Dry sump
A dry-sump system is a method to manage the lubricating motor oil in four-stroke and large two-stroke piston driven internal combustion engines. The dry-sump system uses two or more oil pumps and a separate oil reservoir, as opposed to a conventional wet-sump system, which uses only the main sump (U.S.: oil pan) below the engine and a single pump. A dry-sump engine requires a pressure relief valve to regulate negative pressure inside the engine, so internal seals are not inverted.
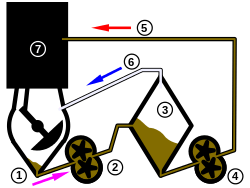
Dry-sumps are common on larger diesel engines such as those used in ships, as well as gasoline engines used in racing cars, aerobatic aircraft and high-performance motorcycles. Dry sump lubrication may be chosen for these applications due to increased reliability, oil capacity, reduction of oil starvation under high g-loads and/or other technical or performance reasons. Dry sump systems may not be suitable for all applications due to increased cost, complexity, and/or bulk, among other factors.
Mechanism
Engines are both lubricated and cooled by oil that circulates throughout the engine, feeding various bearings and other moving parts and then draining, via gravity, into the sump at the base of the engine. In the wet-sump system of most production automobile engines, a pump collects this oil from the sump and directly circulates it back through the engine. In a dry-sump, the oil still falls to the base of the engine, however instead of collecting in a reservoir-style oil sump, it falls into a much shallower sump, where one or more scavenge pumps draw it away and transfer it to a (usually external) reservoir, where it is both cooled and de-aerated before being recirculated through the engine by a pressure pump. Dry-sump designs frequently mount the pressure pump and scavenge pumps on a common crankshaft, so that one pulley at the front of the system can run as many pumps as the engine design requires. It is common practice to have one scavenge pump per crankcase section, however in the case of inverted engines (aircraft engine) it is necessary to employ separate scavenge pumps for each cylinder bank. Therefore, an inverted V engine would have a minimum of two scavenge pumps and a pressure pump in the pump stack.
The main purpose of the dry-sump system is to contain all the stored oil in a separate tank, or reservoir. This reservoir is usually tall and round or narrow and specially designed with internal baffles, and an oil outlet (supply) at the very bottom for uninhibited oil supply. The dry-sump oil pump is a minimum of 2 stages, with as many as 5 or 6. One stage is for pressure and is supplied the oil from the bottom of the reservoir, and along with an adjustable pressure regulator, supplies the oil under pressure through the filter and into the engine. The remaining stages "scavenge" the oil out of the dry-sump pan and return the oil (and gasses) to the top of the tank or reservoir. If an oil cooler is used usually it is mounted inline between the scavenge outlets and the tank. The dry-sump pump is usually driven by a Gilmer or High Torque Drive (HTD) timing belt and pulleys, off the front of the crankshaft, at approximately one half crank speed. The dry-sump pump is designed with multiple stages to ensure that all the oil is scavenged from the pan and also to allow removal of excess air from the crankcase.[1][2]
Advantages
A dry-sump system offers many advantages over a wet-sump. The primary advantages include:[1][3][4]
- Improved engine reliability due to consistent oil pressure. This is the reason why dry-sumps were invented.
- Increased oil capacity by using a large external reservoir, that would be impractical in a wet-sump system.
- Prevention of the engine experiencing oil-starvation during high g-loads, which is particularly useful in racing cars, high performance sports cars, and aerobatic aircraft. Dry-sump designs are not susceptible to the oil movement problems from high cornering forces that wet-sump systems can suffer where the force of the vehicle cornering can cause the oil to pool on one side of the oil pan, possibly uncovering the oil pump pickup tube and causing cavitation and loss of oil pressure.
- Improvements to vehicle handling and stability. The vehicle's center of gravity can be lowered by mounting the engine lower in the chassis due to a shallow sump profile. A vehicle's overall weight distribution can be modified by locating the external oil reservoir away from the engine.
- Improved oil temperature control. This is due to increased oil volume providing resistance to heat saturation, the positioning of the oil reservoir away from the hot engine, and the ability to include cooling capabilities between the scavenger pumps and oil reservoir and also within the reservoir itself.
- The ability to release gasses trapped in the oil from ring blow-by and the action of the crankshaft and other moving parts in the oil, then return these gases via a line from the top of the oil reservoir to the combustion chamber.
- Improved pump efficiency to maintain oil supply to the engine. Since scavenge pumps are typically mounted at the lowest point on the engine, the oil flows into the pump intake by gravity rather than having to be lifted up into the intake of the pump as in a wet-sump. Furthermore, scavenge pumps can be of a design that is more tolerant of entrapped gasses than the typical pressure pump, which can lose suction if too much air mixes into the oil. Since the pressure pump is typically lower than the external oil tank, it always has a positive pressure on its suction regardless of cornering forces.[5]
- Increased engine horsepower due to reduced viscous and air friction. In a wet-sump engine the crank shaft and other moving parts splash through the oil at thousands of RPM causing a "hurricane that whips the oil in a wet-sump engine into an aerated froth like a milkshake in a blender".[6] Additionally, in a wet-sump, each revolution generates minute amounts of parasitic power loss caused by viscous drag and air drag (or 'windage') as the parts move rapidly through the oil and air in the lower engine. At high RPM these small sources of drag compound dramatically, resulting in significant power loss.[6][7] In a dry-sump, the scavenger pump removes the oil and therefore the source of viscous friction, but also creates an air vacuum that significantly reduces air-friction, thus freeing the moving parts of much viscous and air friction and allowing engine power output to increase.[2][8]
- Having the pumps external to the engine makes them easier to maintain or replace.
