Electromagnetically induced acoustic noise
Electromagnetically induced acoustic noise (and vibration), electromagnetically excited acoustic noise, or coil whine is audible sound directly produced by materials vibrating under the excitation of electromagnetic forces. Some examples of this noise include the mains hum, hum of transformers, the whine of some rotating electric machines, or the buzz of fluorescent lamps. The hissing of high voltage transmission lines is due to corona discharge, not magnetism.
The phenomenon is also called audible magnetic noise[1], electromagnetic acoustic noise, or electromagnetically-induced acoustic noise [2], or more rarely, electrical noise [3], or "coil noise", depending on the application. The term electromagnetic noise is generally avoided as the term is used in the field of electromagnetic compatibility, dealing with radio frequencies. The term electrical noise describes electrical perturbations occurring in electronic circuits, not sound. For the latter use, the terms electromagnetic vibrations[4] or magnetic vibrations [5], focusing on the structural phenomenon are less ambiguous.
Acoustic noise and vibrations due to electromagnetic forces can be seen as the reciprocal of microphonics, which describes how a mechanical vibration or acoustic noise can induce an undesired electrical perturbation.
General explanation
Electromagnetic forces can be defined as forces arising from the presence of an electromagnetic field (electrical field only, magnetic field only, or both).
Electromagnetic forces in the presence of a magnetic field include equivalent forces due to Maxwell stress tensor, magnetostriction and Lorentz force (also called Laplace force)[6]. Maxwell forces, also called reluctances forces, are concentrated at the interface of high magnetic reluctivity changes, e.g. between air and a ferromagnetic material in electric machines; they are also responsible of the attraction or repulsion of two magnets facing each other. Magnetostriction forces are concentrated inside the ferromagnetic material itself. Lorentz or Laplace forces act on conductors plunged in an external magnetic field.
Equivalent electromagnetic forces due to the presence of an electrical field can involve electrostatic, electrostrictive and reverse piezoelectric effects.
These phenomena can potentially generate vibrations of the ferromagnetic, conductive parts, coils and permanent magnets of electrical, magnetic and electromechanical device, resulting in an audible sound if the frequency of vibrations lies between 20 Hz and 20 kHz, and if the sound level is high enough to be heard (e.g. large surface of radiation and large vibration levels). Vibration level is increased in case of a mechanical resonance, when electromagnetic forces match with a structural mode natural frequency of the active component (magnetic circuit, electromagnetic coil or electrical circuit) or of its enclosure.
The frequency of the noise depends on the nature of electromagnetic forces (quadratic or linear function of electrical field or magnetic field) and on the frequency content of the electromagnetic field (in particular if a DC component is present or not).
Electromagnetic noise and vibrations in electric machines
Electromagnetic torque, which can be calculated as the average value of the Maxwell stress tensor along the airgap, is one consequence of electromagnetic forces in electric machines. As a static force, it does not create vibrations nor acoustic noise. However torque ripple (also called cogging torque for permanent magnet synchronous machines in open circuit), which represents the harmonic variations of electromagnetic torque, is a dynamic force creating torsional vibrations of both rotor and stator. The torsional deflection of a simple cylinder cannot radiate efficiently acoustic noise, but with particular boundary conditions the stator can radiate acoustic noise under torque ripple excitation[7]. Structure-borne noise can also be generated by torque ripple when rotor shaft line vibrations propagate to the frame[8] and shaft line.
Some tangential magnetic force harmonics can directly create magnetic vibrations and acoustic noise when applied to the stator teeth: tangential forces create a bending moment of the stator teeth, resulting in radial vibrations of the yoke [9].
Besides tangential force harmonics, Maxwell stress also includes radial force harmonics responsible for radial vibrations of the yoke, which in turn can radiate acoustic noise.
Electromagnetic noise and vibrations in passive components
Inductors
In inductors, also called reactors or chokes, magnetic energy is stored in the airgap of the magnetic circuit, where large Maxwell forces apply. Resulting noise and vibrations depend on airgap material and magnetic circuit geometry [10].
Transformers
In transformers magnetic noise and vibrations are generated by several phenomena depending on the load case which include Lorentz force on the windings[11], Maxwell forces in the joints of the laminations, and magnetostriction inside the laminated core.
