Engineering disasters
Shortcuts in engineering design can lead to engineering disasters. Engineering is the science and technology used to meet the needs and demands of society.[1] These demands include buildings, aircraft, vessels, and computer software. In order to meet society’s demands, the creation of newer technology and infrastructure must be met efficiently and cost-effectively. To accomplish this, managers and engineers have to have a mutual approach to the specified demand at hand. This can lead to shortcuts in engineering design to reduce costs of construction and fabrication. Occasionally, these shortcuts can lead to unexpected design failures.
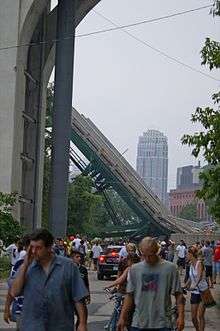
Importance of safety
In the field of engineering, the importance of safety is emphasized. Learning from past engineering failures and infamous disasters such as the Challenger explosion brings the sense of reality to what can happen when appropriate safety precautions are not taken. Safety tests such as tensile testing, finite element analysis (FEA), and failure theories help provide information to design engineers about what maximum forces and stresses can be applied to a certain region of a design. These precautionary measures help prevent failures due to overloading and deformation.[2]
Background of failure
Failure occurs when a structure or device has been used past the limits of design that inhibits proper function.[3] If a structure is designed to only support a certain amount of stress, strain, or loading and the user applies greater amounts, the structure will begin to deform and eventually fail. Several factors contribute to failure including a flawed design, improper use, financial costs, and miscommunication.
Failure due to static loading
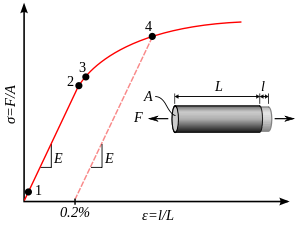
Static loading is when a force is applied slowly to an object or structure. Static load tests such as tensile testing, bending tests, and torsion tests help determine the maximum loads that a design can withstand without permanent deformation or failure. Tensile testing is common when calculating a stress-strain curve which can determine the yield strength and ultimate strength of a specific test specimen.
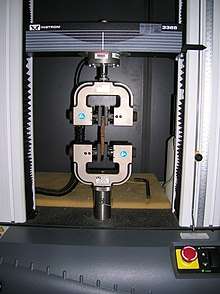
The specimen is stretched slowly in tension until it breaks, while the load and the distance across the gage length are continuously monitored. A sample subjected to a tensile test can typically withstand stresses higher than its yield stress without breaking. At a certain point, however, the sample will break into two pieces. This happens because the microscopic cracks that resulted from yielding will spread to large scales. The stress at the point of complete breakage is called a material’s ultimate tensile strength.[4] The result is a stress-strain curve of the material's behavior under static loading. Through this tensile testing, the yield strength is found at the point where the material begins to yield more readily to the applied stress, and its rate of deformation increases.[5]
Failure due to fatigue
When a material undergoes permanent deformation from exposure to radical temperatures or constant loading, the functionality of the material can become impaired.[6][7] This time–dependent plastic distortion of material is known as creep. Stress and temperature are both major factors of the rate of creep. In order for a design to be considered safe, the deformation due to creep must be much less than the strain at which failure occurs. Once the static loading causes the specimen to surpass this point the specimen will begin permanent, or plastic, deformation.[7]
In mechanical design, most failures are due to time-varying, or dynamic, loads that are applied to a system. This phenomenon is known as fatigue failure. Fatigue is known as the weakness in a material due to variations of stress that are repeatedly applied to said material.[8] For example, when stretching a rubber band to a certain length without breaking it (i.e. not surpassing the yield stress of the rubber band) the rubber band will return to its original form after release; however, repeatedly stretching the rubber band with the same amount of force thousands of times would create micro-cracks in the band which would lead to the rubber band being snapped. The same principle is applied to mechanical materials such as metals.[5]
Fatigue failure always begins at a crack that may form over time or due to the manufacturing process used. The three stages of fatigue failure are:
- 1.) Crack initiation- when repeated stress creates a fracture in the material being used
- 2.) Crack propagation- when the initiated crack develops in the material to a larger scale due to tensile stress.
