation and manufacturing of a particular production process of an intended output and/or end product.
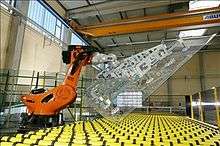
Automation
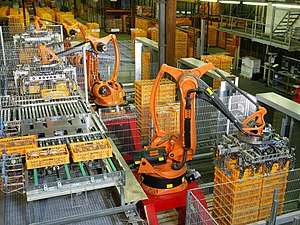
The Automation process is a widely accepted form of production that has made great leaps and bounds in the production process as a whole. Automation has led to the production of sophisticated parts in similar or higher output qualities with only little quality fluctuation.[3] It can also help cut the overall manufacturing costs and create safer working environment for workers.[1] The use of automation in the manufacturing process started by using such technologies as the pneumatic and hydraulic systems for use in applications where their mechanical advantages could be used to utilize a production for higher output quality and efficiency. We have since created a complex and highly integrated systems composed of many different technologies and innovative procedures controlled under High Language programming environments with sophisticated operation drivers. These drivers are often running languages that support 6, 7, and 8 axis controls for sophisticated robotics.
Robotic arm
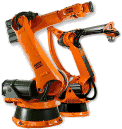
A robotic arm is a type of mechanical arm, usually programmable, with similar functions to a human arm; the arm may be the sum total of the mechanism or may be part of a more complex robot. The links of such a manipulator are connected by joints allowing either rotational motion (such as in an articulated robot) or transnational (linear) displacement. The links of the manipulator can be considered to form a kinematic chain. The terminus of the kinematic chain of the manipulator is called the end effect or and it is analogous to the human hand.
Advantages and disadvantages
The main advantages of automation are:
- Increased through output or productivity.
- Improved quality or increased predictability of quality.
- Improved robustness (consistency), of processes or product.
- Increased consistency of output.
- Reduced direct human labor costs and expenses.
- The following methods are often employed to improve productivity, quality, or robustness.
- Install automation in operations to reduce cycle time.
- Install automation where a high degree of accuracy is required.
- Replacing human operators in tasks that involve hard physical or monotonous work.[17]
- Replacing humans in tasks done in dangerous environments (i.e. fire, space, volcanoes, nuclear facilities, underwater, etc.)
- Performing tasks that are beyond human capabilities of size, weight, speed, endurance, etc.
- Economic improvement: Automation may improve in economy of enterprises, society or most of humanity. For example, when an enterprise invests in automation, technology recovers its investment; or when a state or country increases its income due to automation like Germany or Japan in the 20th Century.
- Reduces operation time and work handling time significantly.
- Frees up workers to take on other roles.
- Provides higher level jobs in the development, deployment, maintenance and running of the automated processes.
The main disadvantages of automation are:
- Security Threats/Vulnerability: An automated system may have a limited level of intelligence, and is therefore more susceptible to committing errors outside of its immediate scope of knowledge (e.g., it is typically unable to apply the rules of simple logic to general propositions).
- Unpredictable/excessive development costs: The research and development cost of automating a process may exceed the cost saved by the automation itself.
- High initial cost: The automation of a new product or plant typically requires a very large initial investment in comparison with the unit cost of the product, although the cost of automation may be spread among many products and over time.
- In manufacturing, the purpose of automation has shifted to issues broader than productivity, cost, and time
References
- Dotoli, Mariagrazia; Fay, Alexander; Miśkowicz, Marek; Seatzu, Carla (2019-08-29). "An overview of current technologies and emerging trends in factory automation". International Journal of Production Research. 57 (15–16): 5047–5067. doi:10.1080/00207543.2018.1510558. ISSN 0020-7543.
- Richards, Dale (2017-03-14). "Escape from the factory of the robot monsters: agents of change". Team Performance Management: An International Journal. 23 (1/2): 96–108. doi:10.1108/TPM-10-2015-0052. ISSN 1352-7592.
- Marinoudi, Vasso; Sørensen, Claus G.; Pearson, Simon; Bochtis, Dionysis (2019). "Robotics and labour in agriculture. A context consideration". Biosystems Engineering. 184: 111–121. doi:10.1016/j.biosystemseng.2019.06.013.