Disadvantages
Dry-sump engines have several disadvantages compared to wet-sump engines, including;[1] [9] [10][11]
- Dry-sump systems add cost, complexity, and weight.
- The extra pumps and lines in dry-sump engines require additional oil and maintenance.
- The performance-enhancing features of dry-sump lubrication can hurt a car's day-to-day driveability. A good example is the classic Mercedes-Benz 300SL, a car that was designed for racing but sold to the general public and used on-road. The car had high oil capacity and a dry-sump system to cope with continuous high-speed running while racing. Owners found in general use, however, that the oil never achieved the correct operating temperature because the system was so efficient at cooling the oil. A makeshift solution was devised to deliberately block the oil cooler airflow to boost the oil temperature.
- The large external reservoir and pumps can be tricky to position around the engine and within the engine bay due to their size.
- As wrist pins and pistons rely for lubrication and cooling respectively, on the oil being splashed around in the crankcase, these parts might have inadequate oiling if too much oil is pulled away by the pump. Installing piston oilers can circumvent this issue, but do so with additional cost and complexity for the engine.[11]
- Inadequate upper valvetrain lubrication can also become an issue if too much oil vapor is being pulled out from the area, especially with multi-staged pumps.[11]
Common engine applications
Dry-sumps are common on larger diesel engines such as those used for ship propulsion, largely due to increased reliability and serviceability. They are also commonly used in racing cars and aerobatic aircraft, due to problems with g-forces, reliable oil supply, power output and vehicle handling. The Chevrolet Corvette Z06 has a dry sump engine which requires initial oil change after 500 miles.
Motorcycle engines
The dry-sump lubrication is particularly applicable to motorcycles, which tend to be operated more vigorously than other road vehicles. Although motorcycles such as the Honda CB750 (1969) feature a dry-sump engine, modern motorcycles tend to use a wet-sump design. This is understandable with across-the-frame inline four-cylinder engines, since these wide engines must be mounted fairly high in the frame (for ground clearance), so the space below may as well be used for a wet-sump. However, narrower engines can be mounted lower and ideally should use dry-sump lubrication.
Several motorcycle models that use dry-sumps include;
- The classic British parallel twin motorcycles, such as BSA, Triumph and Norton, all used dry-sump lubrication. Traditionally, the oil tank was a remote item, but some late-model BSAs, and the Meriden Triumphs, used "oil-in-the-frame" designs.
- The Yamaha TRX850 270-degree parallel twin motorcycle has a dry-sump engine. Its oil reservoir is not remote, but integral to the engine, sitting atop the gearbox. This design eliminates external oil lines, allowing simpler engine removal and providing faster oil warm up.
- The Yamaha XT660Z (and R/X models) use a dry-sump design where the bike's frame tubing is used as the oil reservoir and cooling system[12]
- The Yamaha SR400/500 uses a dry-sump design where the bike's frame tubing doubles as the oil reservoir and cooling system.[13]
- Harley-Davidson has used dry-sump type lubricating oil systems in their engines since the 1930s.
- The Rotax engined Aprilia RSV Mille, and the Aprilia RST1000 Futura both incorporate a dry-sump, along with sister bikes, the SL1000 Falco and ETV1000 Caponord.
- The Honda NX650, XR500R, XR600R, XR650R and XR650L four-stroke dirt bikes utilize a dry-sump with the oil in the frame tubing.
- The Suzuki DR-Z400 has a 2L dry-sump with oil in the frame tubing.
- Chennai built Royal Enfield prior to 2007. Royal Enfield dry sump designs were completely phased out by 2012.
See also
Notes
- "Technical Description - The Dry Sump System". Armstrong Race Engineering, Gary Armstrong, DrySump.com, 08-03-2016.
- "Dry Sump". TorqueCars. Retrieved 2016-12-24.
- Van Valkenburgh,Paul (1976) Race Car Engineering and Mechanics Dodd, Mead & Company, p. 181
- "Dry Sump Oil System - Camaro Performers Magazine". Super Chevy. 2011-09-01. Retrieved 2016-12-24.
- Engineering Explained (4 January 2017). "Wet Sump Vs Dry Sump - Engine Oil Systems". YouTube.com. Retrieved 2 May 2020.
- Reher, David (2013-06-25). "Tech Talk #84 – Dry Sumps Save Lives". Reher Morrison Racing Engines. Retrieved 2016-12-24.
- "Wet sumps | High Power Media". www.highpowermedia.com. Retrieved 2016-12-24.
- "Wet sumps". 2012-03-29. Retrieved 2016-12-24.
- "Why do some engines use a dry sump oil system?". HowStuffWorks. 2000-04-01. Retrieved 2016-12-24.
- "Dry sumps". TorqueCars. Retrieved 2016-12-24.
- Carley, Larry (2012-11-14). "Dry Sump Oiling Systems". Engine Builder Mag. Babcox. Retrieved 2017-03-02.
- "XT660Z | Yamaha Motor Australia". www.yamaha-motor.com.au. Retrieved 2018-05-06.
- "The iconic SR400, 35 years heritage". Suzuki Press Release, MCNews.com, 04-11-2013.
References
![]() |
Wikimedia Commons has media related to Dry sump lubrication. |
- "Why do some engines use a dry sump oil system?". HowStuffWorks. Retrieved 2006-11-16.
- "Technical Explanation The Dry Sump System". ARE. Retrieved 2016-08-03.
- "Wet Sump vs Dry Sump - Engine Oil Systems". YouTube.com. EngineeringExplained. 2017-01-04. Retrieved 2017-01-04.