- 3.) Sudden fracture failure- caused by unstable crack growth to the point where the material will fail
Note that fatigue does not imply that the strength of the material is lessened after failure. This notion was originally referred to a material becoming "tired" after cyclic loading.[5]
Failure due to miscommunication
Engineering is a precise discipline and in order to be precise, communication among project developers is pertinent for a successful product. There are several forms of miscommunication that can lead to a flawed design in a system. There are various fields of engineering that have to intercommunicate when working toward a mutual goal. These fields include civil, electrical, mechanical, industrial, chemical, biological, and environmental engineering. When creating a modern automobile, electrical engineers, mechanical engineers, and environmental engineers are required to work together to produce a fuel-efficient, durable product for consumers. If engineers do not adequately communicate among one another, a potential design could have flaws and be unsafe for consumer purchase. Engineering disasters can be a result of such miscommunication. Such disasters include the 2005 levee failures in Greater New Orleans, Louisiana during Hurricane Katrina, the Space Shuttle Columbia disaster, and the Hyatt Regency walkway collapse.[9][10][11]
An excellent example of this is the Mars Climate Orbiter. "The primary cause of the orbiter's violent demise was that one piece of ground software supplied by Lockheed Martin produced results in a United States customary unit, contrary to its Software Interface Specification (SIS), while a second system, supplied by NASA, expected those results to be in SI units, in accordance with the SIS." Lockheed Martin and the prime contractor spectacularly failed to communicate.
Failure due to software
Software has played a role in many high-profile disasters.
- Ariane 5 Flight 501
- Mars Climate Orbiter
- TAURUS — UK share settlement system and dematerialised central share depository.
- Therac-25 — A radiation therapy machine responsible for six overdoses due to faulty software.
- Failure at Dharan — Patriot Missile clock issue.
Failure due to systems engineering
- Lion Air Flight 610 and Ethiopian Airlines Flight 302 — Faulty "MCAS" system on the Boeing 737 MAX[12]
Infamous disasters in engineering
Engineering products and inventions are utilized everyday including computers, microwaves, and elevators. A broken microwave can have limited consequences; however, when larger projects such as infrastructures and airplanes fail, multiple people can be affected which leads to an engineering disaster. A disaster is defined as a calamity that results in significant damage which may include the loss of life.[13] Large-scale engineering disasters are recorded in the history books. Just like any other mistake, these disasters become reminders and guidelines of how to improve and not repeat the same mistakes. In-depth observations and post-disaster analysis have been documented to a large extent to help prevent similar disasters from occurring.
Infrastructure
Tay Bridge Disaster (1879)
Quebec Bridge collapse (1907)
Tacoma Narrows Bridge collapse (1940)
Hyatt Regency Hotel walkway collapse (1981)
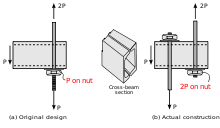
On the night of July 17, 1981, in Kansas City, Missouri, United States, two suspended walkways of the Hyatt Regency Hotel collapsed, killing 114 people and injuring 200 more. During this calamity, the hotel was hosting a dance competition. There were numerous competition attendants and observers standing and dancing on the suspended walkways when connections supporting the ceiling rods that hoisted both the second and fourth floor walkways across the atrium failed and collapsed onto the crowded first floor atrium below.[14]
During investigation after the walkway collapse, architectural engineer Wayne G. Lischka noticed a substantial alteration of the original design. The fabricator constructed a double-rod support system rather than the originally designed single-rod system without approval of the engineering design team. In doing so, the created support beams doubled the loading on the connector which resulted in the failure of the walkway. It was documented that even the single-rod system would have barely supported the expected load and would not have met Kansas City Building Code standards.[14]
The final analysis of the damage had several conclusions reported including:
- The maximum load capacity of the fourth floor walkway was only 53% the maximum load capacity of Kansas City Building Code standards
- The fabrication alterations from the original design doubled the load that was received by the fourth floor walkway
- The deformation and distortion of the fourth floor hanger rods support the notion that the collapse began at that point
- No evidence that the quality of construction or material selection played a role in the walkway collapse.[9]
Aeronautics
Challenger explosion (1986)
The Space Shuttle Challenger disaster occurred on January 28, 1986, when the NASA Space Shuttle orbiter Challenger (OV-099) (mission STS-51-L) broke apart 73 seconds into its flight, leading to the deaths of its seven crew members. Disintegration of the vehicle began after an O-ring seal in its right solid rocket booster (SRB) failed at liftoff.
