ACCC conductor
ACCC (Aluminum Conductor Composite Core) is a registered trade mark for a type of "high-temperature low-sag" (HTLS) overhead power line conductor manufactured by 25 international (and authorized) conductor manufacturers.
Invention
CTC Global (formerly Composite Technology Corporation) developed the patented technology.[1][2] The ACCC conductor's composite core is manufactured according to ASTM B987 / B987M - 17 “Standard Specification for Carbon Fiber Thermoset Polymer Matrix Composite Core (CFC) for use in Overhead Electrical Conductors.” CTC Global manufactures ACCC core in the US and with partners in China and Indonesia. Finished ACCC conductor is produced by more than two dozen conductor manufacturers worldwide under license. As of December 2019, over 80,000 km have been deployed at over 700 projects in 51 countries.
Advantages
It is able to carry approximately twice as much current as a traditional aluminium-conductor steel-reinforced cable (ACSR) cable of the same size and weight,[3][4] making it popular for retrofitting an existing electric power transmission line without needing to change the existing towers and insulators.
In addition to the labor and materials savings, such an upgrade can be performed as a "maintenance and repair" operation, without the lengthy permitting process required for new construction.
It does this by replacing the steel core in ACSR cable with a carbon and glass fiber strength member[4]:2 formed by pulltrusion. This composite strength member provides several advantages:
- It is lighter. The weight saved can be used for more aluminium conductor. ACCC cable uses trapezoidal strands to fit more aluminium into the same cable diameter.
- Softer, fully annealed aluminium can be used for the conductors. ACSR cable uses stronger non-annealed commercially pure aluminium which contributes to the cable's tensile strength and improves sag and pull-out under ice load, but has about 3% less electrical conductivity and limits the maximum operating temperature.[4]:12
- It has a much lower coefficient of thermal expansion (CTE) (1.6 ppm/°C) than ACSR (11.6 ppm/°C).[5]:23 This lets the cable be operated at a significantly higher temperature without excessive sag between poles.
The first two factors result in roughly 30% greater conductivity than an equivalent ACSR conductor, allowing 14% more current to be carried at equal temperature. For example, 1.107 in (28.1 mm) diameter ACCC "Drake" conductor at 75 °C has an AC resistance of 106 mΩ/mile,[6] while equivalent ACSR conductor has an AC resistance of 139 mΩ/mile,[7] 31% higher.
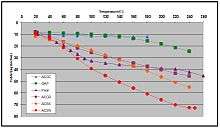
The remaining capacity increase is provided by an increased operating temperature of 180 °C (356 °F) continuous and 200 °C (392 °F) emergency,[8] compared to 75 °C (167 °F) continuous and 100 °C (212 °F) emergency for ACSR.
The manufacturers rate the cable for continuous operation at 180 °C surface temperature,[8][9] Operation at these temperatures implies high line losses, which may be uneconomical, but the ability to carry such current contributes to the redundancy of the electric grid (the high overload capacity can stop a potential cascading failure) and thus can be valuable even when rarely used directly. Even at higher operating temperatures, the ACCC conductor's added aluminum content and lower electrical resistance offers reduced line losses compared to other conductors of the same diameter and weight.
Disadvantages
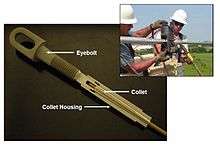
- The primary disadvantage is cost; ACCC costs 2.5–3 times as much as ACSR cable.[2]:17
- Although ACCC has significantly less thermal sag than even other HTLS conductor designs,[5]:20 it has a lower axial stiffness. Therefore, it sags more than other designs under ice load, although an "ultra-low-sag" (higher modulus) version is available at a cost premium.[5]:21 Also, other aluminium alloys with an increased strength at the expense of electrical conductivity can be used to improve ice load sag. Ice load can also lead to the loosening of outer layer strands because of plastic deformation by the attached weight.
- Annealed aluminium is extremely soft and makes the conductor prone to surface damage.
- The conductor has a larger minimum bend radius, requiring extra care during installation.
- The conductor requires special fittings and stringing equipment that are more expensive.
References
- J. Chan; B. Clairmont; D. Rueger; D. Childs; S. Karki (July 2008). Demonstration of Advanced Conductors for Overhead Transmission Lines (PDF) (Report). Electric Power Research Institute. Retrieved 2014-02-03.
- Clairmont, Bernie (September 11, 2008). High-Temperature Low-Sag Conductors (PDF). Electric Power Research Institute.
- Wareing, B. (28 February 2011). Types and Uses of High Temperature Conductors (PDF). CIGRÉ (International Council on Large Electric Systems) Seminar. Bangkok: CIGRÉ Study Committee B2 Working group 11. Archived from the original (PDF) on 3 December 2013. Retrieved 2014-02-03.
- CTC Global (2011). Engineering Transmission Lines With High-Capacity, Low-Sag ACCC Conductor (PDF). ISBN 978-0-615-57959-7.
- Slegers, James (2011-10-18). Transmission Line Loading: Sag Calculations and High-Temperature Conductor Technologies (PDF) (Report). Iowa State University.
- Banerjee, Koustubh (January 2014). Making the Case for High Temperature Low Sag (HTLS) Overhead Transmission Line Conductors (PDF) (M.Sc.). Arizona State University. p. 70.
- "Aluminum Conductor. Steel Reinforced. Bare". Southwire. Archived from the original on 2016-03-04. Retrieved 2016-01-08.
- CTC Global (2012-08-28). "ACCC Specification Sheets" (PDF). Retrieved 2016-01-08.
- Alawar, Ahmad A.; Bosze, Eric J.; Nut, Steven R. (July 13, 2007). High Temperature Strength and Creep of an Al Conductor with a Hybrid Composite Core (PDF). 16th International Conference on Composite Materials.