Capacitors
Capacitors are also subject to large electrostatic forces. When the capacitor voltage/current waveform is not constant and contains time harmonics, some harmonic electric forces appear and acoustic noise can be generated[12]. Ferroelectric capacitors also exhibit a piezoelectric effect that can be source of audible noise. This phenomenon is known as the "singing capacitor" effect[13].
Resonance effect in electrical machines
In radial flux rotating electric machines, resonance due to electromagnetic forces is particular as it occurs at two conditions: there must be a match between the exciting Maxwell force and the stator or rotor natural frequency, and between the stator or rotor modal shape and the exciting Maxwell harmonic wavenumber (periodicity of the force along the airgap)[14].
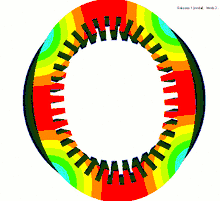
As an example a resonance with the elliptical modal shape of the stator can occur if the force wavenumber is 2. Under resonance conditions, the maxima of the electromagnetic excitation along the airgap and the maxima of the modal shape displacement are in phase.
Numerical simulation
Methodology
The simulation of electromagnetically induced noise and vibrations is a multiphysic modeling process carried in three steps:
- calculation of the electromagnetic forces
- calculation of the resulting magnetic vibrations
- calculation of the resulting magnetic noise
It is generally considered as a weakly coupled problem: the deformation of the structure under electromagnetic forces is assumed not to change significantly the electromagnetic field distribution and the resulting electromagnetic stress.
Application to electric machines
The assessment of audible magnetic noise in electrical machines can be done using three methods:
- using dedicated electromagnetic and vibro-acoustic simulation software (e.g. MANATEE [15])
- using electromagnetic (e.g. Flux,[16] Jmag,[17] Maxwell,[18] Opera[19]), structural (e.g. Ansys Mechanical, Nastran, Optistruct) and acoustic (e.g. Actran, LMS, Sysnoise) numerical software together with dedicated coupling methods
- using multiphysics numerical simulation software environment (e.g. Comsol Multiphysics[20], Ansys Workbench[21])
Examples of device subject to electromagnetic noise and vibrations
Static devices
Static devices include electrical systems and components used in electric power storage or power conversion such as
- inductors
- transformers[22]
- power inverters
- capacitors
- resistors: the braking resistors of electric trains, used to dissipate electrical power when the catenary is not receptive during braking, can make electromagnetically induced acoustic noise
- coils: in magnetic resonance imaging, "coil noise" is that part of total system noise attributed to the receiving coil, due to its non-zero temperature.
Rotating devices
Rotating devices include radial and axial flux rotating electric machines used for electrical to mechanical power conversion such as
- induction motors[23]
- synchronous motors with permanent magnets or DC wound rotor
- switched reluctance motors
In such device, dynamic electromagnetic forces come from variations of magnetic field, which either comes from a steady AC winding or a rotating DC field source (permanent magnet or DC winding).
Sources of magnetic noise and vibrations in electric machines
The harmonic electromagnetic forces responsible for magnetic noise and vibrations in a healthy machine can come from
- Pulse-width modulation supply of the machine[24]
- slotting effects [25][26][27]
- magnetic saturation[28]
In a faulty machine, additional noise and vibrations due to electromagnetic forces can come from
- mechanical static and dynamic eccentricities[29]
- uneven air-gap[30]
- demagnetization
- short circuits
- missing magnetic wedges
Unbalanced Magnetic Pull (UMP) describes the electromagnetic equivalence of mechanical rotating unbalance: if electromagnetic forces are not balanced, a non-zero net magnetic force appears on stator and rotor. This force can excite the bending mode of the rotor and create additional vibration and noise.