Columbia disaster (2003)
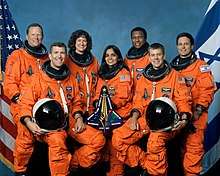
The Space Shuttle Columbia (OV-102) disaster occurred on February 1, 2003 during the final leg of STS-107. While reentering Earth's atmosphere over Louisiana and Texas the shuttle unexpectedly disintegrated, resulting in the deaths of all seven astronauts on board. The cause was later discovered to be damage to thermal shielding tiles from impact with a falling piece of foam insulation from an external tank during the January 16 launch. It was the seventh known instance of this particular piece breaking free during launch.[15] As the shuttle re-entered Earth's atmosphere at a speed of Mach 23, the wing experienced temperatures of 2,800 °F (1,540 °C). The damage from the insulation strike experienced during launch proved fatal as the shuttle disintegrated during the mission return.[11] NASA's investigation team found melted aluminum on the thermal tiles and inside edges of the left wing of the spacecraft, supporting the notion that the Columbia's destruction was due to hot gases that penetrated the damaged spot on the wing.[16]
Roger L. M. Dunbar of New York University and Raghu Garud of Pennsylvania State University procured a case description of what missteps NASA had taken that led to the Columbia spacecraft catastrophe. Mission control deemed that foam shedding was a not a safety factor prior to launch, believed damage of the shuttle panels were not a significant issue which in turn delayed analysis on damages as of January 17, 2003, and denied mission action request between January 18 and 19. It was not until January 24, 2003, that mission control had classified the damage as a problematic issue. These missteps in communication between mission control and the debris assessment team inhibited a proper examination of the damages to the spacecraft.[11]
Vessels
Liberty ships in WWII
Early Liberty ships suffered hull and deck cracks, and a few were lost to such structural defects. During World War II, there were nearly 1,500 instances of significant brittle fractures. Three of the 2,710 Liberties built broke in half without warning. In cold temperatures the steel hulls cracked, resulting in later ships being constructed using more suitable steel.
