Dwell mechanism
A dwell mechanism (either a linkage or cam-follower type) is an intermittent motion mechanism that alternates forward and return motion with holding position(s).[1]
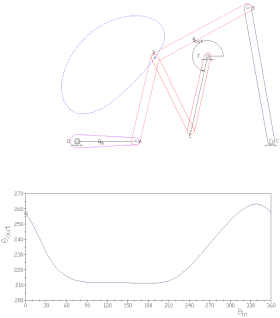
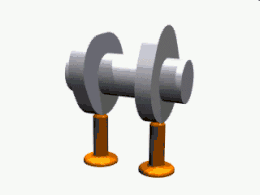
Single vs. Double Dwell
Single Dwell Cam Mechanisms
In a single dwell Cam mechanism, there are three motion functions that follow each other and then repeat: a dwell, a rise, and a return function. It is sometimes desired to use a Rise function such that its acceleration does not become zero at its end. To maintain continuity of acceleration, the return function should begin with a same non-zero acceleration that matches the end of the rise function. There are a number of functions that can provide these motion requirements. A double-harmonic function is a common example used for single dwell.[2]
Dwell with Linkage Mechanisms

Linkage (mechanical) mechanisms can only provide approximate single dwell, and require a minimum of six links. A Four-bar linkage mechanism must be picked first to provide the appropriate coupler curve with a circular region (or approximate circular region). A two link dyad is then added to provide the output link with the desired dwell motion.[4]
The concept for linkage dwell mechanisms is that a node located at the center of the circular arc segment of a coupler curve will remain relatively stationary. Therefore, actual dwell time will depend on the length of the approximate circular arc in the coupler curve. Initial designs may need optimization to improve the dwell characteristics.[5]
Applications
Cam-follower dwell mechanisms are used in pairs in sewing machines to operate the four motion feed dogs, with one cam moving the dog up and down, and the other cam moving the dog forwards and backwards. The cams in this application are usually phased 90 degrees apart allowing a pause in the up/down movement of the dog while it is being moved forwards/backwards. A separate adjustable sliding block or link is used to control the amount of forwards/backwards movement of the dog.
Industrial applications include loading or unloading parts, or transporting a part to a machine and holding it in place for a manufacturing process.[6]
Other applications include assembly lines, package machinery, machine tools etc.
Further reading
- Norton, R (2009) Cam Design and Manufacturing Handbook, Industrial Press
- Rothbart, H (2003) Cam Design Handbook, McGraw Hill
References
- Uicker, J. Pennock, G. & Shigley, J. (2010). Theory of Machines and Mechanisms (4th ed.). Oxford University Press, p. 201.
- Norton, R. (2008) Design of Machinery (4th ed.), McGraw Hill, p.427
- Doane, J. (2015) Machine Analysis with Computer Applications for Mechanical Engineers (1st ed.), Wiley, p299
- Norton, R. (2008) Design of Machinery (4th ed.), McGraw Hill, p.147
- Doane, J. (2015) Machine Analysis with Computer Applications for Mechanical Engineers (1st ed.), Wiley, p167
- Doane, J. (2015) Machine Analysis with Computer Applications for Mechanical Engineers (1st ed.), Wiley, p167