Reduction of electromagnetic noise and vibrations
Reduction of magnetic noise and vibrations in electric machines
NVH mitigation techniques in electrical machines include[31]
- reducing the magnitude of electromagnetic excitations, independently of the structural response of the electrical machine
- reducing the magnitude of the structural response, independently of the electromagnetic excitations
- reducing the resonances occurring between electromagnetic excitations and structural modes
Electromagnetic noise and vibration mitigation techniques in electrical machines include:
- choosing the right slot/pole combination and winding design
- avoiding resonances match between stator and electromagnetic excitations
- skewing the stator or the rotor
- implementing pole shaping / pole shifting / pole pairing techniques
- implementing harmonic current injection or spread spectrum PWM strategies
- using notches / flux barriers on the stator or the rotor
- increasing damping
Reduction of "coil noise"
Coil noise mitigation actions include:
- add some glue (e.g. a layer of glue is often added on the top of television coils ; over the years, this glue degrades and the sound level increases)
- change the shape of the coil (e.g. change coil shape to a figure eight rather than a traditional coil shape)
- isolate the coil from the rest of the device to minimize structure-borne noise
- increase damping
Experimental illustrations
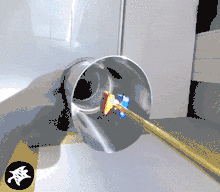
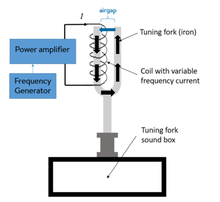
A varying electromagnetic force can be produced either by a moving source of DC magnetic field (e.g. rotating permanent magnet or rotating coil supplied with DC current), or by a steady source of AC magnetic field (e.g. a coil fed by a variable current).
Forced vibration by a rotating permanent magnet
This animation illustrates how a ferromagnetic sheet can be deformed due to the magnetic field of a rotating magnet. It corresponds to an ideal one pole pair permanent magnet synchronous machine with a slotless stator.
Acoustic resonance by a variable frequency coil
The resonance effect of magnetic vibration with a structural mode can be illustrated using a tuning fork made of iron. A prong of the tuning fork is wound with a coil fed by a variable frequency power supply. A variable flux density circulates between the two prongs and some dynamic magnetic forces appear between the two prongs at twice the supply frequency. When the exciting force frequency matches the fundamental mode of the tuning fork close to 400 Hz, a strong acoustic resonance occurs.
Examples of audio files
PMSM motor (traction application)
External links
References
- Le Besnerais, J., Lanfranchi, V., Hecquet, M., & Brochet, P. (2010). Characterization and Reduction of Audible Magnetic Noise Due to PWM Supply in Induction Machines. IEEE Transactions on Industrial Electronics. http://doi.org/10.1109/tie.2009.2029529
- van der Giet, M., (2011). Analysis of electromagnetic acoustic noise excitations – a contribution to low-noise design and to the auralization of electrical machines, RWTH Aachen University, Shaker Verlag.
- Finley, W. R., Hodowanec, M. M., & Holter, W. G. (1999). An Analytical Approach to Solving Motor Vibration Problems, 36(5), 1–16.
- Carmeli, M. S., Castelli Dezza, F., & Mauri, M. (2006). Electromagnetic vibration and noise analysis of an external rotor permanent magnet motor. International Symposium on Power Electronics, Electrical Drives, Automation and Motion (SPEEDAM), 1028–33. http://doi.org/10.1109/SPEEDAM.2006.1649919
- Le Besnerais, J. (2015). Effect of lamination asymmetries on magnetic vibrations and acoustic noise in synchronous machines. In 2015 18th International Conference on Electrical Machines and Systems (ICEMS). http://doi.org/10.1109/icems.2015.7385319
- Belahcen, A. (2004). Magnetoelasticity, magnetic forces and magnetostriction in electrical machines. PhD thesis, Helsinki University of Technology, Finland.
- Tan Kim A. (2013). Contribution à l'étude du bruit acoustique d'origine magnétique en vue de la conception optimale de machines synchrones à griffes pour application automobile. PhD thesis, Université de Technologie de Compiègne, France.
- De Madinabeitia I. G, (2016). Analysis of force and torque harmonics spectrum in an induction machine for automotive NVH Purposes. Master's thesis, University of Technology of Chalmers, Sweden.