Steamboat Sultana (1865)
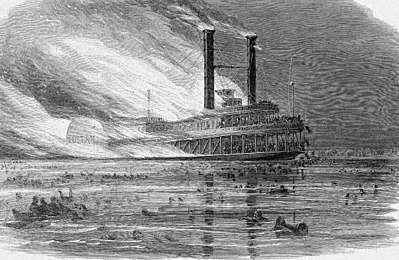
On the night of April 26, 1865, the passenger steamboat Sultana exploded on the Mississippi River seven miles (11 km) north of Memphis, Tennessee. This maritime disaster is categorized as the worst in United States history. The explosion resulted in the loss of 1,547 lives, surpassing the total number of deaths caused by the sinking of Titanic (which, despite New York being the Titanic's intended destination, is not classified as a US maritime disaster since it did not involve a United States - flagged vessel and did not occur in US territorial waters). Sultana was overcrowded due to a soldier-prisoner exchange towards the end of the American Civil War. The overcrowding contributed significantly to the high death toll. Another reason for the high death toll was the steamer's mostly-wood construction, which was documented to have been completely engulfed in flames approximately seven minutes after the explosion. The explosion happened around midnight which was when the Mississippi River was at flood stage. It was documented that the single metal lifeboat on board Sultana was thrown from the upper deck, landing on several people swimming from the steamer, resulting in further deaths.[17]
The disaster was believed to be the result of a repaired boiler explosion that led to the explosion of two of the three other boilers. The initial boiler had been previously found to have had a leak and was improperly repaired by boilermaker R. G. Taylor due to orders from Captain J. Cass Mason because of time constraints in Vicksburg, Mississippi. While chief engineer Nathan Wintringer approved the repaired boiler, Taylor stated that the boiler could not be considered safe since the boiler appeared to be burned from being worked on with too little water. [17] Traveling along the Mississippi River, the boiler exploded causing fire to spread throughout the steamer. The fire on board led to the collapse of both of Sultana's smokestacks, killing many passengers. Sultana's captain died with the ship.[18]
See also
- Industrial disasters
- List of structural failures and collapses
- Nuclear and radiation accidents
- List of spaceflight-related accidents and incidents
- List of maritime disasters
- Structural failure
- Normalization of deviance
References
- "Engineering." Definition of in Oxford Dictionaries (British & World English). N.p., n.d. Web. 22 Feb. 2013.
- Dax, Mark (Dec 1997). "Failure Analysis Prevents Disaster Reoccurance". R&D Magazine. EBSOhost.com: 30–31.
- "Failure." Definition of in Oxford Dictionaries (British & World English). N.p., n.d. Web. 23 Feb. 2013.
- Doehring, James; Fritsky, Lauren. "What Is a Static Load?". WiseGeek. Missing or empty
|url=
(help) - Norton, Robert L. (2011). Machine Design: An Integrated Approach. Boston: Prentice Hall.
- "CreepAbout Our Definitions: All Forms of a Word (noun, Verb, Etc.) Are Now Displayed on One Page." Merriam-Webster. Merriam-Webster, n.d. Web. 23 Feb. 2013.
- Hibbeler, R. C. (2011). Mechanics of Materials. Boston: Prentice Hall.
- "Fatigue." Definition of in Oxford Dictionaries (British & World English). N.p., n.d. Web. 21 Feb. 2013
- Marshall, Richard D. (1982). "Investigation of the Kansas City Hyatt Regency Walkways Collapse". U.S. Dept. Of Commerce, National Bureau of Standards. Washington, D.C.
- Carl Strock. "Defense.gov News Transcript: Defense Department Special Briefing on Efforts to Mitigate Infrastructure Damage from Hurricane Katrina". United States Department of Defense. Archived from the original on 2012-12-31. Retrieved 22 Feb 2013.
- Dunbar, R. L. M.; R., Garud (2009). "Distributed Knowledge and Indeterminate Meaning: The Case of the Columbia Shuttle Flight". Organization Studies. 30 (4): 397–421. doi:10.1177/0170840608101142.
- https://www.bbc.co.uk/news/av/business-47821827/boeing-737-max-mcas-anti-stall-system-explained
- "Disaster." Definition of in Oxford Dictionaries (British & World English). N.p., n.d. Web. 22 Feb. 2013.
- "Hyatt Regency Walkway Collapse." ENGINEERING.com. N.p., n.d. Web. 22 Feb. 2013.
- Columbia Accident Investigation Board, Report Volume 1, August 2003
- "Molten Aluminum found on Columbia's thermal tiles". USA Today. Associated Press. March 4, 2003. Retrieved February 15, 2013
- Berryman, J.O.; Potter; Oliver, S. (May 1988). "The Ill-Fated Passenger Steamer Sultana: An Inland Maritime Mass Disaster of Unparalleled Magnitude" (PDF). Journal of Forensic Sciences. JFSCA. 33 (3): 842–850. doi:10.1520/JFS12500J.
- Expedition Journal Stephen Ambrose May. "Disaster on the Mississippi: The Sultana Tragedy." National Geographic. National Geographic Society, Web. 22 Feb. 2013.