Critical plane analysis
Critical plane analysis refers to the analysis of stresses or strains as they are experienced by a particular plane in a material, as well as the identification of which plane is likely to experience the most extreme damage. Critical plane analysis is widely used in engineering to account for the effects of cyclic, multiaxial load histories on the fatigue life of materials and structures.[1][2][3][4] When a structure is under cyclic multiaxial loading, it is necessary to use multiaxial fatigue criteria that account for the multiaxial loading. If the cyclic multiaxial loading is nonproportional it is mandatory to use a proper multiaxial fatigue criteria. The multiaxial criteria based on the Critical Plane Method are the most effective criteria.[5]
For the plane stress case, the orientation of the plane may be specified by an angle in the plane, and the stresses and strains acting on this plane may be computed via Mohr's circle. For the general 3D case, the orientation may be specified via a unit normal vector of the plane, and the associated stresses strains may be computed via a tensor coordinate transformation law.
The chief advantage of critical plane analysis over earlier approaches like Sines rule, or like correlation against maximum principal stress or strain energy density, is the ability to account for damage on specific material planes. This means that cases involving multiple out-of-phase load inputs, or crack closure can be treated with high accuracy. Additionally, critical plane analysis offers the flexibility to adapt to a wide range of materials. Critical plane models for both metals[6] and polymers[7] are widely used.
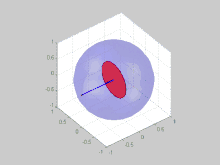
History
Modern procedures for critical plane analysis trace back to research published in 1973 in which M. W. Brown and K. J. Miller observed that fatigue life under multiaxial conditions is governed by the experience of the plane receiving the most damage, and that both tension and shear loads on the critical plane must be considered. [8]
References
- Fatemi, A., & Socie, D. F. (1988). A Critical Plane Approach to Multiaxial Fatigue Damage Including Out‐Of‐Phase Loading. Fatigue & Fracture of Engineering Materials & Structures, 11(3), 149-165.
- Park, J., & Nelson, D. (2000). Evaluation of an energy-based approach and a critical plane approach for predicting constant amplitude multiaxial fatigue life. International Journal of Fatigue, 22(1), 23-39.
- Susmel, L. (2010). A simple and efficient numerical algorithm to determine the orientation of the critical plane in multiaxial fatigue problems. International Journal of Fatigue, 32(11), 1875-1883.
- Draper, John. Modern metal fatigue analysis. EMAS, 2008.
- Socie, D. F.;Marquis, G. B. (2000). Multiaxial Fatigue.Ed. SAE International, USA.
- Glinka, G.; Shen, G.; Plumtree, A. (1995). "A multiaxial fatigue strain energy density parameter related to the critical fracture plane". Fatigue & Fracture of Engineering Materials & Structures. 18 (1): 37–46.
- Barbash, Kevin P.; Mars, William V. (2016). "Critical Plane Analysis of Rubber Bushing Durability under Road Loads". SAE Technical Paper. 2016-01-0393.
- Brown, M. W.; Miller, K. J. (1973). "A theory for fatigue failure under multiaxial stress-strain conditions". Proceedings of the Institution of Mechanical Engineers. 187 (1): 745-755. doi:10.1243/PIME_PROC_1973_187_161_02.
External links
- Book on Multiaxial Fatigue (by Darrell Socie and Gary Marquis)
- Class notes on Multiaxial Fatigue (by Ali Fatemi)
- Multiaxial Fatigue Theory (by MSC.Fatigue' Help)
- Metal FE-Based Fatigue Analysis software: nCode DesignLife (by HBM)
- Metal FE-Based Fatigue Analysis software: fe-safe (by Dassault Systemes SIMULIA)
- Metal FE-Based Fatigue Analysis software: FEMFAT (by Magna Powertrain)
- Metal FE-Based Fatigue Analysis software: MSC.Fatigue (by MSC Software)
- Metal FE-Based Fatigue Analysis software: LMS Virtual.Lab Durability (by LMS)
- Metal FE-Based Fatigue Analysis software: NX Durability (by Siemens)
- Metal FE-Based Fatigue Analysis software: winLIFE (by Steinbeis-Transferzentrum)
- Metal FE-Based Fatigue Analysis software: fatiga (by Fatec Engineering)
- Rubber Fatigue Analysis software: Endurica (by Endurica LLC)