- Devillers E., Le Besnerais J., Regniez M. and Hecquet M., (2017). Tangential effects on magnetic vibrations of induction machines using subdomain method and electromagnetic vibration synthesis, Proceedings of IEMDC 2017 Conference, Miami, USA. https://eomys.com/recherche/publications/article/tangential-effects-on-magnetic-vibrations-and-acoustic-noise-of-induction
- M. Rossi and J. Le Besnerais, Vibration Reduction of Inductors Under Magnetostrictive and Maxwell Forces Excitation, in IEEE Transactions on Magnetics, vol. 51, no. 12, pp. 1–6, Dec. 2015. https://doi.org/10.1109/TMAG.2015.2469643
- Arturi, C.M., 1992. Force calculation in transformer windings under unbalanced MMFs by a non-linear finite element code. IEEE transactions on magnetics, 28(2), pp.1363-1366.
- M. Hurkala, Noise analysis of high voltage capacitors and dry-type air-core reactors. Doctoral dissertation, Aalto University, Finland, 2013
- https://product.tdk.com/en/contact/faq/31_singing_capacitors_piezoelectric_effect.pdf
- Le Besnerais, J. (2008). Reduction of magnetic noise in PWM-supplied induction machines − low-noise design rules and multi-objective optimization. PhD Thesis, Ecole Centrale de Lille, Lille, France. https://hal.archives-ouvertes.fr/tel-00348730/
- "MANATEE software (Magnetic Acoustic Noise Analysis Tool for Electrical Engineering), official website". Retrieved September 15, 2017.
- "Flux software official website".
- "Jmag software official website".
- "Maxwell software official website".
- "Opera software official website".
- "Comsol software official website".
- "Ansys software official website".
- Weiser, B., Pfützner, H., & Anger, J. (2000). Relevance of Magnetostriction and Forces for the Generation of Audible Noise of Transformer Cores, 36(5), 3759–3777.
- Le Besnerais, J. (2008). Reduction of magnetic noise in PWM-supplied induction machines − low-noise design rules and multi-objective optimization. PhD Thesis, Ecole Centrale de Lille, Lille, France. https://hal.archives-ouvertes.fr/tel-00348730/
- Le Besnerais, J., Lanfranchi, V., Hecquet, M., & Brochet, P. (2010). Characterization and Reduction of Audible Magnetic Noise Due to PWM Supply in Induction Machines. IEEE Transactions on Industrial Electronics. http://doi.org/10.1109/tie.2009.2029529
- Le Besnerais, J., Lanfranchi, V., Hecquet, M., & Brochet, P. (2009). Optimal Slot Numbers for Magnetic Noise Reduction in Variable-Speed Induction Motors. IEEE Transactions on Magnetics. http://doi.org/10.1109/tmag.2009.2020736
- Verez, G., Barakat, G., Amara, Y., Bennouna, O., & Hoblos, G. (n.d.). Impact of Pole and Slot Combination on Noise and Vibrations of Flux-Switching PM Machines, (1).
- Zhu, Z. Q., Xia, Z. P., Wu, L. J., & Jewell, G. W. (2009). Influence of slot and pole number combination on radial force and vibration modes in fractional slot PM brushless machines having single- and double-layer windings. 2009 IEEE Energy Conversion Congress and Exposition, ECCE 2009, 3443–3450. http://doi.org/10.1109/ECCE.2009.5316553
- Le Besnerais, J., Lanfranchi, V., Hecquet, M., Lemaire, G., Augis, E., & Brochet, P. (2009). Characterization and Reduction of Magnetic Noise Due to Saturation in Induction Machines. IEEE Transactions on Magnetics. http://doi.org/10.1109/tmag.2008.2012112
- Torregrossa, D., Khoobroo, A., & Fahimi, B. (2012). Prediction of acoustic noise and torque pulsation in PM synchronous machines with static eccentricity and partial demagnetization using field reconstruction method. IEEE Transactions on Industrial Electronics, 59(2), 934–944. http://doi.org/10.1109/TIE.2011.2151810
- Le Besnerais, J. (2015). Effect of lamination asymmetries on magnetic vibrations and acoustic noise in synchronous machines. In 2015 18th International Conference on Electrical Machines and Systems (ICEMS). http://doi.org/10.1109/icems.2015.7385319
- "Noise mitigation techniques in electric machines". www.eomys.com. EOMYS ENGINEERING. Retrieved September 15, 2017.